Abeye, incubée par les opticiens Atol, est la start-up à l’origine de la marque de lunettes Lexilens qui facilitent la lecture des enfants dyslexiques. Il s’agit de lunettes électroniques dont les verres actifs et teintés filtrent les images miroirs à l’origine des difficultés de lecture. Les verres s’activent par une simple pression sur un bouton qui met en fonctionnement le système électronique logé dans les branches. Ce fonctionnement disruptif s’appuie sur une découverte scientifique fondamentale liant dyslexie, œil et cerveau. Les lunettes ont un fonctionnement simple et procurent un effet instantané et universel, ne dépendant pas de la langue parlée. La batterie dispose de 25h d’autonomie et se recharge à l’aide d’un câble USB-C.
La monture des Lexilens, qui pèse seulement 35 grammes, est imprimée entièrement en 3D grâce à la technologie HP Multi Jet Fusion, puis assemblée. « La fabrication des lunettes Lexilens imprimée en 3D est exceptionnelle puisque c’est le premier produit multi-composants imprimé avec une telle complexité d’assemblage. Pas moins de 9 composants ! » commente Nicolas Aubert, Directeur de l’Impression 3D pour HP France. L’expertise de notre partenaire Erpro a été d’autant plus critique dans un contexte de produits multi-composants, où il faut gérer les jeux d’assemblages, sans compromis sur la qualité du produit final. »
Le développement a nécessité la contribution de différents collaborateurs experts dans un domaine précis : le design a été créé par Lexilens, la fabrication a nécessité l’utilisation de la technologie d’impression 3D HP Multi Jet Fusion via le fournisseur de services Erpro Group et l’enseigne Atol les Opticiens est chargée de la commercialisation.
Focus sur la fabrication des lunettes Lexilens
Pour un processus qui nécessitait la fabrication de produits multi-composants, il était important de gérer les jeux d’assemblages, sans compromis sur la qualité du produit final.
« En effet, chaque composant imprimé en 3D ayant ses propres tolérances dimensionnelles, il faut composer avec une méthodologie de chaîne de cotations adaptée pour que ce puzzle 3D prenne forme », explique Loïc Cliquennois, R&D Project Manager chez Erpro Group.
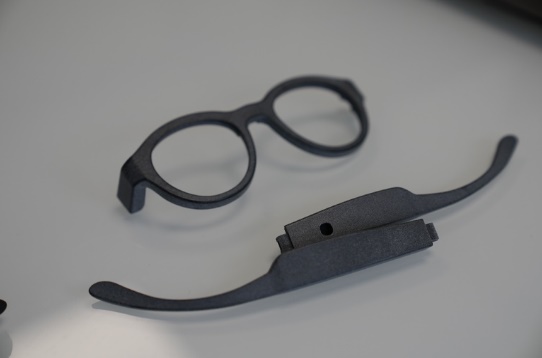
L’étape de pré-production a consisté à éprouver la conception des composants produits puis à optimiser le job de production (orientation, placement, optimisation densité, qualité, volume) à l’aide du logiciel Magics CFAO. L’étape de production s’est déroulée sur des imprimantes HP Multi Jet Fusion 5200 en utilisant le matériau PA11. Une fois sablées, les montures subissent un post-traitement : une partie de la monture est lissée via un processus physico-chimique et les autres composants sont tribofinis, puis teintés dans des bains spécifiques. Un clip-optique en option, permet d’apporter une correction à la vue si nécessaire.
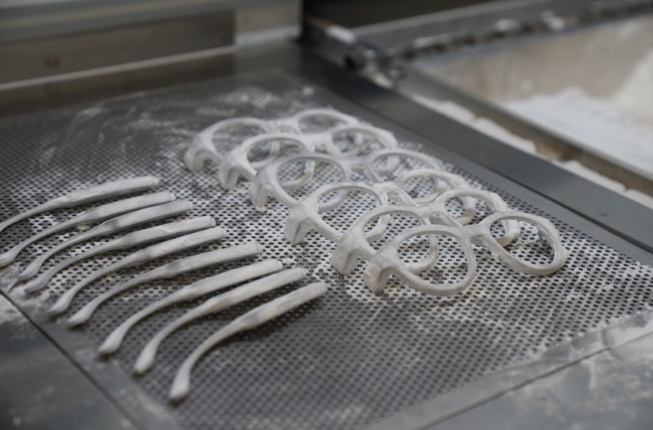
Abeye a ainsi pu tester différents prototypes et réaliser rapidement différentes itérations avant de choisir la bonne technologie et les bons post-traitements.
N’oubliez pas que vous pouvez poster gratuitement les offres d’emploi de l’industrie de la FA sur 3D ADEPT Media ou rechercher un emploi via notre tableau d’offres d’emploi. N’hésitez pas à nous suivre sur nos réseaux sociaux et à vous inscrire à notre newsletter hebdomadaire : Facebook, Twitter, LinkedIn & Instagram ! Si vous avez une innovation à partager pour le prochain numéro de notre magazine numérique ou si vous avez un article à faire connaître, n’hésitez pas à nous envoyer un email à contact@3dadept.com