How many times have you heard that start-ups are the propeller of the Additive Manufacturing industry? Enough to know that we need to keep an eye out for those entrepreneurs who can become the next unicorn in the industry.
While we understand the need for start-ups to remain in stealth mode until their technology is ready enough to be officially introduced in the industry, we can’t help but give kudos to these start-ups that have been created in the midst of the Covid-19 pandemic. Cheers to these twelve startups that, as per Winston Churchill’s words, did not let “a good crisis go to waste”.
1. F3nice
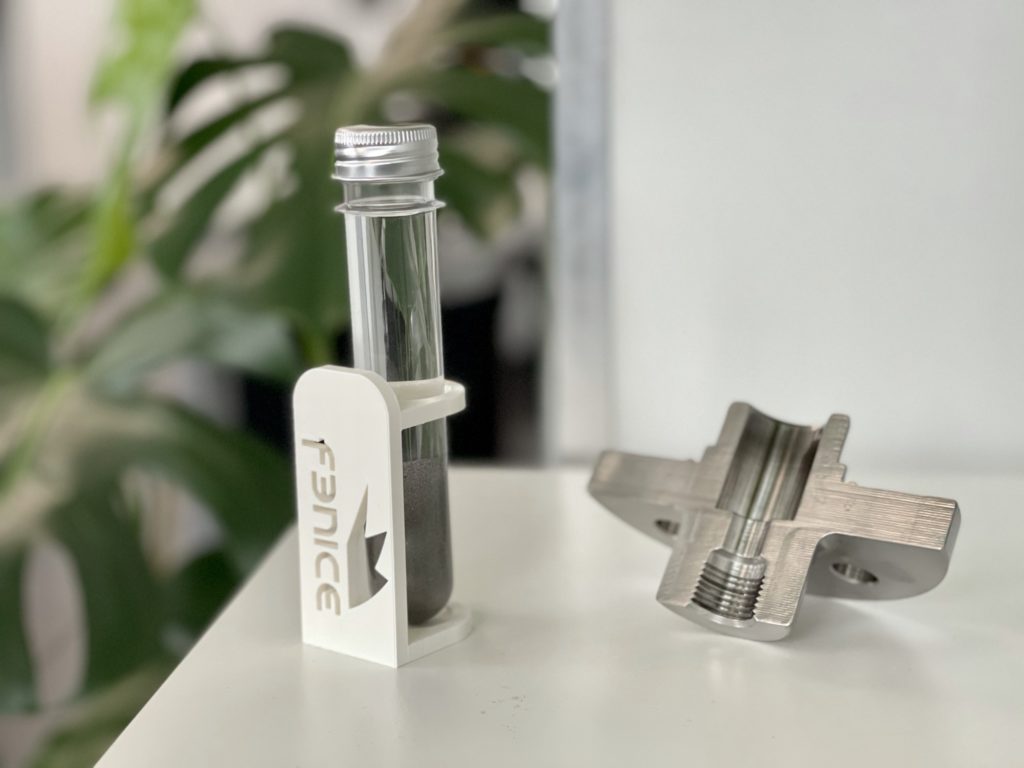
Founded in May 2020, in one of the countries most affected by the pandemic, F3nice is the idea of Luisa Elena Mondora and Matteo Vanazzi. Both cofounders came up with the idea of F3nice in 2019, on the heels of an analysis in the Oil & Gas industries. With the decommissioning of offshore assets for the oldest oil fields in the North Sea, and the digital inventory for on-demand and “just in time” production of spare parts, they investigated the possibilities to use the high value scrap metal from offshore decom to power a circular economy project.
F3nice – whose pronunciation is similar to the Italian word for Phoenix, “Fenice” (the bird that obtains new life by arising from the ashes of its predecessor) – ambitions to live up to its name by sourcing metal scrap and disused parts and transforming them into metal 3D printable powder.
The company’s project has gained traction over time and has raised the interest of Equinor Ventures who signed a Letter of Intent with the team. As part of this contract, the materials producer will process Equinor’s scrap, and the feedstock made with it will be used to print parts for the commissioning of the Johan Castberg field, near Hammerfest, by Fieldmade – in a true Circular Economy Ecosystem.
The start-up told 3D ADEPT Media in an interview that its powder “is identical to any other high-quality powder produced with VIGA technology and can be re-used during the printing process just as many times [as the alloy allows]. The added value is that, once the powder is deemed ‘exhausted’, the OEM can contact F3nice and ask for it to be recycled instead of having the hassle of disposing it (at high cost) as hazardous waste. F3nice can provide this service not only for its products but also for any powder.”
2. SphereCube
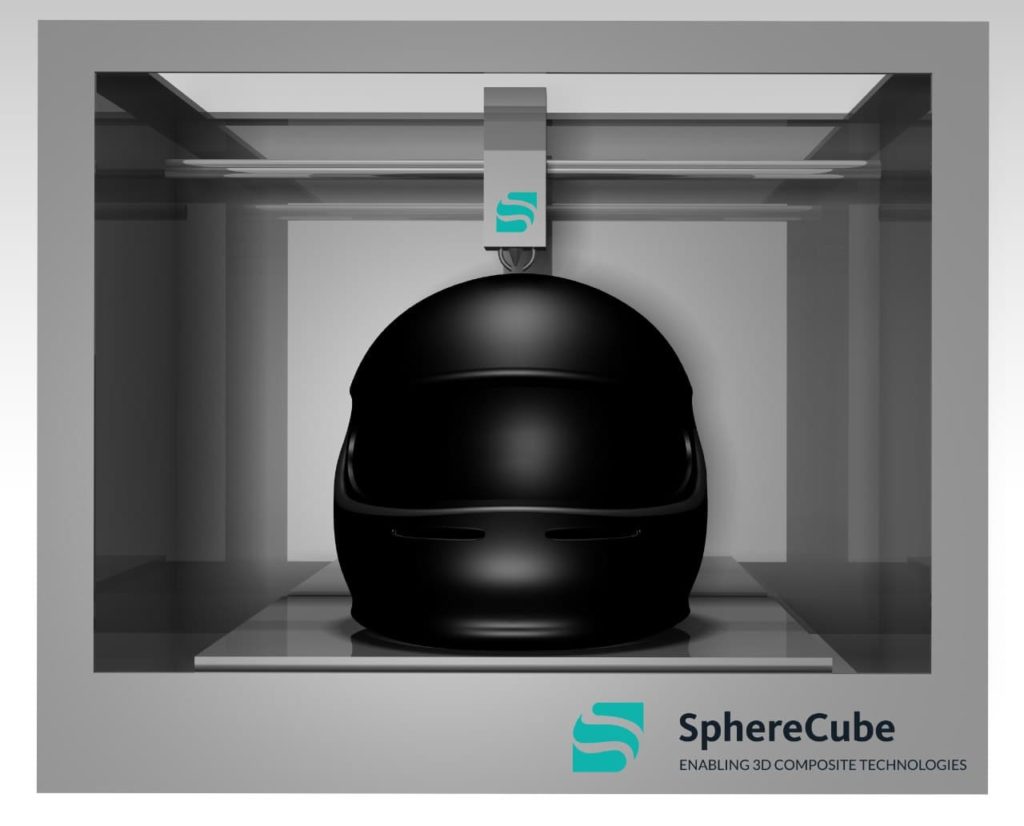
Remember we told you that start-ups have the opportunity to think about a business model that takes environmental concerns into account from the very beginning of their venture? Well, SphereCube has decided to play its part in these environmental concerns at the manufacturing level, by getting rid of composite processing scraps and molds, in order to reduce the environmental impact of composite production.
