Even though there is an economic downturn affecting the industry, this does not prevent bold entrepreneurs and long-standing companies from trying their luck in the AM market. This year again, several companies made their debut in the industry. We have gathered below ten companies that caught our attention.
1. Xenia
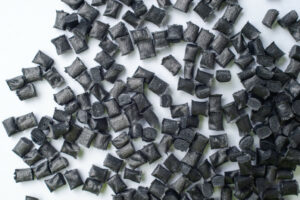
Technically, Xenia debuted in the AM market in 2023, at Formnext but they appeared on our radar at the beginning of this year hence their presence in this list. Headquartered in Italy and founded in 1995, the company builds on its expertise in high-performing thermoplastic composites reinforced fiber and additives to commercialize new materials in the AM market. Its collection of high-performance composites is called 3DP MATERIALS and includes unique resins combined with fiber and additives, adapted for use in any pellet-based type of FDM printers, for LSAM production as well as high-precision production.
The company’s 3DF Materials division launched four new 3D printing filaments at Formnext 2024, designed to meet diverse requirements in industries needing lightweight, structural, and sustainable, materials. Those materials include XECARB® SL 3DF – 15% carbon fiber reinforced PA11, XELIGHT® 3DF – Ultralight PEBA, XECARB® 45 3DF – 10% carbon fiber reinforced PVDF as well as XEGREEN® 23 3DF – 20% carbon fiber reinforced PETG.
I met the team at Formnext 2024 and discovered some of their materials. The team seems experienced and their products seem to be of good quality. I just hope they will have a better journey than their fellow companies in the market that discontinued their activities this year.
2. Fluent Metal
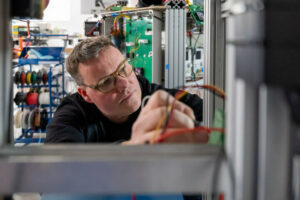
Everything is catchy with this company: their name, their technology, and the fact that they are backed by industry veterans from Desktop Metal, Vulcan Forms, and the MIT Media Lab.
Based in Cambridge, Massachusetts, Fluent Metal launched out of stealth, with an additional $3.2 million in venture capital funding, led by E15 with participation from Pillar VC and industry angels, bringing its total funding to $5.5 million. Its technology is a production-grade liquid metal printing solution that is based on a “drop-on-demand approach”.
Using an inkjet printer-like approach, Fluent Metal describes its process as an alternative lean overhead process that is functional, and operational efficient – not to mention that it produces no waste and uses less energy than powder-based technologies.
Xerox is one of the first companies that I saw developing liquid metal printing. It’s a technology that I personally find super cool to see in action, but my feelings don’t count in a market that does not always recognize its potential. In the market, apart from Xerox whose technology is now commercialized by AddiTEC, there are also ValCUN and Mantle that develop such solutions.
The good news in Fluent Metal’s case is that the people behind the company will give some credibility to this technology and I hope its capabilities could make the technology gain the spotlight it truly deserves.
3. Ecogensus
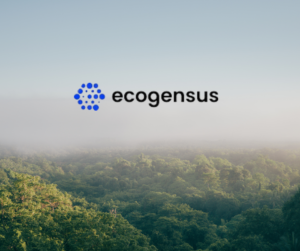
By tapping into billions of unused resources, Ecogensus directly positions itself as a company that advocates for sustainability. The company develops materials from mixed wastes. These wastes are household trashes—such as food waste, diapers, plastics, paper, cardboard, and yard waste— that are transformed into engineered powders.
I like to see these high-performance polymer composite powders as an “all in one” series. They provide a sustainable alternative to conventional plastics by integrating seamlessly with 3D printing, injection molding, and similar technologies.
Using a patented method, the company converts these powders into polymeric composite resins. These resins are designed for easy integration into current manufacturing processes. The patent also describes polymer cross-linking to enhance the structural integrity and versatility of materials derived from processed solid waste.
4. Verne Additive Manufacturing Labs
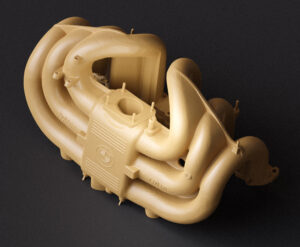
This French company raised our curiosity with an SLS PEKK 3D printing process. So far, the use of this high-performance thermoplastic material has widely been associated with FDM 3D printing, for obvious reasons: in addition to its maturity, FDM 3D printing can reach very high temperatures during the extrusion/material deposition phase, which is crucial to process high-performance materials.
Named Verne STROM, the 3D printer is accompanied by a sieving, mixing, and a powder transfer system called SM-1. Key features of the machine include a build chamber that can go up to 380°C, 40W CO2 Laser, Theta-lens focusing (with fiber laser configuration available as an option), a build size of 220 x 250 x 400 mm (8.7 x 9.8 x 15.7 in), a build rate that goes up to 2 L/h – 35 mm/h – 1.4 in/h or even AI-enhanced scanning strategies and laser power management.
The machine is yet to be commercialized but one can follow its development roadmap here.
5. Zylo 3D
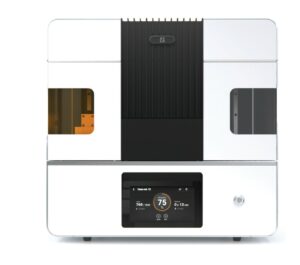
Zylo 3D is a company that would have been founded last year to provide automated 3D printing solutions to the dental industry. The company has not made any formal announcements yet but has recently welcomed on its team Shane Fox – one of the founders of Link3D, a company acquired by Materialise.
