Additive Drives GmbH is one of the first “AM-driven applications” company – if not the only of the industry. In this article, co-founders Philipp Arnold and Jakob Jung provide insights into the use of Additive Manufacturing for electric motors.
Not many companies can pride themselves on raising money during the first three months of their existence, Additive Drives GmbH can and the best part is, the company did so during the first peak of the Covid-19 pandemic last year, when the economy was not at its best.
If securing an investment round is always big news for a company, no matter what size it is, a conversation with Arno Held, Chief Venture Officer (CVO) at AM Ventures – a serial investor in Additive Manufacturing- , shed light on the importance for both investors and early stage founders to understand the market dynamics of the industry in which they operate.
According to Held, three key enablers currently drive the AM market: timing, digital value chain and applications. Interestingly, in the short list of companies that secured money amid the pandemic last year, it turns out that Additive Drive GmbH debuts at the right moment and with a business model that is not widespread yet: a focus on AM-dedicated applications.
So, what does Additive Drives GmbH bring to the market?
Founded by Philipp Arnold, Jakob Jung and Axel Helm, Additive Drives GmbH develops and manufactures additively manufactured electric motor components. With a $1.5 million seed investment from AM Ventures Holding GmbH, Additive Drives GmbH ambitions to drive the electric drives market with new applications.
“Jakob and I, both come from the applications side of the industry. We have been developing electronic robots in the former automotive company we worked for. Engineers by training, we built up extensive experience with copper and additive manufacturing machines. After a deep research, we came to realize that the combination of AM and copper might lead to not only shorter development and test cycles for electric motors but also more performant applications. After a few successful trials, we reached out to Axel Helm who has a solid expertise in manufacturing processes and industrialization. His experience in copper processing and optimization of AM processes is pivotal to define the type of applications we could work on. We have therefore decided to combine our respective strengths to make Additive Drives GmbH a viable business”, Arnold told us from the outset.
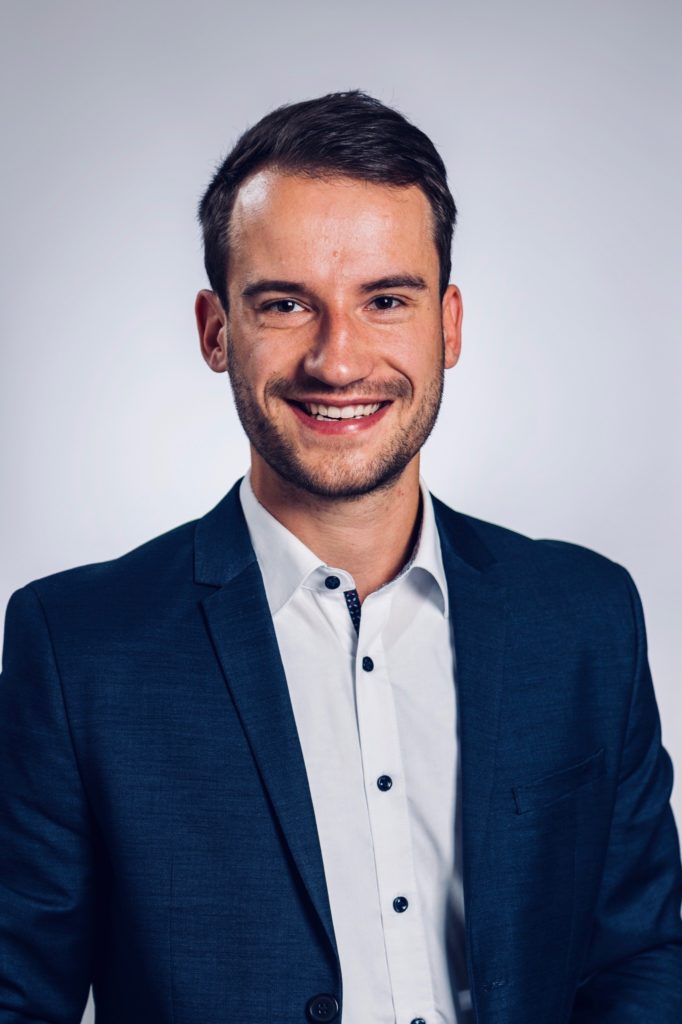
At the time of writing, Helm and Jung are general managers while Arnold is the financial and economic head of the team.
One key focus: driving the electric motors market
With rapid advances in design and manufacturing, the late 1800s saw the golden age of electric motors with new types of electric motors built on improved materials and manufacturing technologies of the time. Over time, with the advancement of manufacturing processes, the manufacturing technologies of the 1800s which are called today conventional manufacturing processes reveal a lack of reliability and repeatability of certain electric motor components, especially the motor coil windings.
Additive Manufacturing might be uniquely positioned to overcome this bottleneck, preventing electrical machines from playing a crucial role in key industrial sectors such as aerospace, automotive and other sectors of the mobility industry.
