Whether it is for homes or for industrial settings, a furnace remains a device that produces heat. In industrial environments, those devices were first used in metallurgy to heat and melt metal or to remove gangue, primarily in iron and steel production. Over time, the use of furnaces has expanded so much that it requires a dedicated trade press to speak about all its ins-and-outs. However, it turns out that when it comes to additive manufacturing, the use of furnaces remains quite limited, yet of paramount importance to achieve the desired finished 3D printed part.
Industrial furnaces may have been used since the beginning of the industrial revolution, but the 20th century came with its share of innovations, not to mention that it expanded the use of these technologies to new applications that were previously not considered in the field. The story does not tell us when exactly occurred the first uses of furnaces with Additive Manufacturing. However, it does reveal that most companies that deliver furnaces to additive manufacturing technologies providers or users are mostly companies that have a solid expertise in the development and commercialization of furnaces for conventional manufacturing processes and other industries such as foundry, forging, thermal process technology, to name a few.
So, why & where are furnaces used in the AM process? What type of 3D printed parts require furnaces? How do we use furnaces? And what are the main features of these machines?
This article aims to provide a glimpse of the use of furnaces for additively manufactured parts.
Why & where are furnaces used?
First and foremost, given their primary nature, furnaces are used for applications that require high processing temperatures.
In the AM industry especially, although applications achieved through metal AM technologies will generally require the use of furnaces, it should be noted that two main reasons may explain the use of furnaces. These reasons also help catalogue the 2 main types of furnaces that are used in the field:
Parts that require sintering (and often debinding) and parts that require heat treatment. To this end, “ceramics and composite 3D printed parts may require to be treated in a vacuum furnace, as do most metal 3D printed parts,”, Andrea Cassani, Sales Director at TAV VACUUM FURNACES SPA notes from the outset.
This means that, basically, all types of 3D printed parts may require the use of a furnace at some point of the production.

Debinding and Sintering
For those who are not familiar with these terms, please note that debinding and sintering occur both after the manufacturing process.
Debinding is a process that consists in removing the primary binding material in a very short time and with the least amount of damage.
Sintering is often considered as the final step of all powder metallurgy processes, including some metal 3D printing processes. During this stage, “green parts (a combination of metal powder and binder) are first heated to a temperature where the binder evolves and is removed from the parts. The furnace then ramps up to the sintering temperature of the metal which is just below the melting temperature of the material, fusing together the metal particles. After sintering is complete there is little or no evidence of the original powder particles, fabrication process and parts have very low porosity”.
However, the operator does not automatically always perform both processes. Even though it is faster to debind and then sinter the parts, the operator can also decide to (skip the debinding step and) directly sinter the part. On the other hand, one should note that there might be several steps to the debinding process, and more than one cycle before the binding material is completely removed before that part goes through sintering.
No matter what cycles are performed, sintering helps get a better density of the part. According to experts from Desktop Metal, during the final stage of sintering, pores continue to shrink, and the part further densifies. To optimize part density, sintering temperatures and holds are closely monitored to control and avoid grain growth, which can occur if parts are left at elevated temperatures.
In general, the following three steps are often observed:
- Removal of binder – either by degradation (chemical interaction with furnace gas) and/or evaporation (vaporized binder)
- Densification and pore removal take place as metal particles migrate and fuse
- Cooling of furnace so that parts can be safely removed.
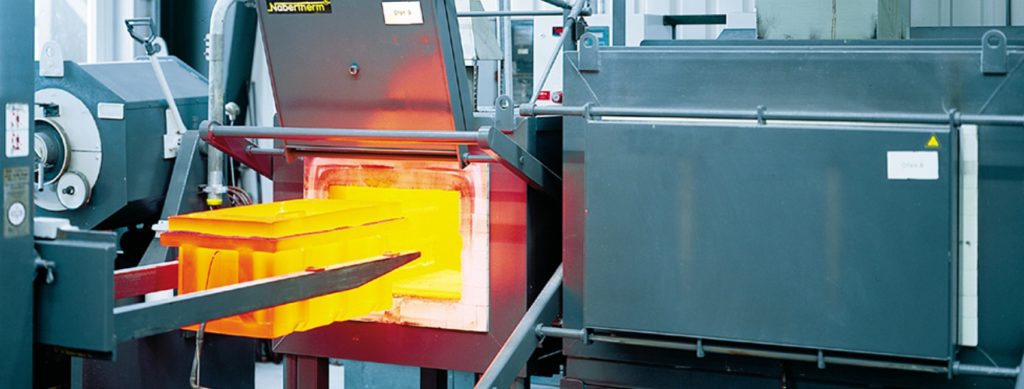
Heat Treatment
As the name implies, heat treatment consists in heating material to a specific temperature and then cooling it to improve its mechanical properties. This material is usually a metal or an alloy. In some manufacturing processes, this part is of paramount importance as it enhances the fabricated part to better withstand wear and tear.
