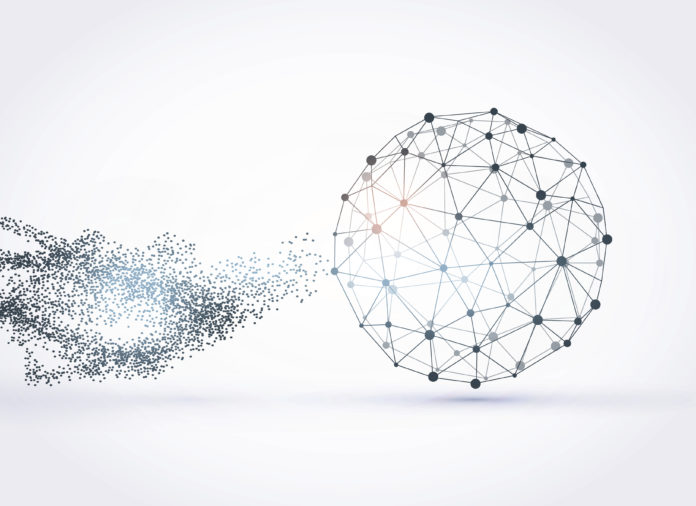
At the beginning of 2019, we asked additive manufacturing experts what were their predictions for the year. The main forecast for participating companies was to focus on education, and how to move AM to production.
Another trend was to focus on the development of new materials. Although, we witnessed some encouraging partnerships between material suppliers and 3D printer manufacturers, it should be noted that there is still a supply/demand imbalance on the market.
Nevertheless, 2019 has been very exciting as it showed various deployment strategies to help the industry move forward. Things were not always easy, as sometimes, the uncertain political climate in some regions was not conducive to business. However, most companies showed optimistic results with regards to their goals while others decided to take a different direction in order to be more efficient.
At the end of the year, we reached out to 21 companies to discover what exactly 2019 meant for them, and more importantly, how they envision 2020. These companies include 3D printer manufacturers, material suppliers, contract manufacturers/3D Printing service bureaus and software publishers. They share their vision below.
Looking Back at 2019 and Forward to 2020
Christophe Schramm, Manager of New Technologies for Solvay’s Specialty Polymers global business unit, material supplier.
“2019 has been a year of deployment of Solvay’s AM strategy, with several partnerships with printer manufacturers, the broadening of our product portfolio, and the deepening of our ecosystem along the entire AM value chain. This strategy is aligning well with the move of many end-user industries from hype to real projects. We expect this trend to continue and accelerate in 2020, with more news to come from Solvay, supporting our ambition to become the leading supplier of AM-ready high-performance material solutions.”

Jon Donner CEO of Nanofabrica, specialist in nano-3D Printing
“2019 was packed with exciting achievements at Nanofabrica. We sent dozens of parts to global customers including Fortune 500 companies. Recipients were highly impressed with the results and with the level of accuracy we reached. Later in the year we finalized our industrial machine which offers an impressive build volume of 50x50x100mm, won a TCT award for it, and signed our first Beta sales. in 2019, Gartner published their forecast for emerging technologies, and stated that nanoscale 3D printing technologies were on the rise. In 2019, we were able to witness this at different conferences and exhibitions across the world. In 2020 we will see for ourselves the real need for this technology. The market asks for it, and we’re here to deliver.”

Phil Schultz, EVP, Operations, 3D Systems, provider of a comprehensive range of products and services, including 3D printers, print materials, software, and on-demand manufacturing services
“In 2019, 3D Systems realized a number of key milestones, the most prominent being that 3D production is no longer a goal, but reality. We’ve seen evidence in the most recent E&Y study that confirms the adoption of additive is ramping – moving from the researching and prototyping phase to production – with nearly 75% of companies embracing the technology. As a company, we continue to put the customer at the center of everything we do – and our customers have been a key element of how we’ve brought production AM to life.”

