The 18th version of Rapid.Tech 3D | Additive Manufacturing Hub reminded us that it is one of the most important Additive Manufacturing events to attend in Germany. The return of the physical event Rapid.Tech 3D proved to everyone involved that after last year’s digital version the industry is more than resilient and ready to push innovations forward across various fields of activity. The gathering that was held from May 17th to 19th in Erfurt (Germany) displayed an ideal platform for visitors and exhibitors who wanted to share their knowledge and their latest developments.
The event was composed of forums at all levels: the conferences in the congress centre, the exhibition hall that connected all the exhibitors (manufacturers of 3D printers, manufacturers of materials, developers of software, manufacturers of post-processing solutions, manufacturers of parts & AM users) while encouraging knowledge sharing and the supporting programme, that involved three core activities made for and by Start-ups to present their fresh ideas: 3D Pioneers Challenge, the Workshop Area, and the 3D Printing Conference.
The event highlighted an emphasis on networking and community building, which remained a top priority under the theme ‘Understand, see, experience’. Over 100 exhibitors and more than 80 speakers from Germany, Austria, France, Poland, Sweden, Spain, Switzerland, the Netherlands and the USA set the tone for the show.
As Daniel Hund, Head of Marketing at AM Solutions noted: “The Rapid.Tech 3D is a fantastic place to exchange ideas with AM experts, but also to network. The congress program has an absolute top level, from which also the exhibitors in the accompanying exhibition area absolutely benefit from.”
The main trends of the industry exemplify the versatility AM players are currently aiming for. It is worth thinking that the convergence with traditional industries is more feasible:
- New machines and developments
- Applications for the Automotive industry
- Aircraft applications
- Change to mass-production
- Medicine
- Academia
Three first keynotes settled the start of the event: firstly, Falk Heilfort of Porsche AG on the use of additive manufacturing in e-drive (he focused on the general output to improve efficiency through component integration). Frank Rethmann, Head of the Industrial Service Center 3D Printing department at Airbus Helicopters came next and highlighted the challenges of upstream and downstream work throughout the printing process. Lastly, Fabian Gafner Head of Engineering from Sauber technologies AG presented the results on how the broken gearbox of a 70-year-old Ferrari could be renovated by exploring state-of-the-art in past designing methods and reproducing the outer geometry of the car by using additive manufacturing.
Latest developments and challenges of the past
