In spring last year, Purdue University’s Composites Manufacturing Simulation Center (CMSC) and Thermwood Corporation announced the establishment of a large-scale additive manufacturing laboratory to execute industry-funded research into large scale composite thermoplastic additive manufacturing.
The CMSC essentially focuses its areas of research on composites manufacturing simulation & validation; composites additive manufacturing as well as mechanics of structure genome. The research center is backed by an online Composites Community (the cdmHUB – which stands for Composites Design and Manufacturing HUB -) that supports certification by analysis through developing and disseminating simulation best practices and through education and evaluation of composites simulation tools.
Thermwood on the other hand is a US based, multinational, diversified CNC machinery manufacturer that has become one of the key references when it comes to large scale additive manufacturing systems for thermoplastic composite molds, tooling, patterns.
Here we are a year later, the partners share the results of one of the projects that have kept them busy since the announcement. The project consisted in designing, prototyping, testing, and fabricating composite support structures for CERN’s Large Hadron Collider (LHC) CMS and ATLAS experiments. This project would be part of the particle collider’s High Luminosity upgrade, whose setting up of final parts is scheduled for 2026-27.
As announced last year, the partners utilized the Thermwood LSAM 105 Additive Printer and five-axis LSAM Trim router for the rapid large-scale printing and machining of trimming fixtures for the high precision composite tube structures.
The LSAM 105 Additive Printer is made up of a moving table single fixed gantry (10’x 5’ Moving = 25 x 12 cm) that can fabricate components with a maximum print height of 4’ (10 cm). Compatible with print heads of 40mm, the machine can reach a maximum temperature of 450°C with a print rate of ≈ 100 lbs/hr (45kg/hr).
The trim or subtractive gantry is a five axis CNC router system equipped with a 12HP (3,000 to 24,000 RPM) Automatic Tool Change Spindle and a ten position automatic tool changer.
The project team 3D printed the 1m long, 208mm radius trimming fixture on the LSAM using Acrylonitrile Butadiene Styrene (ABS) reinforced with 20% by weight of carbon fiber. With the successful completion of this 914mm long prototype of the CMS upgrade inner tracker support tube, the team is confident enough to conduct tests of their structural and detection components.
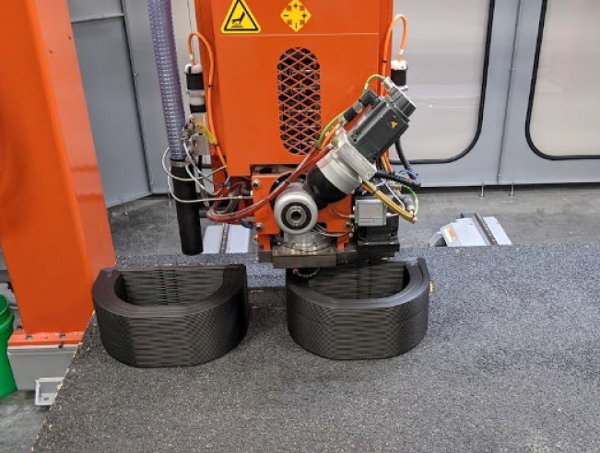
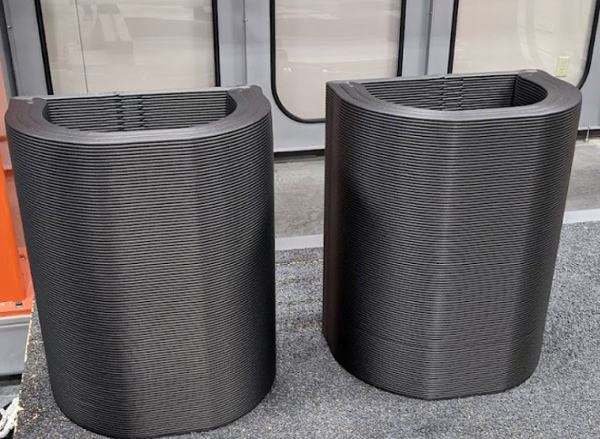
According to Thermwood, individual components installed into this support tube are expected to be positioned within +/- 0.5mm or less, so accurate machining of interface features is critical. This kind of precision at large scale is made possible, economical, and convenient with the aid of systems like LSAM.
