L’impression 3D métal a prouvé à maintes reprises son efficacité dans de nombreuses applications, si bien qu’elle est presque toujours citée comme la voie à suivre dans les applications exigeantes. L’une des principales limites que les experts déplorent souvent est son coût élevé par rapport à d’autres techniques de fabrication additive (FA), en particulier lorsqu’il s’agit de production de masse. Cela incite les équipementiers à explorer les capacités de la FA avec d’autres matériaux qui pourraient potentiellement servir d’alternatives aux métaux. Une catégorie qui mérite d’être mentionnée aujourd’hui est celle des composites, qui bénéficient d’un siècle de recherche sur la production de composants à l’aide de techniques soustractives. Cependant, lorsqu’ils sont combinés à la FA, quelques points doivent être pris en compte : Quel type de matériau serait une bonne alternative aux pièces métalliques imprimées en 3D ? Pour quel objectif de fabrication ? Y a-t-il des choix spécifiques de fabrication et de conception à prendre en compte ? L’article ci-dessous tente de répondre à ces questions.
Nous avons déjà eu une première introduction à l’impression 3D de matériaux composites et aux premières étapes à suivre lorsqu’on travaille avec cette jeune branche de la FA. Les sociétés de FA peuvent l’appeler « la branche la plus jeune de la FA« , mais pour moi, les composites sont comme les alliages. Je trouve fascinant de voir le nombre de matériaux qui peuvent être combinés pour offrir une gamme spécifique de propriétés physiques et chimiques – et former au final un seul matériau qui sera imprimé en 3D pour fabriquer une pièce.
Les applications de la FA dont nous avons déjà été témoins avec les composites montrent que ces matériaux offrent des possibilités d’allègement – ce qui est la marque de fabrique de la FA – et, ce qui est intéressant, la possibilité de construire sur un outil personnalisé.
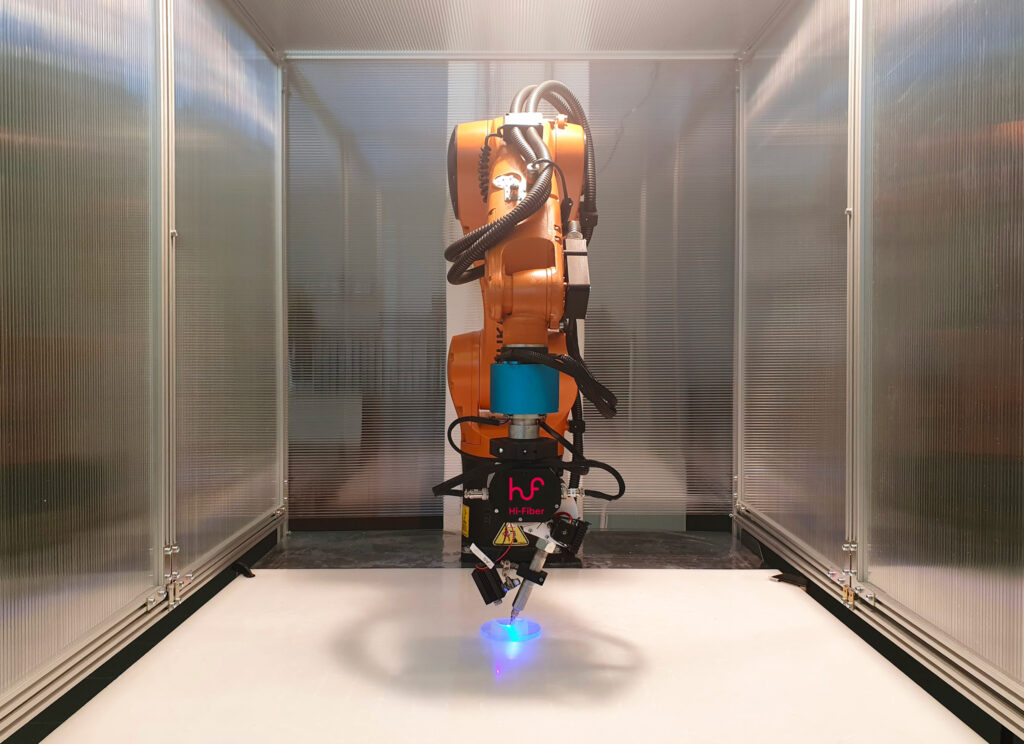
Par ailleurs, l’un de nos premiers dossiers sur les composites révèle que deux types de fibres de renforcement sont compatibles avec la technologie de FA : les fibres coupées et les fibres continues. Selon Michele Tonizzo, directeur technique de Moi Composites, une entreprise spécialisée dans la fabrication de fibres continues, « d’un point de vue structurel, les performances obtenues grâce à l’utilisation de composites à fibres continues sont imbattables, avec une résistance à la traction supérieure à 1,5 GPa (*1) et atteignant 30 fois celles des polymères renforcés par des fibres coupées (*2). Malheureusement, la limitation intrinsèque d’avoir une pièce cohérente et toujours solide pendant l’extrusion limite les complexités géométriques que l’on peut obtenir en utilisant seulement une approche mono-matériau. C’est pourquoi l’approche mise au point par Markforged et Anisoprint, et étendue en trois dimensions par Moi Composites, est la meilleure découverte à ce jour. En déposant des matrices non renforcées, ou renforcées par des fibres hachées, capables de décrire des géométries complexes, et des matrices renforcées par des fibres continues uniquement aux endroits stratégiques, ce qui permet également de réduire les temps d’impression, il est possible d’obtenir des pièces structurelles présentant des géométries complexes telles que des cavités et des renforts internes. L’approche conçue par Moi Composites porte cette idée à un niveau tridimensionnel. En fait, en tirant parti de la liberté multiaxiale des robots, il est possible de décrire des géométries complexes à l’aide de polymères renforcés de fibres courtes, puis d’ajouter des couches de fibres continues unidirectionnelles suivant la géométrie externe pour obtenir l’intégrité structurelle souhaitée ».
