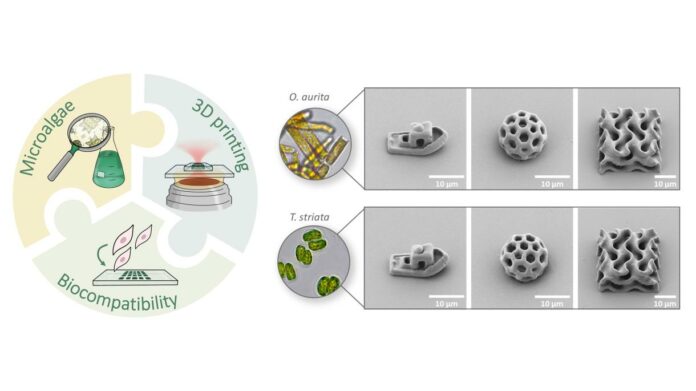
Researchers from Heidelberg University in Germany have fabricated inks for printing complex biocompatible 3D microstructures from the raw materials extracted from the microalgae.
Being led by Professor Dr. Eva Blasco from IMSEAM (Institute for Molecular Systems Engineering and Advanced Materials) at Heidelberg University, the team established the use of microalgae-based materials that could be harnessed for 3D cell cultures or 3D scaffolds.
The use of two-photon 3D laser printing at the manufacturing level
In the long list of AM techniques that could be used, the team identified two-photon 3D laser printing as the most beneficial for manufacturing at the micro- and nanoscale. As explained by the researchers, the process involves focusing a laser beam on a liquid, photoreactive resin, a so-called “ink”. Hence, the laser light activates special molecules known as photoinitiators and triggers a chemical reaction, causing local solidification of the ink.
Read more: The tiny world of micro-additive manufacturing technologies
Why the interest in microalgae to develop new materials?
Well, petrochemical-based polymers currently processed by the two-photon 3D laser printing technique lead to the depletion of fossil fuels and the emission of greenhouse gases – not to mention that they often contain toxic particles.
Microalgae become interesting due to their rapid growth rate, CO2 fixation during cultivation, and biocompatible. Yet, as per the words of Prof. Blasco, “They have hardly been considered as raw materials for light-based 3D printing.”
The team at Heidelberg University used two species of microalgae Odontella Aurita and Tetraselmis Striata with significant triglycerides. These triglycerides were removed & operated using acrylates. The photoactive green pigments contained in the microalgae worked as photoinitiators.
They triggered a chemical reaction to solidify the ink into 3D structures. These 3D structures were precise and had complex cavities with overhanging roofs. The survival rate of the 3D micro-scaffolds was efficient and paved the way for new possibilities of 3D printing with light.
Author: Nagarjun M
Remember, you can post free-of-charge job opportunities in the AM Industry on 3D ADEPT Media or look for a job via our job board. Make sure to follow us on our social networks and subscribe to our weekly newsletter: Facebook, Twitter, LinkedIn & Instagram! If you want to be featured in the next issue of our digital magazine or if you hear a story that needs to be heard, make sure to send it to contact@3dadept.com.