A collaboration between Solukon and Lortek demonstrates the capabilities of Solukon’s Smart Powder Recuperation SPR® technology.
Lortek is the member of BRTA Research Alliance. It is a private technological centre that explores the use of various AM technologies including SLM, LMD and WAAM technologies in all industrial sectors. The centre also manages several European projects and one that recently raised many challenges is FLOWCAASH.
The main goal of this project is to design and manufacture reliable and safe flow control actuators at aircraft scale by Selective Laser Melting (SLM). Those actuators should be able to withstand high temperatures (up to 260 °C) and pressures (5 bar) during flight tests with aerodynamic performance and high resistance to extreme environments.
Two different actuators were considered as part of the project: Pulsed Jet Actuator (PJA) and Steady Blowing Actuator (SBA). However, the challenges to address required a focus on the PJA.
Due to its geometrical complexity and its shape, it was quite binding to install the PJA in between the wing and the nacelle of UHBR (Ultra High By pass Ratio) aircraft engines.The large part is made up of several channels with abrupt and narrow curvatures.
To manufacture the part, operators decided to rely on SLM technology. Distortion prediction simulations performed during the pre-printing stage helped operators find the best orientation but also avoid supports inside the channels; supports that could have been a holy grail to remove after the printing process since it would have not been possible to access the channels.
Distortion prediction
Furthermore, to prevent the blocking of the channels by the sintered powder during the heat treatment, it was crucial to remove the remaining powder. “This is particularly very challenging in case [the powder removal is conducted manually for] the PJA. Solukon de-powdering process has demonstrated to be an effective and fast way to get rid of the residual powder”, explains Ane Miren Mancisidor, Metal Additive Manufacturing Researcher at Lortek.
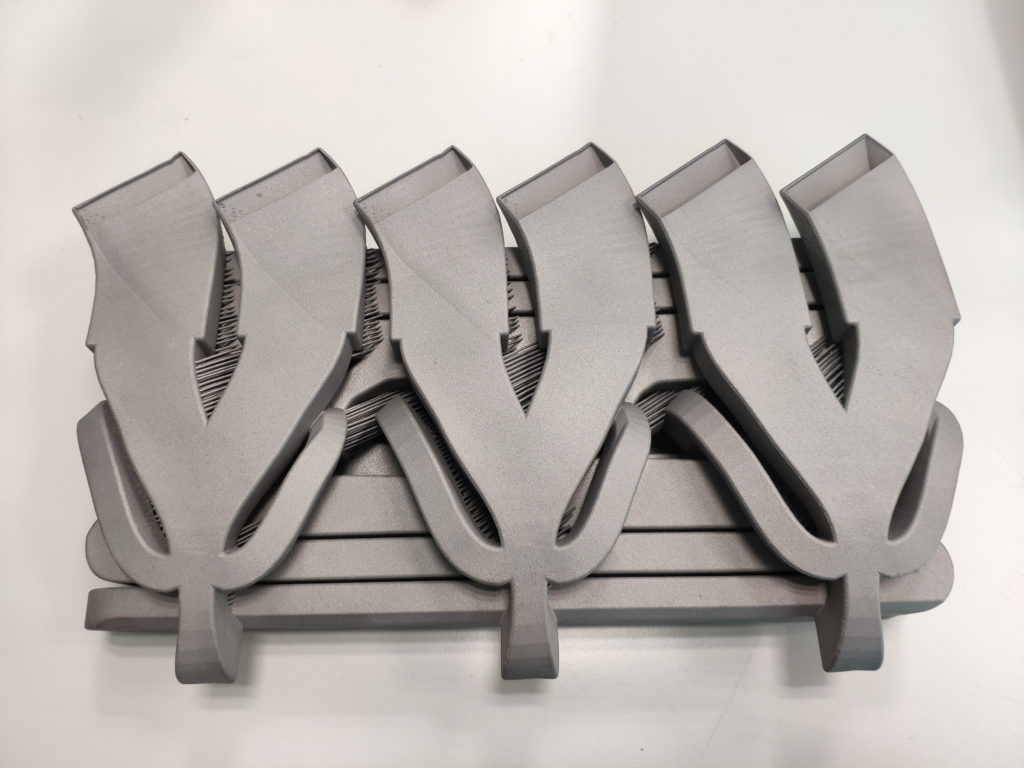
Solukon has a proven record in helping companies address the stage that follows the AM process, using peripheral equipment. The company’s patented technology, Smart Powder Recuperation SPR® enables programmable pivoting of the parts around two spatial axes.
With adjustable frequency, the depowdering machine allows for desired powder flow’s optimization and cleaning of all kinds of openings and channels which are vital for thermal downstream processes. Most importantly, the entire process does not present any risks for the operator as it can operate under inert conditions.
The advanced depowdering unit SFM-AT800-S has been leveraged as part of this process. Launched two years ago in collaboration with Siemens, the automated machine integrates intelligent software that can move the part along any 3D contour and in a safe way.
“Our aim is to give the industry a smart and highly automated and sustainable tool to close the gap between manufacturing and post processing. The process is fully automated and takes place in a protected and safety-controlled atmosphere, thus avoiding contact with harmful fine powders. Our Smart Powder Recuperation SPR® technology helps to save labor time, ensures that the most stringent demands of health and safety are met, and increases the quality process significantly. At the same time, it reclaims the residual powder without contamination and makes it available for further processing and re-use”, Andreas Hartmann Co-founder and technical director comments.
By combining SLM technology and Solukon’s depowdering unit at the post-printing stage, Lortek’s engineers have been able to benefit from a lightweight part, with less fuel and CO2 emissions during the production stage as well as a reduction in material waste and scraps.
Remember, you can post free of charge job opportunities in the AM Industry on 3D ADEPT Media or look for a job via our job board. Make sure to follow us on our social networks and subscribe to our weekly newsletter : Facebook, Twitter, LinkedIn & Instagram ! If you want to be featured in the next issue of our digital magazine or if you hear a story that needs to be heard, make sure to send it to contact@3dadept.com