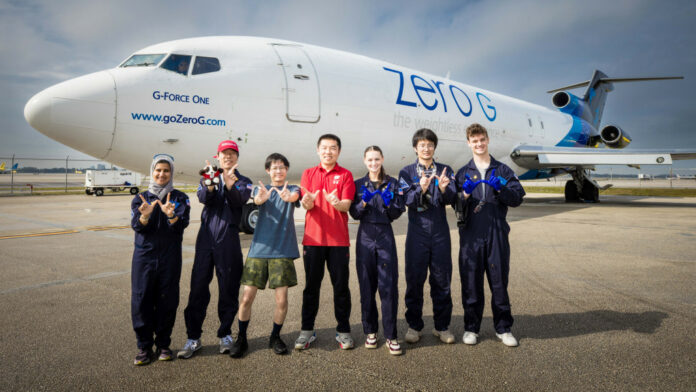
Researchers at the University of Wisconsin–Madison have taken a step toward in-space manufacturing of replacement electronic components by successfully 3D printing RAM device units in zero gravity for the first time.
The group encountered a technical glitch during its first two parabolic test flights — roughly 40-minute jaunts with ascents and dives that simulate brief periods of zero-gravity. The researchers spent the week leading up to their third and final flight troubleshooting potential causes of the glitch during 12- to 15-hour days.
Traditional 3D printing relies upon gravity to extrude material from a printer nozzle, meaning that in-space printing requires a different approach. Hantang Qin’s lab has developed an alternative called electrohydrodynamic, or EHD, printing. Hantang Qin is UW Industrial and Systems Engineering Assistant Professor and lead researcher.
The technique applies electrical force to drive the flow of liquid materials through an extremely thin nozzle that’s only 30 micrometers in diameter, about the average width of a single wool fiber.
“Under this small scale, the surface tension will prevent the liquid from flowing out from this nozzle,” says Qin, whose group is leading the collaboration with researchers from Iowa State University, Arizona State University, Intel and other industry partners. “And then we apply this electrical force to break out of this surface tension force.”
Hantang Qin says EHD printing technology has advantages beyond its ability to function in zero-gravity environments. With traditional 3D printing, nozzle size essentially determines droplet size.
“But using our printing system, we can make the droplet way smaller than the size of nozzle,” he says. “Given a 2-micrometer nozzle, we can make a nanoscale pattern. That’s the huge advantage of this.”
The team eventually pinned down the glitch that hampered testing on the first two flights: Vibrations of the plane’s engine caused an issue with the printer’s calibration sensors. They were able to resolve the problem by rewriting some of their system’s code to compensate for the vibrations, with Pengyu Zhang, a graduate student in electrical and computer engineering, writing code in zero gravity.
All the work paid off during the group’s final test flight. Under the manual control of Wolf and Jacob Kocemba (a 2023 UW–Madison graduate now continuing his studies at the University of Illinois), the lab’s EHD printer successfully produced more than a dozen units with zinc oxide, a semiconducting ink, and a half dozen more with polydimethylsiloxane, an insulating polymer ink.
While the researchers could see their printer was working as they floated around the plane’s cabin, they couldn’t confirm their results on the micro- and nanoscales until huddling around a microscope in their makeshift research lab set up in a hangar at the airport.
The researchers are planning to return to Florida in August and November 2024 for two more test flights, during which they’ll attempt to incorporate their EHD technology into an industry partner’s multi-tool 3D printer, and then progress from printing individual units to full semiconducting devices. If they can meet those project milestones, then they hope to launch their technology for testing aboard the International Space Station.
Read more about zero gravity operations enabled by Additive Manufacturing.
NASA is funding this research in an attempt to develop in-space manufacturing capabilities for electronic components such as semiconductors, actuators and sensors.
Remember, you can post job opportunities in the AM Industry on 3D ADEPT Media for free or look for a job via our job board. Make sure to follow us on our social networks and subscribe to our weekly newsletter: Facebook, Twitter, LinkedIn & Instagram ! If you want to be featured in the next issue of our digital magazine or if you hear a story that needs to be heard, make sure you send it to contact@3dadept.com