Combien de fois avez-vous entendu dire que les start-ups sont le moteur de l’industrie de la fabrication additive ? Assez certainement pour savoir que nous devons garder un œil sur ces entrepreneurs qui peuvent devenir la prochaine licorne du secteur.
Même si nous comprenons la nécessité pour les start-ups de rester en mode furtif jusqu’à ce que leur technologie soit suffisamment prête pour être officiellement introduite dans l’industrie, nous ne pouvons-nous empêcher de féliciter ces start-ups qui ont été créées au milieu de la pandémie de Covid-19. Bravo à ces douze start-ups qui, selon les mots de Winston Churchill, n’ont pas laissé « une bonne crise se perdre ».
1. F3nice
Fondée en mai 2020, dans l’un des pays les plus touchés par la pandémie, F3nice est l’idée de Luisa Elena Mondora et Matteo Vanazzi. Les deux cofondateurs ont eu l’idée de F3nice en 2019, à la suite d’une analyse dans les industries du pétrole et du gaz. Avec le démantèlement des actifs offshore pour les plus anciens champs pétroliers de la mer du Nord, et l’inventaire numérique pour la production à la demande et « juste à temps » de pièces de rechange, ils ont étudié les possibilités d’utiliser la ferraille de grande valeur issue du démantèlement offshore pour alimenter un projet d’économie circulaire.
F3nice – dont la prononciation est similaire au mot italien « Fenice« , qui signifie « phénix » (l’oiseau qui obtient une nouvelle vie en naissant des cendres de son prédécesseur) – a pour ambition de faire honneur à son nom en s’approvisionnant en ferraille et en pièces désaffectées et en les transformant en poudre métallique imprimable en 3D.
Le projet de l’entreprise a pris de l’ampleur au fil du temps et a suscité l’intérêt d’Equinor Ventures qui a signé une lettre d’intention avec l’équipe. Dans le cadre de ce contrat, le producteur de matériaux traitera les déchets d’Equinor, et la matière première qui en sera issue, sera utilisée pour imprimer des pièces destinées à la mise en service du champ Johan Castberg, près de Hammerfest, par Fieldmade – dans un véritable écosystème d’économie circulaire.
La start-up a expliqué dans une interview à 3D ADEPT Media que sa poudre « est identique à toute autre poudre de haute qualité produite avec la technologie VIGA et peut être réutilisée pendant le processus d’impression autant de fois [que l’alliage le permet]. La valeur ajoutée est qu’une fois que la poudre est considérée comme « épuisée », l’équipementier peut contacter F3nice et demander qu’elle soit recyclée au lieu d’avoir à l’éliminer (à un coût élevé) comme un déchet dangereux. F3nice peut fournir ce service non seulement pour ses produits mais aussi pour n’importe quelle poudre »
2. SphereCube
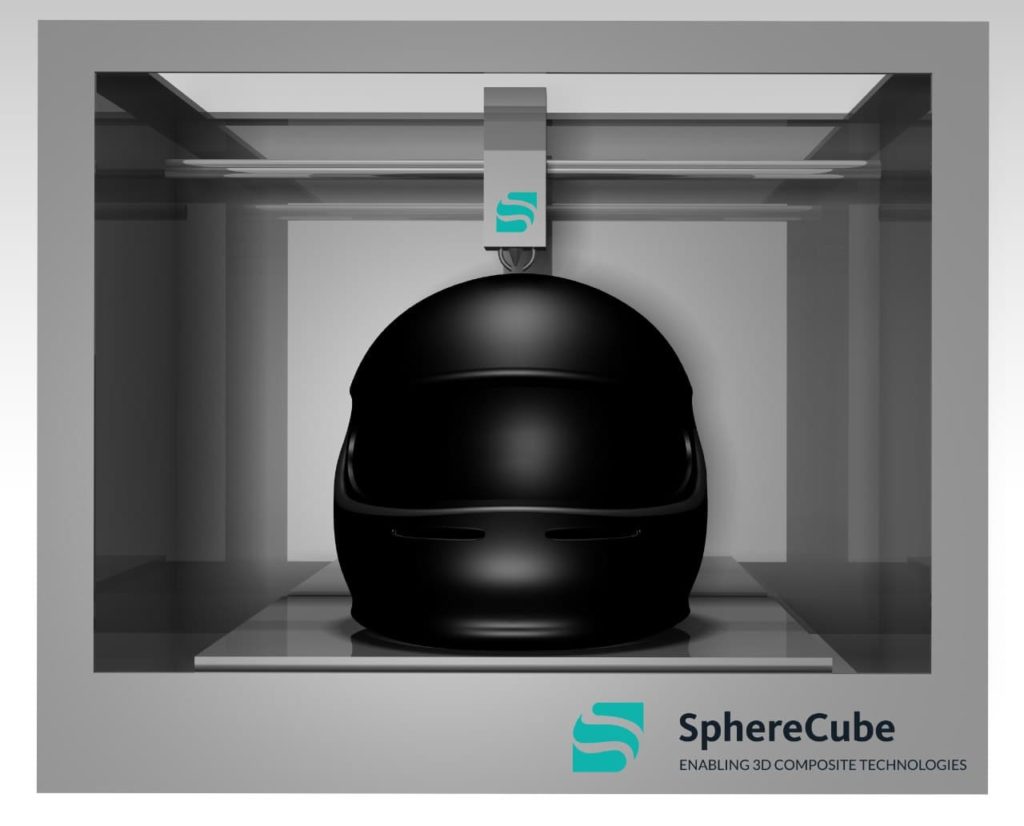
Vous vous souvenez que nous vous avions dit que les jeunes entreprises avaient la possibilité de réfléchir à un modèle économique qui tienne compte des préoccupations environnementales dès le début de leur aventure ? Eh bien, SphereCube a décidé de jouer son rôle dans ces préoccupations environnementales au niveau de la fabrication, en se débarrassant des déchets de traitement des composites et des moules, afin de réduire l’impact environnemental de la production de composites.
Cette start-up spécialisée dans l’impression 3D est une spin-off de l’Université polytechnique des Marches (UNIVPM, Ancône – Italie) qui développe des imprimantes 3D capables de fabriquer des objets composites à l’aide de résines thermodurcissables et de fibres de renforcement continues.
« Grâce à l’interaction d’une source de chaleur avec les matières premières impliquées dans le processus, le système de SphereCube permet la production de composants en matériau composite avec un renforcement en fibres continues et une matrice thermodurcissable. Ce processus de production innovant est capable de créer automatiquement des produits utilisant des matériaux composites de haute performance, sans limitations géométriques », a déclaré la société à 3D ADEPT Media.
La fabrication d’imprimantes 3D composites connectées, moins consommatrices d’énergie et capables de traiter des matériaux biocompatibles, est selon l’entreprise, une étape clé pour aider les industries à construire une chaîne d’approvisionnement 100% durable.