This 3D printing start-up is a spinoff of the Marche Polytechnic University (UNIVPM, Ancona – Italy) which develops 3D printers capable of fabricating composite objects using thermosetting resins and continuous fiber reinforcement.
“Through the interaction of a heat source with the raw materials involved in the process, SphereCube’s system enables the production of components in composite material with continuous fiber reinforcement and thermosetting matrix. This innovative production process is able to automatically create products using high-performance composite materials, without geometrical limitations”, the company told 3D ADEPT Media.
The manufacture of connected composite 3D printers that are less energy-consuming and that can process biocompatible materials is according to the company, a key step in helping industries build a 100% sustainable supply chain.
SphereCube has filed its first patent “Method and system for composite material 3D printing” (Italian patent n. n. 102021000006800) and has registered its European trademark.
2022 will see a key focus on the development of the design and fabrication of the Minimum Viable Product and customers’ feedback will help to further validate the company’s technological solution.
3. Replique
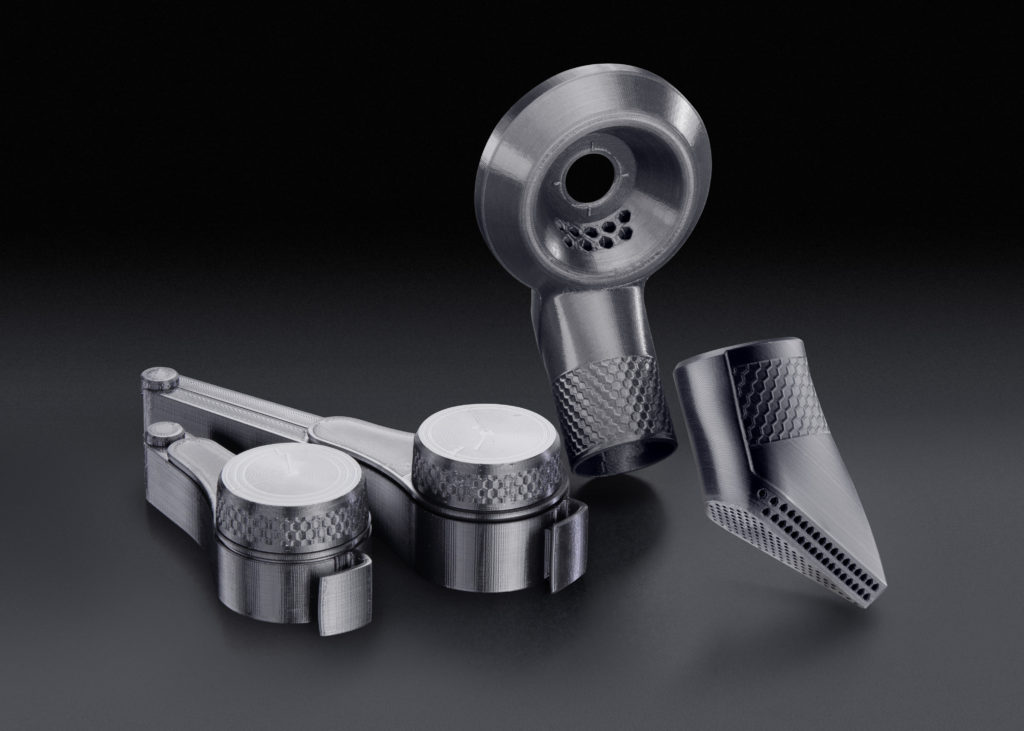
Replique, a Mannheim-based venture of the BASF business incubator Chemovator received some media hype when it announced a partnership with Miele, a German home appliance manufacturer. Under the terms of the partnership, the company receives the exclusive right to produce and ship high-quality 3D printed accessories from Miele using its decentralized production network.
Founded in 2020 by János Váradi, Dr. Henrike Wonneberger, and Dr. Max Siebert, the company provides an industrial 3D printing platform that enables OEMs to provide parts on demand to their customers through a global, decentralized and secured 3D printing network. It is entering a market that is worth more than 500 billion USD and which enables revenue potentials with significantly higher margins compared to the sale of new services.
From qualification of 3D printable parts, to digital inventory and production network, the company provides a solution broader than what is usually seen on the market.
For industrial production, Replique uses their global network of quality-approved industrial manufacturing service bureaus. With this solution, OEMs are reducing their total costs of ownership while increasing flexibility. Not to mention that they can provide better aftermarket services to their customers, with parts always being available, even at the end of the product lifecycle; thus gaining competitive advantages.
Amid the companies that have already benefitted from Replique’s services, one counts OEMs in the automotive industry, and recently Siena Garden, an expert in the category of garden tools and garden furniture.
