Launching a company or breaking into a new market is one thing; achieving lasting growth is a whole other challenge. In the ever-evolving world of Additive Manufacturing, where innovation meets fierce competition, entrepreneurs are constantly seeking opportunities to drive the industry forward. At 3D ADEPT, we’ve made it our mission to spotlight the bold newcomers shaping this dynamic industry. With this in mind, we’re circling back to some of the 3D printing ventures that emerged from stealth mode last year. Have they survived the test of time?
Among the wide range of companies that debuted in the AM market last year, 12 companies drew our attention: Data center solution company EdgeCloudLink (ECL), Finnish stainless steel manufacturer Outokumpu, provider of filtration and separation of fluids services Evove, KeyProd production monitoring solution provider JPB Système, Swiss robotics company Saeki, 3D BioFibR, a company that specializes in biomaterials for tissue engineering, vertical integrated company flō optics, software company Additive Appearance, manufacturer of 3D printed maritime spare parts Pelagus 3D, Indian steel giant ArcelorMittal, 3D printer manufacturer Forivory, as well as Metafold, a newcomer in Design for Additive Manufacturing.
How have they navigated their AM journey so far?
EdgeCloudLink (ECL)
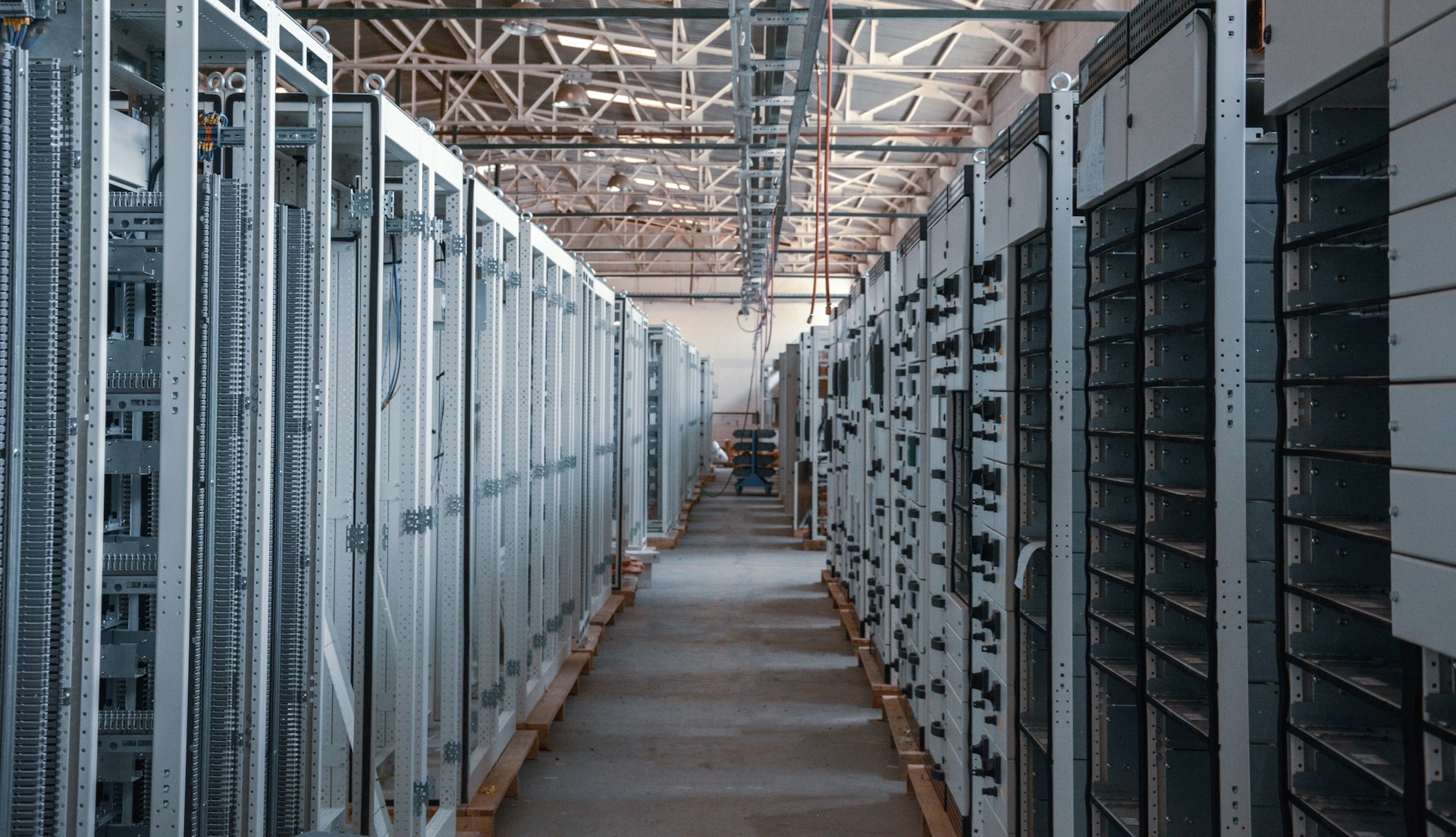
It can be difficult to guess how a data center solution company could leverage Additive Manufacturing but EdgeCloudLink (ECL) initially shared that it would use a construction 3D printer to build a zero-emission data center in Mountain View, California. These modular data centers would stand out from the crowd by the use of construction 3D printing and their ability to run on their own hydrogen-powered microgrids.