Il y a toujours eu une bataille entre les partisans du renforcement par fibres coupées et ceux du renforcement par fibres continues. Dans cette optique, il est important de garder à l’esprit que chaque matériau possède son propre ensemble de caractéristiques, de domaines d’application et de technologies qui lui sont associés.
Le tableau ci-dessous résume quelques-unes des caractéristiques les plus importantes relevées jusqu’à présent :
Renforcement par fibres continues | Renforcement par fibres coupées |
Plus de résistance et de rigidité : sa résistance réside dans la continuité des brins qui peuvent absorber et répartir les charges sur toute leur longueur. | La rigidité peut être améliorée de manière significative en fonction du matériau. |
Décrit comme plus solide et plus fiable que les structures métalliques | Idéal pour améliorer la qualité de surface, la résistance à l’usure ou encore l’aspect d’une pièce tout en réduisant le poids de celle-ci |
Compatible avec plusieurs technologies | Matériau moins cher |
Lorsque nous parlons d’impression 3D aérospatiale avec des matériaux composites, même s’il y a une utilisation prédominante du renforcement par fibres continues, nous avons remarqué quelques applications composées de matériaux de renforcement par fibres coupées.

Tonizzo a participé à plusieurs projets visant tous à réduire le poids ou les délais d’exécution des pièces aérospatiales. Selon lui, l’un d’entre eux, particulièrement réussi, visait à réduire le poids total de l’avion en redessinant des pièces non structurelles, en l’occurrence les supports qui fixent les sièges au plancher. « La réduction du poids est venue de l’élimination de matériaux ne contribuant pas à l’intégrité structurelle tout en maintenant l’unidirectionnalité et la continuité des fibres, ce qui est impossible avec les méthodes traditionnelles manuelles ou automatisées de production de composites », explique-t-il.
« La pièce obtenue présente des performances mécaniques similaires tout en réduisant le poids de manière significative. D’après mon expérience, l’avantage concurrentiel de la fabrication additive de composites pour le remplacement de pièces métalliques dans un environnement de production a presque toujours été lié aux performances que l’on peut obtenir en créant des géométries en treillis, ce qui augmente les performances de résistance par rapport au poids de la pièce », ajoute Tonizzo.
Il est intéressant de noter que, qu’il s’agisse de FA ou de procédés de fabrication conventionnels, le facteur le plus important qui conduit à l’utilisation de composites plutôt que de métal reste « les performances de résistance au poids que l’on ne peut obtenir qu’avec des polymères unidirectionnels renforcés par des fibres de carbone » – selon Tonizzo.