4. Marklix
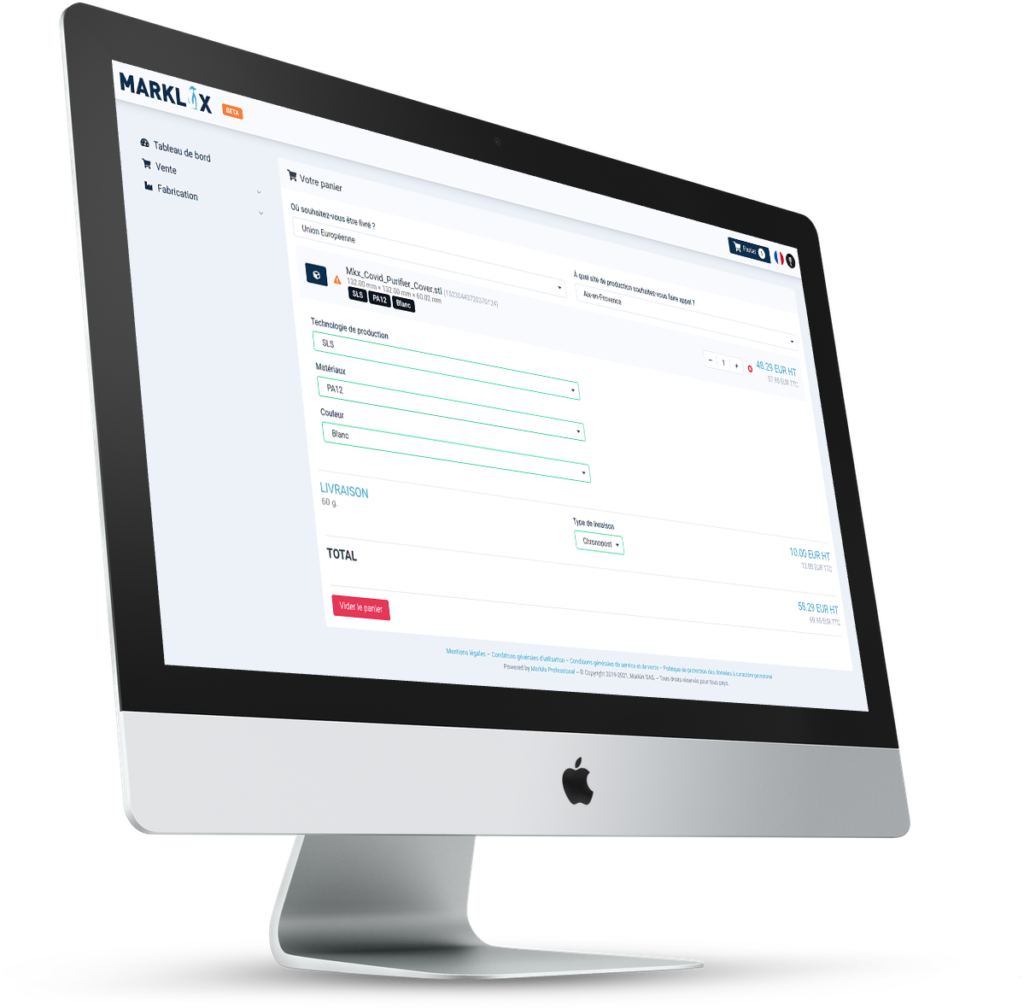
Still in the field of spare parts, another start-up has been founded last year in France – in February 2020 precisely, with the mission of making “obsolescence obsolete”. This original baseline makes any expert in the AM industry rapidly understand that Marklix enables manufacturers to qualify and distribute spare parts by producing on-demand and locally using 3D printing.
Their journey started with the development of a “marketplace”, where the idea was to be able to find all the parts of all the manufacturers, for example a hoover part, and thus allow individuals to repair their hoover without having to change the entire appliance. Two challenges popped up during this project: the price of parts was too expensive – it was often cheaper to buy a new appliance than to order a part -, the parts were not digitized which means one could not 3D print them with just a simple click.
To overcome these hurdles, the Marklix team decided to develop new software solutions:
The first software solution addresses the price issue of the spare parts by enabling manufacturers to be more competitive and to save time.
“It is an ERP/MES that allows them to manage their machine park, to edit invoices and delivery notes, to take orders online while letting the manufacturer choose whether to let the customer pay directly or not, by securing the files, etc. The feedback we have received indicates an average time saving of 40 minutes/order and a better visibility and efficiency for their company. Our partners are therefore more competitive, making the prices more attractive”, the company explains.
The second solution consists of the digitalization of stocks, which is of crucial importance for some companies because of the high cost of spare parts stocks. In this vein, this software solution heps engineers achieve five main tasks: identification of 3D printable parts thanks to AI, qualification of the parts with the right materials and production technology, calculation of ROI (from an economic and ecological standpoints), transfer the parts that have passed the 3 first steps on an online catalogue and printing. The last task can be done internally or externally if the company does not have the production means.
Following the positive response they receive on the launch of their first software, the Marklix team led by Pierre-Jacques LYON and Thomas BOULLIER, respectively CEO and CTO, does not intend to rest on their laurels. They will continue to serve the needs of 3D printer manufacturers and part producers, with their dog Reynolds, a young White Swiss Shepherd that has the heavy responsibility to create and maintain an atmosphere conducive to work.
5. Addiblast
It’s not every day that we talk about AM in Slovenia…and the start-up that is making us envision more than just a touristic journey in the country with stunning caves is Addiblast. This team makes us explore the field of the manufacturing process that every operator fears: post-processing. Founded in 2020, the start-up is part of FerroECOBlast® Europe, a family company that has established a strong reputation for solving the most demanding surface treatment problems. The parent company’s portfolio includes a wide range of solutions such as air blasting, shot peening, enamelling & coating solutions, dry ice & dry snow cleaning, as well as UHP water jetting.
Addiblast therefore leverages over five decades of experience from its parent company to provide the AM industry with a portfolio that comprises blasting, depowdering and recycling.