SphereCube a déposé son premier brevet « Méthode et système d’impression 3D de matériaux composites » (brevet italien n. n. 102021000006800) et a déposé sa marque européenne.
En 2022, l’accent sera mis sur le développement de la conception et de la fabrication du produit minimum viable et le retour d’information des clients permettra de valider davantage la solution technologique de l’entreprise.
3. Replique
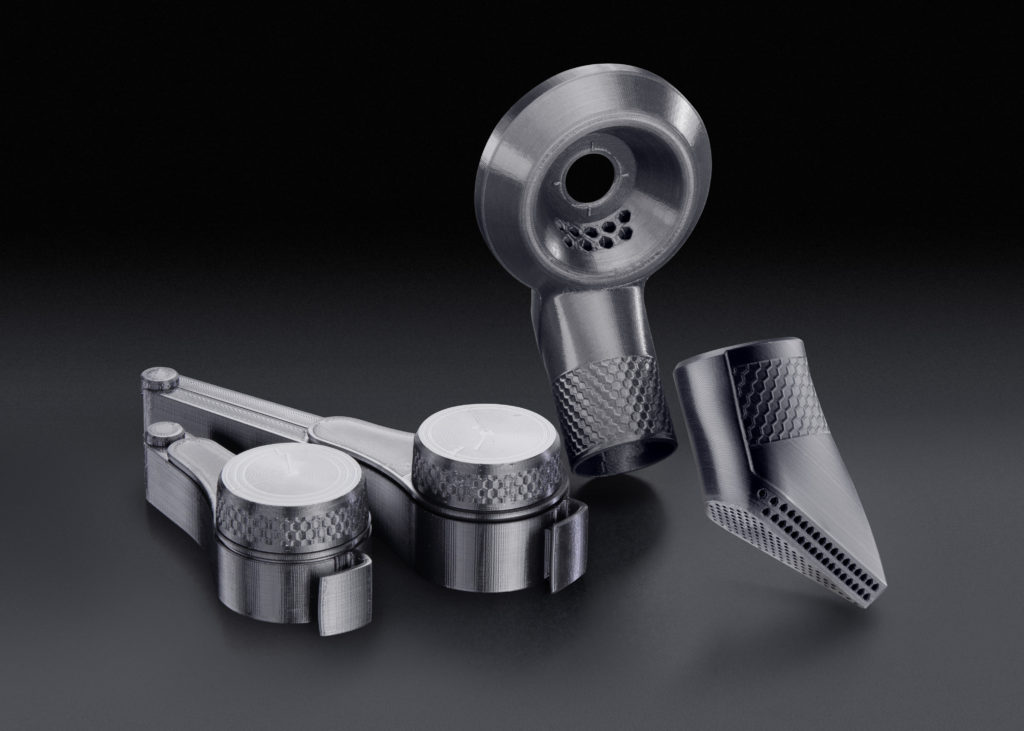
Replique, une entreprise de Mannheim issue de l’incubateur d’entreprises Chemovator de BASF, a bénéficié d’un certain engouement médiatique lorsqu’elle a annoncé un partenariat avec Miele, un fabricant allemand d’appareils ménagers. Selon les termes du partenariat, l’entreprise reçoit le droit exclusif de produire et d’expédier des accessoires imprimés en 3D de haute qualité de Miele en utilisant son réseau de production décentralisé.
Fondée en 2020 par János Váradi, le Dr Henrike Wonneberger et le Dr Max Siebert, l’entreprise fournit une plateforme d’impression 3D industrielle qui permet aux équipementiers de fournir des pièces à la demande à leurs clients grâce à un réseau d’impression 3D mondial, décentralisé et sécurisé. Elle entre sur un marché qui vaut plus de 500 milliards de dollars et qui offre des possibilités de revenus avec des marges nettement plus élevées que la vente de nouveaux services.
De la qualification des pièces imprimables en 3D, à l’inventaire numérique et au réseau de production, l’entreprise offre une solution plus large que ce que l’on voit habituellement sur le marché.
Pour la production industrielle, Replique utilise son réseau mondial de bureaux de services de fabrication industrielle agréés pour la qualité. Grâce à cette solution, les équipementiers réduisent leurs coûts totaux de propriété tout en augmentant leur flexibilité. Sans compter qu’ils peuvent offrir de meilleurs services après-vente à leurs clients, les pièces étant toujours disponibles, même à la fin du cycle de vie du produit ; ils gagnent ainsi des avantages concurrentiels.
Parmi les entreprises qui ont déjà bénéficié des services de Replique, on compte des équipementiers de l’industrie automobile, et récemment Siena Garden, un expert dans la catégorie des outils et des meubles de jardin.
4. Marklix
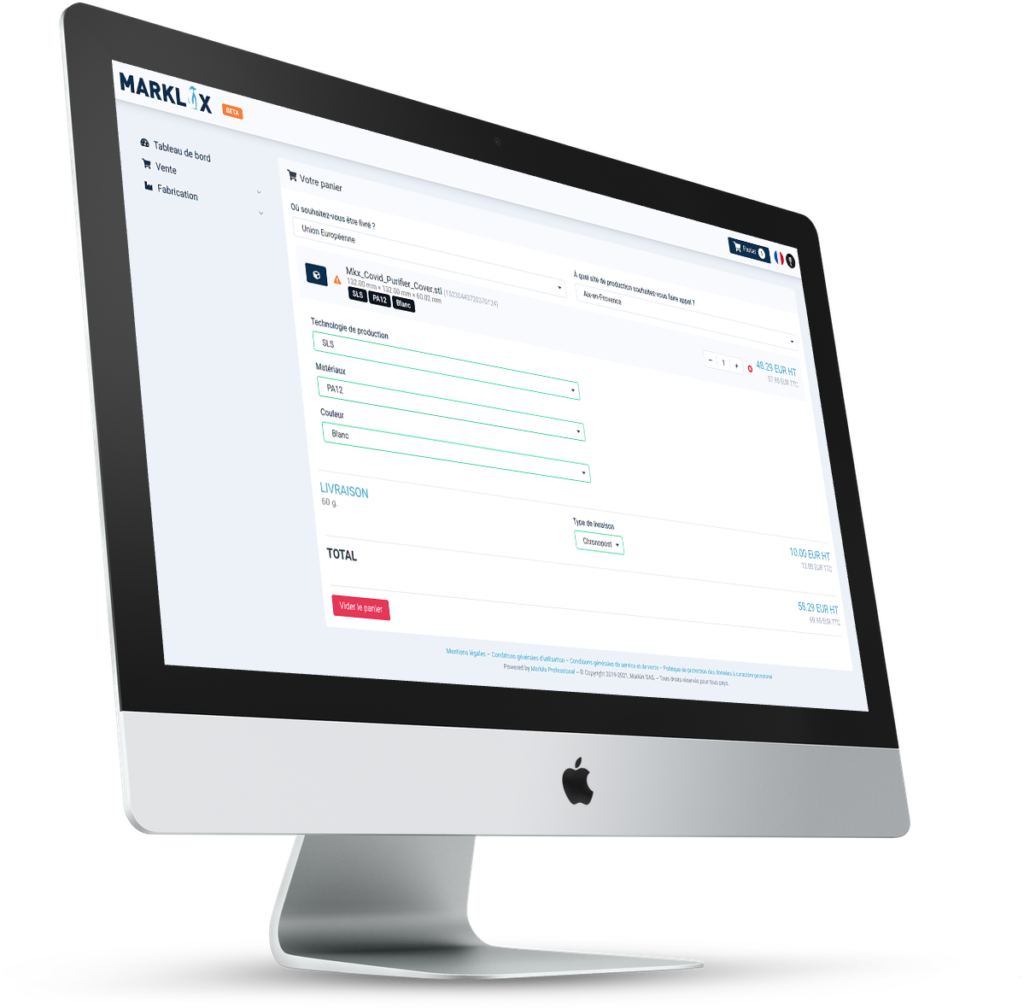
Toujours dans le domaine des pièces détachées, une autre start-up a été fondée l’année dernière en France – en février 2020 précisément, avec pour mission de rendre « l’obsolescence obsolète« . Cette baseline originale fait comprendre rapidement à tout expert de l’industrie de la FA que Marklix permet aux industriels de qualifier et distribuer des pièces détachées en produisant à la demande et localement par impression 3D.
