Avec plus de 30 ans d’expérience dans l’industrie, la fabrication additive continue d’évoluer. S’il est clair pour beaucoup qu’elle n’est plus seulement une solution de prototypage rapide, les idées préconçues concernant son utilité en tant que technologie de production doivent souvent être réévaluées. Alors que nous évoluons dans un contexte où l’attention se déplace vers des applications à plus grand volume telles que la personnalisation de masse et la fabrication de pièces standard, les pertes de production dues à la variabilité du processus et à l’utilisation inefficace des machines peuvent être des préoccupations communes – ce qui amène les utilisateurs de la Fabrication Additive (FA) à se poser une question à un million de dollars : quels sont les indicateurs clés de performance pour une « bonne » production par FA (métal) ?
Compte tenu des contraintes économiques actuelles, nombreux sont ceux qui évaluent la valeur de la FA à l’aune de son ROI (retour sur investissement – en anglais, return on investment). Ce n’est pas une mauvaise chose en soi, car cela peut aider à déterminer le nombre de pièces que les machines peuvent produire ou l’augmentation de la production au cours d’une journée de travail moyenne, facilitant ainsi le calcul du rapport coût-bénéfice. Le problème est qu’il peut être difficile de définir la FA sur la base des chiffres du retour sur investissement, et ce pour une raison simple : La FA ne fonctionne pas de la même manière que les autres machines de l’usine de production.
Les utilisateurs de la FA ont donc besoin d’une autre approche pour évaluer les paramètres de réussite de la FA. Ce dossier se situe à l’intersection des considérations commerciales générales et des besoins de fabrication des industries.
En se concentrant sur quatre procédés de FA des métaux (DED, FA par projection à froid et extrusion de matériaux), ce dossier vise à aider les utilisateurs de FA à évaluer les capacités de fabrication via la FA, à évaluer la candidature d’une technologie à la production de masse et à découvrir les indicateurs qui permettent à un utilisateur de déterminer les performances d’une machine.
La comparaison constante avec la fabrication traditionnelle : le jeu en vaut-il encore la chandelle ?
En général, et depuis longtemps, l’évaluation des paramètres de réussite de la FA se fait par rapport à la fabrication traditionnelle. Cela semble logique quand on connaît les avantages clés (liberté de conception et fabrication souple et rapide) que la FA apporte par rapport aux processus de fabrication traditionnels (reconnus pour leur capacité à permettre une production de masse ou une grande économie d’échelle).
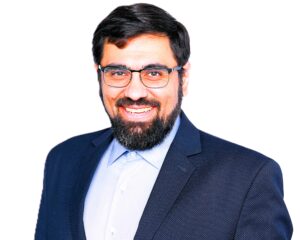
En réalité, parler de production et de FA ne fait pas nécessairement référence à la production de masse. « Lorsqu’on parle de production et de fabrication additive, en particulier dans le domaine de la FA des métaux, on ne pense pas nécessairement à la production de masse. La production peut impliquer un large éventail de conditions, depuis la validation initiale du concept (POC – proof of concept) et le prototypage jusqu’à la production personnalisée ou en petits lots, la production initiale à faible cadence (LRIP), la production à pleine cadence et la production de masse », explique le Dr Behrang Poorganji, directeur de la technologie de Nikon AM Synergy Inc.
Herbert Koeck, directeur général de Titomic, établit une comparaison claire avec le moulage et le forgeage :
« Contrairement aux fonderies de moulage et/ou de forgeage qui peuvent nécessiter des économies d’échelle plus importantes pour justifier l’investissement dans l’outillage et la production de pièces, la fabrication additive par pulvérisation à froid (en anglais, Cold Spray AM – CSAM) peut, pour certaines géométries, offrir une alternative de pièces presque nettes. La CSAM peut être configurée pour la production de masse, même si l’investissement dans la technologie CSAM présente l’avantage supplémentaire de la polyvalence, où un jour la machine produit comme une fonderie de titane, et le jour suivant comme une fonderie de cuivre ».
Toutefois, cette comparaison n’est pas toujours applicable si l’on se rend compte que la FA vient souvent améliorer les processus existants, les rendant plus efficaces et efficients. En outre, la FA est parfois victime de son propre succès : plus la technologie progresse, plus elle complexifie d’autres domaines de la chaîne de fabrication, même lorsque le processus réduit les coûts industriels, raccourcit les délais ou améliore la durabilité de la fabrication.