One year later, we can confirm that ECL has done its job. The company is finalizing the integration and commissioning of a 1MW data center, running on fuel cells at its headquarters in California. However, the CEO Yuval Bachar told our media colleagues from DCD that they finally did not leverage construction 3D printing as there was a vacant warehouse on its plot. According to Bachar, reusing a building is greener than 3D printing a new one “and when 3D printing is needed, it will be the “easy” part of delivering a data center.”
Outokumpu
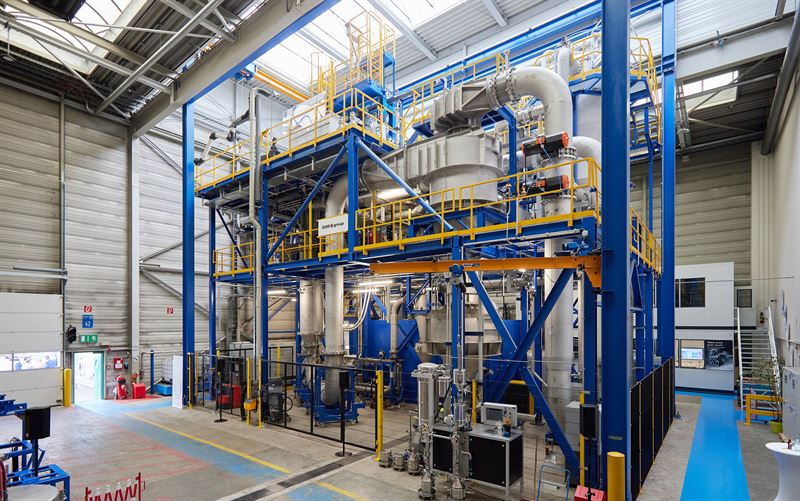
The stainless steel powders introduced by Outokumpu can be used in various manufacturing processes like Metal Injection Moulding (MIM), and Binder Jetting (BJ). Beyond powder manufacturing, the company sought to create a viable AM ecosystem to support its customers in producing customizable 3D printed parts. This goal has not been met yet as the company first focused on strengthening its circular economy efforts which consist of producing annually up to 330 tons of metal powder from its own recycled material – 100% stainless steel scrap. This year, the company has entered the commercial production phase of this pilot project.
He also began several research and development cooperation projects with companies from a wide range of industries that want to use steel powder for new products. Outokumpu has been entering a collaboration with steel trading company STAHL KREBS, as part of the public-funded project REACT** by the German government. Another collaboration in the pipeline is within the medical and jewelry industry to work on nickel-free materials, which can be used for implants, medical tools and watches. The collaboration is taking place via a publicly funded project by EIT Raw Materials, HiPAM***, led by VTT Technical Research Centre of Finland.
That being said, Outokumpu’s primary focus remains the production of metal powders that are not yet on the market – suited for companies that use technologies to produce parts for demanding specialty applications. To support customer-specific requirements, Outokumpu operates its proprietary test laboratory, where the applications can be modified and validated directly on-site.