Leur parcours a commencé par le développement d’une « place de marché », où l’idée était de pouvoir trouver toutes les pièces de tous les fabricants, par exemple une pièce d’aspirateur, et ainsi permettre aux particuliers de réparer leur aspirateur sans avoir à changer tout l’appareil. Deux défis sont apparus au cours de ce projet : le prix des pièces était trop élevé – il était souvent moins cher d’acheter un nouvel appareil que de commander une pièce -, les pièces n’étaient pas numérisées, ce qui signifie que l’on ne pouvait pas les imprimer en 3D d’un simple clic.
Pour surmonter ces obstacles, l’équipe de Marklix a décidé de développer de nouvelles solutions logicielles :
- La première solution logicielle s’attaque au problème du prix des pièces détachées en permettant aux fabricants d’être plus compétitifs et de gagner du temps.
« Il s’agit d’un ERP/MES qui leur permet de gérer leur parc de machines, d’éditer des factures et des bons de livraison, de prendre des commandes en ligne tout en laissant le choix au fabricant de laisser le client payer directement ou non, en sécurisant les fichiers, etc. Les retours que nous avons reçus indiquent un gain de temps moyen de 40 minutes/commande et une meilleure visibilité et efficacité pour leur entreprise. Nos partenaires sont donc plus compétitifs, ce qui rend les prix plus attractifs », explique l’entreprise.
- La deuxième solution consiste en la digitalisation des stocks, ce qui est d’une importance cruciale pour certaines entreprises en raison du coût élevé des stocks de pièces détachées. Dans cette optique, cette solution logicielle permet aux ingénieurs de réaliser cinq tâches principales : identification des pièces imprimables en 3D grâce à l’IA, qualification des pièces avec les bons matériaux et la bonne technologie de production, calcul du ROI (d’un point de vue économique et écologique), transfert des pièces ayant passé les 3 premières étapes sur un catalogue en ligne et impression. Cette dernière tâche peut être réalisée en interne ou en externe si l’entreprise ne dispose pas des moyens de production.
Suite à l’accueil positif qu’ils ont reçu lors du lancement de leur premier logiciel, l’équipe Marklix dirigée par Pierre-Jacques LYON et Thomas BOULLIER, respectivement CEO et CTO, ne compte pas se reposer sur ses lauriers. Ils continueront à répondre aux besoins des fabricants d’imprimantes 3D et des producteurs de pièces, avec leur chien Reynolds, un jeune berger blanc suisse qui a la lourde responsabilité de créer et de maintenir une atmosphère propice au travail.
4. Addiblast
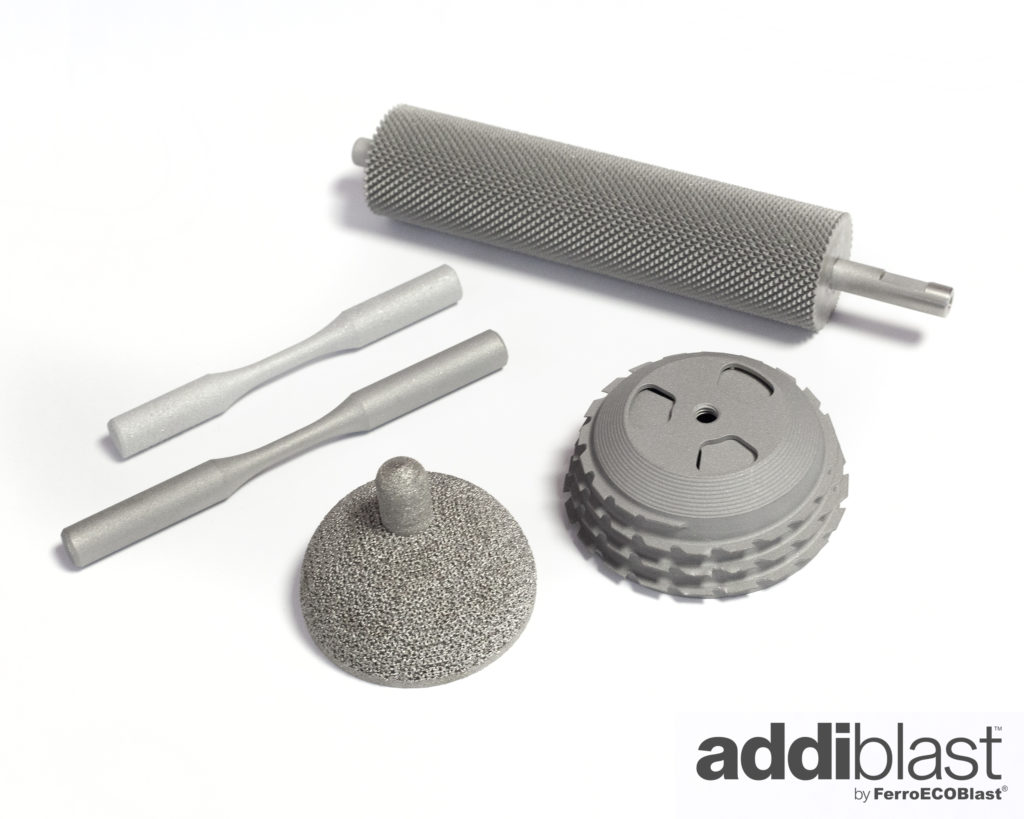
Ce n’est pas tous les jours qu’on parle de FA en Slovénie… et la start-up qui nous fait envisager plus qu’un simple voyage touristique dans ce pays aux grottes époustouflantes est Addiblast. Cette équipe nous fait explorer le domaine du processus de fabrication que tout opérateur redoute : le post-traitement. Fondée en 2020, la start-up fait partie de FerroECOBlast® Europe, une entreprise familiale qui s’est forgée une solide réputation en résolvant les problèmes de traitement de surface les plus exigeants. Le portefeuille de la société mère comprend un large éventail de solutions telles que le sablage à l’air, le grenaillage, les solutions d’émaillage et de revêtement, le nettoyage à la glace sèche et à la neige sèche, ainsi que le jet d’eau UHP.