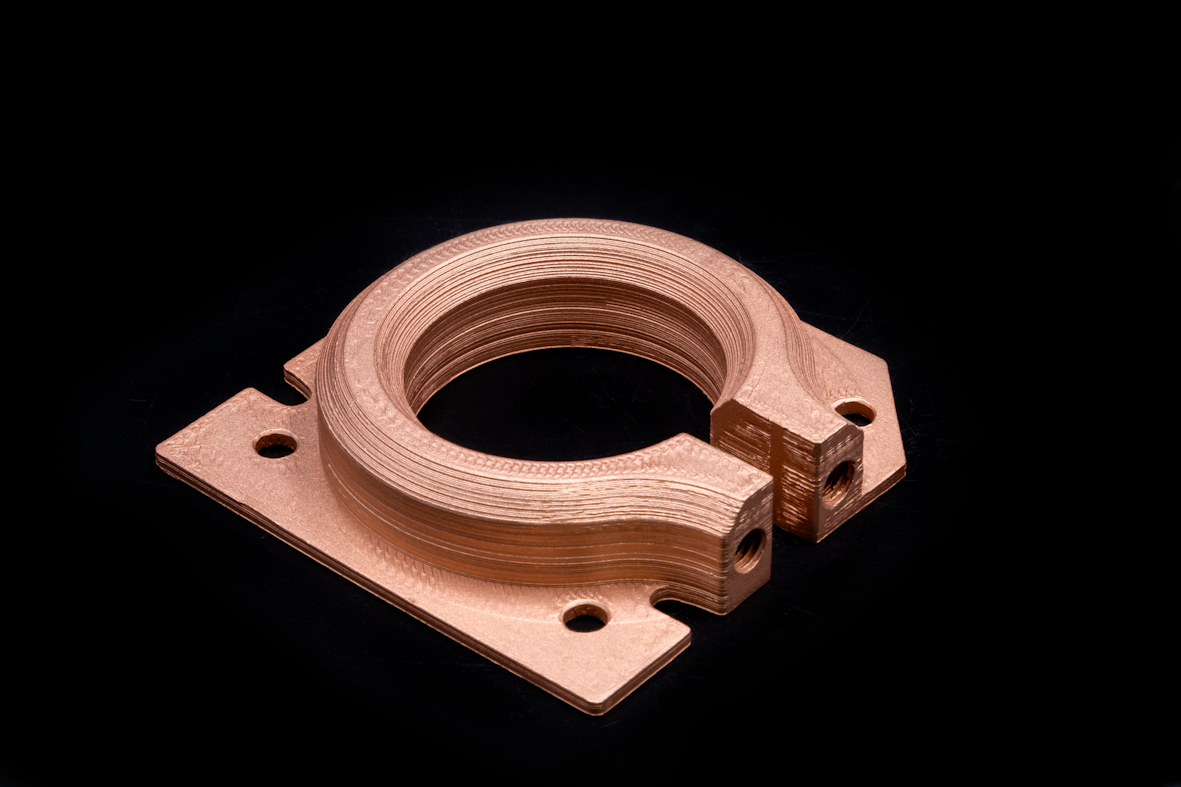
Ces considérations font évoluer la définition de la FA parmi ses utilisateurs et conduisent souvent à une comparaison entre les technologies de FA elles-mêmes.
Avec plus de vingt procédés d’impression 3D métal différents, le paysage de la FA métal est probablement le domaine de fabrication le plus diversifié. Si l’application détermine souvent le choix de la technologie, la fusion laser sur lit de poudre reste la technologie la plus répandue. Pour des raisons évidentes, nous avons décidé de nous concentrer sur trois autres procédés de FA métal qui gagnent du terrain sur le marché.
Ceci étant dit, pour ceux qui cherchent à faire leurs premiers pas dans le domaine de la FA, il n’y a pas de communication claire sur l’utilisation appropriée et le champ d’application de chaque technologie.