“At Additive Drives GmbH, we do not throw away the capabilities of conventional manufacturing processes. As a matter of fact, we are well aware of the fact that everything cannot be produced via AM. However, we want to enable industries to take advantage of opportunities within the design and manufacture of electric motors that can leverage the advantages that AM can provide over traditional manufacturing. The first of these advantages is ‘timing’. From about 36 months of development cycle to a few weeks with AM, this is already one notable reason to envision AM, the other ones being quality and performance”, Arnold explains.
While Additive Drives’ interest in AM is understandable, the choice for materials in every application is of paramount importance to achieve the desired manufacturing performance.
For those who are not familiar with all the components of an electric motor, it should be noted that the motor coil windings are a pivotal component that helps create an electric field in an electrical machine. These windings are usually made up of a series of coils, which on the other hand, are wires made of a conductive material surrounded by an insulative material.
That being said, one of the key electrical properties materials for such applications should have, is electrical conductivity, which is the main characteristic acknowledged in copper but also in alloys made from silver, gold, or aluminium, all of them being of interest to process by Selective Laser Melting technology.
Taking the example of additively manufactured copper windings of electric motors produced for a racing engine, Arnold outlines that copper processed by SLM brings an increased performance to the printed part. Using SLM for such a production brings high copper fill factors, better thermal behaviour as well as optimized power displacement to the engine, not to mention that the manufacturing process delivers optimized wire geometries that are not always seen with conventional manufacturing processes.
Jung talks about a copper filling factor of 65% with AM compared to 45% with conventional manufacturing processes. Furthermore, with AM, the forced heat transfer from winding to laminated core prevents hotspot formation often found in conventional manufacturing methods. On the other hand, variable conductor thicknesses reduce current displacement leading to maximum performance of the part.
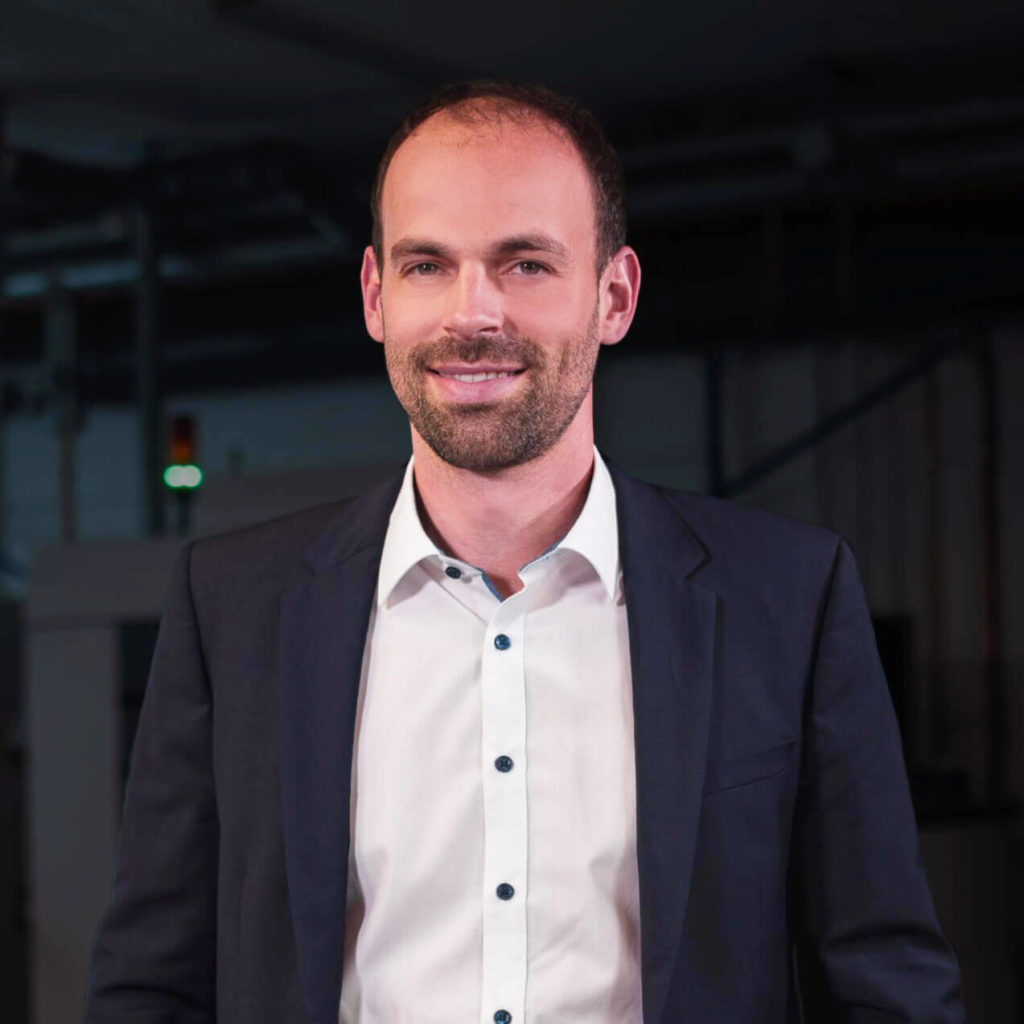