Addiblast tire donc parti de plus de cinq décennies d’expérience de sa société mère pour fournir à l’industrie de la FA un portefeuille comprenant le grenaillage, l’enlèvement de poudre et le recyclage.
La société a fait ses débuts à Formnext cette année en présentant les capacités de ses trois principaux produits :
– La station BAM, une solution de traitement de surface conçue pour divers processus tels que le lissage, l’ébauche, l’unification et le polissage des surfaces, la suppression des structures de support et le retrait précis de la poudre de structures extrêmement complexes. Elle est fabriquée en acier inoxydable et convient à tous les types de grenaille.
– La série MARS (Metal Additive Removal System)
Disponibles en trois options, ces machines permettent l’enlèvement des poudres de pièces complexes ou de grandes dimensions. Chaque machine dispose d’un système de communication et d’échange de données avec les autres machines du constructeur. La principale différence entre MARS01, MARS02 et MARS03 est que cette dernière est une solution entièrement automatisée, antidéflagrante et conforme à la directive ATES. En outre, en permettant un flux d’atmosphère inerte en boucle fermée, la machine peut maintenir un niveau d’oxygène inférieur à 2 %. Cela permet d’éviter la contamination et l’oxydation de la poudre pendant le dépoudrage et le conditionnement, et porte la réutilisation de la poudre à de nouveaux niveaux.
– La dernière née de cette gamme est la STAR (Station for Transfer and Additive Recycling). Conçue comme une station centrale qui contrôle en continu et automatiquement le transfert pneumatique, le recyclage et le conditionnement de la poudre, cette machine permet une connexion directe avec l’imprimante 3D et d’autres équipements. C’est son principal avantage par rapport aux autres solutions du fabricant. Elle peut également être utilisée pour purifier la poudre vierge et, comme la série MARS, elle empêche la contamination et l’oxydation de la poudre pendant le dépoudrage et le conditionnement, et porte la réutilisabilité de la poudre à de nouveaux niveaux.
6. NematX AG
La prochaine startup de cette liste est une spin-off de l’ETH Zurich fondée par Raphael Heeb et Silvan Gantenbein. Avec l’ambition d’inaugurer la prochaine génération d’impression 3D avec des polymères de haute performance et de dépasser de manière significative les références actuelles dans les composants d’utilisation finale correspondants, la start-up suisse cible toutes les industries verticales dont la fabrication de pièces doit résister à des conditions environnementales difficiles.
NematX AG, qui a été l’un des lauréats du concours Formnext 2020 pour les start-up, développe ce qu’elle appelle une technologie d' »impression 3D nématique » qui vise à aider les industries à rendre leurs activités à faible volume plus rentables et durables.
« Les polymères à cristaux liquides – en abrégé LCP = Liquid crystal polymers – appartiennent à la famille des matériaux plastiques de haute performance. Par rapport aux thermoplastiques classiques tels que le PEEK ou le PEI, les molécules de LCP sont comparativement courtes et rigides et possèdent des propriétés uniques qui rendent leur utilisation dans l’impression 3D très intéressante. À l’état fondu, les LCP adoptent un ordre de courte portée, semblable à des paquets de rondins de bois flottant sur une rivière », explique l’entreprise.
La technologie d’impression 3D Nematic est donc basée sur l’extrusion de matériaux (impression 3D FFF). « Pendant l’impression, nous pouvons aligner ces paquets individuels LCP le long de la direction d’impression pour produire des pièces aux propriétés mécaniques et thermiques inégalées issues de la fabrication additive de polymères », explique la société NematX AG sur son site web.
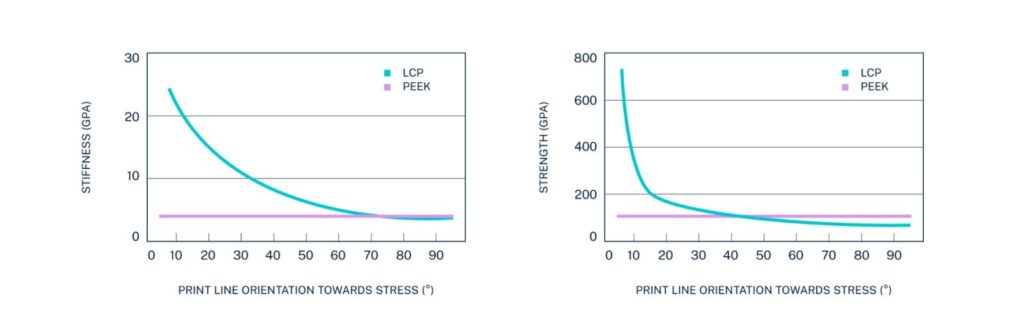
« En contrôlant l’alignement moléculaire de nos matériaux d’impression 3D LCP, nous obtenons une rigidité et une résistance supérieures grâce à l’impression 3D polymère. Dans le sens de l’impression, nous pouvons atteindre des modules d’Young allant jusqu’à 25 GPa et des résistances ultimes à la traction de 650 MPa. Dans le sens transversal, les valeurs de rigidité et de résistance d’autres thermoplastiques tels que le PEEK ou le PLA sont atteintes », souligne l’équipe.