Rösler Oberflächentechnik GmbH under its post-processing division AM Solutions, showcased the C1 machine for the first time in public. The machine enables the full automatic post-processing of 3D printed polymers and enhances efficiency while delivering shorter processing times. The photopolymer resins faced two main challenges in the post-processing of 3D printed components: first, removing the support structures on the 3D printed parts is complex; secondly, operators need to deal with a certain level of toxicity. The special development of the Bavarian company therefore allows a non-hazardous processing of polymers as the C1 uses convenient processing compounds. This non classification of the compound as hazardous material adds a very important value to the stability of the process and the reduced operational costs.
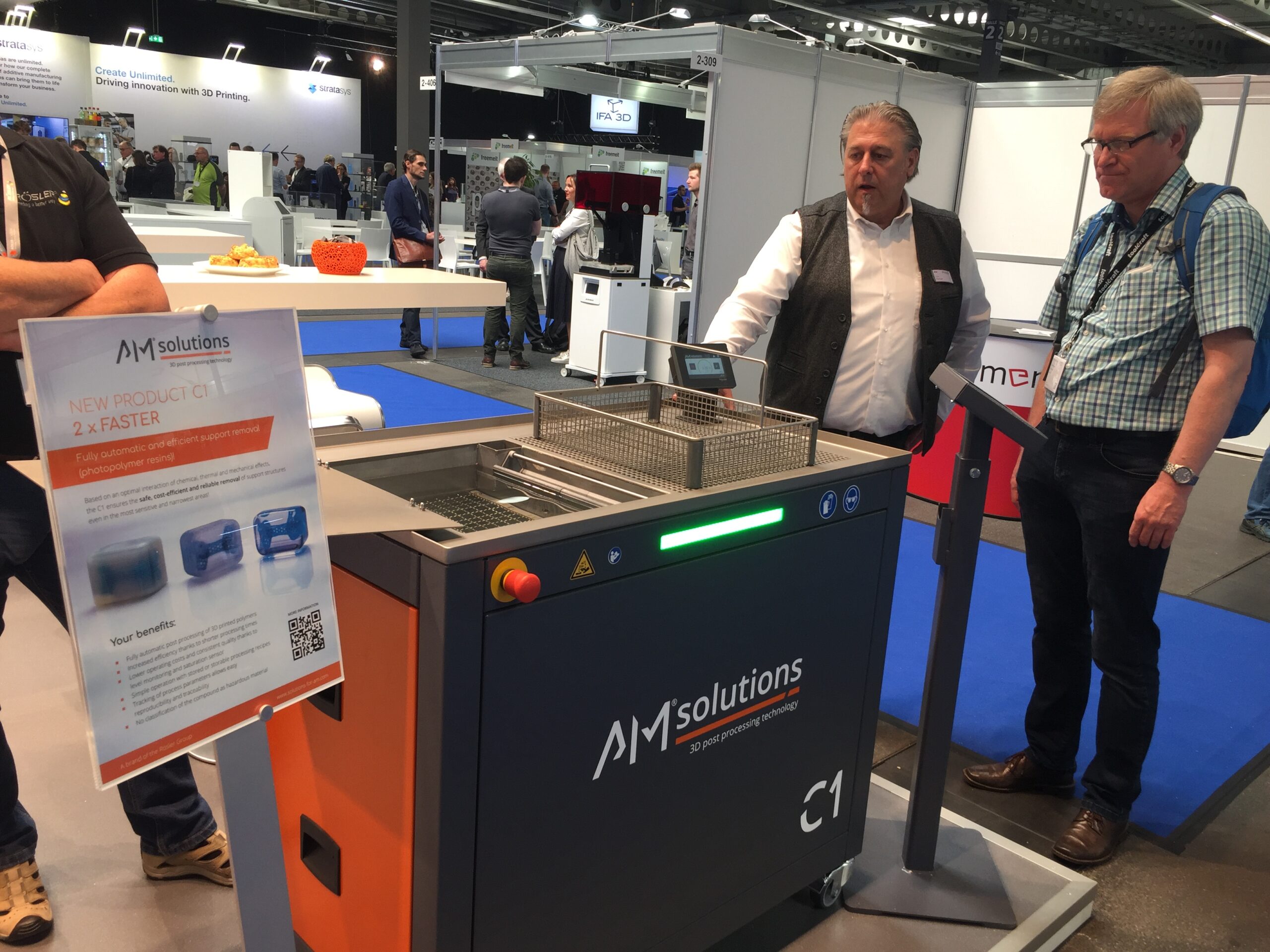
Similarly, Genera, the Wien based start-up with their automatisation process can deliver interesting production results by combining the capabilities of the G2 machine – a DLP system that allows the production of both large components and highly detailed smaller components – with the UV-post curing chamber in the cleaning process. The integration of the process is possible by achieving a confluence of the two technologies of the G2 and F2 machines; the workflow allows the parts to be automatically cleaned after the printing process.
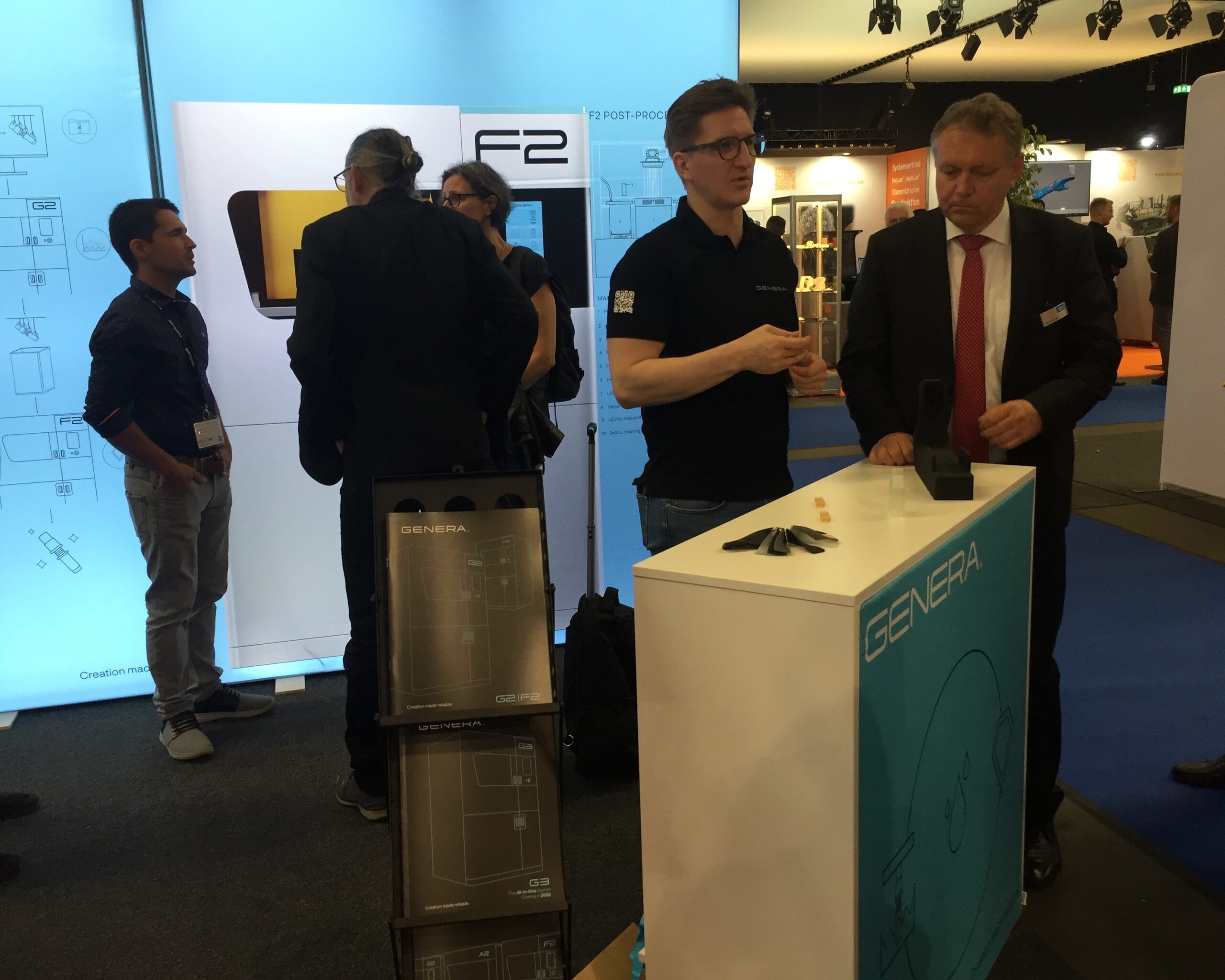
However, let’s not forget one of the trends that were already being defined since Frankfurt’s Formnext 2021. We know how Stratasys through its PolyJet technology achieved an important step in high-performance materials. The OEM is currently