Evove
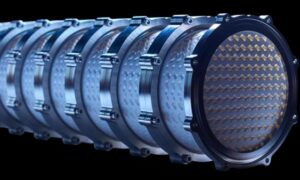
Evove is definitely making the list of vertical-integrated companies that I will watch next year. Its core business is simple: addressing the limitations linked to the production of membrane filters with AM. On the heels of their recent collaboration with Lithoz, a short conversation with Andrew Walker, Chief Commercial Officer, taught me that the company’s Separonics membrane facilitates the production of battery-grade lithium on-site without having to ship it elsewhere. Furthermore, the company’s 3D printed membrane can filter lithium directly out of the brine, eliminating the need for ponds.
The conversation with Walker at Formnext also made me believe that the company is doing well as it is working with Chile’s SQM, the world’s second-largest lithium producer, as well as Northern Lithium in the U.K.
JPB Système
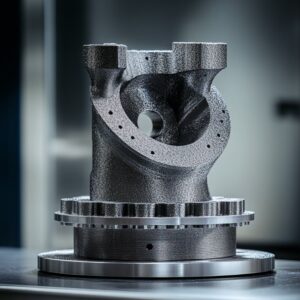
JPB Système took its first steps in the AM market, by acquiring a stake in France-based 3D printer manufacturer start-up, Addimetal. The company had promised it will be involved in the development of Addimetal’s open hardware platform, technology and associated process to ensure both existing and future application needs are met. The company lived up to that promise as this year, ADDIMETAL announced the launch of its flagship metal binder jetting 3D printer. Given ADDIMETAL’s bold ambitions in the industry, we believe we will continue to hear about JPB Système.
SAEKI
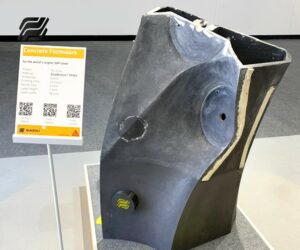
SAEKI claims its robots can make 3D printed formwork which can help in the manufacture of non-standard and custom construction elements risk-free. They say they provide a platform for low-volume production of non-standard concrete elements. They have remained quiet about their activities this year but their recent presence at Formnext 2024, at the booth of their partner Sika, indicates they are still in operations.
Visitors at the show could discover a tool used for the creation of a 3D printed tower. This tool – a concrete formwork – was produced using SAEKI’s printing and machining solution.
3D BioFibR
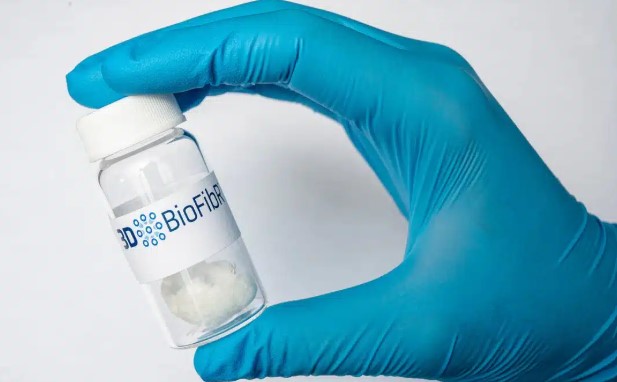
As a reminder, 3D BioFibR focuses on collagen products that can serve 3D cell culture and tissue engineering applications, especially the cellular scaffolds segment. The company continues to be involved in several R&D projects in tissue engineering and has recently made its μCollaFibR™ – Additive for bioinks and hydrogels – available through distributors worldwide.