7. Additive Drives GmbH
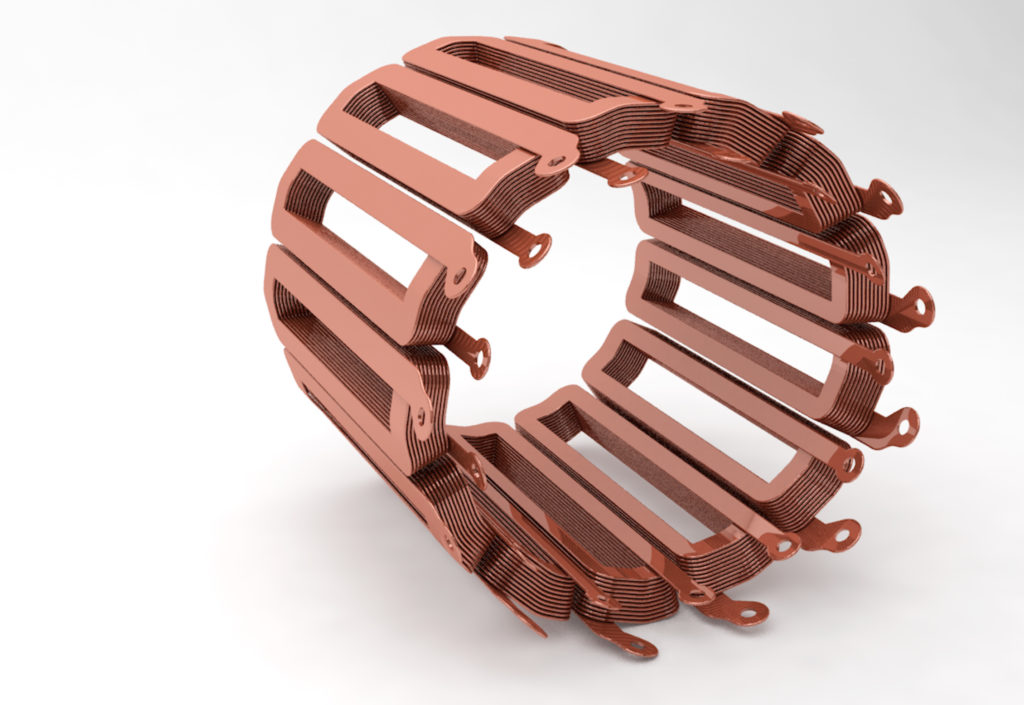
Légende : Bobines simples. Image : Additive Drives GmbH
Peu d’entreprises peuvent s’enorgueillir d’avoir levé des fonds au cours des trois premiers mois de son existence, Additive Drives GmbH le peut et le meilleur dans tout ça, c’est que l’entreprise l’a fait pendant le premier pic de la pandémie de Covid-19 l’année dernière, alors que l’économie n’était pas au mieux.
Fondée par Philipp Arnold, Jakob Jung et Axel Helm, Additive Drives GmbH développe et fabrique des composants de moteurs électriques par fabrication additive. Grâce à un investissement d’amorçage de 1,5 million de dollars d’AM Ventures Holding GmbH, Additive Drives GmbH a l’ambition de dynamiser le marché des moteurs électriques avec de nouvelles applications.
« Jakob et moi venons tous deux du secteur des applications. Nous avons développé des robots électroniques dans l’ancienne entreprise automobile pour laquelle nous travaillions. Ingénieurs de formation, nous avons acquis une grande expérience du cuivre et des machines de fabrication additive. Après une recherche approfondie, nous avons réalisé que la combinaison de la fabrication additive et du cuivre pouvait conduire non seulement à des cycles de développement et de test plus courts pour les moteurs électriques, mais aussi à des applications plus performantes. Après quelques essais réussis, nous avons contacté Axel Helm, qui possède une solide expérience des processus de fabrication et de l’industrialisation. Son expérience dans le traitement du cuivre et l’optimisation des procédés de FA est déterminante pour définir le type d’applications sur lesquelles nous pourrions travailler. Nous avons donc décidé de combiner nos forces respectives pour faire d’Additive Drives GmbH une entreprise viable », a déclaré Arnold dans une interview à 3D ADEPT Media.
Avec 13 employés à son bord, Additive Drives GmbH a pour ambition d’améliorer les performances des moteurs électriques jusqu’à 45 % en se concentrant sur les enroulements en cuivre, le principal composant d’un moteur électrique. La FA fait définitivement partie de ce jeu, car la fabrication directe à partir des données CAO permet de raccourcir les cycles de développement et d’essai. En outre, elle ne compromet pas les paramètres des matériaux et offre au contraire une conductivité électrique du même niveau que la production conventionnelle.
Alors que l’équipe d’Additive Drives GmbH est prête à vivre de nouvelles aventures dans ce domaine d’application, il convient de noter qu’elle a remporté le Gründerpreis Sachsen/ Prix de la jeune entreprise la plus innovante de Saxe, un État libre situé dans le sud-est de l’Allemagne.
Ce que l’espace Start-up a réservé pour l’année 2021 …
8. Axtra 3D
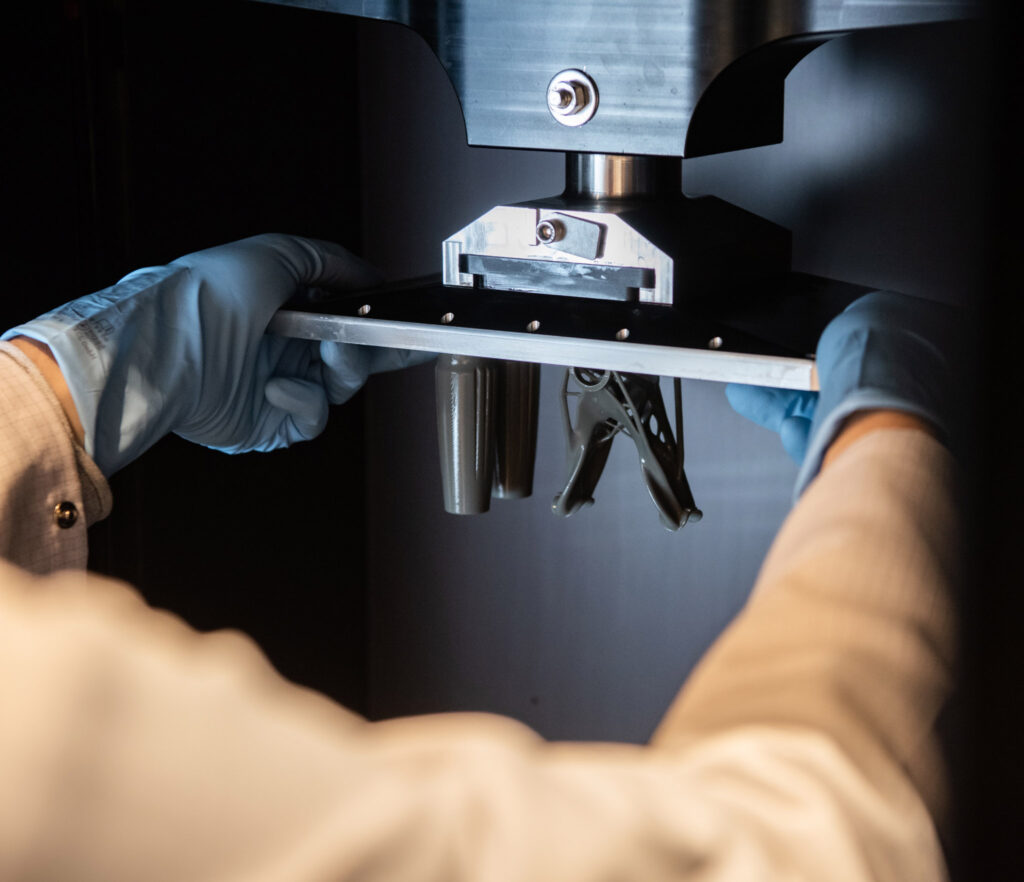
On trouvera rarement une start-up qui a fait un véritable coup d’éclat lors de ses débuts sur la scène internationale de l’industrie de la FA. Axtra 3D l’a fait à Formnext 2021, avec le lancement d’une imprimante 3D unique. Nous en avons récemment appris plus sur l’innovation de cette entreprise et deux choses nous ont vraiment marqués : le temps de développement du produit qui ne prend que 9 mois ainsi que la technologie. Cette solution technologique est le résultat d’une collaboration entre la plateforme de fabrication à la demande Xometry et Axtra3D, un développeur de solutions avancées de fabrication additive utilisant l’optoélectronique.