We’ve collaborated closely to first understand the application each customer is addressing, and then where we can add value in their respective workflow. In many cases, our customers’ needs for production workflows have been the catalyst for our innovation, which is exactly what happened with the newest materials we’ve launched. In the last four months of the year, the majority of our 10 new materials were designed for production applications. By the end of 2019, 3D Systems’ application-specific production solutions will yield approximately 200 million end-use production parts – an unprecedented industry first.
As the integration of our technology into customer workflows continues to accelerate in 2020, so too will the number of manufacturers 3D printing plastic and metal end-use parts for applications in healthcare, aerospace, automotive, dental and consumer goods. 3D printing will transform how companies create new, improved products while gaining efficiencies that place them well ahead of their competitors.”
Stephan Kühr, CEO, 3YOURMIND, 3D printing software company.
“In 2019, 3YOURMIND added their first customer focused primarily on serial additive manufacturing: Erpro Group. We have seen our other customers also validate many small and large series AM parts that will move into production in 2020. We were happy to enable this with our Part Identification, Order- and Production Management Software.“

“As we expand our features to manage these new use cases, we are coming much closer to full automation. The work we began with umati in 2019 to establish machine connectivity is also a significant step towards this goal of a fully digital AM workflow.
We know our customers will be putting many more parts into production in 2020 and 2021 – so we will focus on digitizing and tracking the production and documentation processes in the Agile MES even better. With our Agile PLM we will help customers to identify many more positive use-cases and store them in a digital inventory, so that they are ready to be ordered on demand.“
Meddah Hadjar, CEO of SLM Solutions, manufacturer of 3D metal printers
“SLM Solutions reflects back on 2019 and describe it as a resetting year. We announced that our order grew by 21% YoY and doubled in Q4. The confidence that customers and the partners put in our products and in our company is impressive.”

“This is demonstrated not only by the growth in the orders but also by numerous successful projects and partnerships throughout the year – whether the recently announced letter of intent to expand cooperation developing the next generation machine with Divergent3D, the Honeywell announcement on 90micron parameter development, the collaboration with Bugatti to realize functional components or the use of Selective Laser technology in race cycling from the Danish Institute of Technology and CeramicSpeed. SLM Solutions presented these and many other exciting projects at the leading trade fair for additive manufacturing; Formnext, which turned out to be another highlight of 2019. The large number of trade visitors showed great interest in SLM® Multi-laser technology, and the trade fair appearance was crowned by several sales deals and partnerships that were signed.
For 2020, we will continue to make progress in the marketplace. We will work with our customers on increasing additive adoption and SLM Solutions is well positioned to lead in the laser powder bed fusion. As the pioneers of multi-laser powder bed fusion, our expertise in productive, reliable machines will continue to provide production solutions for a range of users. Looking to the future, we will be working on further advancing the technologies highlighted as future technologies at our booth to make them available to customers as industrialized solutions that will give an entirely new perspective to the concept of productivity in metal additive manufacturing. SLM Solutions heads into 2020 with focus on industrialization of our machines, productivity, and process parameters.”
Bruno Bourguet, Managing Director, PostProcess Technologies International
Here at PostProcess, in 2019 we saw our customers’ volumes grow significantly, particularly at companies that rely on fast innovation to drive growth, such as those leveraging 3D printing for fast prototyping. We also noted a heightened interest by more companies considering additive manufacturing for low volume production. With these trends of volumes increasing, 2020 will bring an accelerated need for scalable solutions for the post-printing step.”

The legacy approach of completing post-printing with manual labor and traditional mechanical solutions will no longer be practical options for production scale applications looking to connect the end-to-end digital thread. Additionally, in 2019, the market continued to expand its materials offerings and enable more complex geometries. This is also exciting as PostProcess expands our offerings in 2020 to enhance our fully automated, data-driven solutions to help end-users achieve increased throughput and consistency of their final parts.
Jack Cheng, DGM, Head of Global Sales & Marketing of Farsoon Technologies, Industrial 3D Printer Manufacturer
“With our commitment to offer truly open and high-performance additive systems to industrial AM users, Farsoon achieved significant machine sales growth in 2019.”

“Farsoon was able to expand its footprint in a variety of additive applications including aerospace, automotive and the prototyping industries. With continuous technology innovation, Farsoon is able to offer differentiated systems to the market, including HT1001P, FS421M, Flight Technology and the latest FS301M.
In 2020, Farsoon will focus on additive innovation and industrialization — working closely with global industrial customers to share and grow our know-how in material, additive technology, and applications with a goal to transform Farsoon’s innovation into true manufacturing reality.”
Fernando Hernandez, MD EMEA at XYZprinting, 3D printer manufacturer
“2019 was certainly a memorable one for XYZprinting. It’s the year we have launched our Industrial range of devices, consolidating the offer in technologies such as SLS, Binder JEtting and SLA/DLP. But we didn’t stop, also we’ve seen the announcement of multiple new industrial printers that are some of our most innovative products to date, such as the PartPro120 xP delivering speeds that are up to 75 times faster than conventional 3D printers without sacrificing printing quality or resolution, thanks to XYZprinting’s Ultra-Fast Film technology. With almost every vertical solution and service to offer, we’ve continued to stand out as a market leader in desktop, retail, education, and luxury item printing, and building on our presence in professional printing too.”