flō optics
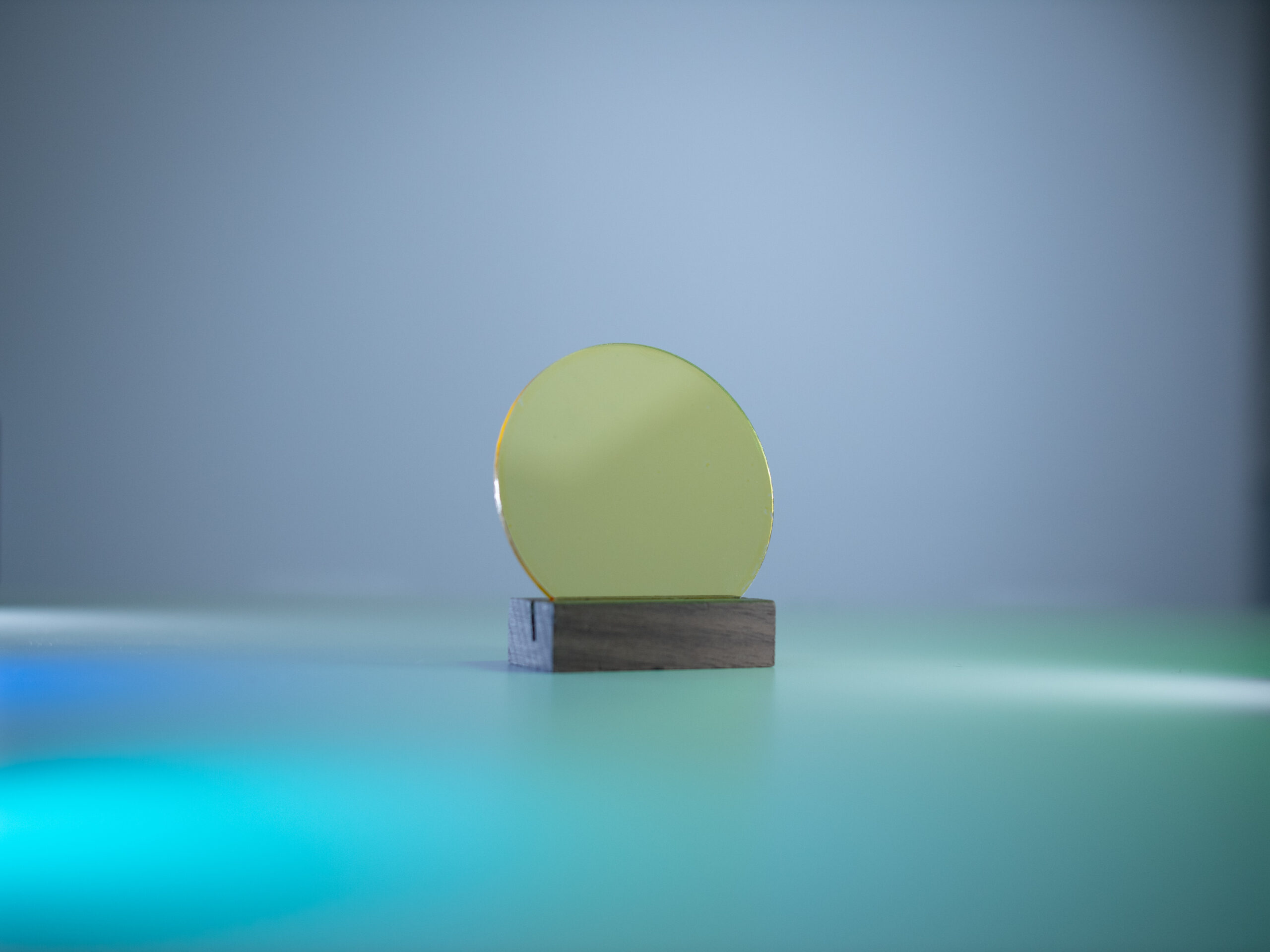
flō optics has made a real splash last year in 2023 when it launched on the market. The company develops an inkjet-based 3D printing technology that applies unique, multi-material, multi-layer coatings to lenses. Ever since it signed an exclusive agreement with Yeda Research and Development Co., the company has remained quiet on its activities.
We have reached out to the company’s CEO to have a quick update on their activities and we will update this article once we receive new information.
Additive Appearance
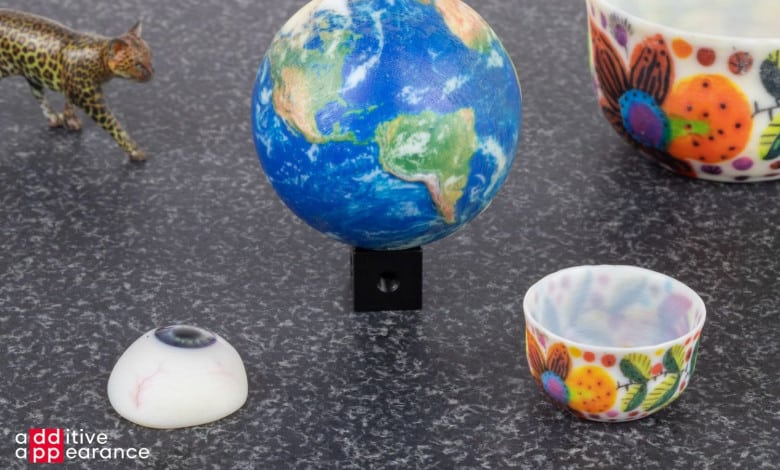
This one-year-old software company aims to enhance full-color 3D printing. The company develops a slicer solution that makes every layer count. It has been pitching at various events this year to attract potential investors who would help it grow its business.