Si nous devions évaluer l’utilisation et le champ d’application appropriés des processus de fabrication traditionnels, nous aurions pris en compte des caractéristiques telles que le coût et le prix, ainsi que d’autres considérations liées à la production de masse et à la chaîne d’approvisionnement mondiale. Ces considérations peuvent inclure la main-d’œuvre, l’énergie, les matières premières, le soutien à la production, la recherche, la conception et l’amortissement de l’ingénierie, pour n’en citer que quelques-unes.
(Le coût indique l’efficacité de la fabrication, tandis que le prix est une mesure orientée vers le client qui reflète idéalement la valeur du produit).

Dans le cas de la FA des métaux, « la première question que nous devons nous poser est de savoir pourquoi nous choisirions la FA pour la production de masse et envisagerions d’utiliser une chaîne d’approvisionnement mondiale à cette fin. Prenons-nous en compte le coût, la fonctionnalité, la performance, le délai d’exécution, les incidences sur l’environnement et la durabilité, la sécurité, etc. comme facteurs de décision dans le choix de la FA ?
La rentabilité, la disponibilité et les propriétés des matériaux, la complexité de la conception (où la FA offre des avantages considérables), les exigences de précision et de qualité et l’évolutivité sont autant de facteurs qui déterminent la pertinence de la production de masse. Les produits très demandés dont la chaîne d’approvisionnement est soumise à des contraintes en raison de l’utilisation de technologies de fabrication conventionnelles pourraient être de bons candidats à la production de masse par FA métal et à la mise en place d’une chaîne d’approvisionnement mondiale. Les considérations relatives à la propriété intellectuelle sont également importantes lorsqu’il s’agit de tirer parti d’une chaîne d’approvisionnement mondiale dans le domaine de la FA des métaux », souligne Poorganji.
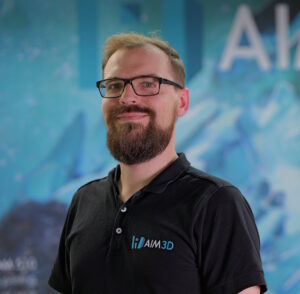
Pour Clemens Lieberwirth, directeur technique d’AIM3D GmbH, « il n’existe pas d’argument commercial valable en faveur de la production de masse par FA, mais pour ce qui est de la production en petites séries, il existe à mon avis trois indicateurs :
- Taille de la série – en fonction de la taille/complexité de la pièce, jusqu’à 10 000 pièces/an
- Conception du produit optimisée pour la FA (en fonction du processus de FA) – la taille de la pièce, l’épaisseur de la paroi, les porte-à-faux, les plus petits détails et les canaux internes doivent être adaptés au processus de FA spécifique afin d’obtenir le meilleur résultat en termes de qualité et de coût.
- Indépendance en termes de choix des matériaux et de lieu de production. Les systèmes qui ont des politiques ouvertes en matière de matériaux permettent d’obtenir les meilleures performances en termes de coût et de qualité et rendent la ligne de production sûre en cas de crise ».
Ainsi, une comparaison entre les processus traditionnels et les processus de FA peut être intéressante, mais elle n’est plus indispensable pour déterminer les indicateurs de performance clés d’une bonne production par FA.
En outre, nous pouvons associer la fabrication conventionnelle à la production de masse, mais nous devons garder à l’esprit que la valeur de la fabrication additive ne réside pas dans la reproduction de ce que la production de masse accomplit déjà, mais dans le fait d’exceller là où la production de masse peine à être efficace.
La question de la normalisation
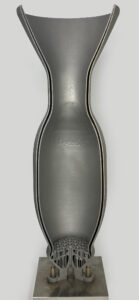
Il aurait été difficile de ne pas mentionner la question de la normalisation quand on sait que les stratégies de fabrication qui s’appuient sur des processus de fabrication traditionnels défendent la normalisation. En effet, certains produits – en particulier ceux qui sont produits en masse ou certaines industries – accordent plus de valeur à la standardisation alors que cette valeur semble diminuée avec la FA qui favorise la personnalisation.
« Pour la production à haute cadence dans l’aérospatiale et la défense, la reconnaissance ISO/ASTM aide à obtenir des résultats cohérents lorsqu’un produit passe du développement à la production à grande échelle qui nécessite la collaboration d’équipes plus importantes », souligne l’expert de Titomic.
