Additive Drives GmbH est la première société d’applications de la fabrication additive dans le secteur. Dans cet article, les cofondateurs Philipp Arnold et Jakob Jung donnent un aperçu de l’utilisation de la fabrication additive pour les moteurs électriques.
Peu d’entreprises peuvent s’enorgueillir d’avoir levé des fonds au cours des trois premiers mois de leur existence, mais Additive Drives GmbH le peut et la partie la plus intéressante de l’histoire, c’est que l’entreprise l’a fait lors du premier pic de la pandémie de Covid-19, alors que l’économie n’était pas au mieux.
Si l’obtention d’un tour d’investissement est toujours une grande nouvelle pour une entreprise, quel que soit son secteur d’activité, une conversation avec Arno Held, Chief Venture Officer (CVO) chez AM Ventures – un investisseur en série dans la fabrication additive -, a mis en lumière l’importance pour les investisseurs et les fondateurs en phase de démarrage de comprendre la dynamique du marché de l’industrie dans laquelle ils opèrent.
Selon Held, trois facteurs clés stimulent actuellement le marché de la fabrication additive : le ‘timing’, la chaîne de valeur numérique et les applications. Il est intéressant de noter que, dans la courte liste des entreprises qui ont obtenu des fonds dans le contexte de la pandémie de l’année dernière, Additive Drive GmbH fait ses débuts au bon moment et avec un modèle commercial nouveau : un focus sur les applications de la FA.
Alors, qu’apporte Additive Drives GmbH sur le marché ?
Fondée par Philipp Arnold, Jakob Jung et Axel Helm, Additive Drives GmbH développe et fabrique des composants de moteurs électriques par fabrication additive. Grâce à un investissement d’amorçage de 1,5 million de dollars d’AM Ventures Holding GmbH, Additive Drives GmbH a l’ambition de dynamiser le marché des moteurs électriques avec de nouvelles applications.
« Jakob et moi venons tous deux du secteur des applications. Nous avons développé des robots électroniques dans l’ancienne entreprise automobile pour laquelle nous travaillions. Ingénieurs de formation, nous avons acquis une grande expérience du cuivre et des machines de fabrication additive. Après des recherches approfondies, nous avons réalisé que la combinaison de la fabrication additive et du cuivre pouvait permettre non seulement de raccourcir les cycles de développement et d’essai des moteurs électriques, mais aussi d’obtenir des applications plus performantes. Après quelques essais réussis, nous avons contacté Axel Helm, qui possède une solide expérience des processus de fabrication et de l’industrialisation. Son expérience dans le traitement du cuivre et l’optimisation des procédés de FA est déterminante pour définir le type d’applications sur lesquelles nous pourrions travailler. Nous avons donc décidé de combiner nos forces respectives pour faire d’Additive Drives GmbH une entreprise viable« , nous dit Arnold dès le début.
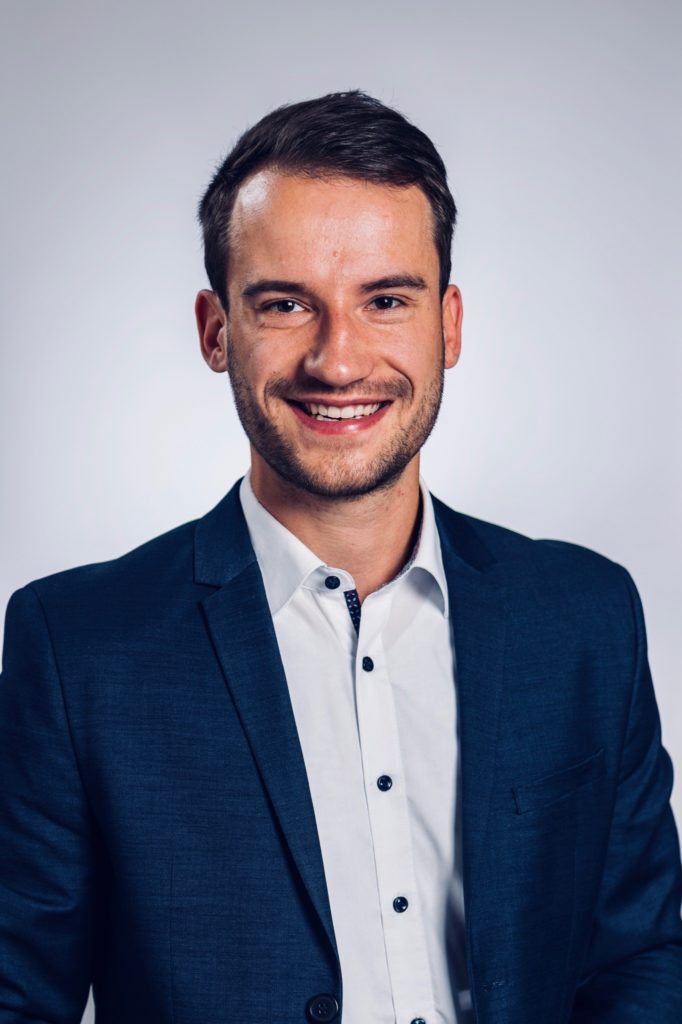
À l’heure où nous écrivons ces lignes, Helm et Jung sont directeurs généraux tandis qu’Arnold est le responsable financier et économique de l’équipe.