“Going ahead, we will set our sights on further carving our mark on the automotive, medical and architecture industries too.
Looking ahead, 3D printing will be advanced forward by the volume and quality of new materials, something XYZprinting will help with by entering our own materials partnerships with popular third-party companies. Another key theme I anticipate for 2020 will be a shift in perception of how 3D printing can in fact complement traditional manufacturing as opposed to being in competition with it. Adding to this, 2020 will also see the 3D printing industry leverage the latest software to improve supply chains leading to superior quality outcomes. One thing is certain, the forecast for 2020 is bright.”
John Dulchinos, VP, Digital Manufacturing for Jabil Additive, manufacturing services company
“2019 was a year of continued growth for Jabil Additive as the organization took advantage of its rich history in materials science innovation to accelerate the development of custom materials and advance the entire additive manufacturing market forward.”

“Jabil forecasts continued momentum in 2020, especially the growth of integrated solutions featuring engineered materials, rigorous processes and certified 3D printing machines to support applications for highly regulated industries, such as aerospace, automotive, industrial and healthcare, as well as those requiring optimized geometries or consolidated bills of material (BOMs).
Jabil also projects an increase in certified additive manufacturing solutions built upon robust quality management systems that accelerate the use of distributed production networks to meet stringent part quality and performance demands. Additionally, Jabil anticipates an influx of new engineered materials with unique properties to enable new applications while reducing time-to-market and cost in bringing the highest quality parts to market. To that end, Jabil will continue to evaluate, qualify and validate a diverse mix of engineered materials for use with its interconnected Additive Manufacturing Network of world-class 3D printers and quality processes to provide a faster path from prototyping to full-scale production of disruptive products.“
Lukas Pawelczyk, Head of Freeformer Sales, Arburg, manufacturers of injection molding machines & 3D Printers
“Additive manufacturing will continue to grow in significance in the field of medical technology, as demonstrated by a number of well-known Arburg Plastic Freeforming (APF) customers in 2019. They are now using our open system to process biocompatible, resorbable, sterilisable and FDA-approved original materials. I think that, in 2020, we will see implants being produced with the Freeformer in clean room environments and used in the human body.
For us as a machine manufacturer, quality assurance and process monitoring are also very important in the AM process.”

“With the Freeformer and our comprehensive know-how in the field of plastics processing, we are able to automate the additive manufacturing process and record all of the relevant construction parameters via OPC/UA interfaces. It is becoming more and more important to ensure high quality standards when producing functional parts using additive manufacturing, and to document this process reliably.
Our main focus in 2020?
Think additive! As a machine manufacturer, we need to work with our customers to develop the areas of application for additive manufacturing and make the most of the new degrees of freedom in this field. We will also be focusing on topics such as resource conservation and sustainability, both here and in the injection moulding sector.”
Fedor Antonov, CEO at Anisoprint, 3D Printer manufacturer
“For Anisoprint, 2019 was the year of conquering new territories: “anisoprinting” is now distributed in more than half of Europe with our entry-level product — desktop continuous fiber 3D printer Composer.”

“We also look into the future of the technology: there will be even more possibilities for replacing metals or non-optimal composites with our new ProM IS 500 — an industrial 3D printer specifically designed for printing high temperature thermoplastics with continuous fiber reinforcement.
In 2020, the AM industry will continue to look for better materials, approaches and applications to make additive manufacturing inventions competitive in comparison to traditional technologies. Anisoprint that integrates a team of researchers and engineers with extensive experience in composites will also contribute in this process: we’ll continue to develop continuous fiber 3D printing that tends to become popular due to its advantages. Some of the biggest companies in the AM area have already understood that, and we’re waiting for more in the coming years.”
Keyvan Karimi, Founder & CEO, AMFG, supplier of workflow automation software for additive manufacturing
“2019 was a tremendous year for AMFG, as we witnessed more companies recognising the role of MES software in establishing a scalable, automated and connected additive manufacturing workflow. In 2019, we significantly grew our customer base across industries including automotive, consumer and industrial goods, and opened an office in Germany as part of our company’s expansion.”