Applications et limites
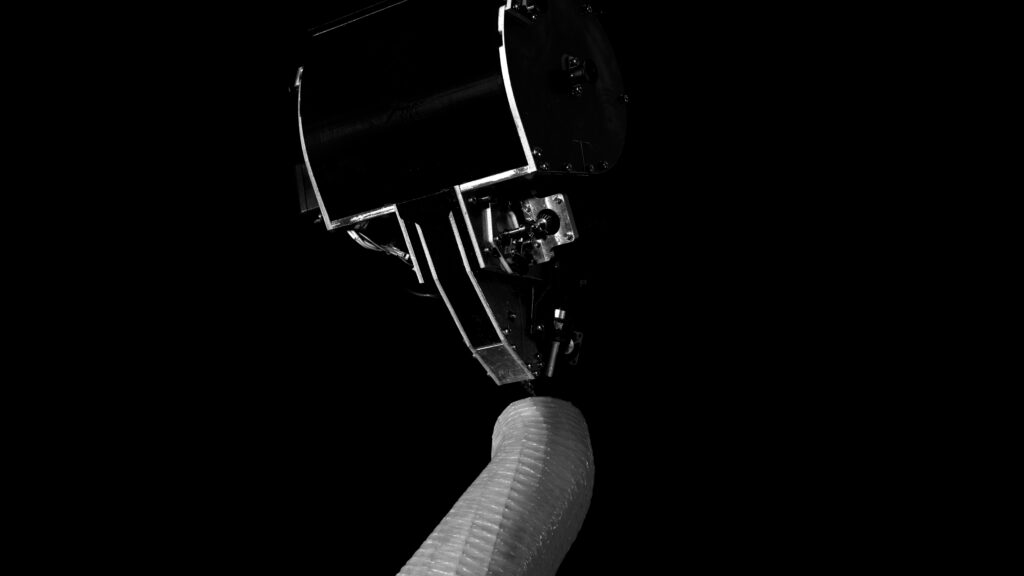
Si les crochets ont été mentionnés comme une application clé de la FA aérospatiale, la FA des composites reste également un candidat idéal pour la production d’attaches, également utilisées dans les aérostructures. Malgré la complexité de cette application, Thermwood a démontré à plusieurs reprises que l’outillage en autoclave peut être une application clé de la FA des composites dans l’industrie aérospatiale.
D’autres possibilités de développement des composites pourraient consister à combiner la FA avec les processus de fabrication de composites existants. Une entreprise qui travaille discrètement dans ce domaine est Electroimpact, une société américaine qui est également un fournisseur de Boeing. Electroimpact a mis au point une solution pour appliquer les composites sur l’avion Boeing 787. Cette solution combine le placement automatisé de fibres ou AFP. L’entreprise explique qu’elle « a intégré un processus d’AFP thermoplastique in situ hors autoclave et un processus d’impression 3D FFF avancé dans un système unifié de fabrication additive robotisée de composites évolutifs (Scalable Composite Robotic Additive Manufacturing, SCRAM). SCRAM est une véritable imprimante 3D industrielle à 6 axes continus, renforcée par des fibres, qui permet la fabrication rapide et sans outil de structures composites intégrées de qualité aérospatiale. Des thermoplastiques haute performance combinés à un pourcentage élevé de renforcement par fibres continues sont utilisés pour produire des pièces aux propriétés matérielles exceptionnelles, inédites dans le monde de la fabrication additive ».
La solution d’Electroimpact est unique en son genre dans l’industrie et nous espérons en entendre parler davantage à l’avenir.
La question à laquelle il faut encore répondre est celle de la finalité de la fabrication : la FA des composites ne permet-elle que le prototypage et la production de faibles volumes ? Pour le directeur technique de Moi Composites, la FA des composites reste l’une des rares technologies où l’impression 3D peut être utilisée dans un environnement de travail, et pas seulement pour la production de faibles volumes.
« J’ai constaté qu’un produit conçu dès le départ avec la fabrication additive à l’esprit est plus facile à mettre en production qu’une nouvelle conception d’une pièce existante. Par exemple, « Hi-Fiber », le produit de renforcement dentaire développé par Moi Dental, la spin-off de Moi, a été conçu et ne peut être produit qu’avec la fabrication additive de composites, avec des milliers de pièces produites par an. Étant donné que la production en grand volume de pièces composites n’est pas étroitement comparable aux quantités produites par moulage par injection de plastique, je suis convaincu que, si la pièce possède une valeur ajoutée suffisante, elle peut être produite en grand volume avec les technologies de FA », souligne M. Tonizzo.