Par ailleurs, il n’existe que sept catégories de processus de FA établies par l’ISO/ASTM (l’Organisation internationale de normalisation). Pour ceux qui découvrent la FA, ces catégories comprennent l’extrusion de matériaux, la projection de matériaux, la fusion sur lit de poudre, le laminage de feuilles, la projection de liants, le dépôt direct d’énergie (DED) ainsi que la photopolymérisation (VAT). Cela n’empêche pas les utilisateurs de FA d’utiliser des procédés de FA des métaux qui n’entrent pas dans ces catégories.

La question est de savoir si cela a de l’importance. Les experts ont des avis différents sur le sujet :
« La reconnaissance dans le cadre d’une norme mondiale telle que les normes conjointes ISO/ASTM pour la FA est très importante, mais sa nécessité absolue dépend de l’industrie et des produits. Il existe d’autres normes et spécifications telles que SAE AMS, AWS, MIL qui sont nécessaires dans certains contextes pour des produits/industries spécifiques. Les normes sont essentielles pour garantir la qualité lorsqu’il s’agit de la répétabilité et de la fiabilité du processus. Elles établissent également un langage commun permettant d’instaurer la confiance et la crédibilité, de comprendre les risques et de satisfaire aux exigences réglementaires spécifiques définies par des agences telles que la FAA, la FDA, la NASA, etc. en définissant des exigences et en établissant des processus de certification », a déclaré l’expert de Nikon AM Synergy Inc.
« Je ne pense pas que cela soit absolument important aujourd’hui. Les normes sont en partie très générales et tentent de fusionner différentes technologies, qui ont des principes d’action technologiques différents. De nombreux clients sont encore déconcertés par le nombre de technologies de FA différentes et ne parviennent pas à différencier ce qui est adapté à un processus ou à un autre. Les normes qui mélangent ces processus n’y changeront rien. Mais bien sûr, une plus grande clarté et des normes adaptées pourraient également y contribuer à l’avenir », affirme le directeur technique d’AIM3D.
Quels sont donc les indicateurs de performance à prendre en compte pour une production par FA et pour une imprimante 3D ?
Dans ce dossier, les termes « facteurs de succès » et les « indicateurs clés de performance » sont utilisés de manière interchangeable pour qualifier une production de FA et les performances d’une machine. Pour une production par FA, nous pensons que si un processus de FA a été capable d’apporter de la valeur grâce à la personnalisation, de permettre la complexité à faible coût et en petits volumes, de permettre la fabrication à la demande et d’assurer l’amortissement, c’est déjà une victoire.
Certaines considérations techniques peuvent mettre l’accent sur ce point :
« Dans la production par FA métal, il existe plusieurs indicateurs clés de la réussite de la production. La qualité des pièces, la répétabilité et la fiabilité du processus de fabrication, la rentabilité et l’efficacité de la production, les délais de production et de livraison, ainsi que la durabilité en ce qui concerne la réduction des déchets et la possibilité de réutiliser et de recycler les matériaux font partie de ces indicateurs.
Lorsqu’il s’agit d’évaluer les performances des machines de FA, le temps de fonctionnement, la fiabilité, la facilité d’utilisation et la disponibilité des services et de la maintenance sont des facteurs essentiels. D’autres considérations critiques incluent le débit de la machine, le volume de fabrication, la résolution d’impression, l’automatisation du processus (en particulier dans la production en série, ou lorsque les opérateurs qualifiés ne sont pas facilement disponibles), et l’intégration de la surveillance en cours de processus pour l’état de la machine et l’assurance qualité », souligne le Dr Behrang Poorganji.
Herbert Koeck, de Titomic, donne un exemple parlant de leur technologie :
« La cohérence des processus est très importante et Titomic la mesure de plusieurs façons. L’une des principales mesures des systèmes de Titomic est la vitesse de la poudre et le dépôt de matériau. Avec des taux de dépôt élevés, Titomic produit des pièces en titane grandes et solides à raison de 5 kg par heure, en fonction de l’application. »
Avant de mettre en avant les indicateurs de performance de leurs imprimantes 3D industrielles, notons que Nikon AM Synergy Inc. apporte son expertise en tant que fabricant de technologies DED. La société a récemment dévoilé une imprimante 3D DED Lasermeister qui attire les clients à la recherche de la plus haute qualité et précision pour réparer des pièces critiques telles que des pales de turbine ou des moules et matrices complexes et coûteux. L’une des principales caractéristiques de cette solution DED est sa taille compacte et ses capacités d’automatisation avec numérisation intégrée, compensation géométrique et génération de trajectoires d’outils pour la réparation de pièces complexes. Cela permettra d’obtenir un taux de rebut extrêmement faible, ainsi qu’un traitement hautement efficace et reproductible, indépendamment du niveau de compétence de l’opérateur de la machine.