The company debuted at Formnext this year by showcasing the capabilities of its three main products:
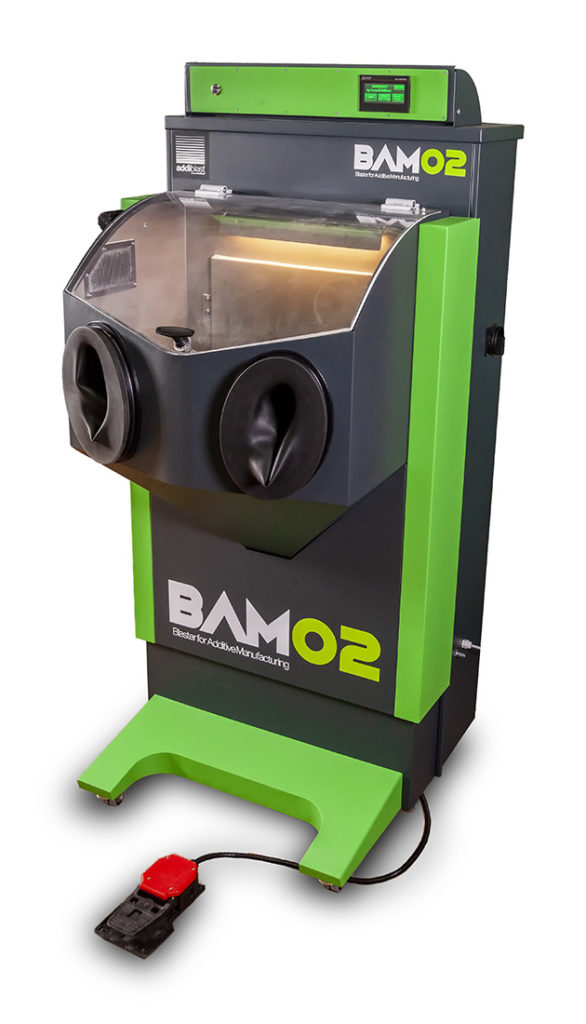
The BAM station, a solution for surface treatment designed for various processes such as smoothing, roughing, unifying, and polishing surfaces, removing support structures, and precise removal of powder from extremely complex structures. It is made of stainless steel and is suitable for all types of shot blasting media.
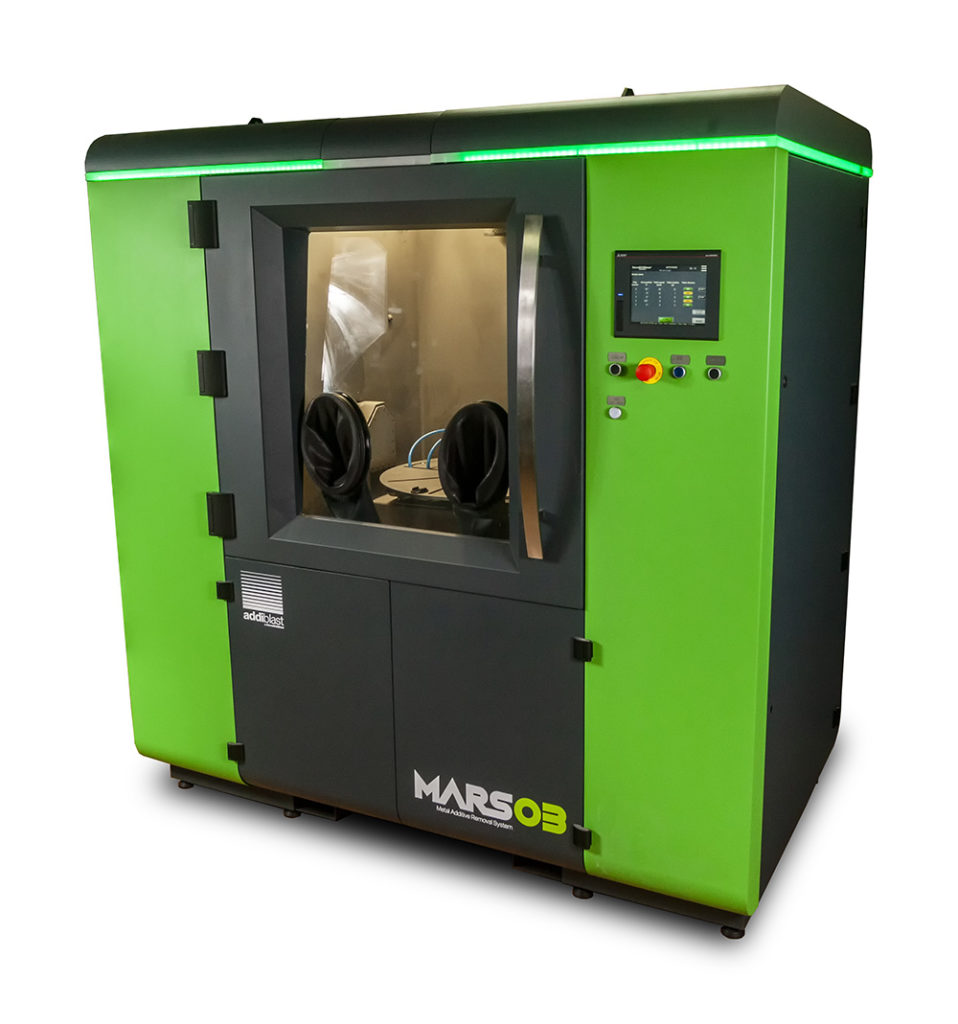
- The set of MARS (Metal Additive Removal System)
Available in three options, these machines enable the de-powdering of parts that are complex or large. Each machine features a communication and exchange data system with other machines from the manufacturer. The main difference between MARS01, MARS02 and MARS03 is that the latter is a fully automated solution that is explosion-proof and that complies with the ATES directive. Furthermore, by enabling a closed-loop inert atmosphere workflow, the machine can maintain oxygen level below 2%. This prevents contamination and oxydation of the powder during de-powdering and conditioning, and brings powder reusability to new levels.

The latest in this portfolio is the STAR (Station for Transfer and Additive Recycling). Designed as a central station that continuously and automatically controls the pneumatic transfer, recycling, and conditioning of powder, this machine enables a direct connection with the 3D printer and other equipment. That is its main advantage compared to other solutions from the manufacturer. It can also be used to purify the virgin powder and like, the MARS series, it prevents contamination and oxydation of the powder during de-powdering and conditioning, and brings powder reusability to new levels.
6. NematX AG
The next startup in this list is a spin-off of ETH Zurich founded by Raphael Heeb and Silvan Gantenbein. With the ambition of ushering in the next generation of 3D printing with high-performance polymers and significantly surpassing the current benchmarks in corresponding end-use components, the Swiss start-up targets all vertical industries whose parts manufacturing has to withstand harsh environmental conditions.