Un objectif clé : stimuler le marché des moteurs électriques
Grâce aux progrès rapides de la conception et de la fabrication, la fin du XIXe siècle a vu l’âge d’or des moteurs électriques, avec de nouveaux types de moteurs électriques construits à partir de matériaux améliorés et des technologies de fabrication de l’époque. Au fil du temps, avec l’avancement des processus de fabrication, les technologies de fabrication des années 1800 que l’on appelle aujourd’hui les processus de fabrication conventionnels révèlent un manque de fiabilité et de répétabilité de certains composants de moteurs électriques, en particulier les enroulements de la bobine du moteur.
La fabrication additive pourrait être particulièrement bien placée pour surmonter ce goulot d’étranglement, qui empêche les machines électriques de jouer un rôle crucial dans des secteurs industriels clés tels que l’aérospatiale, l’automobile et d’autres secteurs de l’industrie de la mobilité.
« Chez Additive Drives GmbH, nous ne rejetons pas les capacités des processus de fabrication conventionnels. En fait, nous sommes bien conscients du fait que tout ne peut pas être produit par FA. Toutefois, nous voulons permettre aux industries de tirer parti des possibilités offertes par la conception et la fabrication de moteurs électriques en exploitant les avantages que la FA peut offrir par rapport à la fabrication traditionnelle. Le premier de ces avantages est le temps. Passer d’environ 36 mois de cycle de développement à quelques semaines avec la FA, c’est déjà une raison notable d’envisager la FA, les autres étant la qualité et les performances« , explique Arnold.
Si l’intérêt d’Additive Drives pour la FA est compréhensible, le choix des matériaux dans chaque application est d’une importance capitale pour obtenir les performances de fabrication souhaitées.
Pour ceux qui ne sont pas familiers avec tous les composants d’un moteur électrique, il convient de noter que les enroulements de la bobine du moteur sont un élément central qui contribue à créer un champ électrique dans une machine électrique. Ces enroulements sont généralement constitués d’une série de bobines, qui, elles, sont des fils constitués d’un matériau conducteur entouré d’un matériau isolant.
Cela dit, l’une des principales propriétés électriques que doivent posséder les matériaux destinés à de telles applications est leur conductivité électrique, principale caractéristique reconnue au cuivre mais aussi aux alliages d’argent, d’or ou d’aluminium, tous intéressants à traiter par la technologie de fusion sélective par laser.
Prenant l’exemple des enroulements en cuivre de moteurs électriques fabriqués de manière additive pour un moteur de course, Arnold souligne que le cuivre traité par SLM apporte une performance accrue à la pièce imprimée. L’utilisation de la technologie SLM apporte des facteurs de remplissage de cuivre élevés, un meilleur comportement thermique ainsi qu’un déplacement de puissance optimisé vers le moteur, sans oublier que le processus de fabrication permet d’obtenir des géométries de fil optimisées qui ne sont pas toujours observées avec les processus de fabrication conventionnels.
