L’industrie ferroviaire est souvent considérée comme plus « traditionnelle » que les secteurs automobile et aérospatial lorsqu’il s’agit d’adopter les nouvelles technologies dans l’industrie manufacturière. Avec le besoin croissant de faciliter la production et les travaux de maintenance, les entreprises se tournent progressivement vers la fabrication additive.
Le choix de cette technologie s’accompagne d’une série de défis que les entreprises de transport doivent relever. Ces défis varient d’un pays à l’autre, et parfois, d’une entreprise à l’autre car ils nécessitent une compréhension approfondie des rôles des parties prenantes : opérateurs, entreprises de maintenance et fournisseurs de matériel roulant.
« Dans toute l’Allemagne, les exploitants de trains s’occupent des opérations quotidiennes des trains et jouent le rôle de gardiens des transports publics. Les sociétés de maintenance assurent la disponibilité et parfois l’attrait des trains, tandis que je définirais les fournisseurs de matériel roulant comme les fournisseurs de véhicules ferroviaires et d’infrastructures au propriétaire – qui pourrait être l’exploitant ou une société de location. En ce qui concerne Siemens, nous pouvons remplir chacun de ces rôles, de sorte que nous sommes en mesure de soutenir nos clients avec un portefeuille complet, en fonction de l’installation et de la demande », déclare Michael Kuczmik, responsable de la fabrication additive/services à la clientèle de mobilité – Siemens Mobility.
« Chez Bombardier, nous fonctionnons de la même manière. Parfois, nous sommes le seul fournisseur de matériel roulant, tout en étant responsable de la maintenance et de l’exploitation efficace des réseaux ferroviaires. Tout dépend du modèle économique de nos clients », complète André Bialoscek, responsable de l’intégration physique des véhicules, Hennigsdorf – Bombardier Transport.
« Au Royaume-Uni, il est quelque peu fragmenté. Nous avons les fournisseurs de matériel roulant qui financent les trains et les louent aux opérateurs de trains. Les opérateurs de trains assurent les services quotidiens et la maintenance de base. Ensuite, nous avons des sociétés de maintenance et de révision qui assurent les grands travaux de remise à neuf et de révision des véhicules, et enfin nous avons des sociétés de soutien en ingénierie comme DB ESG qui fournissent des services techniques à l’industrie », explique Martin Stevens, directeur de l’ingénierie mécanique – Deutsche Bahn ESG.
Bombardier Transport, Deutsche Bahn ESG et Siemens Mobility sont des entreprises de transport basées en Europe qui partagent la même volonté d’utiliser les technologies de fabrication numérique pour faire avancer la production dans l’industrie ferroviaire. Toutefois, l’utilisation de ces technologies s’accompagne de défis en termes de vitesse et de coûts. Kuczmik, Bialoscek et Stevens partagent leurs points de vue sur la manière dont leur entreprise surmonte ces défis.
