A recent dossier of 3D ADEPT Mag that discussed the secrets of resin 3D printing, shed light on the various features one should consider when choosing a resin 3D printing technology. While the choice for one technology over another finally comes down to the taste of the chef in the kitchen, it should be noted that one disadvantage often highlighted in the use of resin 3D printing is the toxicity of the materials used.
As companies always strive to do better, we came to realize that some industry insiders currently explore solutions to address this issue. One of them is Liqcreate. The Netherlands-based materials’ producer has dedicated its core business to the development of resins. It understands that each 3D printing application has its own requirements which are not often met by ‘off-the-shelf’ resins.
If you are interested in resin 3D printing, then you probably know that the company recently launched a nano-ceramic reinforced Composite-X resin for 3D-printed heavy-duty parts. In this Opinion of the Week, we caught up with Ruben Bosch, Sales and Marketing Executive at Liqcreate to discuss the a few non-toxic solutions that can be used in a resin 3D printing process.
With a background in International Business and Management, Bosch came to realize the potential of 3D printing – SLA/DLP 3D printing technology especially – in 2012 at a dental technology company. With a keen interest in (digital) technologies, the sales expert’s entrepreneurial and creative mind-set has been enhanced ever since he started working in the resin 3D printing market. As per his words, the technology helps him “see opportunities and build bridges between companies and people.”
Could you tell us more about Liqcreate?
Liqcreate is a company that develops and manufactures premium photopolymers for SLA, DLP and MSLA/LCD technologies. The company was founded in 2017 and delivers its services to a wide range of industries including prototyping, industrial, entertainment, consumer goods, healthcare and automotive.
We also offer solutions to re-brand our product portfolio into any shape. This could be a turn-key solution to simply attach your own label on our products or we can provide our photopolymers in bulk volumes.
Furthermore, we offer the possibility to develop unique resins for specific applications. Our chemists can create photopolymers with different colours and different polymeric properties. Moreover, we can support 3D-printer manufacturers with the development of photopolymers with specific polymerization kinetics to work on any 3D printer.
As an independent manufacturer with sales, R&D, and manufacturing facilities, we are also able to rapidly scale production where needed. As a result, we can offer large scale 3D printing bureaus and manufacturers the opportunity to quickly get their resin to market in relatively low quantities to minimize their risks.
Despite the numerous advantages of resin 3D printing, resins are often said to be toxic. How can operators recognize a toxic resin from a non-toxic resin?
When working with resins, it is important to pay attention to the GHS safety symbols and hazard statements which can be found on the product label and Safety Data Sheet (SDS). These are the main items to look for when evaluating the toxicity of a resin.
To properly understand how toxicity is defined, we have to dive into the hazard statements resins have and evaluate each one. There are certain rules and regulations to define the toxicity of a product. These rules and regulations are the CLP Regulations, which are maintained and controlled by the European Chemicals Agency (ECHA). It is the central agency that implements the EU’s chemical legislation to protect people and the environment from the hazards of chemicals.
To simplify this, toxicity can be divided into “toxic for the environment” and “toxic for human beings.” Toxic for human beings is split into acute and long-term effects. If a mixture is not toxic it can still have health hazards, for example, skin irritation, eye irritation, allergic reaction etc.
