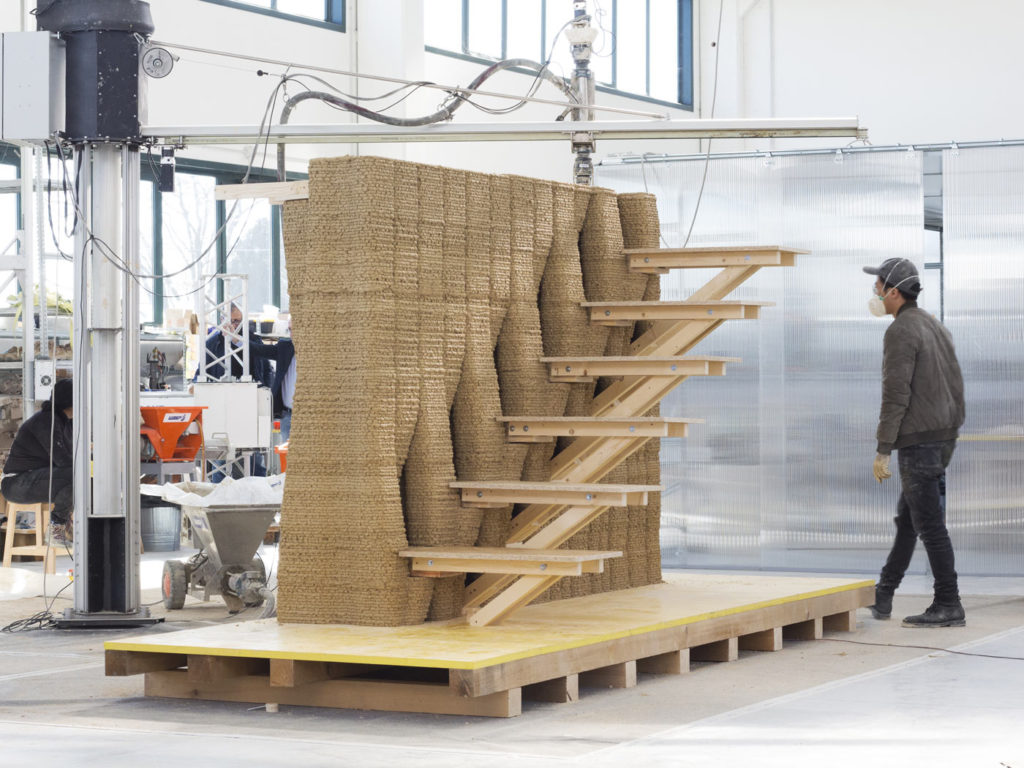
In the quest for using 3D printing for sustainable living, WASP continuously develops projects that can foster the development of construction processes through 3D printing and digital fabrication. The last one is a 3D printed wall with embedded staircase designed by IAAC and produced using Crane WASP technology as part of the Open Thesis Fabrication research.
The latter is a programme of the Institute for Advanced Architecture of Catalonia (IAAC) that focuses on additive manufacturing in the field of construction. At IAAC, students and researchers develop projects that aim to propose urban, architectural and construction solutions arising from the use of new technologies and, in turn, incorporates computer design and analysis to provide innovative solutions for a more sustainable habitat and city.
In this particular case, WASP and IAAC aimed at proposing an architectural solution for affordable sustainable housing for and partially built by the people. Thanks to international networks with universities of architectural design, the team used WASP labs and technologies, enabling ths way all collaborators to participate in the current architecture lines of research.
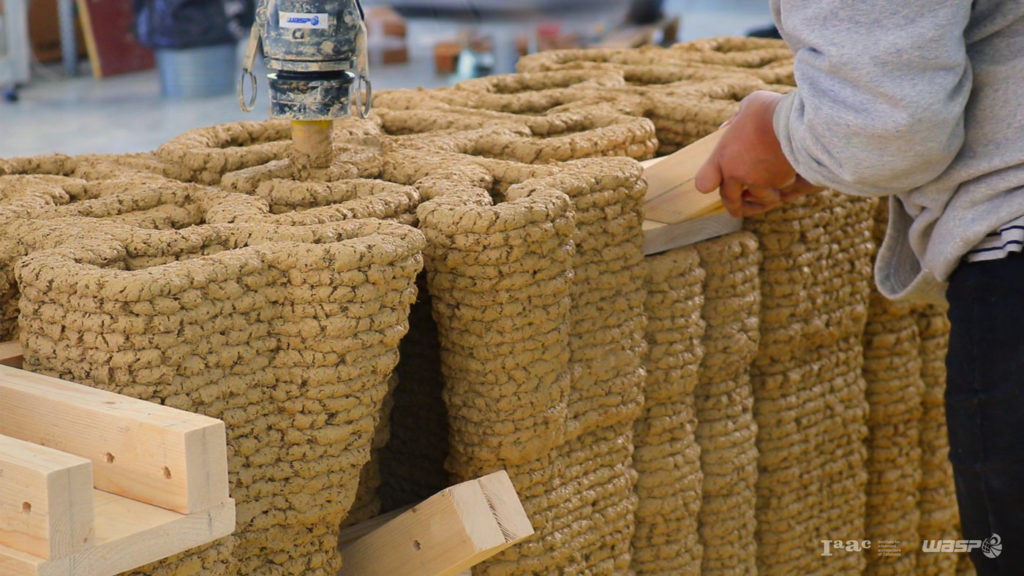
As far as the prototype is concerned, the Italian manufacturer reveals that it represents a wall portion 40 cm thick, with timber elements interlocked, providing support for stairs and floor structures. Designed for being anchored to the printed part, the wall marks a milestone in the realization of load-bearing earthen structures.
It requires a mixture of clay and rice fibres and took 40 hours to achieve the printing process. With an overall material amount of 2 cubic meters, internally modeled multiple surfaces confer both solidity and aesthetic expressivity to the wall.
For further information about 3D Printing, follow us on our social networks and subscribe to our newsletter
Would you like to subscribe to 3D Adept Mag? Would you like to be featured in the next issue of our digital magazine? Send us an email at contact@3dadept.com
//pagead2.googlesyndication.com/pagead/js/adsbygoogle.js (adsbygoogle = window.adsbygoogle || []).push({});