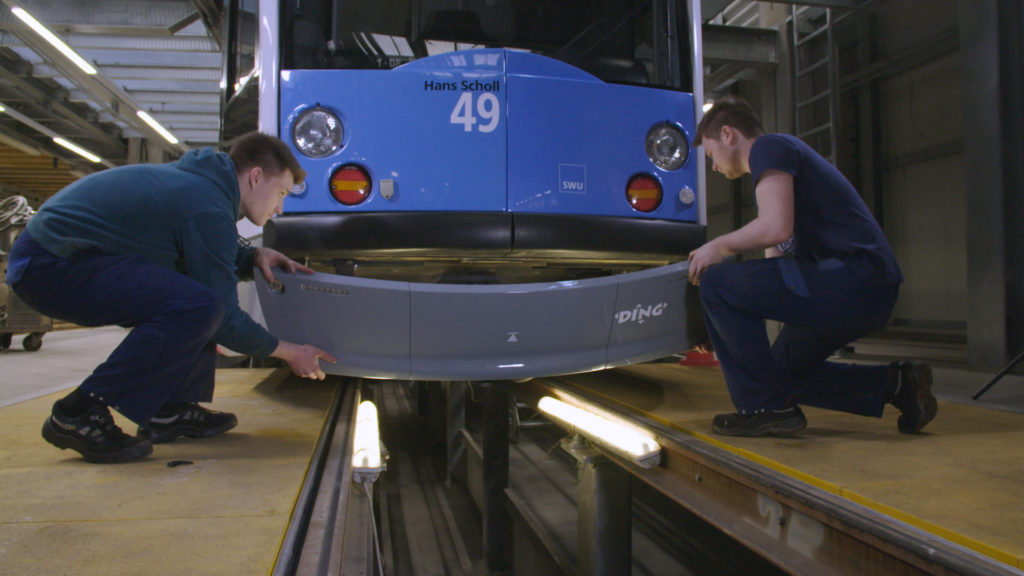
Atteindre de faibles volumes de production tout en maintenant de faibles coûts
Un seul train peut fonctionner pendant plus de trois décennies avant d’être retiré du marché. Au fil du temps, ce train peut nécessairement avoir besoin de maintenance et de réparation de pièces de rechange. La seule chose est que ces pièces de rechange ne peuvent pas toujours être produites en masse car tous les trains n’ont pas besoin des mêmes pièces de rechange, sans compter que les fabricants développent toujours des conceptions de train différentes, ce qui apporte une complexité supplémentaire au niveau de la production.
À cet égard, les faibles volumes de production s’avèrent être une solution viable pour répondre aux besoins de maintenance et c’est là que la FA entre en jeu.
« Nous devons livrer les trains beaucoup plus rapidement qu’il y a trois à cinq ans. Cela augmente la pression générale sur toutes les facettes de nos opérations, y compris l’ingénierie, l’approvisionnement, la fabrication et les essais/homologation. Nous devons constamment nous adapter rapidement à l’évolution constante du marché, ce qui nous oblige souvent, en tant qu’entreprise, à relever le défi de rester en tête. C’est là qu’intervient la fabrication additive », explique M. Bialoscek.
Quelques applications de la FA dans l’industrie ferroviaire comprennent les bouches d’aération, les pièces de carter avant (tramways) ou même les poignées de maintien intérieures.
« Si cinq ouvertures d’aération étaient nécessaires pour une petite flotte de trains, cela ne peut être réellement réalisé qu’avec la fabrication additive. Bien que le coût unitaire soit plus élevé, vous pouvez en acheter cinq et les recevoir en quelques semaines, plutôt que d’en acheter 10 000 et les recevoir en trois mois. Les énormes avantages l’emportent de loin sur les petits inconvénients. En fait, nous nous sommes récemment associés à Angel Trains, l’un des trois grands fournisseurs de matériel roulant du Royaume-Uni, et à l’opérateur ferroviaire Chiltern Railways, pour déployer et tester avec succès les premières pièces imprimées en 3D dans les trains de voyageurs britanniques », souligne M. Stevens.
En ce qui concerne le processus de fabrication des poignées intérieures, par exemple, DB ESG utilise le matériau en résine Stratasys, conforme aux normes en matière d’incendie, de toxicité et de fumée ULTEM™ 9085. Ce matériau est d’autant plus important qu’il intègre des propriétés qui facilitent la certification des pièces de rechange en conformité avec toutes les normes, lois et règlements régissant l’industrie ferroviaire.