NematX AG that was one of the winners of the 2020 Formnext start-up challenge is developing what it calls a “Nematic 3D Printing” technology that aims to help industries make their low-volume business more profitable and sustainable.
“Liquid crystal polymers – short LCPs – belong to the family of high-performance plastic materials. In comparison to conventional thermoplastics such as PEEK or PEI, LCP molecules are comparably short and stiff and possess unique properties that makes their use in 3D printing highly attractive. In the molten state, LCPs adopt a short range order, similar to packages of tree logs floating on a river”, the company explains.
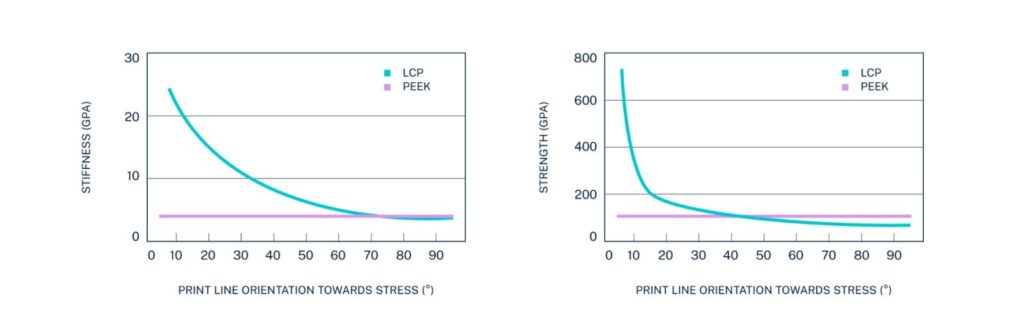
The Nematic 3D Printing technology is therefore based on material extrusion (FFF 3D printing). “During printing, we can align these individual packages LCPs along the print direction to produce parts with unmatched mechanical and thermal properties from polymer additive manufacturing”, the NematX AG explains on their website.
“By controlling the molecular alignment of our LCP 3D printing materials, we achieve superior stiffness and strength from polymer 3D printing. In printing direction, we can achieve Young’s moduli of up to 25 GPa and ultimate tensile strengths of 650 MPa. In transverse direction, stiffness and strength values of other thermoplatics such as PEEK or PLA are achieved”, they outline.
7. Additive Drives GmbH
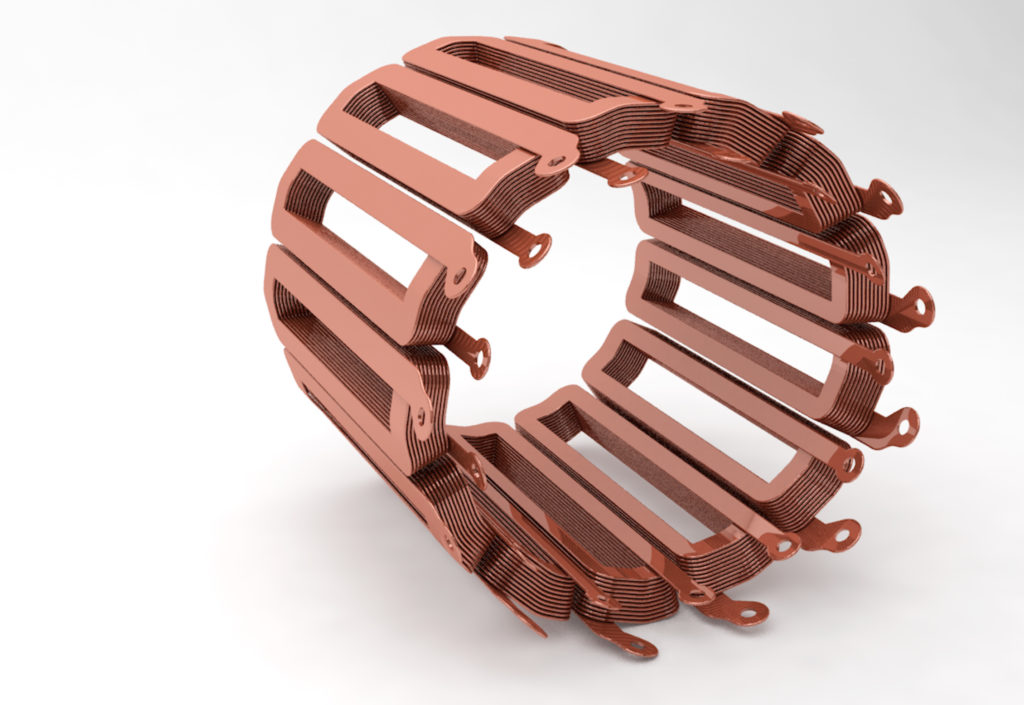
Not many companies can pride themselves on raising money during the first three months of their existence, Additive Drives GmbH can and the best part is, the company did so during the first peak of the Covid-19 pandemic last year, when the economy was not at its best.
Founded by Philipp Arnold, Jakob Jung and Axel Helm, Additive Drives GmbH develops and manufactures additively manufactured electric motor components. With a $1.5 million seed investment from AM Ventures Holding GmbH, Additive Drives GmbH ambitions to drive the electric drives market with new applications.
“Jakob and I, both come from the applications side of the industry. We have been developing electronic robots in the former automotive company we worked for. Engineers by training, we built up extensive experience with copper and additive manufacturing machines. After a deep research, we came to realize that the combination of AM and copper might lead to not only shorter development and test cycles for electric motors but also more performant applications. After a few successful trials, we reached out to Axel Helm who has a solid expertise in manufacturing processes and industrialization. His experience in copper processing and optimization of AM processes is pivotal to define the type of applications we could work on. We have therefore decided to combine our respective strengths to make Additive Drives GmbH a viable business” Arnold told 3D ADEPT Media in an interview.
With 13 employees on board, Additive Drives GmbH ambitions to enhance performance of electric motors by up to 45% by focusing on copper windings, the main component of an electric motor. AM is definitely part of this game as the direct manufacturing from the CAD data allows for shorter development and test cycles. Moreover, it does not jeopardize material parameters and offers instead an electrical conductivity at the same level as conventional production.
While the Additive Drives GmbH team is up to new adventures in this applications field, it should be noted that they have won the Gründerpreis Sachsen/ Award for the most innovative young company of Saxony, a free State on the south east corner of Germany.
