Industry events give people the opportunity to discover the latest solutions from exhibiting companies or to evaluate how far they have gone in their activities. Analyzing the latest innovations from players we already know can be misleading: we may have the impression they are advancing at a very fast pace or that they are not fast enough in their activities.
What about the industry players of Formnext? – the example of Arburg & Trumpf
Arburg and the famous Freeformer

We announced it in our Formnext preview. Arburg has indeed unveiled the Freeformer 300-3X. 300 in the name refers to the available surface area of the platform in square centimetres. The build chamber of the system can produce parts with dimensions of up to 234 x 134 x 230 millimetres.
Designed for automation and process integration, the system integrates a two-part build chamber door that can be opened to insert the part platform or remove the finished part. Furthermore, a great improvement is that it is possible to refill the materials containers when the machine is functioning by opening the top half of the door.
Above and beyond the additive manufacture of one-off parts and small-volume batches, high-volume parts can also be enhanced and customer wishes incorporated directly in the added value chain in batches as small as a single unit by combining additive manufacturing, injection moulding and Industry 4.0 technologies.
Among the key industrial sectors, the Freeformer will raise the interest of healthcare professionals, especially prosthesis manufacturers.
The company stated at its press conference that, for now, the system is only available for a select range of customers. It will be officially commercialized in Spring 2019.
People were speechless in front of Trumpf’s demonstration
The manufacturer of TruPrint 1000 has demonstrated how TruPrint 5000, preheated to 500 degrees Celsius, is capable to print high-carbon steel or titanium alloy components that don’t crack or severely warp.
Tool and mold makers frequently work with carbon tool steel 1.2343, an extremely hard and wear-resistant material that easily dissipates heat.
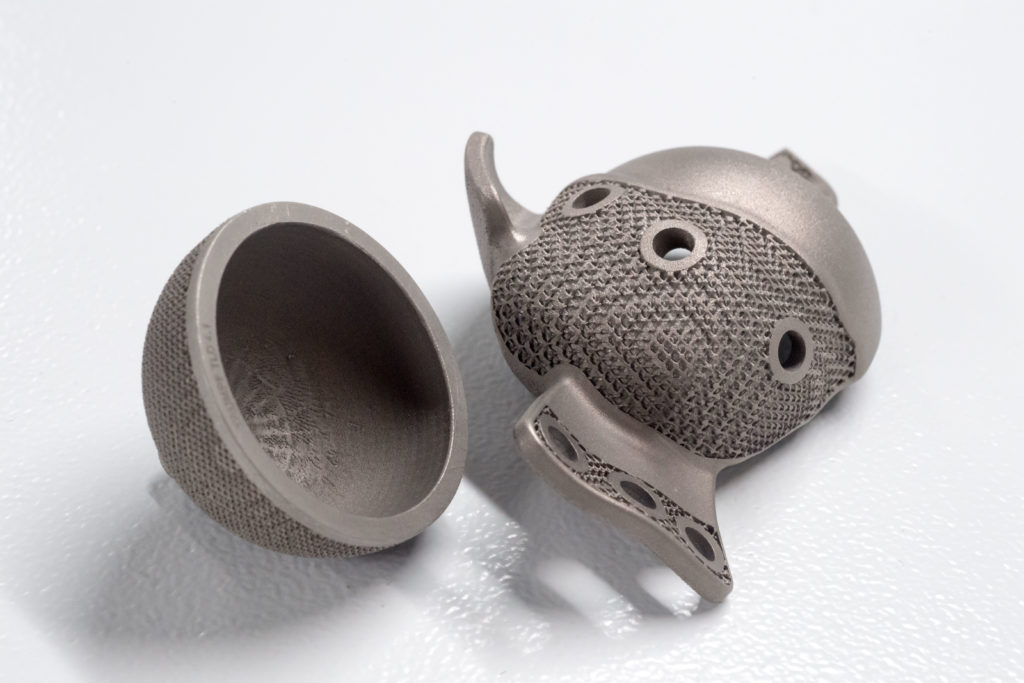
However, it is not easy to handle it on a 3D printer because the components crack during the printing process. “The laser beam melts the component surface, which subsequently cools back down to room temperature. The components weren’t able to withstand this temperature drop, and cracks formed,” says Tobias Baur, TRUMPF General Manager Additive Manufacturing in charge of technology.
That’s why the substrate plate of the TruPrint 5000 3D printer can be preheated to 500 degrees Celsius. This lessens the temperature drop following laser melting. “The material quality and surface of carbon steels are significantly better than without preheating, preventing fractures in the components,” explains Baur.
New “Collaborations” that have emerged: “AddUp & ESI“, “LSS & Arkema“.
Industry players have proven more than once that unity is strength. Be it in software, materials or 3D printers, bringing teams together leads to good quality work.
AddUp, a famous specialist in industrial solutions for additive manufacturing, and ESI Group, that specializes in virtual prototyping solutions based on material physics, have collaborated on a new software module: Distortion Simulation AddOn.
