
“When it comes to XJET, we can’t talk about ceramic 3D printing without mentioning metal 3D Printing”
In an industry where metal AM drives the market, it is easy to not see the potential of other technologies such as ceramic 3D printing. In order to find out more about this latter technology, we reached out to XJET, an Israel-based manufacturer of 3D printing systems. Our talk with Hanan Gothait, CEO and Founder of the company, made us realize that, when it comes to XJET, we can’t talk about ceramic 3D printing without mentioning metal 3D Printing. The reason is simple: The manufacturer produces a multi-purpose 3D Printer that is based on liquid inkjet technology.
The strategy of manufacturing is wise since the company is drastically jetting off into the future by providing the market with 2 technologies: metal whose growth is exponential and ceramic whose potential seems certain but not yet known.
Without further ado, let’s discover what Hanan Gothait has to say about this topic. #OpinionoftheWeek
A few words about Hanan Gothait and XJET
Acknowledged for his expertise in the field of inkjet printing, Hanan has the ability to create companies that supply disruptive technologies to the market. Prior to XJET, the mechanical engineer co-founded Objet, that specializes in polymer jetting technologies and photopolymer 3D Printing systems as well as Idanit, that develops wide format printers for the production of outdoor signages.
With XJET, the entire team focuses on NanoParticle Jetting. “We believe that we are redefining metal and ceramic additive manufacturing”, said Hanan. Although the statement might be extreme, Hanan explains that unlike other systems, theirs has no powders. Their technology is based on jetting nano-particles of materials, which is made possible through their suspension in a liquid, that forms layer by layer accurate metal 3D printed parts or ceramic 3D Printed parts at a fast pace.
Simply put, in addition to its ability to print high resolution parts, the company has simplified the manufacturing process by separating the fusion process from the printing process. Furthermore, manufacturers do not have to deal with recycling issues thanks to the closed cartridge materials. Since there is no need for inert gas infeed, the process is clean and much healthier.
The last characteristic that enables the 3D printer to distinguish itself among others of the same range is at the post-processing stage where the material removal process has been made much easier.
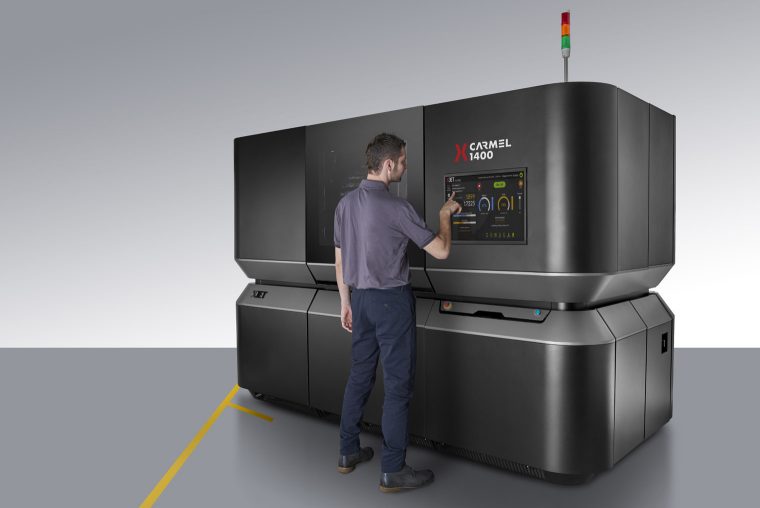
Why this focus on Ceramic 3D printing when professionals do not seem to believe it is profitable for the industry? As a matter of fact, some big players of the industry have even closed this part of their services.
There is no doubt that metal is the largest market and is evolving at a fast pace. However, we saw a lot of advantages in ceramic 3D printing which can be used in the medical, dental, automotive, electronics industries as well as in so many other applications. Experience has demonstrated that, although equipment to 3D print parts in ceramic is very limited, these industries are also the ones that take advantage of metal additive manufacturing. We have therefore decided to develop the same printer for both metal and ceramic.
As far as the ceramic 3D Printing market is concerned, one notes that at the beginning, it was a very small market that increasingly evolves, especially, because at the technical level, we haven’t yet seen a technology that can deliver accurate parts, with no powder and no recycling. The need has always been there but there was not yet a solution.
Why is ceramic 3D Printing used?
Ceramic is used whenever we need isolation, high temperature and high strength to parts. That’s the reason why this technology is widely used in the industry. Furthermore, thanks to its scalability, several industries already take advantage of this technology.
What are the main challenges those industries might encounter?
One of the main challenges is the variety of materials. The variety of materials still raises a lot of questions, and the current researches will provide more answers to these questions and will enable users to know what best meets their needs.
Another challenge is “adoption”. It takes time to be confident with the technology and its results and the process can be relatively long. However, once the users are convinced, they are willing to move forward.
The last challenge is qualification. We are aware of the requirements of the industries and the opening or our AM center in Israel shows that we step up our efforts to meet these requirements. On the other hand, it also demonstrates that we are willing to invest extra miles to convince our customers.
How do you perceive this market share in the upcoming years?
Many doors opened the discussion on opportunities aroused by ceramic 3D Printing and while looking at the variety of equipment available today, I must say that it evolves at its own way but I won’t say that it evolves as quickly as the metal AM market.
As far as XJET is concerned, a big part of our market will remain ceramic, because it is attractive but I can’t say it will constitute the majority of our revenues.
Your last word?
Michael Jordan once said: “some people want it to happen, some wish it would happen, others make it happen.” We believe we make it happen because the industry can experience a different level of the technology.
For further information about 3D Printing, follow us on our social networks and subscribe to our newsletter
Would you like to subscribe to 3D Adept Mag? Would you like to be featured in the next issue of our digital magazine? Send us an email at contact@3dadept.com
//pagead2.googlesyndication.com/pagead/js/adsbygoogle.js (adsbygoogle = window.adsbygoogle || []).push({});