To make it happen, what better way than using a furnace which can maintain heat at a desired temperature for a defined amount of time, before cooling.
“While it’s hot, the metal’s physical structure, also called the microstructure changes, ultimately resulting in its physical properties being changed. The length of time the metal is heated for is called the ‘soak time.’ Knowing what temperatures to heat and cool metals at, as well as how long each step of the process should take for a specific metal or alloy is extremely complicated. Because of that, material scientists known as metallurgists, study the effects of heat on metal and alloys and provide precise information on how to perform these processes correctly”, an expert from General Kinematics explains.
Taking the example of parts that have been manufactured using SLM technology, TAV VACUUM FURNACES SPA explains that most materials that are printed with SLM technology need a heat treatment.
“This heat treatment can be de-tensioning (to release most of the internal tensions accumulated in the material during the printing phase) or of another type (to try to optimize the mechanical properties of the component according to its specific application). Usually these treatments are carried out in air or in controlled atmosphere”, the expert highlights. Furthermore, materials such as stainless steel, titanium superalloys, superalloys of nickel and CoCr alloys, could require the use of vacuum.
What type of 3D printed parts require furnaces?
As mentioned earlier, all types of 3D printed parts may require the use of furnaces at some point of their production. The thing is, there are so many furnaces that a metal 3D printed part will not require the same furnace as a ceramics or a polymer 3D printed part. In the same vein, they will not necessarily go through the same stages after the debinding or sintering phases.
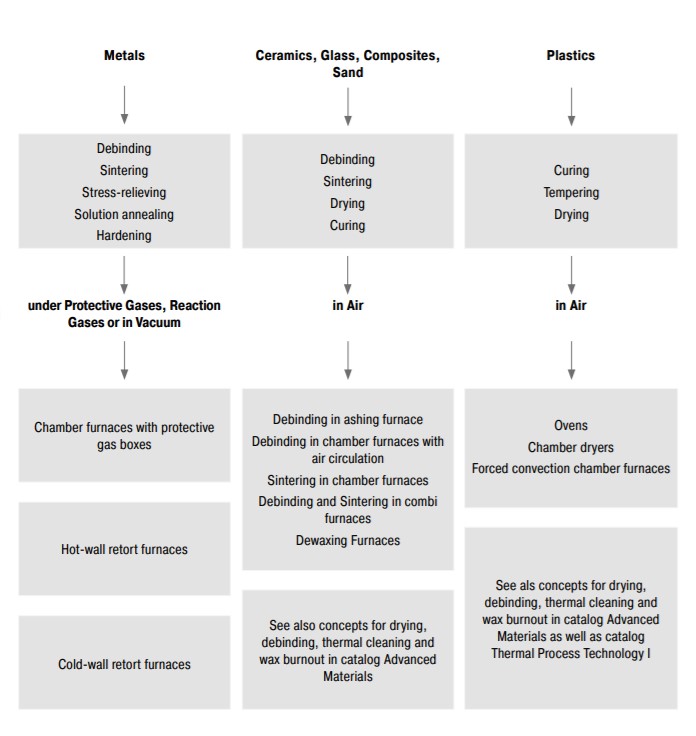
Please note that, 3D printed parts produced in ceramics, glass, composites or sand can be treated in vacuum furnaces or in air.
How do we use furnaces? And what are the main features of these machines?