This module will enhance the range of functionalities of the AddUpManagerTM software for the definition and production tracking of parts in additive manufacturing.
Thanks to this module, users will better understand material processes and behavior, a key factor to improve the competitiveness of the additive manufacturing process.
The optimization of process parameters is a crucial stage in the additive manufacturing process and a driver of competitive differentiation.
So far, in conventional processes, production validation has meant primarily producing parts, then assessing their conformity. Introducing a simulation tool, all too often limited expert users, required multiple feedback loops between different functions, creating discontinuity over the digital chain.
LSS & Arkema
This collaboration will certainly remind you of one of these Franco-German treaties. LSS Laser-Sinter-Service GmbH, a Dortmund-based 3D printing service provider based in (Germany), will use ARKEMA‘s Kepstan® polyetherketone-ketone (PEKK) polymer for its new range of RAPTOR TM 3D printers.
PEKK Kepstan® is a halogen-free material ideal for selective laser sintering (SLS). According to Arkema, the material is suitable for its thermomechanical properties and superior chemical and fire resistance (low flame, smoke and toxicity). Furthermore, it allows industrial AM applications in the Electrical & Electronics sectors.
The material will be used on 3D printers that incorporate the ThermoMelt™ technology, patented by Airbus. It will serve for the manufacturing of high-performance industrial parts.
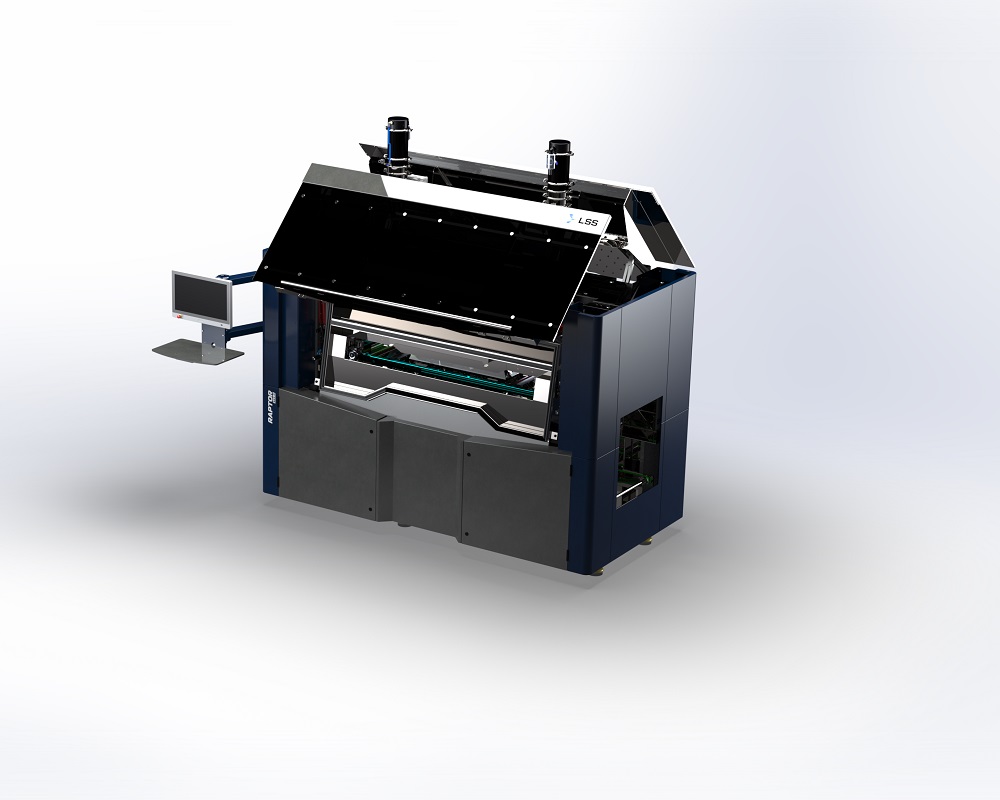
Their first times
While some players such as LSS, Stratasys, Arburg, Prodways or even Oerlikon have become loyal customers of Formnext, this year also marks the first time for some companies from different regions to showcase at Formnext.
From Italy, we had the pleasure to meet Prosilas, which officially marked its entrance on the German market. Already present in France at the 3D Print exhibition, Prosilas is increasingly marking its territory in Europe.
From France, in addition to Arkema, AddUp (& BeAM) that have already been mentioned, Kimya, Techniques Chimiques Nouvelles, Erpro Group, and Synthene were exhibiting alongside Prodways this year.
On the Belgian side, Colossus, Any Shape, Materialise and the great Solvay have joined Twikit, Flam3D and its group.
Coming from the United States, you will probably recognize Avi Reichental and its partner companies (Nexa3D, Techniplas, Xponential Works), Sintavia, Desktop Metal, Carbon…
For further information about 3D Printing, follow us on our social networks and subscribe to our newsletter
Would you like to subscribe to 3D Adept Mag? Would you like to be featured in the next issue of our digital magazine? Send us an email at contact@3dadept.com