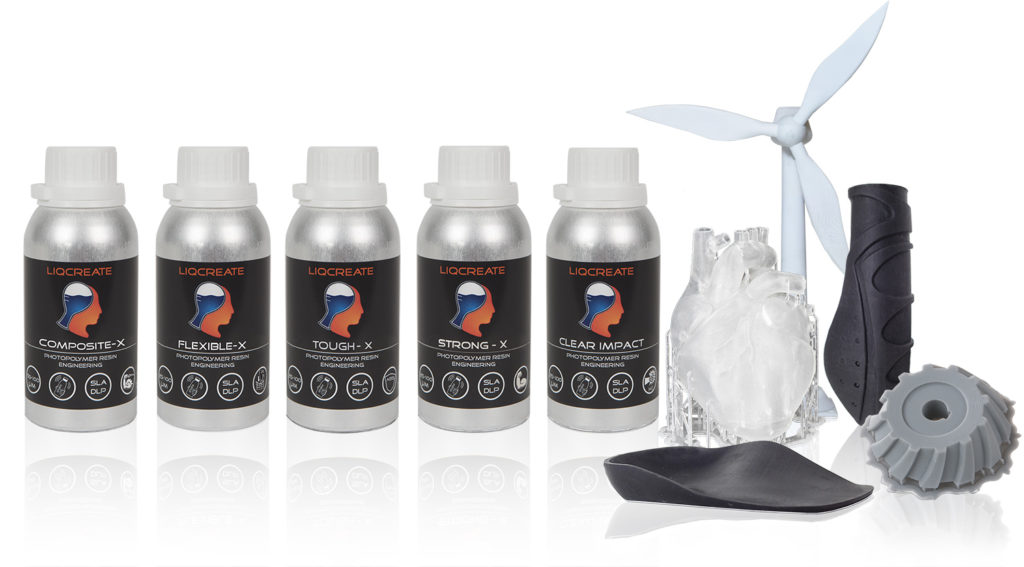
Liqcreate started with the development of a non-toxic resin-cleaning agent. Why not a non-toxic resin first?
Developing a non-toxic resin with high-end features which is suitable for stereolithography is very complex. Creating a resin without hazards is kind of impossible. At the moment, our suppliers for raw materials are not yet able to produce raw materials without any health hazards which is why we are limited in our options to create such a resin.
However, looking at our standard materials we did manage to keep the amount of hazards to a bare minimum. Furthermore, we are also working on bio-based resins.
In 2018 we participated in a study to formulate a resin with novel renewable (meth)acrylates based on soybean oil for stereolithography 3D printing, together with the University of Groningen, Stenden/NHL University and Green PAC (link to Dutch article)(data study). During this study, we evaluated the possibilities to create a bio-based resin. Results showed that we successfully create a resin with up to 85% bio-based content and interesting properties for prototyping applications. The study even won the first price in the SABIC KNCV-MM HBO Poster Award presented by GreenPac during the Dutch Polymer Days (DPD) in 2019. Together with multiple universities, we are now looking further into the market opportunities within recyclable and bio-based materials.
Let’s talk about resin cleaning agents. How do we use them?
Ultimately, a resin cleaner aims to clean the part you have printed before post-curing the part in UV light, which is the final state of post-curing any resin. Operators use to perform resin cleaning with isopropyl alcohol or ethanol. This solvent can easily be obtained anywhere and does a very good job dissolving resin leftovers from 3D printed parts. The excess resin will get dissolved in the IPA, which eventually turns from a clear liquid to a coloured and polluted fluid after many prints have passed through. Cleaning with IPA works especially well if IPA concentration is 80% or higher and if it is actively circulated, a feature usually found in resin cleaning equipment.
There are however a couple of problems. IPA is not exactly a safe material, although it is commonly available. It is flammable, and cannot be stored without safety precautions. It tends to open up pores of the skin if exposed, and this allows for faster entry of dissolved resin if you’re working with a “dirty” IPA.
For these reasons, we felt there was a need to make post-processing safer and more environmentally friendly. Therefore, we developed our Liqcreate Resin Cleaner.
Could you please provide further details on the main features of this solution? And the resin-based technologies with which it is compatible?