What the Start-up area had in store for this year 2021 …
8. Axtra 3D
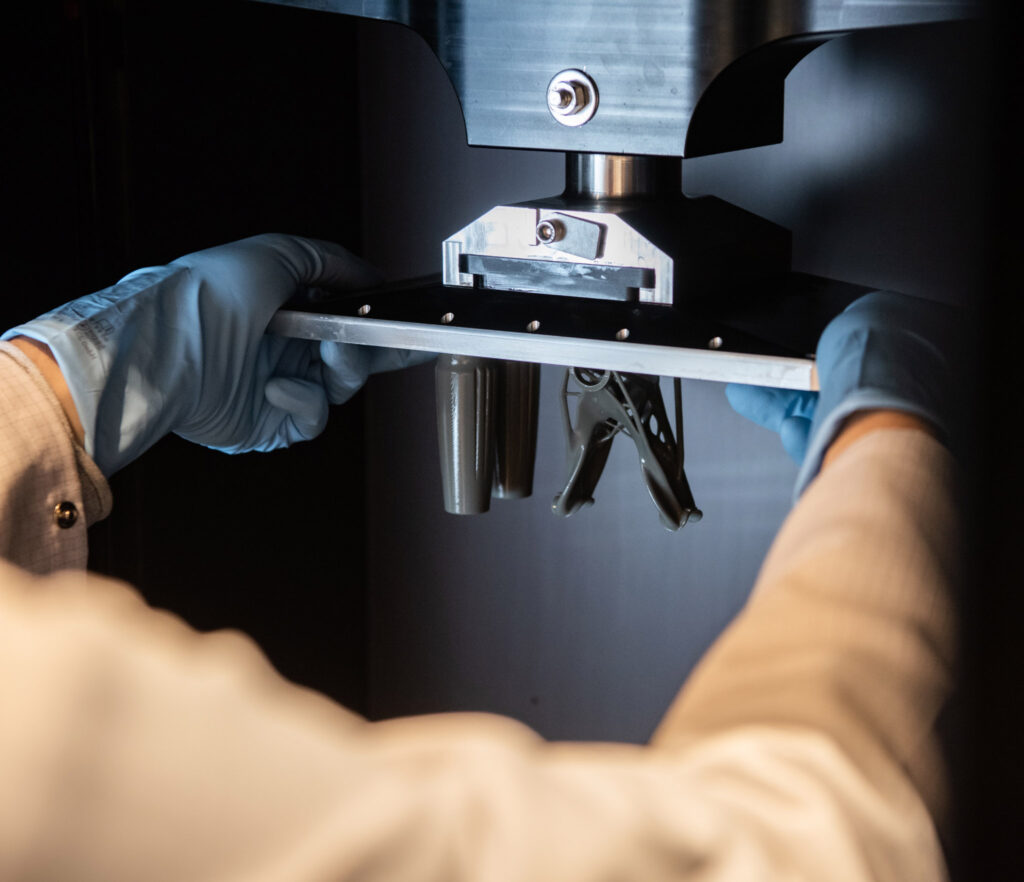
We will rarely find a start-up that has made a real splash on its debuts on the International Scene of the AM industry. Axtra 3D did it at Formnext 2021, with the launch of a unique 3D printer. We recently learned more about this company’s innovation and two things really marked us: the product development time that only takes 9 months as well as the technology. This technological solution is the result of a collaboration between on-demand manufacturing platform Xometry and Axtra3D, a developer of advanced Additive Manufacturing solutions using Optoelectronics.
Together they have created a 3D printer based on a patented Hybrid PhotoSynthesis (HPS) technology, which could combine the benefits of SLA, DLP, and LCD. The stake is even higher when we know that, when it comes to resin 3D printing, operators are often hesitant between the advantages and disadvantages of SLA, DLP and LCD. According to Xometry, choosing between these three solutions requires compromises, either on print speed and resolution (DLP/LCD) or on surface quality and print area (SLA).
So, what makes Hybrid PhotoSynthesis (HPS) outstanding?
HPS enables a printing process with fine resolution and delivers high print speeds and excellent surface quality even with large print areas. The process combines two light sources in a custom assembly (DLP & Laser) in order to create a harmonized light engine that efficiently harnesses the power of the two sources.
“In our HPS technology, the Laser defines the resolution and as a result, HPS offers higher resolution and fine feature reproducibility than a standard DLP,” explains Gianni Zitelli, one of the founders of Axtra3D.
The new process therefore delivers the speed of DLP/LCD with the surface quality and scalability of SLA, along with ultra-fine resolution, continuous printing and isotropic part performance capabilities.
“Users often have high surface finish costs,” states Praveen Tummala, the other cofounder of the company, “but with the fine surface quality and resolution offered by HPS, they can save time and money as the 3D printed parts don’t require any post-print surface finishing”.
Where does Xometry come into play?
As the story goes, the project started at the beginning of 2021 with the objective of launching their 3D printer during Formnext 2021 edition . “We thought it would take us about 18 months to complete a project like this,” explains Tummala. “Thanks to the team and our partners in Europe, it only took us 9 months”.
In August, the Italian team launched the first simulation of the complex optical system which was a resounding success. This breakthrough then accelerated the whole production process. “A lot of the credit goes to Xometry, as they were able to deliver about 2,000 parts in 6 weeks, an extremely demanding timeline,” states Zitelli. “We have access to CNC providers in Italy, but it wouldn’t have been a strategic move for our company. Working with Xometry gives us access to thousands of providers worldwide—this is the real value of our collaboration”.
In order to finish the project in time for the forum, Axtra3D called on Xometry to produce every single aluminium CNC machined part used to assemble the printer, from very small components for the light system to elements for the printer’s base. “We can’t imagine any other partner who could have been able to deliver the parts in time to allow us to launch the product and exhibit it at Formnext,” says Tummala. “
The Axtra3D team worked very closely with Liana Zedginidze of Xometry during the entire production process. “We are highly indebted to Liana for her support of our project. She was available for us round the clock and ensured that the ordered parts were produced and delivered on time,” said Zitelli.
The next step for both partners is now to produce 10 beta 3D printers by June 2022 in order to launch their product on the industrial market.