“We’re, therefore, extremely optimistic about the industry’s growth in 2020. This year, we predict that AM will continue its shift from rapid prototyping to serial production, and that new and innovative end-use applications will be made possible with the technology.
Additionally, MES software will play an even bigger role in 2020, as more companies invest in 3D printing and seek ways to optimise, automate and scale their operations.
This means that AMFG will continue to develop solutions focused on enabling companies to do just this. This includes initiatives such as enabling machine connectivity, which we began by announcing our partnership with EOS last November. We will also extend the capabilities of our production management and scheduling solutions and to enable further automation of the AM process.
Through these initiatives, we aim to make serial production with AM a reality.”
Filemon Schoffer, Co-founder and CCO of 3D Hubs, online manufacturing platform
“We’ve seen a real shift in 3D printing orders in 2019. More and more small to medium engineering businesses are taking advantage of the prototyping speed and geometric complexity 3D printing has to offer. This has had a significant impact on the adoption rate of 3D printing in the product development process (e.g. the speed and number of iterations), as well as in high-end applications, where the benefits of 3D printed complex parts, outweigh its cost (e.g. unparalleled strength to weight ratio performance in aerospace).”

“Because of this, access to virtually unlimited on-demand 3D printing capacity, as well as a wide breadth of technologies, these relatively small businesses have become globally competitive in hardware development. We expect the adoption rate of 3D printing keeps to accelerate over 2020, as more companies catch on to its huge potential.
At 3D Hubs, we’re gearing up to support this increasing demand in 3D printing by adding ever-faster lead times, more material options, and other manufacturing services including CNC machining, injection molding, and sheet metal fabrication. The faster engineers can receive their prototypes and end-parts, the faster they can iterate and bring their products to market. 3D printing will continue to play a pivotal role in speeding up that process.”
Andreas Hartmann, Co-founder & CEO/CTO of Solukon, specialist in end to end post-processing solutions for Additive Manufacturing
“2019 was a very successful year for Solukon. We have installed many systems and received great feedback from our customers. For example, Materials Solutions as a very forward-thinking company has installed its sixth large depowdering unit and we are very proud to supply technologically leading aerospace companies in USA and Europe.”

“We have also taken major steps in the growth of our company and co-founded AMP+ as a specialized powder solution network. And to top it all off, we won the TCT Award Postprocessing together with Siemens.
We are pleased that the AM industry is increasingly recognizing the need and value of our highly automated depowdering solutions to ensure safe and efficient production.
In 2019, the aerospace and energy industry again pushed AM forward with new lightweight and thermodynamic design. Here in particular, we were able to score points with our new depowdering algorithms for complex geometries.
We also see a great future for parts with large heights such as rocket-engines and will soon be offering a solutions for depwodering 1 metre parts.”
Due to the positive experiences with the cooperation with Siemens, we are now again teaming with other highly specialized AM users in order to step up our experience and consistently advance our technologies.”
Guillaume Boisot, Head of Business Development, e-Xstream engineering, software company
“In 2019, the additive manufacturing industry has been ramping up and has reached a maturity level where simulation plays a central role. Industry is not anymore only investigating topology optimization and fancy geometries but is now rising the right questions: can it be print? how can it be lightweight & strong? can I print right the first time? how can I manage all my data related to the materials, the builds, the powder microstructure, …”

Those are the typical questions we have been answering in 2019 and we expect it will increase in 2020. We predict our additive manufacturing ecosystem will keep growing in 2020 adding more and more materials suppliers, OEM printers, printing bureau, and obviously end-users and support the industrialization of AM.”
Gauthier Wahu, Managing & Technical Director, CoreTechnologie France, software publisher
“2019 marked the launch of our 4D_Additive software. Our first customers, from the automotive, aeronautics and medical industries, have been won over and the marketing prospects for 2020 are excellent”

“Our Texture workshop is acclaimed by the Design and Innovation teams for its ergonomics and printing quality.
In collaboration with our customers, our 2020 developments will focus on productivity and design innovations. This year, our teams will reinforce the technology of the Texture workshop by integrating colour management and plan to add the “Batch Nesting” function to 3D PartFinder. 4D_Additive will also be optimized for SLM technology.
Printed and sublimated colours to make you look good.
4D_Additive will transfer the colors from the texture to the model to be printed for a more coherent and more aesthetic rendering. Technically, the .OBJ output format will allow to transcribe both deformations and colors.”
Tiago Brito e Faro, Head of Engineering at Adira, manufacturer of sheet metal working machinery
“The Market Product Release of Adira‘s Large Metal Printer is set to the end of 2020. While actively searching to increase our beta testers network, we are also consolidating the strategic partnership relations we already have in place
During the upcoming year we have narrowed down a few points that still need fine tunes, focused mainly in the usability of the equipment. These tunes will ultimately improve our final product UX and UI to all our Beta Testers / Customers.”