Since critical surfaces would be machined later, and to increase production speed for the prismatic geometry, the tool was split into two vertically-printed segments. The halves were bonded with adhesive and dowel pins for joint strength and stability, the company explains on its website.
Interestingly, the project reveals the importance of combining AM and machining to deliver the most desired results.
Indeed, after machining the faces that would become the trimming fixture base, they used the printed and machined fixture to trim the composite part edges, drill interface holes and with mating surfaces machined flat, they fabricated a scarf joint to join the two half cylinders. The precision trimmed composite halves were then able to be bonded together.
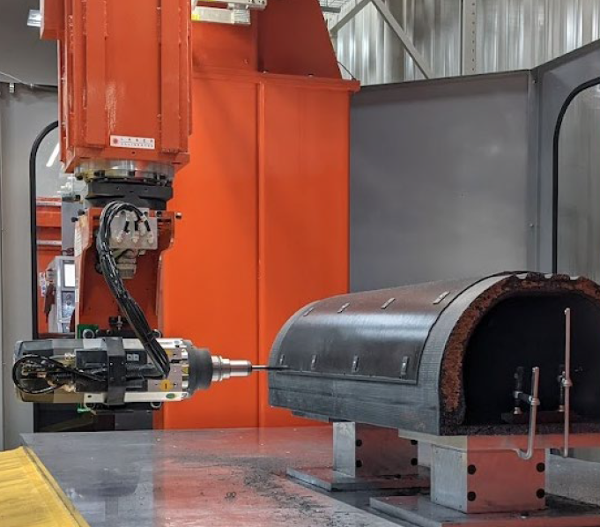
The final result reveals a tube, 3.2m long that can withstand 140kg of mass while only allowing sub millimeter deflections to occur.
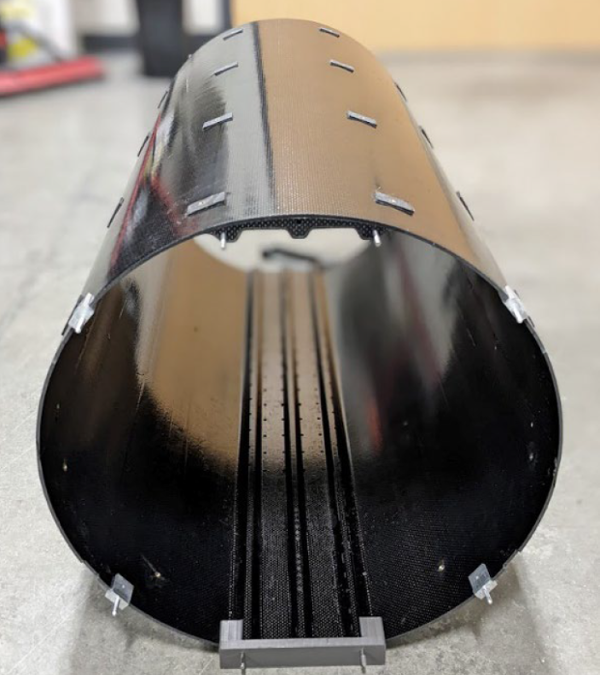
Moving forward, we can expect the team Purdue CMSC/PSDL to design, fabricate, and test other composite support structures for the CERN LHC upgrade, structures that would be as small as 0.5mm sheet goods and as large as 2.4m x 5m sandwich panel tubes. With Large Scale Additive Manufacturing apart of the projects, we will be able to assess further capabilities of this technology solution.
Remember, you can post job opportunities in the AM Industry on 3D ADEPT Media free of charge or look for a job via our job board. Make sure to follow us on our social networks and subscribe to our weekly newsletter : Facebook, Twitter, LinkedIn & Instagram ! If you want to be featured in the next issue of our digital magazine or if you hear a story that needs to be heard, make sure to send it to contact@3dadept.com