Pelagus 3D
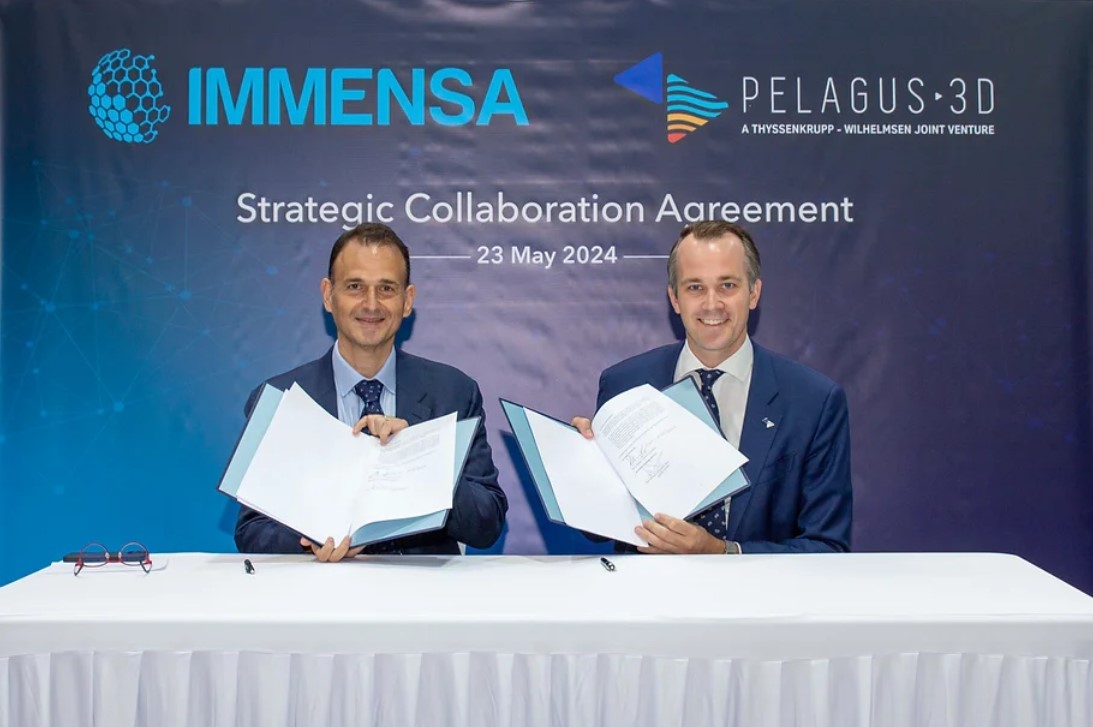
Pelagus 3D, a provider of maritime 3D printed parts and a joint venture of thyssenkrupp and Wilhelmsen, seems to be doing well: the company is hiring, and is signing partnerships to develop spare parts for MENA maritime and energy sectors. The latest one has been signed with digital manufacturing firm Immensa. On top of that, the company also recently achieved International Standard requirements ISO 9001:2015, ISO 14001:2015, and ISO 45001: 2018 certifications across its global operations. These certifications demonstrate commitment to quality, environmental, health and safety management as they imply the implementation of a comprehensive Integrated Management System (IMS).