paving the way to large-scale production of polymer units with new developments like the recently launched Origin One. Furthermore, a new range of high-performance materials enables applications in different businesses from aerospace, to medical, automotive, and also footwear industries.
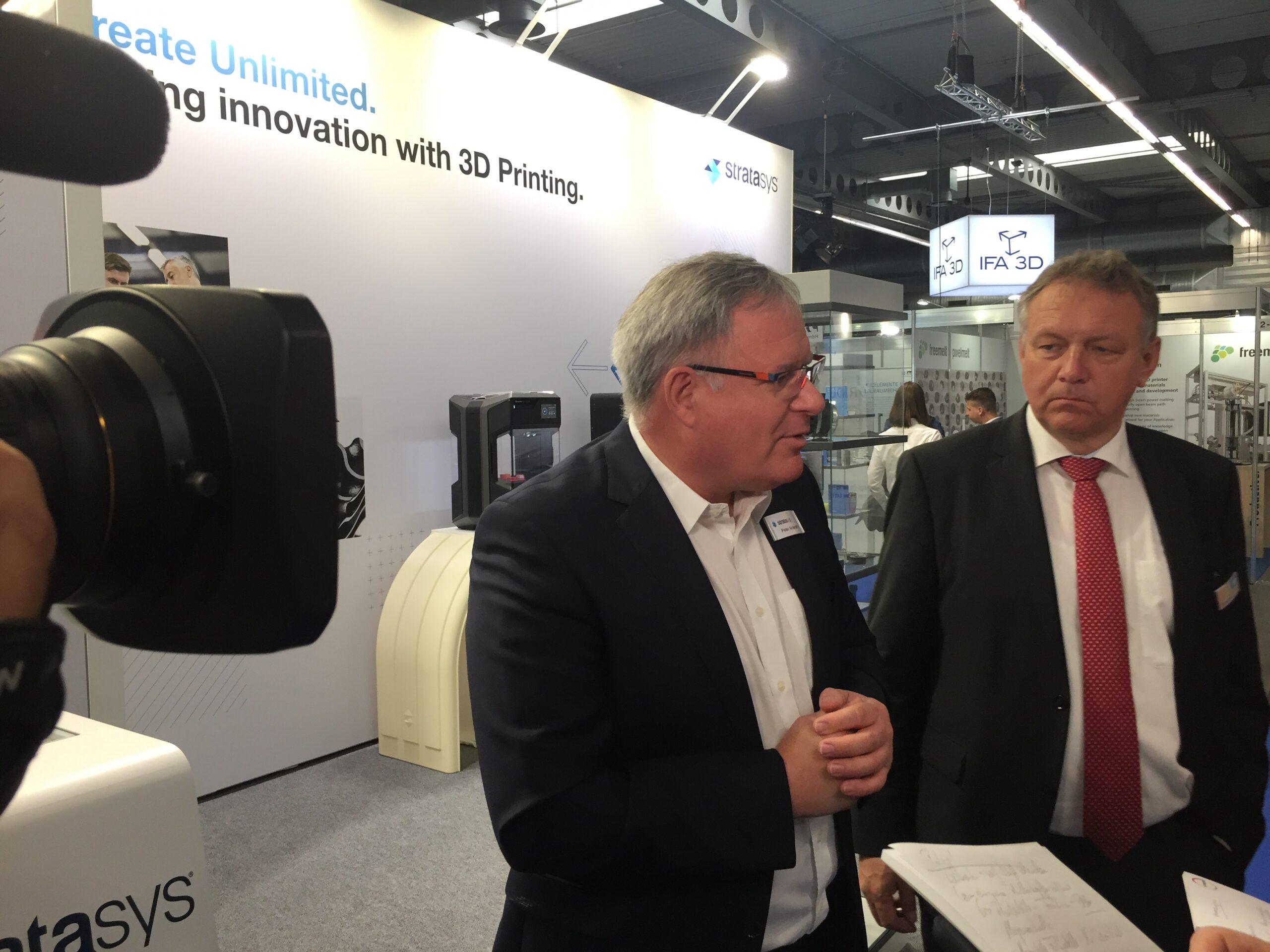
The variety of materials available for the J850™ TechStyle include:
- VeroTM & VeroUltraTM + VeroVividTM colors • Agilus30TM Clear, Black, White, Cyan, Magenta, Yellow
- Transparent VeroClearTM and VeroUltraTM Clear
- VeroTM ContactFlex for soft touch model coating
Speaking of mass production, General Manager Peter Alderath, stated that these material developments and the recently launched technologies can achieve a new level of speed while delivering cost efficiency within the value chain. Technologies such as Stratasy’s SAF Technology (powder bed fusion) or the introduction of the newest Origin One (DLP Technology) are therefore designed for users interested in producing parts at industrial scale.
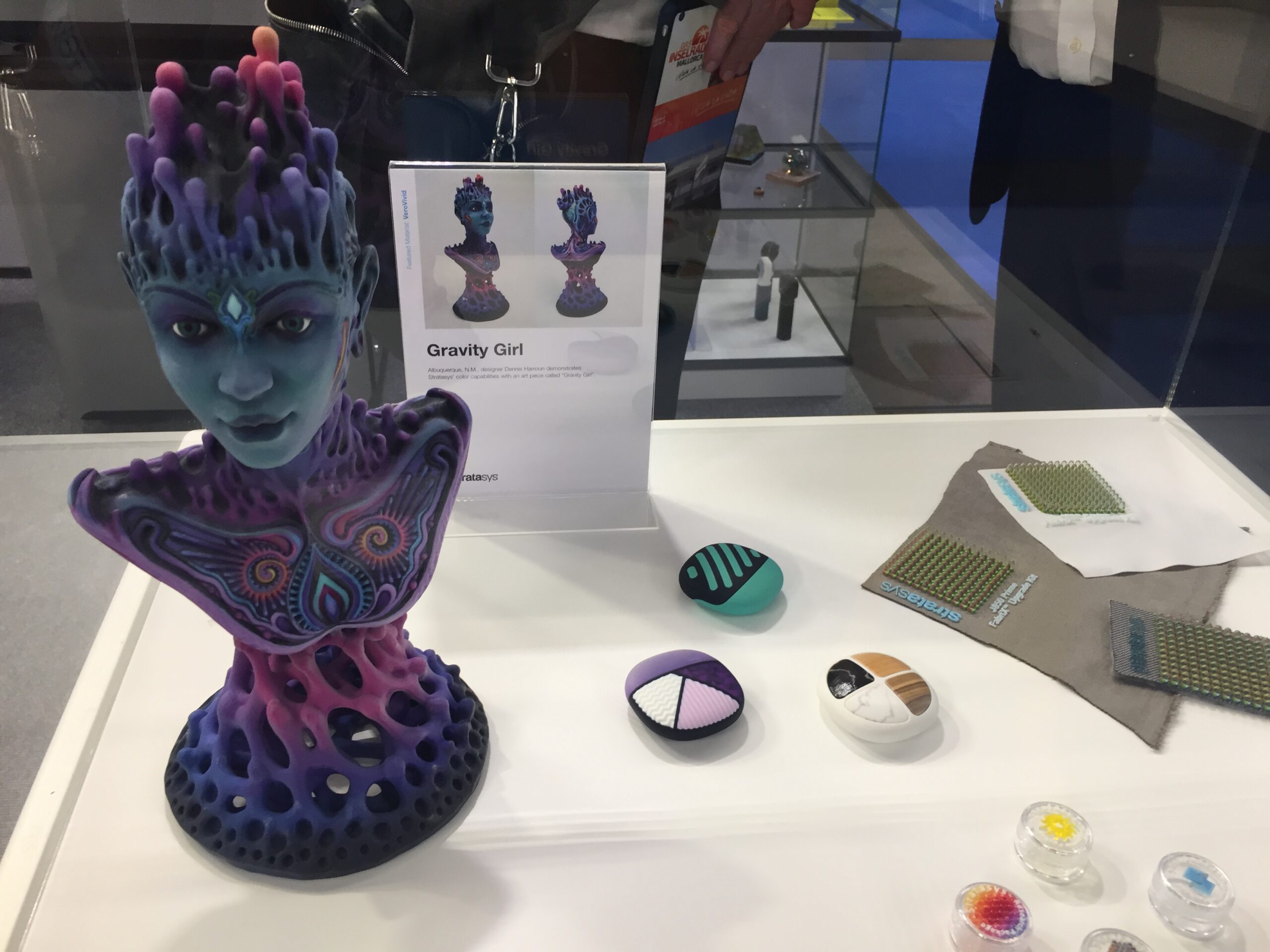
From AM manufacturers to AM users: the aerospace industry
The aerospace industry has been using AM to add components within the processes of engines and designs for some time. The last day at Rapid.Tech was dedicated to this industry. However, it is gaining ground concerning the convergence with AM technologies. Conveniently, last month, Sintavia’s CEO Brian Neff told 3D ADEPT Media about the directions the commercial aerospace market is taking to embrace holistic integration. Specifically, and in the context of the event, MT Aerospace AG, participated for the first time to introduce themselves to the industry. The company currently overcomes the most important barriers in AM aerospace while exploring new possibilities for new applications.
Robert Bonné (Sales Additive Manufacturing in MT Aerospace) noted that AM is crucial to address two main challenges in aerospace: the reduction of weight thanks to topology optimization and the merging of parts which enables to reduce the quantity of single parts within a structure. This last aspect leads to less time during repair or maintenance work. It therefore enables to maximise the system performance and reduce the expense on overhauling.
Moreover, the larger volume of units and the complexity of parts and materials for lightweight design remain essential for aviation itself and rocket construction. 8 speakers in this field discussed the potential of AM during the event. Issues such as establishing a certified production system for example were discussed by Stephan Keil Managing Director of Aviation AM Centre GmbH. On the other hand, Lars Langhans Head of Project Management of FIT AG noted the reduction of CO2 emissions through fuel savings, an innovation that we also covered with NASA’s 3D printable alloy.
Lastly, as we highlighted on several occasions, the use of industrialised AM services is pulling the sector for a more large-scale production focus.
