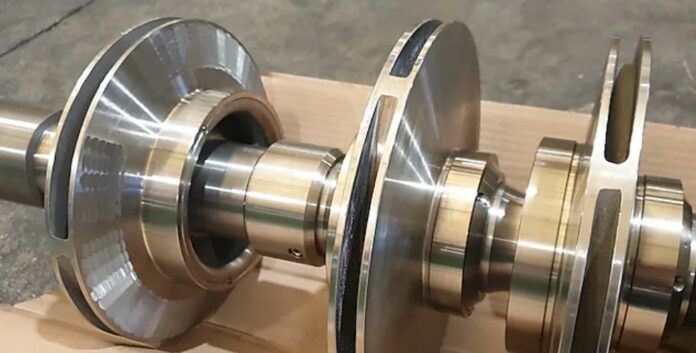
Oil and Gas company Shell envisions a strong digital future for 3D printed spare parts management…And they keep demonstrating how this future can be made possible thanks to AM.
The latest project the company has been involved in, demonstrates that 3D printed impellers can safely and reliably meet the needs of critical pumps, removing the need to store these impellers. As a reminder, it’s been a decade that Shell has been leveraging AM. However, this goal is the result of a decision taken in 2019, a decision that required to collaborate with key global suppliers to increase the portfolio of 3D printed spare parts that can be supplied to Shell.
One of these suppliers is Baker Hughes, American international industrial service company and one of the world’s largest oil field services companies. Together, for each production, both teams decide on the information that must be stored to enable buying spare parts on demand.
Furthermore, in this specific case, both partners needed to design a repeatable qualification process for vendors of 3D printed parts. If successfully completed, this milestone would help to easily scale up the use of AM in the energy industry.
“Our journey with additive manufacturing started more than 10 years ago in our laboratories and today we use the technology in our manufacturing sites. In collaboration with Shell, we are adopting innovative additive manufacturing solutions to reduce lead time and decrease physical inventories, while minimizing the carbon footprint of operations. We believe it can significantly improve the way the supply chains work, including that of centrifugal pumps”, Enrico Mangialardo, General Manager, Baker Hughes Pump Division states.
As far as 3D printed impellers are concerned, the use of AM does not only enable to achieve the desired outcome in terms of quality, but also provides the certainty that the team can stop stocking these impellers. Indeed, stocking these parts costs around a hundred thousand dollars for each pump in operation. This opened the door to significant, scalable savings for our manufacturing assets, Shell notes.
The thing is, despite the advantages of AM, one of the challenging parts of the process remains the criteria and testing to ensure the technical integrity of 3D printed parts. It is not easy to qualify a 3D printed part for deployment in our operations, especially for production critical applications, Shell recalls. Both teams learned a lot from mapping out the qualification requirements for the spare parts and in understanding the differences between companies in how they order parts and manage their supply chains.
The centrifugal pump was successfully started up with the additive manufactured components in May 2022. The pump has been subjected to intensive pre-installations testing to be accepted for operation and time will tell if, as expected, the 3D printed components will perform on par if not better than traditional impellers.
Shell qualified Baker Hughes facilities in Talamona in Italy to supply its assets with 3D printed spare parts, and the two companies are working together to further create a digital portfolio of impellers that can be 3D printed for Shell.
Lastly, despite the success of this project, Shell is aware that the road is still long to go to convince industry leaders to embrace a digital inventory strategy and additive manufacturing which is why the company also endeavours to be involved in the definition of global standards for the use of additive manufacturing in the energy sector.
Remember, you can post job opportunities in the AM Industry on 3D ADEPT Media free of charge or look for a job via our job board. Make sure to follow us on our social networks and subscribe to our weekly newsletter : Facebook, Twitter, LinkedIn & Instagram ! If you want to be featured in the next issue of our digital magazine or if you hear a story that needs to be heard, make sure to send it to contact@3dadept.com