Alessio Lorusso, Founder & CEO of Roboze, 3D Printer manufacturer
“2019 meant for Roboze contributing to the continuous innovation in the 3D printing technology market. All the innovations Roboze showcased in 2019 address the needs of all those entrepreneurial realities aiming at increasing their productivity thanks to high temperature super polymers and composite materials for the production of finished parts with the highest precision.

We are in the middle of a Fourth Industrial Revolution, where Additive Manufacturing has a key role. The industry is changing quickly, and Roboze constantly analyses the global market’s changes in order to meet the real needs of the final customers. One of the main goals for Roboze will be contributing to the development of those smart factories capable to benefit from the technological advantages resulting from the integration of machines, production processes and final products.
We are aware that manufacturers will increasingly rely on 3D Printing alongside CNC machining, another strong indicator of how essential additive manufacturing is becoming within the production processes.
Europe, United States and Asia are certainly the fastest growing regions where nowadays Additive Manufacturing is developing on a global level. That’s where we are focusing our efforts to increase Roboze’s business growth, especially in the United States. In 2020, our main goal will be to make Roboze 3D Printing solutions a key player in the Industry 4.0 progress by offering high performance materials suitable for Metal Replacement applications and the production of functional prototypes and finishes parts globally.”
Joseph Crabtree, Founder & CEO, Additive Manufacturing Technologies (AMT), specialist in end to end post-processing solutions for Additive Manufacturing
“2019 has been a pivotal year for Additive Manufacturing Technologies (AMT) Ltd.

Founded in 2017, we are now fully commercial, and today there are a growing number of OEMs worldwide that are using our safe, sustainable, and fully automated AM post-processing solutions. Post-processing is one of the key areas of focus as companies seek to integrate additive manufacturing into speedy and cost-efficient production cycles, and the demand is for fully automated solutions that significantly reduce cost-per-part. Our process enhances material characteristics as well as completely smoothing surfaces, and fits within our overall drive towards wholly connected, customized, end-to-end digital manufacturing systems. That is the area in which AMT is operating in order to bring practical industrial solutions to OEMs using AM as a production technology, and will be our continued focus through 2020.”
Kristof Sehmke, Communication Manager, Materialise, Software company & 3D Printing Service bureau
“In 2019, Materialise collaborated with its partners to advance AM technology on many crucial fronts – faster machines, new materials, and more finishing options.

Today, we see all of these advances coming together to create an exciting climate of innovation that will spark entirely new applications that were unthinkable or unachievable before.
As we develop new products and technologies to help our customers create meaningful applications, sustainability needs to become top of mind. Already, AM provides companies with an instrument to manufacture in a more sustainable way – both socially and environmentally. However, that’s simply not enough. Collectively, we need to develop initiatives to reduce energy consumption, to increase usage of recycled powder and to create the workplaces of the future. So, moving forward, the question is not: is AM a more sustainable manufacturing technology? The question becomes: what can we do to make AM more sustainable?”
Guillaume Feliksdal, Co-Founder of FELIXprinters, 3D Printer manufacturer
“2019 was a pivotal year for FELIXprinters as the company established itself as a key player in the industrial additive manufacturing space, offering cost-effective but highly accurate AM platforms for prototyping and production applications. During 2019 we added two larger build area machines to our portfolio, the Pro L and Pro XL, which are now sold into various sectors of industry where the demand is for easy-to-use, accurate, repeatable, and price sensitive AM solutions. The company also has the capacity to customise solutions to specific customer applications, and this is unique in the lower cost industrially-oriented area of the AM market-place.

For 2020, we will continue to position our industrial AM solutions, and will also be promoting our new FELIX BIO machine, which is making waves in the highly dynamic area of 3D printing and biomedical applications.”
This article has originally ben published in the January-February issue of 3D ADEPT Mag.
Featured image: ccam-va.com – Remember, you can post free of charge job opportunities in the AM Industry on 3D ADEPT Media or look for a job via our job board. Make sure to follow us on our social networks and subscribe to our weekly newsletter : Facebook, Twitter, LinkedIn & Instagram ! If you want to be featured in the next issue of our digital magazine or if you hear a story that needs to be heard, make sure to send it to contact@3dadept.com.