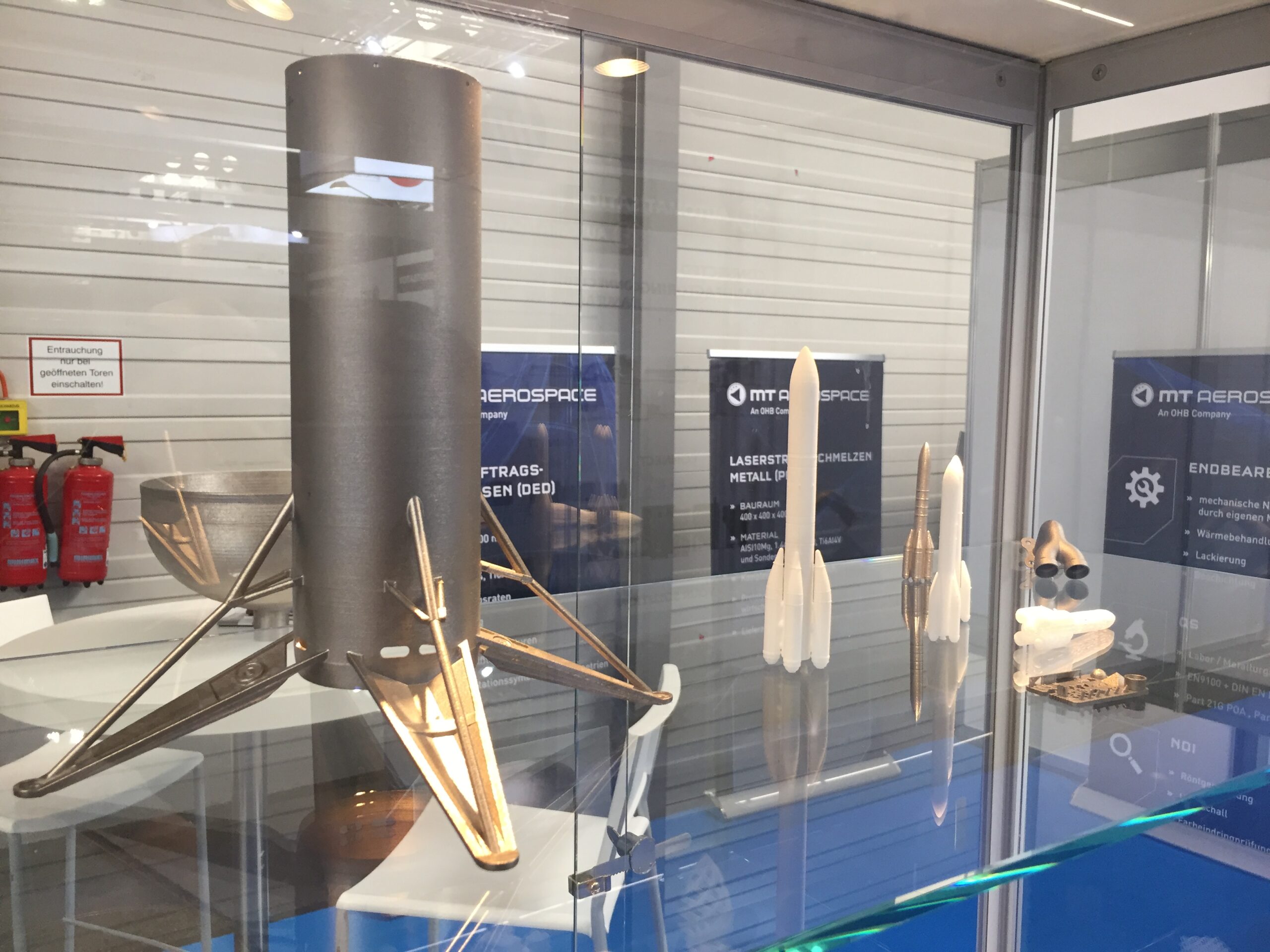
Convergence and applications
We at 3D ADEPT Media have always been keen on following the applications of additive technologies in numerous fields. This is also the case of Oechsler AG, which provides customers with dedicated 3D printing services: from automobile chairs, to 3D-printed midsoles with Adidas, lounge chairs, and even NFL helmets, they demonstrate that they can adapt to any production requirements.