L’attente de Tonizzo implique inconsciemment une limitation qui entraînerait des coûts si/quand la FA des composites est explorée dans des applications de masse. Au niveau technologique, il mentionne également certaines des complexités peu évoquées des composites à fibres continues : ils ne peuvent pas être fondus et mis en forme, taillés ou fraisés à partir d’un objet solide.
« Contrairement aux autres méthodes de fabrication, il est extrêmement difficile d’obtenir des performances élevées à partir d’une pièce produite couche par couche, car elles souffrent encore plus du comportement anisotrope de l’impression 3D. Toutes ces limites sont bien connues et déjà résolues par les fabricants de composites qui, au contraire, apprécient grandement l’approche numérique apportée par la FA à l’industrie des composites. Par conséquent, l’adoption de la FA ‘CFC’ est plus facile pour les fabricants de composites que pour les industries de FA. En raison du lourd travail de conception et de fabrication nécessaire pour produire une pièce à l’aide de la FA ‘CFC’, je doute qu’il y ait un « Shapeways » pour les composites, malheureusement », conclut-il.
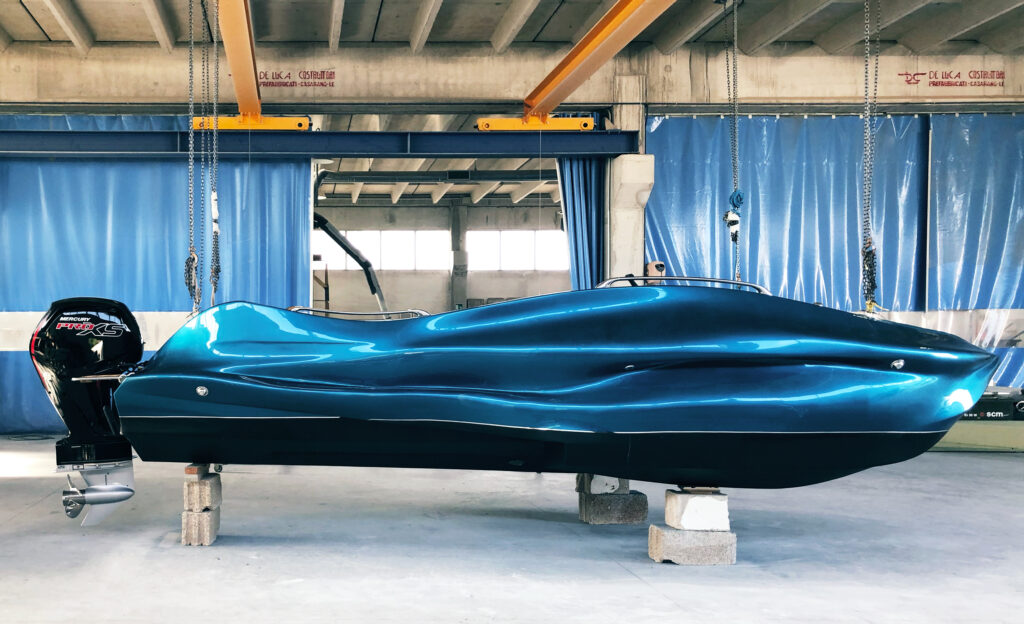
Notes de l’éditeur
Michele Tonizzo – le contributeur clé qui a partagé ses idées sur ce sujet – est le cofondateur et président de Moi Composites, une entreprise spécialisée dans l’impression 3D de matériaux composites qui est apparue sur notre radar lorsqu’elle a présenté un bateau en fibre de verre imprimé en 3D au salon nautique de Gênes en 2020. Avant de fonder Moi, il était responsable de la recherche à l’université Politecnico di Milano +LAB, où il étudiait de nouvelles méthodes de FA pour les matériaux polymères, et lauréat du prix le plus prestigieux pour l’innovation dans le domaine des composites, le JEC Innovation Award 2017.
Moi Composites se concentre désormais sur le développement industriel de Sistema, son système de bout en bout visant à simplifier la production de composites par la robotique et la FA. Avec le programme bêta qui sera bientôt lancé, l’entreprise recherche activement les premiers adopteurs et testeurs de Sistema dans les départements R&D des universités et des industries.
Références :
*1 : Baur JW, Abbott AC, Barnett PR, et al. Mechanical properties of additively printed, UV-cured, continuous fiber unidirectional composites for multifunctional applications. Journal of Composite Materials. 2023;57(4):865-882. doi:10.1177/00219983221146264
*2 : Informations basées sur la fiche technique du matériau Onyx ESD de Markforged.