9. Additive Appliances
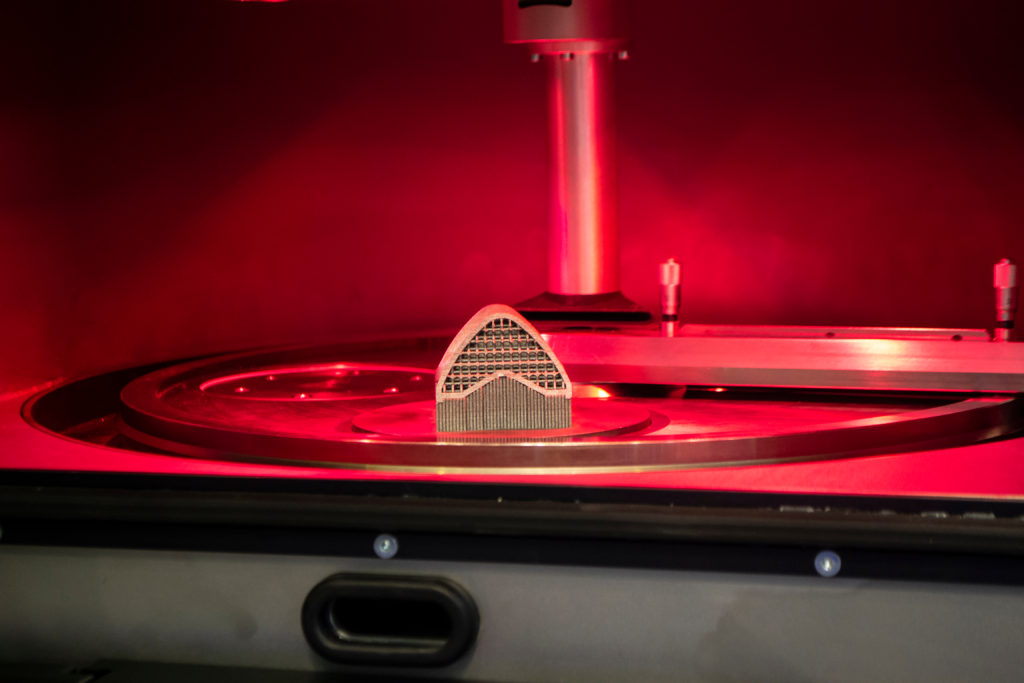
Thereafter comes Additive Appliances, a start-up that was incorporated in April 2021, with the goal of developing the next generation of household appliances such as coffee brewers, and personal care products. From the very beginning, the company has received the support of angel investors, including a university spin-off company that specializes in Computational Fluid Dynamics and Topology Optimization.
Together with Kilometro Rosso, a private innovation hub in Italy, Additive Appliances has secured an EU Grant via the Digital Innovation Hub World’s First Open Call. The funding will accelerate Additive Appliances development for its “3D Printed Heat-Exchanger for Household Coffee Machines” project.
The Italian start-up comes with decades of experience in 3D printing applications such as heat-exchangers. In this case, it explains controlling water’s temperature and pressure is key to extracting the best out of coffee and the solution allows for a more efficient and sustainable beverage preparation.
Electro-thermic household equipment controls the process’ variables by embedding several (hardly recyclable) components, while traditional thermo-mechanic devices do not directly control them, showing quality and repeatability issues. Currently, consumers have to trade-off between quality and sustainability, a press communication from the company reports.
Interestingly, to enhance performance, explore new features and functional personalization, AM could be utilized at different stages of product development, including end-use production. As we saw in an application shared by Additive Drives Gmbh, combining AM and conventional manufacturing processes enables a better control of temperature, pressure through embedded, conformal, high-efficiency yet ultra-compact heat exchangers.
This means that small batches can for instance be engineered to exalt specialty coffee varieties, down to individual consumer preferences. On the other hand, a single piece of mechanic can replace auxiliary electronic components, significantly reducing the carbon footprint of the equipment’s lifecycle from production to recycling. In a nutshell, an ecological experience of coffee.
USA Tech, the Living Space for Additive Technologies of Kilometro Rosso, will be a crucial partner during the DIHWorld’s experiment. Its 3D printing infrastructure will help the company quickly leverage the technology hands-on and perform in-depth process assessments through real-time monitoring systems -speeding up manufacturing optimization, the company concludes.
10. Vispala Technologies
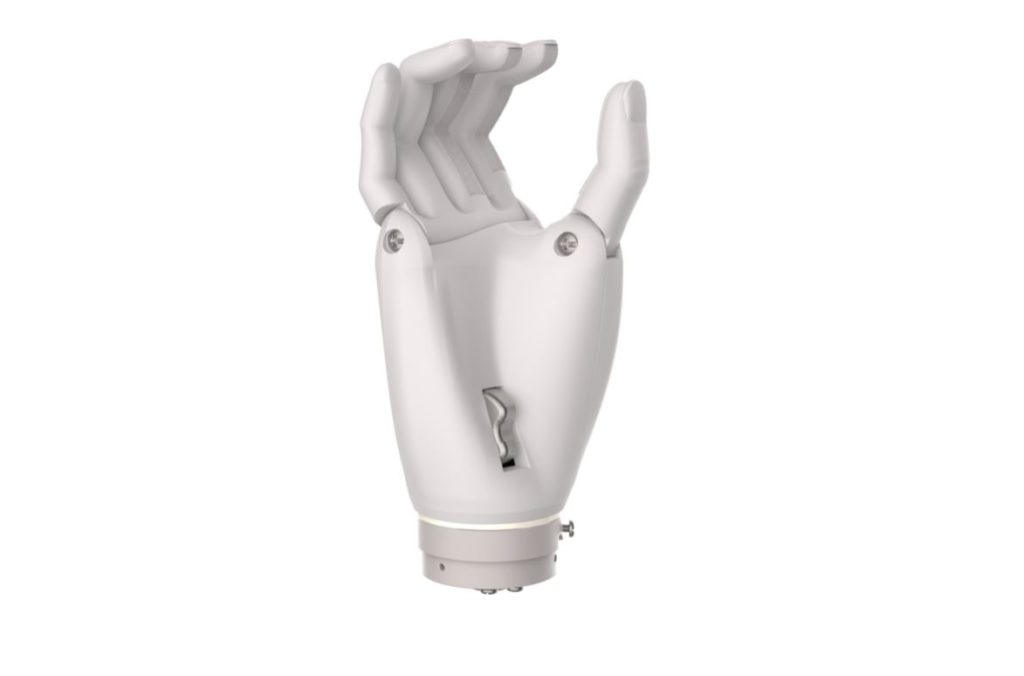
This India-based company impacts the lives of disabled people with its 3D printed hand prosthesis iGrip. The company that develops customized 3D printed orthotics, 3D printed artificial limbs and prosthetics, has made an official entrance on the International Stage of the AM industry by taking part in the 2021 Formnext Start-up challenge.