Jung parle d’un facteur de remplissage du cuivre de 65 % avec la FA, contre 45 % avec les procédés de fabrication conventionnels. De plus, avec la FA, le transfert forcé de la chaleur de l’enroulement vers le noyau laminé empêche la formation de points chauds souvent observés dans les méthodes de fabrication conventionnelles. D’autre part, l’épaisseur variable des conducteurs réduit le déplacement du courant, ce qui permet de maximiser les performances de la pièce.
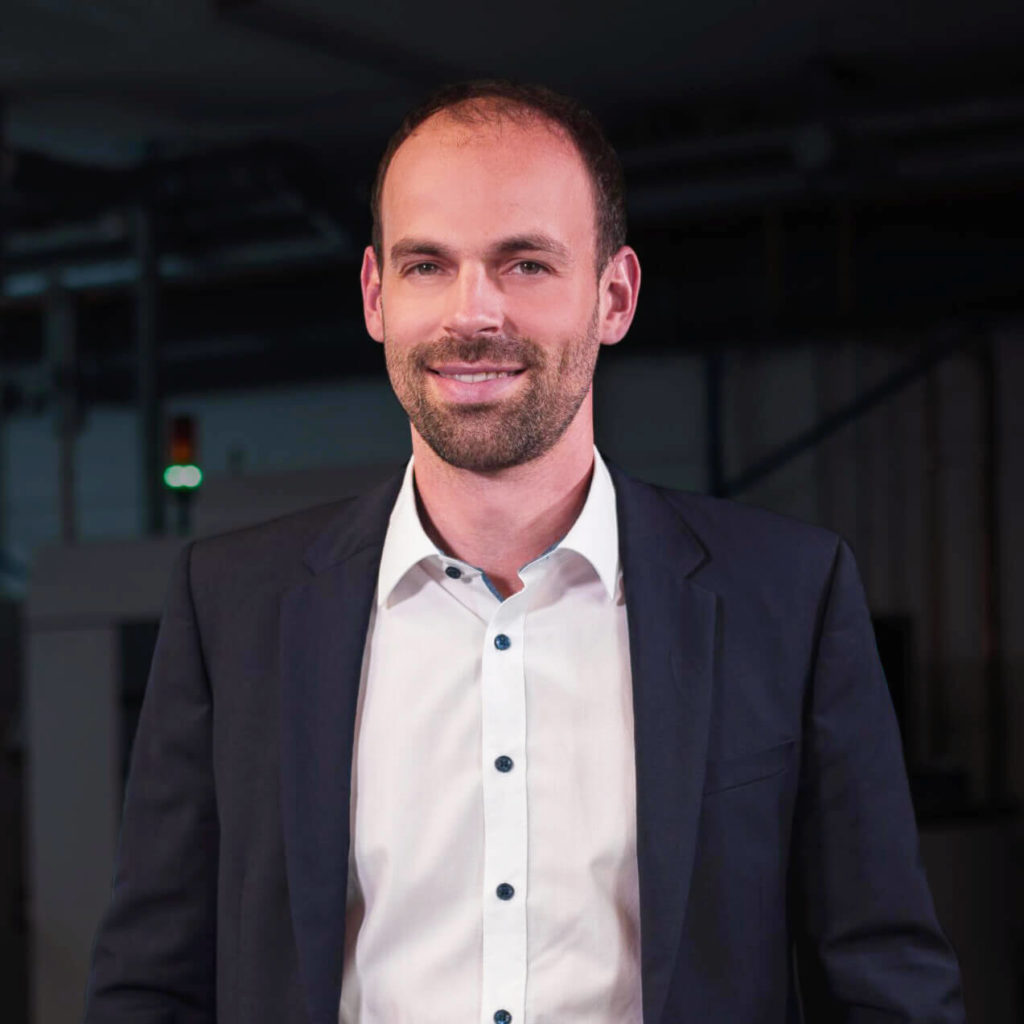
La comparaison entre les procédés de fabrication additive et conventionnels pour la production de bobinages en cuivre imprimés en 3D n’est qu’un exemple parmi d’autres de la production directe de lots sur mesure réalisée par l’entreprise allemande. D’autres exemples incluent notamment des moteurs pédaliers et des moteurs de traction électrique.