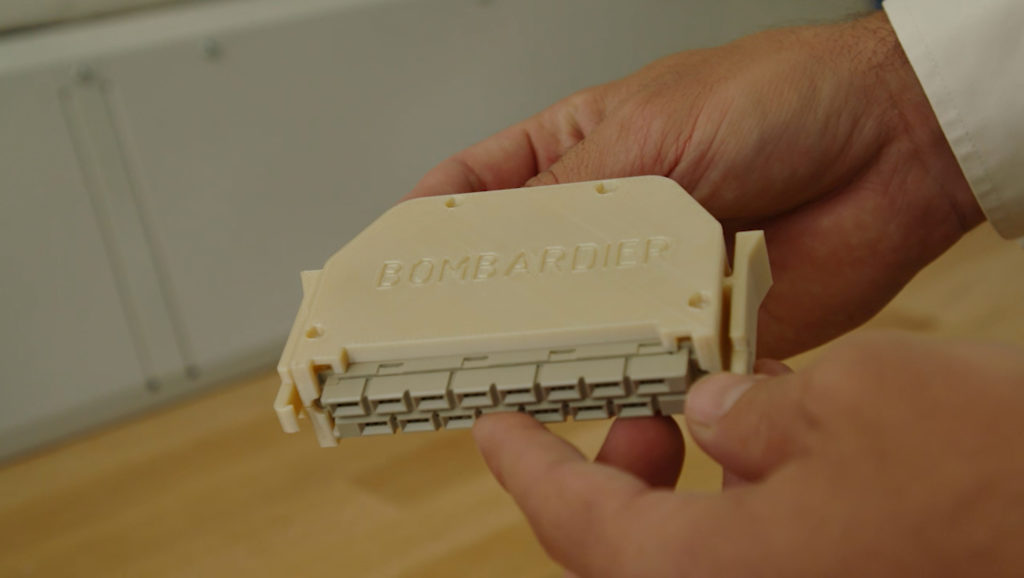
« Les certificats types contiennent les propriétés du matériau comme la résistance au feu et l’allongement à la rupture, ainsi que les calculs de résistance spécifiques aux pièces. Comme les pièces peuvent avoir une incidence sur la sécurité, une mise à jour de l’analyse des risques pour l’ensemble du système est souvent nécessaire. C’est pourquoi nous utilisons également le site ULTEM™ 9085, « matériel conforme à la sécurité incendie », complète Kuczmik.
Le responsable de la fabrication additive/services à la clientèle de Siemens Mobility va plus loin. En effet, ces entreprises de transport peuvent désormais s’occuper du remplacement des pièces détachées mais pour maintenir de faibles coûts de production, il est crucial de ne fabriquer ces pièces que lorsqu’elles sont nécessaires, d’où la nécessité d’un inventaire numérique. La réalité est qu’avec l’entrepôt numérique, les fabricants peuvent avoir un accès instantané aux fichiers de conception, ce qui facilite une production plus agile et en flux tendu.
« Nous sommes convaincus que le passage au stock virtuel est essentiel pour aller de l’avant – au moins pour les pièces de rechange correctives, pour lesquelles nous ne savons pas exactement si, quand et à quelle fréquence elles seront nécessaires. Siemens Mobility offre déjà cette possibilité grâce à notre concept Easy Sparovation. Celui-ci comprend plusieurs options possibles : commande standard dans les délais de livraison habituels en raison des contraintes de production classiques, livraison dans les vingt-quatre heures en Europe à partir de notre stock, et impression à la demande. L’entreprise de maintenance ou l’opérateur peut décider en fonction de l’urgence du besoin », informe le porte-parole de Siemens Mobility.
À l’avenir, les sociétés de transport développeront de nouvelles applications dans le secteur ferroviaire et imprimeront des pièces plus grandes. Comme la production locale devient de plus en plus essentielle, les opérateurs devront assurer une connexion plus solide entre un inventaire numérique, des systèmes de FA et un logiciel d’impression 3D, en particulier les logiciels MES (Manufacturing Execution System).
N’oubliez pas que vous pouvez poster gratuitement les offres d’emploi de l’industrie de la FA sur 3D ADEPT Media ou rechercher un emploi via notre tableau d’offres d’emploi. N’hésitez pas à nous suivre sur nos réseaux sociaux et à vous inscrire à notre newsletter hebdomadaire : Facebook, Twitter, LinkedIn & Instagram !