En plus du coût et du temps de production, un autre challenge auquel les entreprises sont confrontées est la possibilité de fabriquer sans avoir recours à plusieurs machines. Xerion, un fabricant berlinois de systèmes de fabrication additive, offre une solution qui pourrait résoudre ce problème.
Baptisée Fusion Factory, la machine est une sorte de duplex qui fournit une ligne de production complète pour la FA métal en une seule machine. A travers cette machine, XERION entend répondre aux besoins de l’industrie des pièces détachées.
Selon Siddharth Tiwari, responsable R&D chez XERION, « un certain nombre d’entreprises européennes fournissent leurs systèmes complexes à travers le monde entier et la défaillance de petites pièces mécaniques (à géométrie complexe) peut entraîner des temps d’arrêt considérables des machines ».
De quoi est-elle constituée ?
Intriguant mais innovant, ce système semble combiner différents types de fabrication. En effet, le système de fabrication peut produire une pièce en trois étapes : Impression, Traitement et Frittage. (Printing – Debinding – Sintering).
Inspirée du MIM (Metal Injection Molding), Fusion Factory combine donc une imprimante à filament 3D (principe FFF), une station de déliantage (qui fonctionne selon le principe de l’élimination des solvants) ainsi qu’un four de frittage.
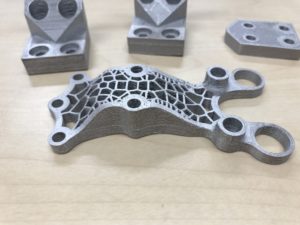
Lorsque nous avons demandé à Siddharth Tiwari pourquoi ils l’avaient construit sur la base de la technologie FFF, il nous a répondu que « le principe FFF est un procédé relativement propre et exempt de tout risque sanitaire dû aux poudres métalliques microscopiques requises dans des méthodes comme le SLM.
La poudre métallique est incorporée dans le filament à l’aide d’un liant et le gaspillage des matières premières est presque négligeable.
En plus du fait que ces filaments sont beaucoup moins chers, ce qui se traduit par des coûts de fabrication moins élevés par kilogramme, on peut également utiliser plusieurs filaments simultanément pour produire des pièces hybrides.
Ça pourrait être du métal avec de la céramique, du métal avec du métal et de la céramique avec de la céramique. »
Pour ce qui est des détails techniques, il convient de noter qu’un système intégré basé sur Siemens S7 (fail-safe) contrôle la machine en forme de duplex. De plus, avec une température de fonctionnement maximale de 1.550°C, le four de frittage permet à l’utilisateur de choisir parmi différentes atmosphères de frittage dont 100% d’hydrogène.
Selon Siddharth, « avec l’usine de fusion, les pièces endommagées peuvent être produites dans l’atelier même en 2 jours ouvrables normaux, ce qui élimine même les coûts liés au stockage de milliers de pièces par machine.
Cependant, au cours du développement, les avantages évidents du système de prototypage et de fabrication de géométries complexes sont devenus évidents et ont conduit à nos tentatives de commercialisation de la technologie pour des applications au-delà de la fabrication de pièces de rechange. »
Pour des informations exclusives sur l’impression 3D, abonnez-vous à notre newsletter et suivez-nous sur les réseaux sociaux !
Vous souhaitez-vous abonner à 3D ADEPT Mag ? Ou vous voulez figurer dans le prochain numéro de notre magazine numérique ? Envoyez-nous un email à contact@3dadept.com