Ensemble, ils ont créé une imprimante 3D basée sur une technologie brevetée de photo-synthèse hybride (HPS = Hybrid PhotoSynthesis), qui pourrait combiner les avantages de la SLA, de la DLP et du LCD. L’enjeu est d’autant plus important quand on sait que, lorsqu’il s’agit d’impression 3D en résine, les opérateurs hésitent souvent entre les avantages et les inconvénients du SLA, du DLP et du LCD. Selon Xometry, choisir entre ces trois solutions nécessite de faire des compromis, soit sur la vitesse d’impression et la résolution (DLP/LCD), soit sur la qualité de surface et la zone d’impression (SLA).
Alors, qu’est-ce qui rend la photo-synthèse hybride (HPS) exceptionnelle ?
La HPS permet un processus d’impression avec une résolution fine et offre des vitesses d’impression élevées et une excellente qualité de surface, même avec de grandes surfaces d’impression. Le procédé combine deux sources lumineuses dans un assemblage personnalisé (DLP et laser) afin de créer un moteur lumineux harmonisé qui exploite efficacement la puissance des deux sources.
« Dans notre technologie HPS, le laser définit la résolution et, par conséquent, la HPS offre une meilleure résolution et une meilleure reproductibilité des détails qu’une DLP standard », explique Gianni Zitelli, l’un des fondateurs d’Axtra3D.
Le nouveau procédé offre donc la vitesse de la DLP/LCD avec la qualité de surface et l’évolutivité de la SLA, ainsi qu’une résolution ultrafine, une impression continue et des capacités de performance de pièces isotropes.
« Les utilisateurs ont souvent des coûts de finition de surface élevés », déclare Praveen Tummala, l’autre cofondateur de la société, « mais avec la qualité de surface fine et la résolution offertes par HPS, ils peuvent économiser du temps et de l’argent car les pièces imprimées en 3D ne nécessitent pas de finition de surface après impression ».
Où Xometry entre-t-elle en jeu ?
Comme l’histoire le raconte, le projet a commencé au début de 2021 avec l’objectif de lancer cette imprimante 3D lors de l’édition Formnext 2021 . « Nous pensions qu’il nous faudrait environ 18 mois pour mener à bien un tel projet« , explique Tummala. « Grâce à l’équipe et à nos partenaires en Europe, cela ne nous a pris que 9 mois« .
En août, l’équipe italienne a lancé la première simulation du système optique complexe, qui a été un succès retentissant. Cette percée a ensuite accéléré l’ensemble du processus de production. « Une grande partie du mérite revient à Xometry, car ils ont pu livrer environ 2 000 pièces en 6 semaines, un délai extrêmement exigeant », déclare Zitelli. « Nous avons accès à des fournisseurs de CNC en Italie, mais cela n’aurait pas été une décision stratégique pour notre entreprise. Travailler avec Xometry nous donne accès à des milliers de fournisseurs dans le monde entier – c’est la véritable valeur de notre collaboration ».
Afin de terminer le projet à temps pour le forum, Axtra3D a fait appel à Xometry pour produire chaque pièce en aluminium usinée par CNC utilisée pour assembler l’imprimante, des très petits composants pour le système d’éclairage aux éléments pour la base de l’imprimante. « Nous ne pouvons pas imaginer un autre partenaire qui aurait pu livrer les pièces à temps pour nous permettre de lancer le produit et de l’exposer à Formnext », déclare Tummala. «
L’équipe d’Axtra3D a travaillé en très étroite collaboration avec Liana Zedginidze de Xometry pendant tout le processus de production. « Nous sommes très redevables à Liana pour son soutien à notre projet. Elle était disponible pour nous 24 heures sur 24 et a veillé à ce que les pièces commandées soient produites et livrées à temps », a déclaré M. Zitelli.
La prochaine étape pour les deux partenaires est maintenant de produire 10 imprimantes 3D bêta d’ici juin 2022 afin de lancer leur produit sur le marché industriel.
9. Additive Appliances
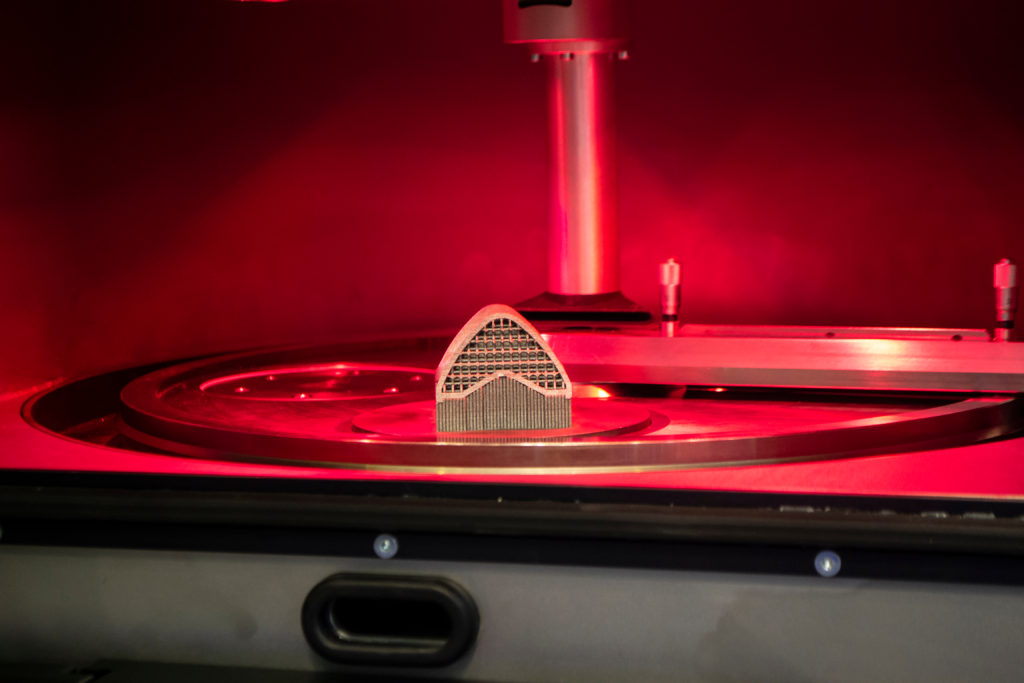
Par la suite vient Additive Appliances, une start-up qui a été constituée en avril 2021, dans le but de développer la prochaine génération d’appareils électroménagers tels que les cafetières, et les produits de soins personnels. Dès le début, l’entreprise a reçu le soutien de business angels, dont une entreprise dérivée d’une université spécialisée dans la dynamique des fluides computationnelle et l’optimisation de la topologie.