Crédit : Nikon AM Synergy Inc.
Voici comment Poorganji décrit les performances de son imprimante 3D à la lumière des critères de valeur ci-dessous :
Critères de valeur | Réponses |
Cela permet-il d’obtenir une épaisseur de paroi ? | Les systèmes de réparation DED Lasermeister de Nikon sont tout à fait capables de produire des parois de faible épaisseur et des caractéristiques à haute résolution, jusqu’à 500 microns (0,5 mm). Nos machines à haut rendement de la prochaine génération ont des capacités encore plus fines, avec une résolution de 200 microns (0,2 mm). |
Quelles sont les dimensions minimales et maximales des pièces réalisables ? | Notre système de génération actuelle peut produire des pièces d’une hauteur maximale de 400 mm avec une section transversale approximative de 300 x 200 mm. Notre système DED de prochaine génération pourra produire des pièces allant jusqu’à 650 mm. |
Taux de construction | Notre système de réparation DED dernière génération peut fournir 2 à 5 cc/h. Pour notre système DED de nouvelle génération, nous visons +100 cc/h. |
Assurance qualité | Nous disposons d’une option de surveillance qui fonctionne durant le processus de fabrication dans notre système DED pour la fusion et le taux d’alimentation en poudre. |
Inspection et contrôles de qualité | Notre solution de réparation DED est intégrée à un système de numérisation optique pré et post 3D pour garantir la précision des dimensions. Chez Nikon, nous bénéficions également de l’inspection non destructive Nikon X-CT. |
Finition et post-traitement? | La haute résolution de notre système de réparation DED et le dépôt de matériaux fins permettent d’obtenir des surfaces très lisses et de minimiser la zone affectée par la chaleur (HAZ) et la distorsion thermique. L’utilisation de notre solution de réparation Nikon DED permet de réduire le temps et les coûts de l’étape de post-traitement. |
Matériaux? | Nous disposons de paramètres pour une grande variété de matériaux et notre système est compatible avec les poudres réactives et non réactives. A titre d’exemple, nous pouvons traiter les aciers, les alliages de Ti, les alliages de Ni, les alliages de Cu et les alliages de Nb. |
Sensibilité à la qualité (nécessite-t-elle des outils spécifiques pour contrôler les défauts, par exemple ?) | La caractérisation microstructurale standard, les propriétés mécaniques et physiques des matériaux et les essais non destructifs (END) standard sont les outils conventionnels que nous utilisons. |
La technologie de pulvérisation à froid de Titomic excelle dans la création de grandes pièces à partir de titane pur à une forme presque nette. Titomic développe les meilleures solutions de projection à froid au monde pour répondre aux demandes de ses clients. Des systèmes portables à basse et moyenne pression aux systèmes de fabrication additive à haute pression Titomic Kinetic Fusion®, les solutions de pulvérisation à froid de Titomic constituent une plate-forme solide pour la mise en œuvre de la pulvérisation à froid dans les organismes de R&D, industriels et gouvernementaux, y compris les applications dans les domaines de la défense et de l’aérospatiale.