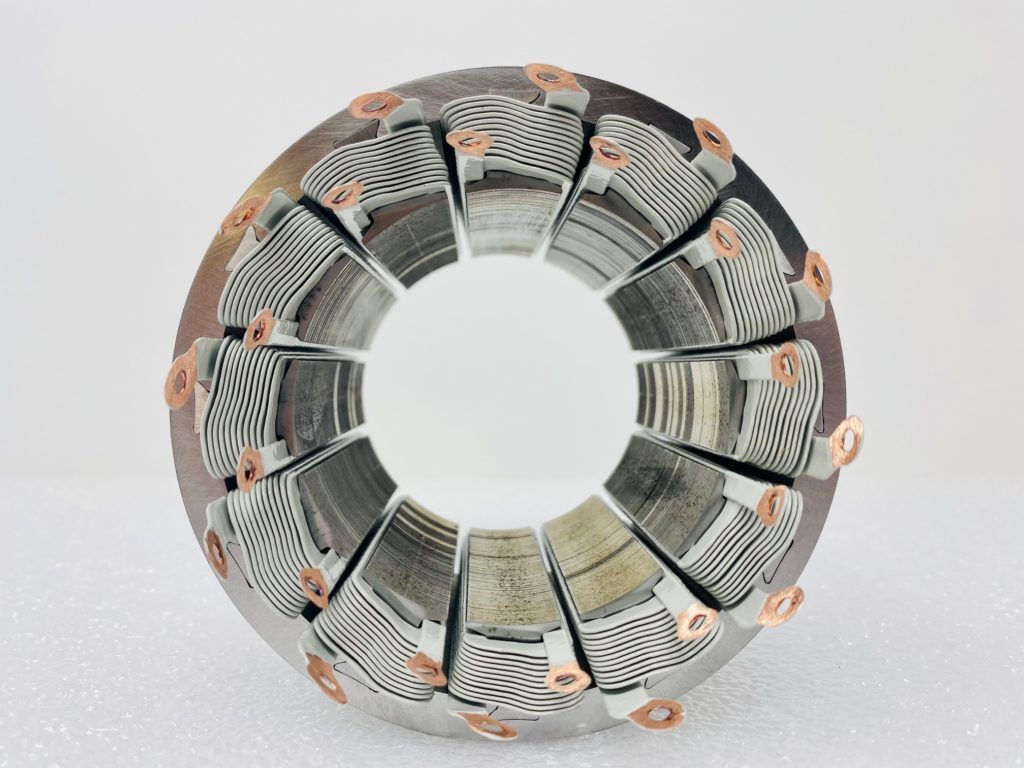
The comparison between AM & conventional manufacturing processes when it comes to the production of 3D printed copper windings is just one example in the list of direct production of tailor-made lots achieved by the Germany-based company. Other examples include for instance pedelec motors and e-traction motors.
While the AM of electric motor components, especially windings, enables varying designs to be approved quickly and easily without the need for tools, Arnold also points out that, due to their ability to provide fast prototype implementation, they can have real-time feedback from customers that is pivotal to ensure the required operating properties and to enhance quality assurance.
Moving forward…
To date, Additive Drives GmbH is a ISO9001:2015 certified company. This means their Quality Management System enables them to continuously improve performance and maintain a high level of quality in their manufacturing environment.
Speaking of the next steps for the company, Jung recalls they “are coming from the applications side of the industry, which means [they] are combining various “toolkits” that are required in this business model.” “We are now working to significantly improve electric drives, and electric models through new designs. To do so, this is a time where we should identify series production where AM makes sense and provides economic advantage”, Jung notes.
“We are willing to invest extra miles to support our customers in their ongoing developments and bring them to serial production. So far, our proof of concept demonstrates a number of applications for electric motors that can be achieved via AM, but we do not intent to stop here. We will continue focusing on electric motors, as we believe in the potential the technology can bring to this market. To do so, we will look for other applications where SLM could be used as a serial production technology”, Arnold concludes.
Featured image: single coil – courtesy of Additive Drives GmbH – Remember, you can post job opportunities in the AM Industry on 3D ADEPT Media free of charge or look for a job via our job board. Make sure to follow us on our social networks and subscribe to our weekly newsletter : Facebook, Twitter, LinkedIn & Instagram ! If you want to be featured in the next issue of our digital magazine or if you hear a story that needs to be heard, make sure you send it to contact@3dadept.com