En collaboration avec Kilometro Rosso, un centre d’innovation privé en Italie, Additive Appliances a obtenu une subvention de l’UE via le premier appel ouvert mondial du centre d’innovation numérique. Le financement permettra d’accélérer le développement d’Additive Appliances pour son projet « Échangeur de chaleur imprimé en 3D pour les machines à café domestiques« .
La start-up italienne bénéficie de plusieurs décennies d’expérience dans les applications d’impression 3D telles que les échangeurs de chaleur. Dans ce cas, elle explique que le contrôle de la température et de la pression de l’eau est essentiel pour extraire le meilleur du café et la solution permet une préparation plus efficace et durable de la boisson.
Les équipements ménagers électrothermiques contrôlent les variables du processus en intégrant plusieurs composants (difficilement recyclables), tandis que les dispositifs thermomécaniques traditionnels ne les contrôlent pas directement, ce qui pose des problèmes de qualité et de répétabilité. Actuellement, les consommateurs doivent faire un compromis entre la qualité et la durabilité, indique un communiqué de presse de la société.
Il est intéressant de noter que pour améliorer les performances, explorer de nouvelles caractéristiques et la personnalisation fonctionnelle, la FA pourrait être utilisée à différents stades du développement du produit, y compris la production d’utilisation finale. Comme nous l’avons vu dans une application partagée par Additive Drives Gmbh, la combinaison de la FA et des processus de fabrication conventionnels permet un meilleur contrôle de la température et de la pression grâce à des échangeurs de chaleur intégrés, conformes, à haut rendement et ultra-compacts.
Cela signifie que de petits lots peuvent, par exemple, être conçus pour exalter des variétés de café spécialisées, selon les préférences individuelles des consommateurs. D’autre part, une seule pièce de mécanique peut remplacer les composants électroniques auxiliaires, ce qui réduit considérablement l’empreinte carbone du cycle de vie de l’équipement, de la production au recyclage. En un mot, une expérience écologique du café.
USA Tech, l’espace de vie pour les technologies additives de Kilometro Rosso, sera un partenaire crucial pendant l’expérience de DIHWorld. Son infrastructure d’impression 3D aidera l’entreprise à tirer rapidement parti de la technologie et à effectuer des évaluations approfondies des processus grâce à des systèmes de surveillance en temps réel – ce qui accélérera l’optimisation de la fabrication, conclut l’entreprise.
10. Vispala Technologies
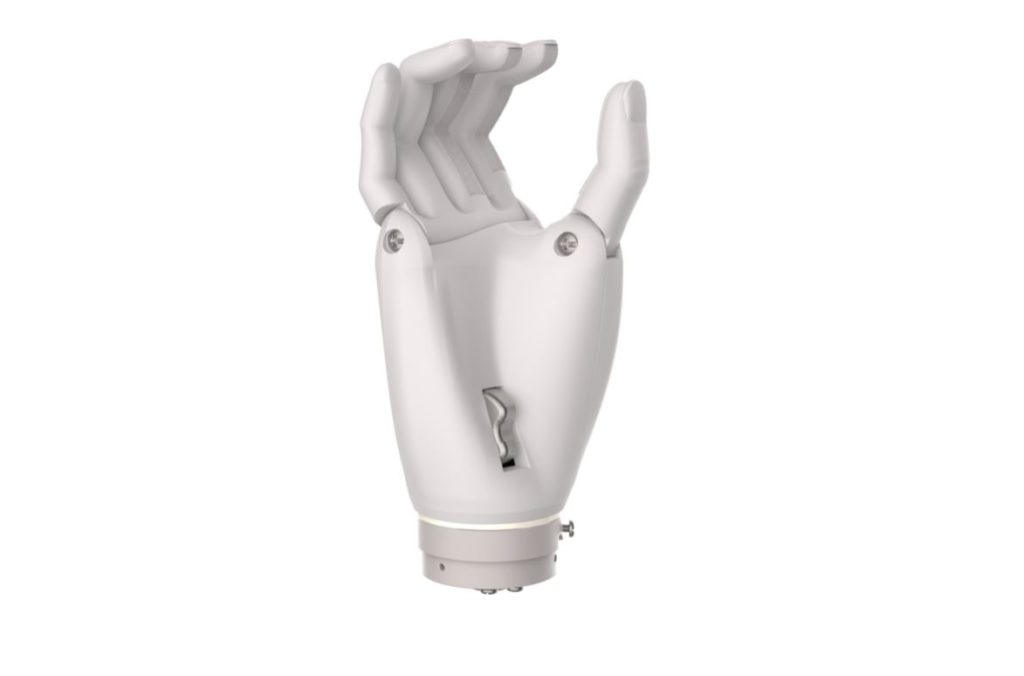
Cette entreprise basée en Inde a un impact sur la vie des personnes handicapées grâce à sa prothèse de main imprimée en 3D iGrip. L’entreprise qui développe des orthèses imprimées en 3D personnalisées, des membres artificiels imprimés en 3D et des prothèses, a fait une entrée officielle sur la scène internationale de l’industrie de la FA en participant au « Formnext Start-up Challenge 2021 ».
L’entreprise s’est distinguée en remportant le prix AM Ventures Impact Award, qui récompense l’approche du gagnant en matière de durabilité, une approche qui tient compte des 17 objectifs de développement durable des Nations unies, des considérations environnementales (telles que l’énergie verte et la conservation des ressources) et des aspects sociaux (par exemple, l’éducation et l’égalité).
L’iGrip de Vispala est une prothèse de main alimentée par le corps, abordable et légère, qui aide les patients à effectuer des travaux liés à leur vie quotidienne.
