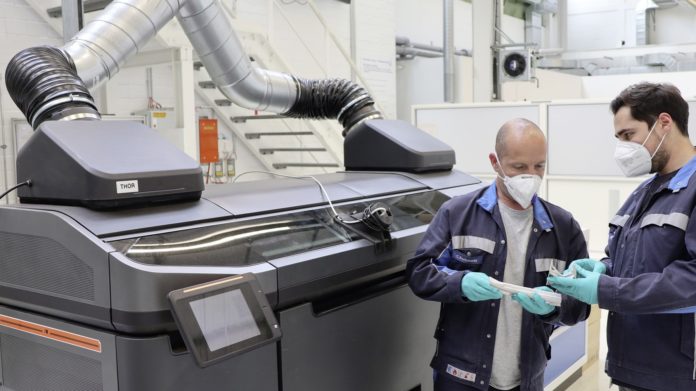
Les premiers composants fabriqués à l’aide du procédé de jet de liant sont allés à Osnabrück pour être certifiés : il s’agit de composants pour le pilier A du cabriolet T-Roc.
Jusqu’à présent, la technologie de fusion sur lit de poudre était le procédé de FA métallique de prédilection du constructeur automobile Volkswagen. Avec la maturité croissante des technologies sur le marché, le constructeur automobile prévoit d’ajouter un autre procédé à la production de ses véhicules : le binder jetting.
Pour rappel, le binder jetting ne consiste pas à utiliser un laser pour construire un composant couche par couche mais plutôt un adhésif.
Pour réaliser cette avancée, Volkswagen a investi un montant de l’ordre de plusieurs millions d’euros au cours des cinq dernières années.
En outre, d’un point de vue technologique, l’entreprise bénéficie du soutien de Siemens au niveau des logiciels. En effet, grâce au logiciel de Siemens, VW optimise le positionnement des composants dans la chambre de fabrication. Connue sous le nom de nesting, cette technique permet de produire deux fois plus de pièces par session d’impression.
Cedrik Neike, membre du conseil d’administration de Siemens AG et CEO de Digital Industries : « Nous sommes très fiers de soutenir Volkswagen avec nos solutions innovantes d’impression 3D. Nos solutions d’automatisation et de logiciels sont à la pointe des applications de production industrielle. Grâce à cette technologie, Volkswagen sera en mesure de développer et de produire des composants plus rapidement, avec plus de souplesse et en utilisant moins de ressources. »
VW a également approfondi sa collaboration existante avec le fabricant d’imprimantes 3D HP Inc, qui fournira le nouvel équipement de fabrication.
Avec la première utilisation à grande échelle du jet de liant, ils ont l’intention d’acquérir une expérience importante et d’apprendre, par exemple, quels composants peuvent être produits économiquement et rapidement à l’avenir ou comment la fabrication additive peut soutenir la transformation numérique de la production dans leur usine.
« Malgré les défis permanents de la pandémie de coronavirus, nous continuons à travailler sur l’innovation« , déclare Christian Vollmer, membre du directoire de la marque Volkswagen responsable de la production et de la logistique. « Avec nos partenaires, nous souhaitons rendre l’impression 3D encore plus efficace dans les années à venir et adaptée à une utilisation sur les chaînes de production. »
Dès l’été, les trois entreprises ont l’intention de mettre en place une équipe d’experts commune au centre d’impression 3D de haute technologie qui a ouvert ses portes à Wolfsburg fin 2018 et permet la fabrication de composants automobiles complexes par impression 3D. Le centre forme également les employés à l’utilisation de ces technologies.
D’ici 2025, l’objectif est de produire chaque année jusqu’à 100 000 composants par impression 3D dans son usine principale de Wolfsburg, en Allemagne. Les premiers composants fabriqués à l’aide du procédé de jet de liant sont allés à Osnabrück pour être certifiés : il s’agit de composants pour le pilier A du cabriolet T-Roc. Ces pièces pèsent près de 50 % de moins que les pièces conventionnelles en tôle d’acier. Cette seule réduction rend le procédé particulièrement intéressant pour les applications de production automobile.
Volkswagen a déjà réalisé avec succès des crash-tests sur des composants automobiles métalliques imprimés en 3D. Jusqu’à présent, la production de volumes plus importants n’était pas assez rentable. Toutefois, la nouvelle technologie et la collaboration rendront désormais l’utilisation sur les chaînes de production économiquement viable.
N’oubliez pas que vous pouvez poster gratuitement les offres d’emploi de l’industrie de la FA sur 3D ADEPT Media ou rechercher un emploi via notre tableau d’offres d’emploi. N’hésitez pas à nous suivre sur nos réseaux sociaux et à vous inscrire à notre newsletter hebdomadaire : Facebook, Twitter, LinkedIn & Instagram !