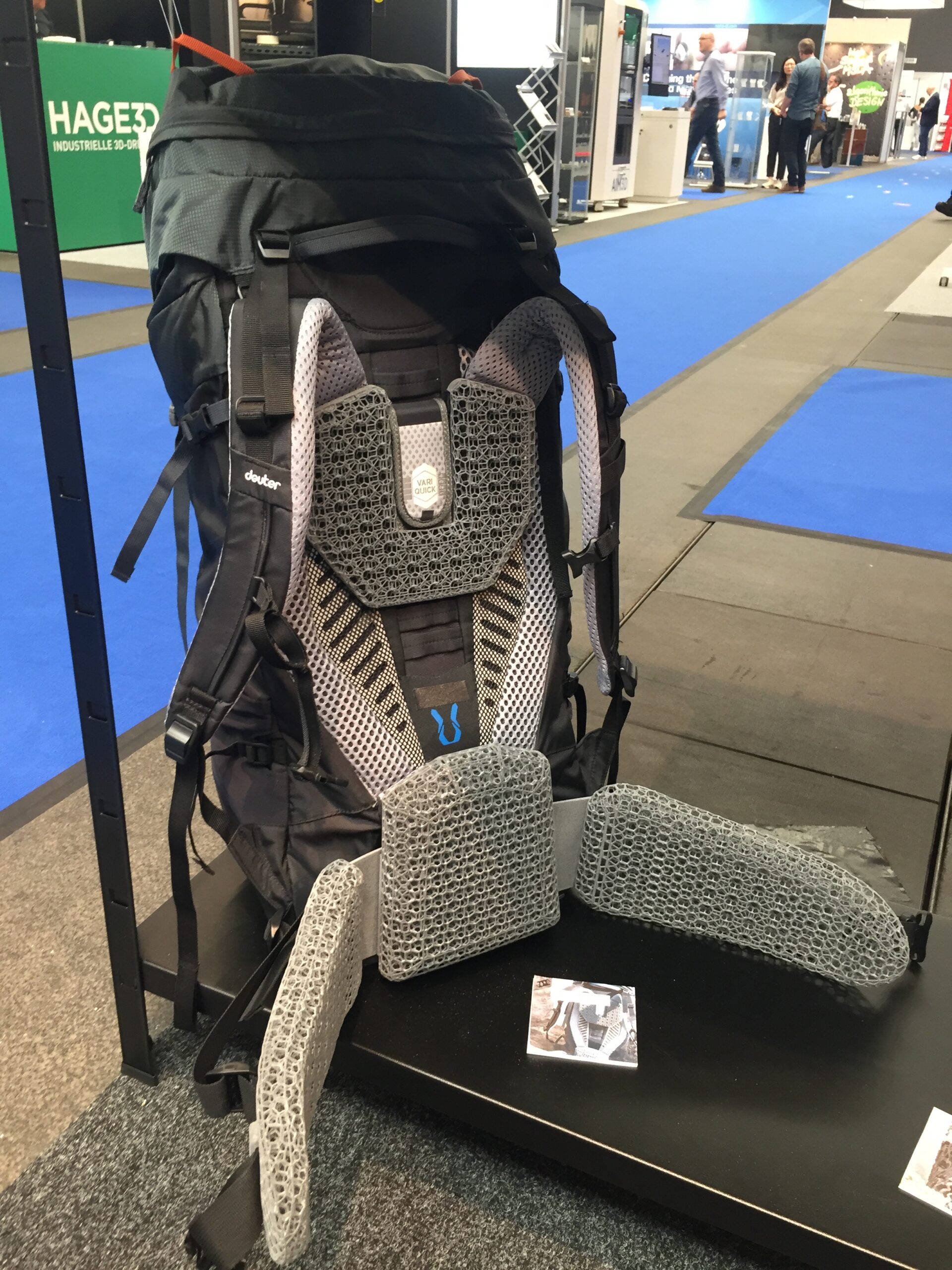
Another company that continues to add interesting contributions to the industry is the Swiss Start-up Spectroplast, which is transforming the AM world with its silicone 3D printing. The team presented the world’s first high-precision additive technology for silicones in Erfurt. Spectroplast caught our attention after securing a €1.38 million seed funding from AM Ventures. The versatility of silicone to adapt to all types of applications is truly something remarkable. For instance, the prostheses and anatomical models for medical purposes can be fitted into patient-specific needs. This can lead to new solutions on the healthcare market. It is not surprising that the company was awarded prizes during the Formnext’s Start-up challenge, and the 2019 CES innovation awards.
We have stated before at 3D ADEPT Media that the disruptive tendencies brought by new ideas and young initiatives are always refreshing for the industry; there is no doubt that Spectroplast’s Silicone Additive Manufacturing (SAM) follows this premise. According to the company, their process from CAD designs to post-processing of products, is 90% faster compared to Liquid injection moulding (LIM). This requires a certain level of material performance and brings a new range of benefits to the production of silicone products which becomes less expensive than traditional methods.