« Chez Vispala, nous relevons le défi de moderniser le secteur des prothèses grâce à la technologie et à l’innovation et de redonner aux utilisateurs 50 % ou plus de leurs moyens de subsistance grâce à des solutions confortables et esthétiques« , a déclaré Dipak Basu, CEO de Vispala Technologies. « Simultanément, nous construisons une entreprise sociale durable pour étendre notre travail. »
7. Nobula
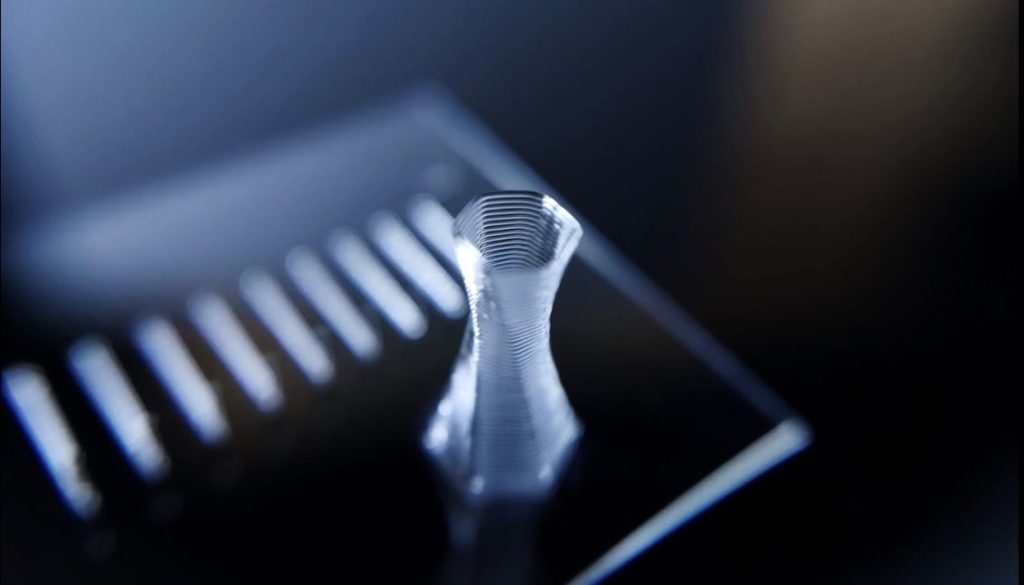
Nobula est une autre startup que le Formnext Start-up Challenge 2021 a mis en lumière. Cette startup d’impression 3D sur verre est une spin-off de KTH en Suède qui apporte beaucoup de diversité dans l’éventail des technologies de FA déjà disponibles sur le marché.
Leur innovation ? Une imprimante 3D en verre Nobula™ basée sur le dépôt laser direct sur verre (DGLD™ = Direct Glass Laser Deposition) qui permet de produire des structures 3D complexes en verre.
La société a déposé deux brevets, l’un pour l’imprimante 3D en verre et l’autre pour la technologie du matériau d’impression, ce qui lui permettra de fournir une impression 3D en verre personnalisée pour la science, le développement et la production.
On peut s’attendre à ce que l’entreprise finalise son prototype d’imprimante et lance le premier modèle avant l’été 2022.
8. AM Entrepreneur
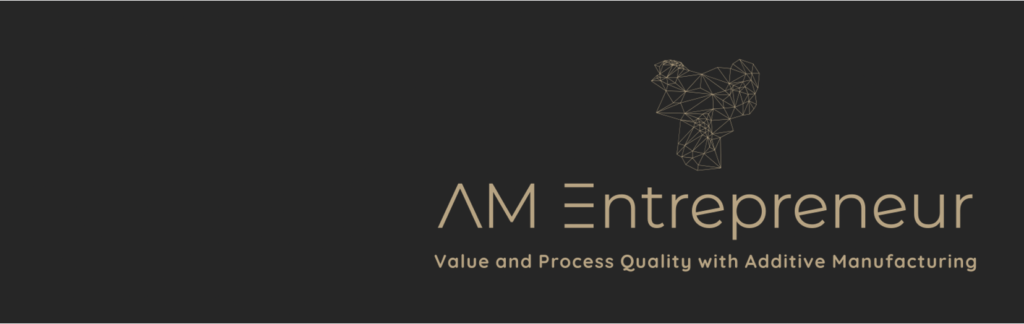
Enfin, cette start-up basée en Allemagne vise à « normaliser la mise en œuvre de la valeur technologique de la FA au sein de modèles commerciaux rentables et durables« . Derrière cette vision ambitieuse se cache Gregor Reischle, qui a lancé et fait avancer la feuille de route de la FA chez TÜV SÜD.
La création d’AM Entrepreneur est partie d’un constat :
« La fabrication distribuée au sein des modèles d’entreprise contribuera à atteindre nos objectifs en matière d’émissions de CO2 et ouvrira de nouveaux modèles d’entreprise numériques et de nouveaux potentiels de positionnement stratégique. Dans la structure actuelle des « business units » des entreprises, nous constatons souvent un manque d’ADN entrepreneurial transversal, ce qui entraîne souvent la stagnation des projets. La complexité de la conception de l’entreprise dans le domaine de la fabrication additive exige strictement la collaboration entre toutes les unités opérationnelles et tous les esprits« , ce qui est une capacité qu’AM Entrepreneur veut établir au sein des entreprises industrielles.
Au sein d’AM Entrepreneur, Reischle vise donc à fournir une incubation de l’esprit d’entreprise pour toutes les Start UP de la FA et les équipes intrapreneuriales, à fournir des actifs numériques qui permettront une mise en œuvre évolutive des processus de FA tout en assurant la prévisibilité du retour sur investissement. Enfin, il fournira également des services de conseil, de formation, d’encadrement et d’assistance pratique pour surmonter les problèmes de qualité, d’approbation et de conception commerciale auxquels les industries sont souvent confrontées.
Jusqu’à présent, AM Entrepreneur a déjà fourni des rapports sur les résultats d’ateliers et d’évaluations, des évaluations de fournisseurs et des rapports GAP basés sur les normes de qualité, de santé et de sécurité de l’AM, telles que les normes ISO/ASTM 52901 et 52920, ainsi que le coaching de « l’AM Innovation TEAM » pendant la « phase de conception commerciale » (programme de plusieurs semaines). Il a déjà soutenu l’installation de systèmes de FA dans des environnements réglementés, conformément aux exigences de la CE ou de l’assurance qualité – évaluations basées sur la norme ISO/ASTM 52930 et autres.
« Après une vingtaine d’années de carrière en entreprise, j’ai finalement réussi à me retirer et à créer une entreprise. La liberté de pouvoir voyager à nouveau, après avoir été vacciné, et de participer à l’exposition FormNext en retrouvant mes amis du secteur de la FA. Mon activité de conseil et de création d’un incubateur d’entreprises débouche sur de nouveaux modèles économiques et des solutions logicielles rentables. Mon « état d’esprit de créateur pratique », donne aux cadres et aux équipes opérationnelles les moyens de créer de nouveaux modèles commerciaux fructueux, tout en incubant les valeurs de la FA », a déclaré Reischle à 3D ADEPT Media.
Remarques finales
Cet espace « Start-up » montre qu’il y a un plus grand nombre de start-ups qui ont été fondées en 2020 qu’en 2021. Cela révèle la résilience de l’industrie et sa capacité à trouver le bon dans n’importe quelle crise et surtout, cela atteste de la volonté de la FA de créer un modèle économique exclusivement basé sur les applications.
Ce dossier exclusif a été initialement publié dans le numéro de Novembre/Décembre de 3D ADEPT Mag.
N’oubliez pas que vous pouvez poster gratuitement les offres d’emploi de l’industrie de la FA sur 3D ADEPT Media ou rechercher un emploi via notre tableau d’offres d’emploi. N’hésitez pas à nous suivre sur nos réseaux sociaux et à vous inscrire à notre newsletter hebdomadaire : Facebook, Twitter, LinkedIn & Instagram !