The company stood out from the crowd by winning the AM Ventures Impact Award, which recognizes the winner’s approach to sustainability, an approach that takes into account the 17 sustainable development goals of the United Nations; environmental considerations (such as green energy and resource conservation) and social aspects (for example, education and equality).
Vispala’s iGrip is an affordable, lightweight body-powered hand prosthesis that helps patients perform work related to their daily living.
“We at Vispala are taking on the challenge to modernize the prosthetics sector through technology and innovation and restore 50% or more livelihood capability to users with comfortable and aesthetically pleasing solutions,” said Dipak Basu, CEO of Vispala Technologies. “Simultaneously, we are building a sustainable social enterprise to scale up our work.”
11. Nobula
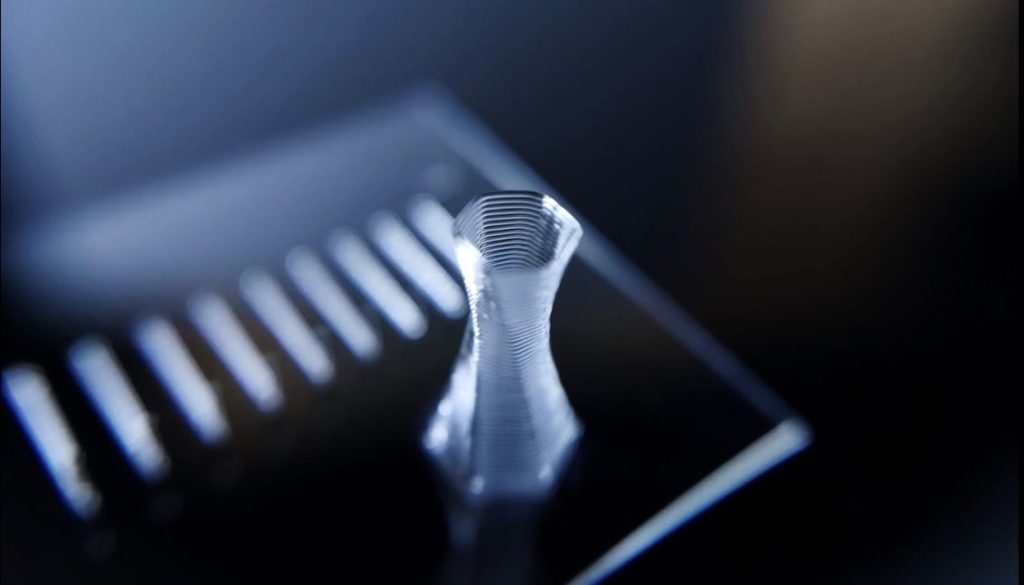
Another startup that the 2021 Formnext startup challenge brought to limelight is Nobula. This glass 3D printing startup is a spin off from KTH in Sweden that brings a lot of diversity in the range of AM technologies already available on the market.
Their innovation? A Nobula™ glass 3D printer based on Direct Glass Laser Deposition (DGLD™) that can produce complex 3D structures in glass.
The company has filed for two patents, one for the glass 3D printer and one for the printing material technology, which will enable them to provide custom glass 3D printing for science, development and production.
Moving forward, we may expect the company to finalize its prototype printer and to launch the first model before summer 2022.
12. AM Entrepreneur
Last but not least, this Germany-based start-up aims to “standardize the implementation of AM technological value within profitable and sustainable business models.” Behind this ambitious vision is Gregor Reischle, who launched and pushed the AM roadmap at TÜV SÜD forward.
AM Entrepreneur’s creation was founded based on one observation:
“Distributed manufacturing within Business models will help to reach our CO2 emission goals as well as open complete new digital business models and strategical positioning potentials. In today’s corporate “business unit” structure, we quite often realize a lack of cross-disciplinary, entrepreneurial TEAM DNA which often results in projects stagnation. The complexity of the business design within Additive Manufacturing strictly requires the collaboration between all operational units and minds”, which is an ability AM Entrepreneur wants to establish within industry companies.
Within AM Entrepreneur, Reischle therefore aims to provide an entrepreneurial mindset incubation for all AM Start UP and intrapreneurial TEAMs, provides digital assets that will enable scalable implementation of AM processes while assuring predictability on return on investment. Lastly, he will also deliver consulting, training, coaching, and hands-on support to overcome the quality, approval, and business design challenges industries often face.
So far, AM Entrepreneur has already delivered workshop and assessment result reports?, supplier assessments and GAP Reports based on AM quality and health & safety standards like ISO/ASTM 52901, 52920; AM Innovation TEAM coaching during the “business design phase ( multiple weeks program ). It has already supported the installation of AM systems in regulated environments, in compliance with CE, or quality assurance requirements – assessments based on the ISO/ASTM 52930 and others.
“After around 20 years at corporate career, I finally managed to spin off and start up. The freedom to be able to travel again, after being vaccinated and be part of the FormNext exhibition reunion with AM industry friends. My consulting and business incubator start-up leads to new profitable business models and software solutions. My “hands-on creator mindset” empowers executives and operational teams to build new successful business models, while incubating AM values”, Reischle told 3D ADEPT Media.
Closing remarks
This “Start-up” area shows that there is a greater number of start-ups that have been founded in 2020 than in 2021. This reveals the industry’s resilience and its ability to find the good in any crisis and most importantly, this attests to AM’s readiness to create a business model exclusively based on applications.
This content has first been published in the 2021 November/December edition of 3D ADEPT Mag.
Remember, you can post job opportunities in the AM Industry on 3D ADEPT Media free of charge or look for a job via our job board. Make sure to follow us on our social networks and subscribe to our weekly newsletter : Facebook, Twitter, LinkedIn & Instagram ! If you want to be featured in the next issue of our digital magazine or if you hear a story that needs to be heard, make sure you send it to contact@3dadept.com