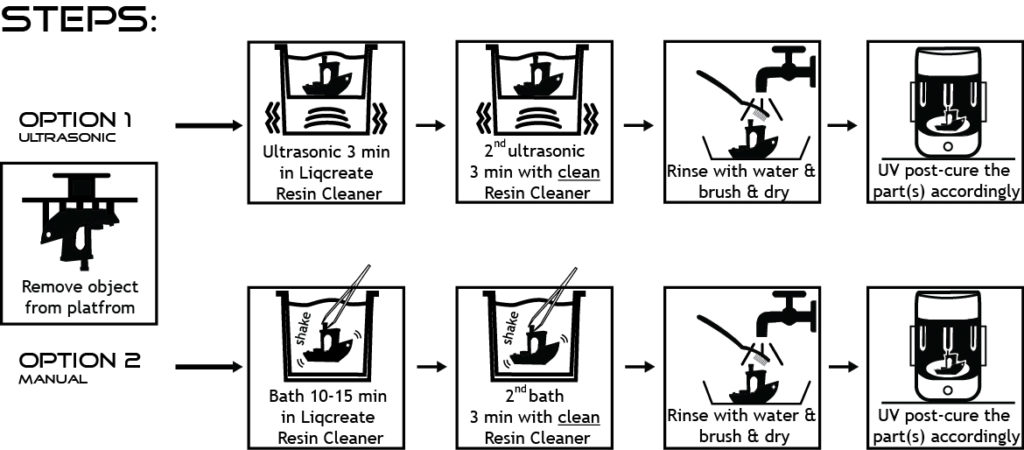
Of course, our Resin Cleaner is a non-toxic cleaning solution for 3D printed objects. It is a safe, highly effective solvent that cleans faster than cleaning liquids based on IPA, bio-ethanol and other chemicals. Moreover, it is not a dangerous good, non-flammable and has less odour. Therefore it is excellent for in-office printing. The cleaning liquid can clean SLA, DLP and LCD/MSLA 3D-printed objects, platforms and instruments.
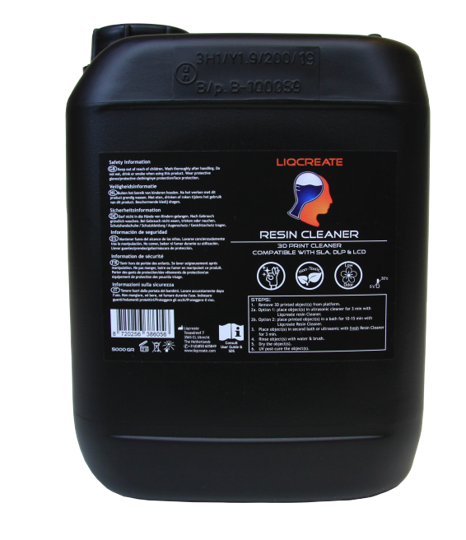
Apart from toxicity, are there any differences between non-toxic resin cleaning agents and other resin-cleaning agents?
Apart from toxicity, our Resin Cleaner is more effective compared to IPA and can be used in ultrasonic cleaners. Due to the flammability of IPA, it is not recommended to use this in combination with ultra-sonic cleaners. Using alternative resin cleaners often require a new washing protocol. IPA and Ethanol work great for washing printed parts and are easy to use because the leftover IPA and Ethanol will evaporate. After evaporating, the parts are ready for post-curing. This fast evaporation brings some health side-effects, which are not present in our resin cleaner. The down-side is that the resin cleaner will require a second washing step to remove the excess resin cleaner on the part.
Is there anything else you would like to share on this topic?
Some small tips from our side for using Liqcreate Resin Cleaner to save some money, work more efficiently, and reduce your carbon footprint:
- When using two separate containers (two-step system) for cleaning your 3D printed objects, you will not only work faster but also reduce your carbon footprint and save money. Using two separate containers will help increase the number of washing cycles which means, you can work longer with the Resin Cleaner.
- To achieve a perfect surface finish of your part, always wash a second time in a fresh Resin Cleaner.
- Although our resin cleaner works very well to clean 3D-printed objects, printer build plates and equipment, it should be noted that ABS plastic can crack when in contact with the resin cleaner for an extended time. For instance, handles of your ultrasonic cleaner or other ABS plastic parts.
- When your Resin Cleaner is very dirty please replace it with fresh Resin Cleaner to ensure your parts will not get a sticky surface.
Remember, you can post job opportunities in the AM Industry on 3D ADEPT Media free of charge or look for a job via our job board. Make sure to follow us on our social networks and subscribe to our weekly newsletter : Facebook, Twitter, LinkedIn & Instagram ! If you want to be featured in the next issue of our digital magazine or if you hear a story that needs to be heard, make sure to send it to contact@3dadept.com