ArcelorMittal Powders
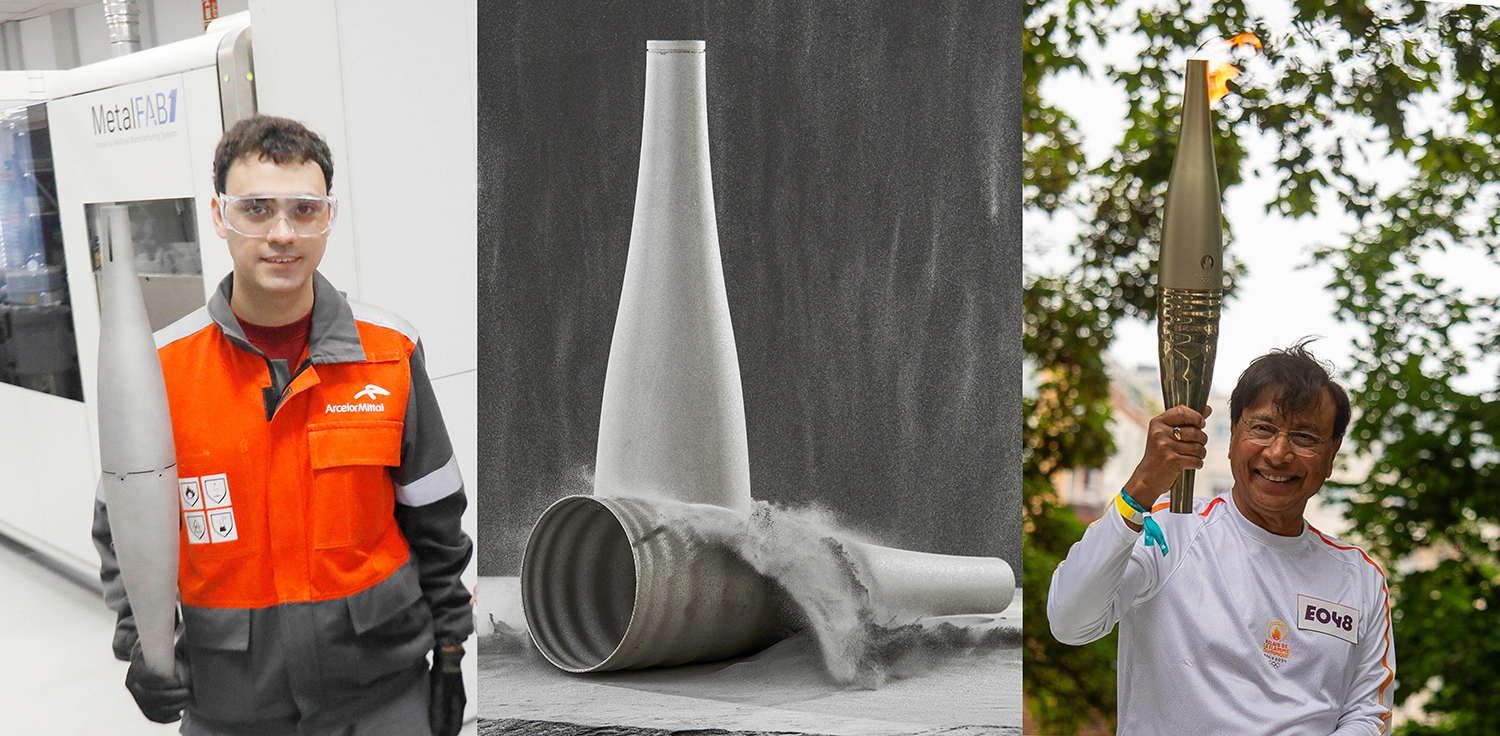
Not only were they present at key tradeshows of the industry, but they further gained momentum after the Paris 2024 Olympic Torch’s prototypes were made by laser powder bed fusion, in ArcelorMittal Global R&D’s Additive Manufacturing labs and using ArcelorMittal Powders’ AdamIQ™ 316L powder.
I would define ArcelorMittal’s year as a year marked by collaborations with the likes of Materialise and HP and by the development of key products and services such as the AdamIQ™ algorithm. This algorithm helps to address the complexities of the laser powder bed fusion (LPBF) technology, to maximize laser up-time, while minimizing printing time. As the company explains, AdamIQ™ algorithmic optimization happens as a final step of build preparation. All build job parameters and configurations should be prepared and frozen by the customer (printer) in their version of the build job. The AdamIQ™ optimization is an add-on that improves the customer’s build job in a single pass. A few minutes of re-vectorization can save hours of printing time.
Forivory
“Forivory”, a brand of Jelect, unveiled the industrial 3D printer FT400 with a key focus on the Korean market to start the distribution. The company was supposed to prepare for oversea delivery after participating in SIMTOS in April 2024 but no information has been shared regarding this status.
