Pour ceux qui ne sont pas familiers avec les composants industriels, sachez qu’un échangeur de chaleur, comme son nom l’indique, est un système utilisé pour transférer la chaleur entre deux ou plusieurs fluides de températures différentes. Cela signifie qu’ils peuvent être utilisés à la fois dans les processus de refroidissement et de chauffage.
Ces dispositifs constituent généralement un excellent exemple d’applications de la fabrication additive dans des secteurs exigeants comme l’aérospatiale. Toutefois, même si le résultat final est presque toujours surprenant, l’utilisation de la fabrication additive pour des composants complexes tels que les échangeurs de chaleur s’accompagne de son lot de défis, notamment en matière de fabricabilité et d’inspection.
En réalité, les échangeurs de chaleur à calandre sont généralement constitués de dizaines de composants soudés ensemble. La géométrie des tubes reliant les chambres d’entrée et de sortie est généralement limitée à des tubes droits, ce qui entraîne la présence de poudre piégée dans les canaux et de contraintes résiduelles susceptibles de déformer les pièces.
Une façon de résoudre ce problème a été de tirer parti des principes de « DfAM ». (Design for AM). L’équipe d’ingénieurs du Manufacturing Technology Centre, basé au Royaume-Uni, a exploré ces principes pour le composant tube d’un échangeur de chaleur tubulaire à passage unique. Ces principes ont été utilisés aux côtés d’une fusion laser à poudre métallique, d’un usinage par électroérosion à fil, d’un usinage CNC ainsi que d’un contrôle non destructif comme autres technologies de fabrication et de contrôle.
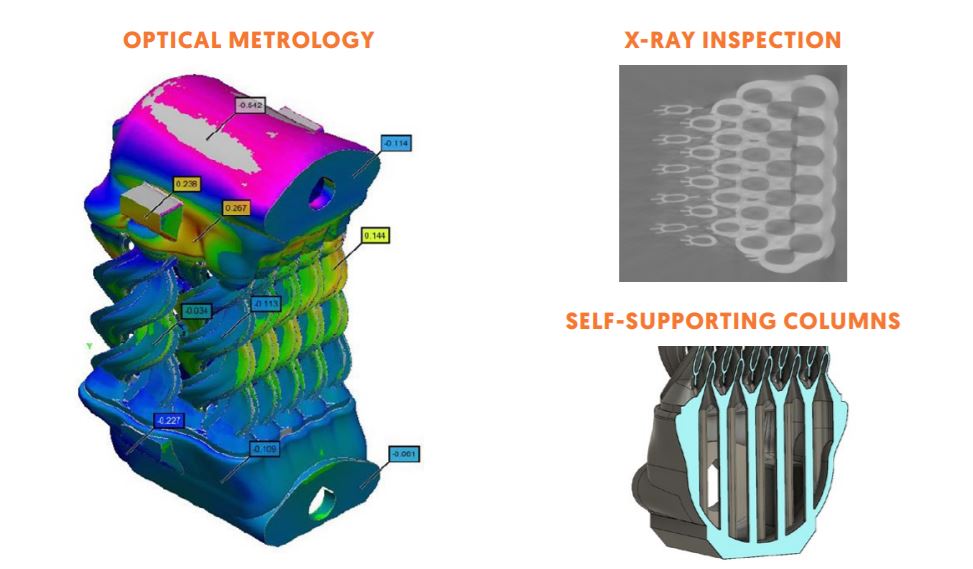
Le processus de fabrication révèle qu’en redessinant le noyau du nouveau tube de l’échangeur de chaleur avec 33 canaux hélicoïdaux, ils ont pu augmenter la longueur du transfert de chaleur et des ailettes pour accroître la surface. Au niveau de la conception, ils ont utilisé Autodesk Fusion 360 pour générer les structures et ils ont fabriqué la pièce avec du Ti6Al4V sans structures de support internes.
Au final, l’équipe a révélé qu’elle avait réussi à regrouper 40 pièces en une seule. Alors que les méthodes d’inspection avancées les aident à identifier rapidement la poudre piégée dans le composant, les étapes qu’ils ont entreprises au niveau de la fabrication ont permis de mieux comprendre la distorsion géométrique dans un tel composant.
Le plus intéressant, c’est la validation des processus de fabrication et de post-traitement de bout en bout et l’évaluation des données générées.
Vous pouvez maintenant poster vos offres d’emploi sur 3D ADEPT Media. Pour des informations exclusives sur l’impression 3D, abonnez-vous à notre newsletter et suivez-nous sur les réseaux sociaux : Facebook, Twitter, LinkedIn & Instagram ! Vous souhaitez-vous abonner à 3D ADEPT Mag ? Ou vous voulez figurer dans le prochain numéro de notre magazine numérique ? Envoyez-nous un email à contact@3dadept.com