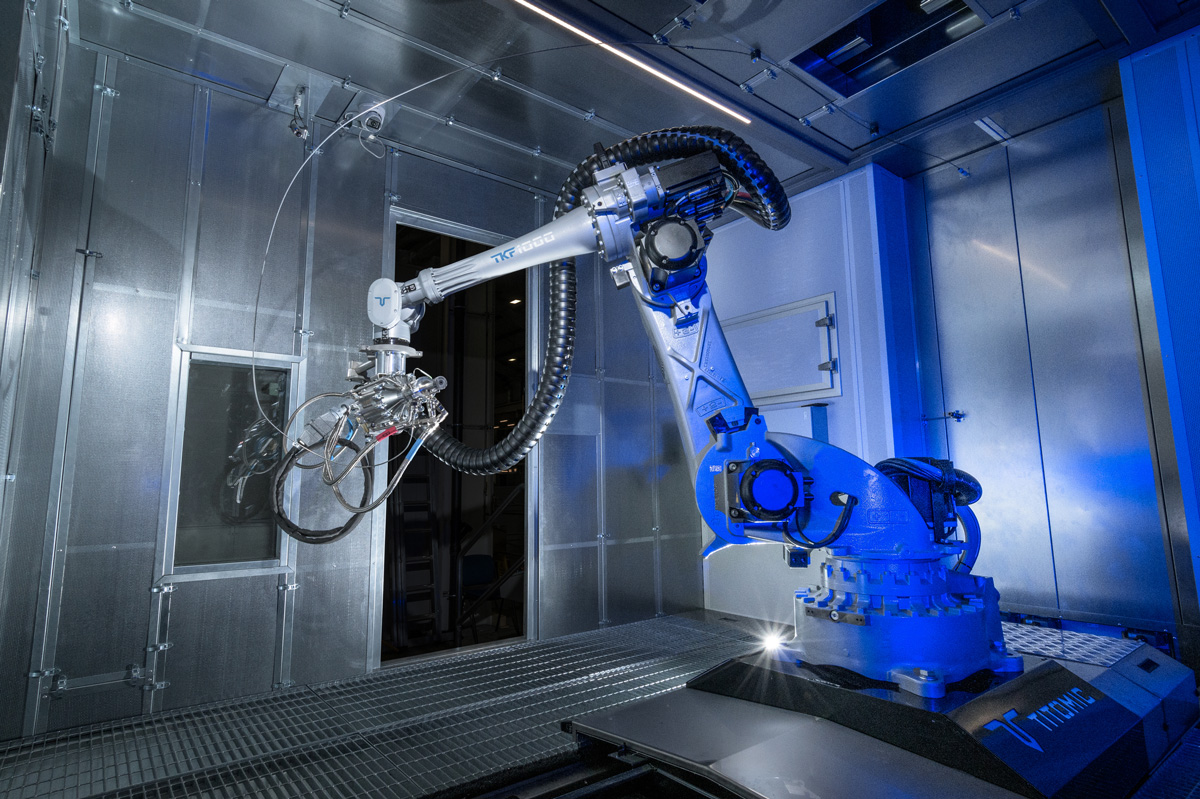
Le système de projection à froid haute pression TKF-1000 de Titomic est un système modulaire de projection à froid conçu pour le prototypage et la R&D, ainsi que pour la production à petite échelle. Il est doté d’une robotique et de systèmes de contrôle avancés, de vitesses de fabrication inégalées dans l’industrie et d’un matériel de pointe.
Crédit : Titomic. Système de pulvérisation à froid haute pression TKF-1000
Voici comment Herbert Koeck décrit les performances de son imprimante 3D à la lumière des critères de valeur ci-dessous.
Critères de valeur | Réponses |
Cela permet-il d’obtenir une épaisseur de paroi ? | Oui. L’épaisseur de la paroi dépend du matériau, des paramètres de pulvérisation à froid utilisés et de la géométrie construite (pièces plates ou rotatives). Par exemple, Titomic a obtenu une épaisseur de paroi de 75 mm en CP-Ti. |
Quelles sont les dimensions minimales et maximales des pièces réalisables ? | La limite maximale est soit une limite de contrainte résiduelle, soit une limite de post-traitement telle que la taille du traitement thermique disponible.
Le minimum dépend de la géométrie et du système de pulvérisation à froid utilisé. Avec un diamètre de prune allant de 3 à 12 mm, les pièces issues d’un moulage proche du filet ou de pièces forgées peuvent être bien adaptées à la projection à froid. |
Taux de construction | Un taux de production raisonnable est de 1 litre par heure. Pour les matériaux soumis à des contraintes plus élevées, cette cadence est ramenée à 0,5 et 0,25 litre par heure.
Titomic peut produire du titane et d’autres pièces à des taux de 5kg/heure, en fonction des exigences de l’application du produit, y compris l’optimisation des propriétés du matériau. |
Assurance qualité | Titomic enregistre soigneusement tous les paramètres de la pulvérisation à froid, tels que le débit d’alimentation, la température du gaz et la pression. |
Inspection et contrôles de qualité | Des techniques de contrôle non destructif peuvent être utilisées, telles que les ultrasons, pour vérifier que les pièces ne présentent pas de défauts.