The website of Jelect does no longer feature the FT400 as part of its offering. It seems that the company has discontinued this line of products.
Metafold
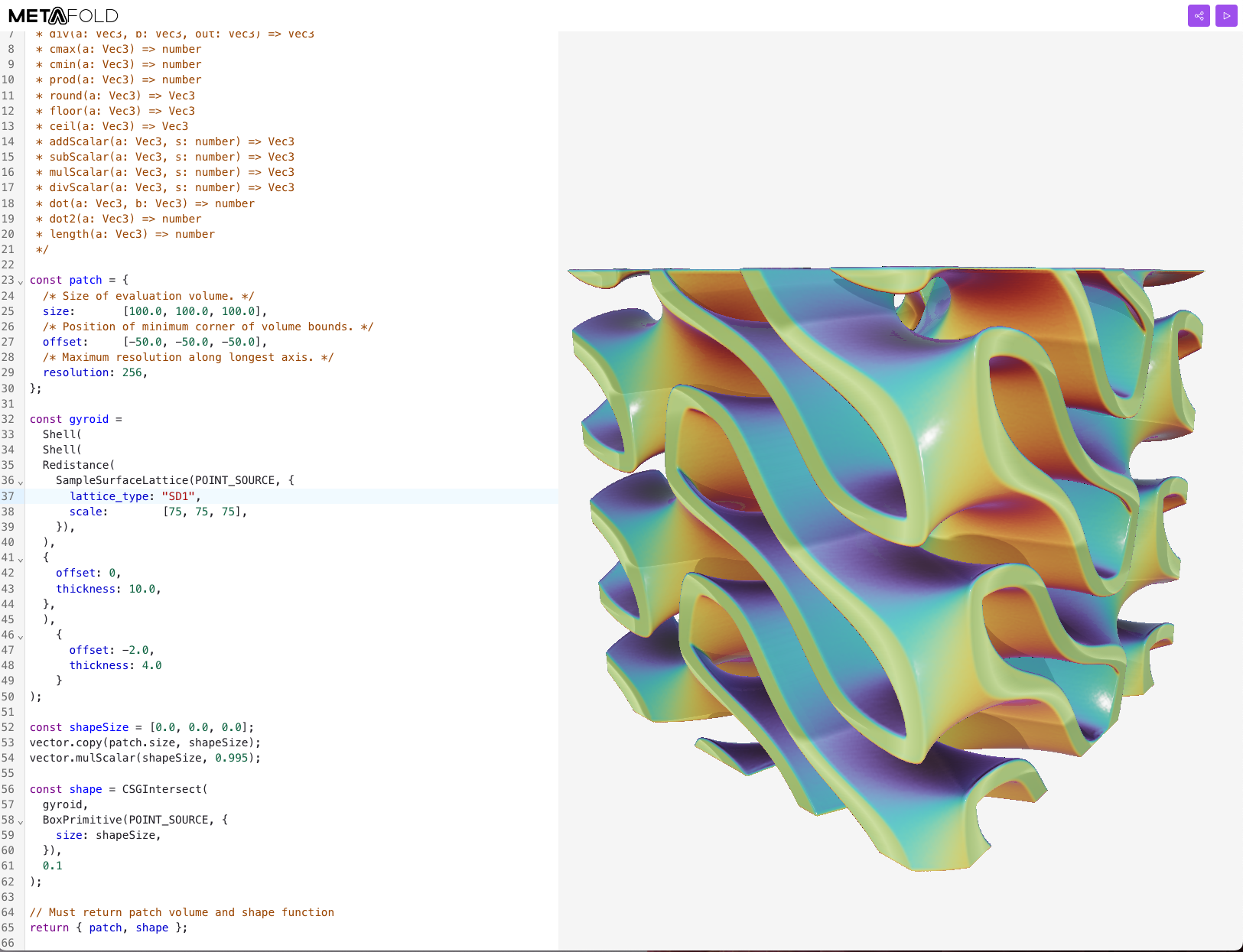
Metafold continues to offer a commercially licensable API and high-quality developer experience for web-based geometry creation, editing, simulation, rendering and print preparation.
The company continues to demonstrate the capabilities of its software development toolkit through case studies and collaborations with companies.
This dossier has first been published in the 2024 November/December edition of 3D ADEPT Mag.