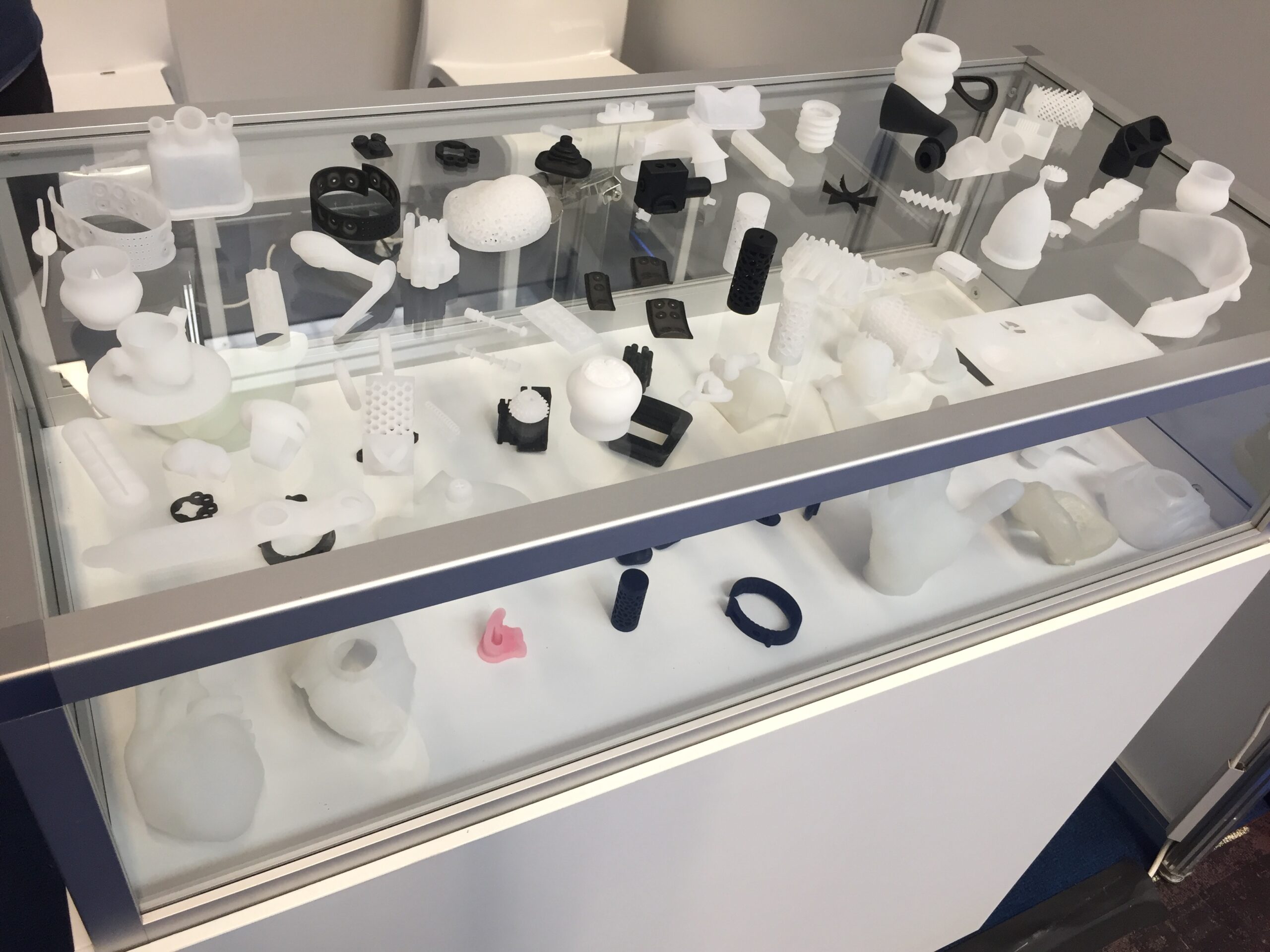
Lastly, as part of the 3D Pioneers Challenge, the main prize was awarded to “Bellow rail brake”, a project achieved by the team from ETH Zurich. They developed a brake for the high-speed transport system Hyperloop using 3D printing technologies.
These highlights of Rapid.Tech 3D are just the tip of the iceberg. As the industry moves forward, more advances will illustrate the progress of AM technologies and the convergence with a whole range of traditional industries.
Either way, 3D ADEPT Media will continue to follow and track the latest trends in the additive manufacturing industry as well as the news of these and other companies. Stay tuned for more.
Remember, you can post job opportunities in the AM Industry on 3D ADEPT Media free of charge or look for a job via our job board. Make sure to follow us on our social networks and subscribe to our weekly newsletter : Facebook, Twitter, LinkedIn & Instagram ! If you want to be featured in the next issue of our digital magazine or if you hear a story that needs to be heard, make sure to send it to contact@3dadept.com