I have always been a huge fan of Fox’ work and what he did at Link3D, so I was curious to see where he will land next after selling his company. And the answer is Zylo3D – a company that bears the same name as its flagship product – a 3D printer that he describes as a “game-changer” in the dental industry.
Why? The “all-in-one” 3D printer would integrate build, wash, and cure functions in a fully automated system that requires no human intervention.
The company’s promise is quite strong: “You can print, wash, dry, and cure all in a single synced machine that requires minimal space and no prior printing experience while eliminating complexities associated with resin handling,” the company’s website explains. Fox is bringing some credibility to a product that is quite fascinating. I can’t wait to discover more about it through user feedback.
6. Fugo Precision 3D
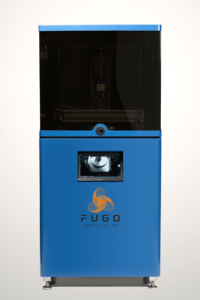
Fugo Precision 3D is a California-based manufacturer that promises AM users they can achieve precision with sub-30-micron accuracy. The new 3D printer named Fugo Model A would integrate multiple post-production processes into a single machine, significantly reducing costs and increasing efficiency for manufacturers. With this all-in-one system, users can print, wash, dry and post-cure parts, streamlining the entire production process.
The 3D printer can process a wide range of photopolymers and as per the company’s words, the 3D printer would be ten times faster than traditional stereolithography (SLA) printers. The company plans to deliver the initial commercial production machines in Q1 of 2025.
7. Sprybuild
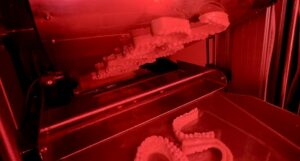
Sprybuild brings an SLA 3D printer to the market. The machine would integrate a patented continuous build process on a conveyor belt – instead of a build platform and a rigid optical interface.
This metallic belt moves at a sharp angle to DLP projection and has a remarkably high degree of surface stabilization, achieved through the utilization of an efficient yet simple patented magnetic system. Additionally, it offers an automatic printed parts release feature that virtually eliminates printer downtime, Sprybuild explains.
Sprybuild’s solid optical interface enables a continuous build process similar to, yet distinct from, the CLIP technology developed by Carbon3D. The challenge here was twofold: to eliminate the need for inhibiting resin near the interface and, at the same time, to create “dead zones” where the resin could remain liquid.
These zones are crucial for ensuring a steady flow of resin into the printing area, a key factor in achieving high-speed printing. Sprybuild’s ingenuity led to the development of an interface that meets these requirements, ensuring sufficient resin flow and curing only where necessary.
In addition to speed that is enhanced, the 3D printer would enable cost reduction through automation and the use of widely available UV resins. Not to mention that automated slicing, nesting, and the post-processing unit would make it easy to address complexity of the printing process.
The SLA 3D printer would be ideal for dental models, shoe soles, and orthopedic insoles, eyeglass frames and fashion accessories, hearing aids, prosthetic components, printed molds, and combustible models for precision casting.
8. SUGINO
As you may have seen in our Formnext coverage, SUGINO, a Japanese newcomer in the AM market, debuts its CASF solution. This processing solution stands for Cavitation Abrasive Surface Finishing, and helps to remove abnormal layers from the surface of objects, perform surface smoothing and imparting compressive stress due to the cavitation effect by injecting high-pressure water in a tank filled with abrasive suspension.
Akiteru Tsuiji, Managing Director of the German subsidiary told 3D ADEPT Media that abnormal layers such as poor melting and cavities that occur from the surface layer to a depth of 200 um can be removed together with surface smoothing treatment and compressive stress. This results in increased fatigue strength and better fatigue life of the final part.
9. VRC Metal Systems (aka VRC)
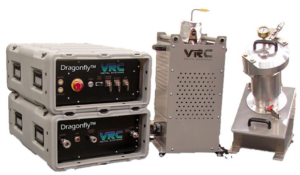
There are less than five companies developing Cold Additive Manufacturing technology in the market and VRC Metal Systems is now part of them. VRC is not that “new” in the AM market: it was founded in 2013 after obtaining an exclusive license to commercialize the patent-pending cold spray technology. It licensed the patent after a joint ownership agreement between the South Dakota School of Mines & Technology and the Army Research Laboratory was completed. It thereafter expanded its scope of expertise to AM in 2021, with VRC Cold Spray being the first solution it introduced in the metal AM market.
Named Dragonfly Cold Spray System, the machine can be used across industries such as maritime repairs, aeronautical maintenance, repair and overhaul, and the energy sector. The Dragonfly™ modules include the electrical assembly, the gas train, the powder feeder, and the heating unit.
The entire system is controlled by a VRC Pendant Controller, allowing users to initiate a cold spray process with just a few button clicks. Internal data logging, available via both USB and non-USB transfer options, enables users to record their cold spray processes anywhere and back up data for future analysis. The pendant can store up to 100 Cold Spray Recipes, providing flexibility for common use cases.
10.nPower Technologies
nPower Technologies is on a mission to address the scheduling challenges on the AM shopfloor through its nPower Scheduler™ solution. The company is the brainchild of ProfitKey, a provider of software and services that helps SMEs in their manufacturing operations.
nPower Scheduler™ provides a rich, graphical interface and seamless integration with existing ERP systems, enabling users to visualize and manage jobs on the shop floor.
This article has first been published in the November/December edition of 3D ADEPT Mag. Featured image: unsplash – Austin Distel