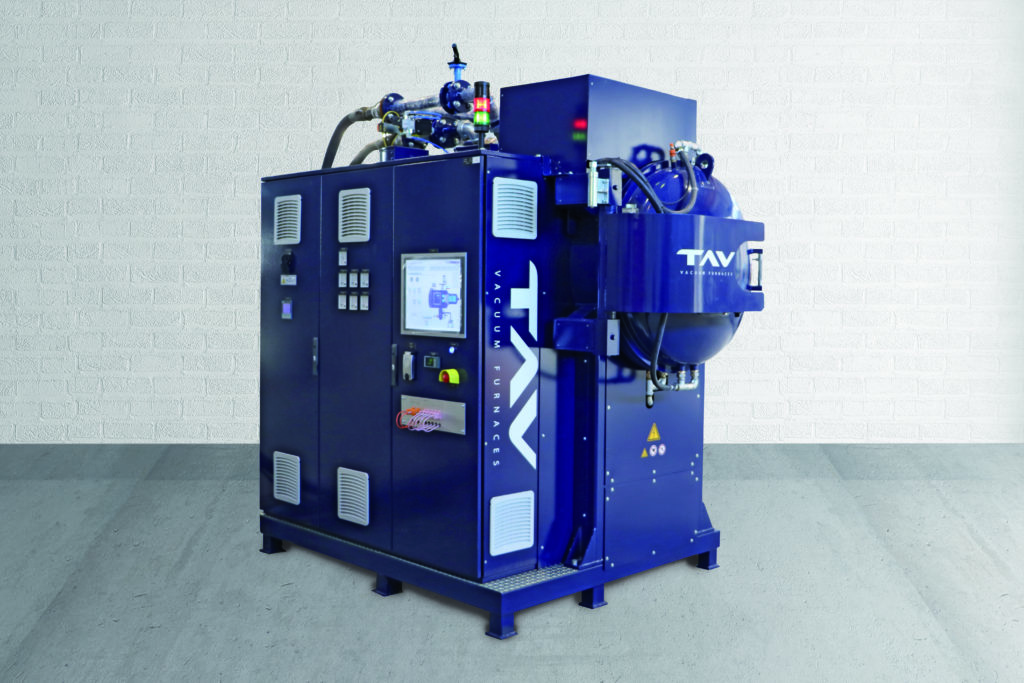
We started this article with the assumption that we could draw a general use of furnaces for 3D printed parts. We were wrong. Contributors and resources we relied on to write this article reveal that with the many types of furnace that exist, it would not be possible to catalogue the main features of furnaces – at least not here.
So, how can we help AM users to make a decision? Cassani attempts to provide a useful answer:
“We cannot make a generic statement valid for all kind of vacuum furnaces. We can say that today the temperature range required for 3D printing parts is approx. between 500 and 1400°C for sintering and heat treatment or below 900°C for debinding/presintering. In the case, a part has to be sintered often; we split the process and the furnaces in 2 steps: first step a debinding furnace to take out parts from the binder and second step (at higher temperature) a sintering furnace.
In the case of parts to have to be heat-treated the furnace is very close to a classic vacuum heat treatment furnace, with some specific features/characteristics. You often need to consider that whoever buys a furnace for the heat treatment of 3D printed parts uses the furnace only for these parts, so [an optimised design is generally justified].”
In the same vein, one can take note of the following recommendations from TAV VACUUM FURNACES SPA & SECO/WARWICK S.A. to companies looking for a new furnace:
- Usually, when using the same technology for 3D printing processes and materials, it is not needed to adapt/change the furnace.
- However, the furnace size needs to be adjusted to match estimated production capacity.
- After the use of furnaces, the part often requires finishing and in some cases some small machining.
- If the furnace is correctly customized, the furnace itself only represents a small percentage of the investment required for 3D printers and it can generally work with something between 4 to 16 printers
- One technology may require sintering, while another would need stress relieving. Thus, taking into consideration the manufacturer’s future goals – such as standardization of a furnace, mass production, or constant flow of orders – helps invest in the right industrial furnace and helps companies avoid most of the obstacles before they even occur.
Moving forward…
The truth is, as AM expands, the need for better technological capabilities continue to rise and it’s only recently that heat treatment processes have started to occupy a more important place in the AM landscape.
It is no longer a great achievement to have an industrial (metal/polymer) 3D printer. As a matter of fact, several reports including PostProcess’ ‘Additive Post-Printing Survey’ reveal that over 50% of 3D printer users have two or three different types of technologies within their facility.
This means that the disadvantages of one manufacturing process will ultimately be compensated by the advantages of others and, in this production scheme; furnaces will have to accommodate both.
That’s the reason why collaborations between developers of furnaces and 3D printer manufacturers or private and public research centres/universities are also prevalent here. As is the case with TAV VACUUM FURNACES SPA, such collaborations help producers of 3D printers and research centres/universities define post-processing standards and constantly improve the furnace features in terms of performance, productivity and quality on the 3D printed parts.
Resources:
Main contribution: Interview with Andrea Cassani, Sales Director at TAV VACUUM FURNACES SPA.
External contributions: SECO/WARWICK S.A. – Desktop Metal – Nabertherm – General Kinematics
This exclusive feature has first been published in the 2021 July/August Edition of 3D ADEPT Mag.