Titomic procède à d’autres inspections dans son laboratoire sur place et dans ses installations de finition des machines. |
Finition et post-traitement? | Les pièces de Titomic peuvent être utilisées telles quelles dans certaines applications. Sinon, la pièce telle qu’elle a été pulvérisée est directement usinable. Les pièces fabriquées par pulvérisation à froid étant proches de la forme nette, elles peuvent nécessiter un usinage pour enlever 5 à 10 % de matière afin d’atteindre la tolérance finale.
Une fois terminée, la pièce peut nécessiter un traitement thermique, en fonction du résultat final souhaité ou de l’application de la pièce. Titomic a obtenu de très bons résultats dans l’utilisation du pressage isostatique à chaud, avec des pièces présentant des valeurs significatives de résistance par rapport au poids.
|
Matériaux? | La plupart des métaux qui peuvent être pulvérisés peuvent l’être à froid. Cependant, si une poudre a un rapport résistance/densité élevé, elle peut être difficile à fabriquer car elle nécessite une vitesse élevée des particules et peut donc être fortement sollicitée pendant le dépôt (par exemple, les aciers au carbone).
Le processus de pulvérisation à froid de Titomic excelle dans la fabrication et le revêtement du cuivre et de ses alliages, du titane et de ses alliages, du tantale, des aciers inoxydables et de l’Inconel In718 et 625. |
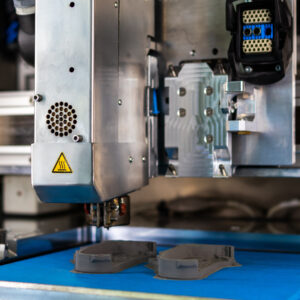
AIM3D GmbH a mis au point une imprimante 3D multi-matériaux qui imprime des produits en métaux, céramiques, plastiques et plastiques renforcés à partir de granulés de moulage par injection standard, sans conversion coûteuse des machines.
C’est ainsi que Clemens Lieberwirth décrit les performances de sa technologie d’impression 3D à la lumière des critères de valeur ci-dessous.
Critères de valeur | Réponses |
Cela permet-il d’obtenir une épaisseur de paroi ? | Oui, elle permet d’obtenir des épaisseurs de paroi. |
Quelles sont les dimensions minimales et maximales des pièces réalisables ? | Taille minimale de la pièce ~ 0,125 cm³ (taille d’une dent)
Taille maximale de la pièce ~ 500 cm³ (taille d’une paume) |
Taux de construction | ~ 60 -250 cm³/h |
Assurance qualité | Contrôle des paramètres du processus (température, mouvement, extrusion, obstruction de la buse) |
Inspection et contrôles de qualité | Inspection visuelle, poids, mesures dimensionnelles |
Finition et post-traitement? | Ébarbage, frittage, coupe des filets, ponçage, polissage si nécessaire |
Matériaux? | Aciers inoxydables, aciers faiblement alliés, métaux non ferreux comme le titane, le cuivre, le laiton, les alliages ferromagnétiques, les métaux durs, les céramiques … |
Sensibilité à la qualité (nécessite-t-elle des outils spécifiques pour contrôler les défauts, par exemple ?) | Dépend du cas d’utilisation |
En résumé…
Alors qu’une bonne production avec les procédés de fabrication conventionnels dépend de sa capacité à assurer une production de masse et à répondre aux exigences de la chaîne d’approvisionnement, une bonne production avec la FA dépend de nombreux paramètres qui impliquent la performance de la machine, sa capacité à fournir de la valeur grâce à la personnalisation, à permettre la complexité à faible coût et en petits volumes, ainsi que la capacité à permettre la fabrication à la demande. En outre, compte tenu du contexte économique actuel du marché, la grande accessibilité, la rapidité, les coûts d’entrée et les faibles coûts de production par unité sont également des indicateurs de performance qui jouent en faveur de la FA. Ils révèlent que plus la FA évolue et est utilisée, plus les indicateurs de performance sont identifiés sur la voie de la réussite.