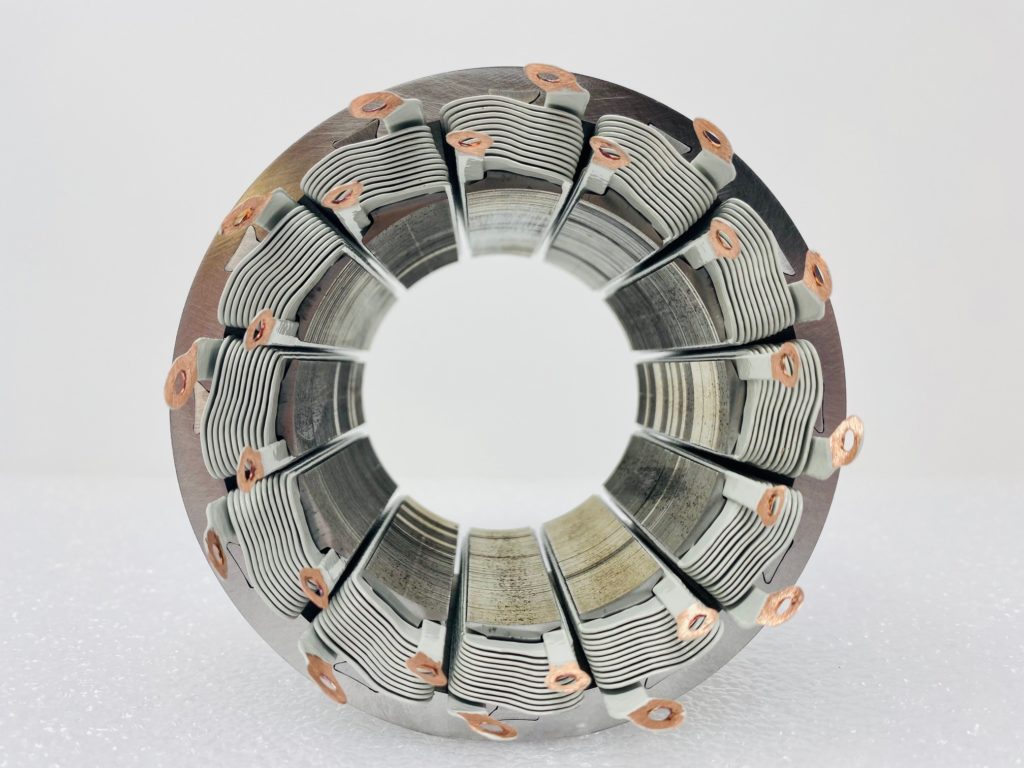
Si la FA des composants de moteurs électriques, en particulier des bobinages, permet d’approuver rapidement et facilement des conceptions différentes sans avoir besoin d’outils, Arnold souligne également que, grâce à leur capacité à fournir une mise en œuvre rapide des prototypes, ils peuvent avoir un retour d’information en temps réel de la part des clients, ce qui est essentiel pour garantir les propriétés de fonctionnement requises et améliorer l’assurance qualité.
Le prochain pas pour l’entreprise
À ce jour, Additive Drives GmbH est une entreprise certifiée ISO9001:2015. Cela signifie que son système de gestion de la qualité lui permet d’améliorer continuellement ses performances et de maintenir un haut niveau de qualité dans son environnement de fabrication.
En parlant des prochaines étapes pour l’entreprise, Jung rappelle qu’ils « ont de l’expérience dans les applications de l’industrie, ce qui signifie qu'[ils] combinent diverses « boîtes à outils » qui sont nécessaires dans ce modèle économique. » « Nous travaillons actuellement à l’amélioration significative des entraînements électriques, et des modèles électriques par le biais de nouvelles conceptions. Pour ce faire, c’est le moment d’identifier la production en série où la FA a du sens et offre un avantage économique », note Jung.
« Nous sommes prêts à investir des kilomètres supplémentaires pour soutenir nos clients dans leurs développements en cours et les amener à la production en série. Jusqu’à présent, notre preuve de concept démontre un certain nombre d’applications pour les moteurs électriques qui peuvent être réalisées par FA, mais nous n’avons pas l’intention de nous arrêter là. Nous allons continuer à nous concentrer sur les moteurs électriques, car nous sommes convaincus du potentiel que cette technologie peut apporter à ce marché. Pour ce faire, nous chercherons d’autres applications où la SLM pourrait être utilisée comme technologie de production en série« , conclut Arnold.