With the growing production of larger product batches, PROTOTEC, a Germany-based 3D printing service bureau, decided to streamline its post-processing operations by relying on AM Solutions’ S1 System.
Showcased at formnext 2021 and currently utilized by a number of well-established industrial companies, including OECHSLER and Alfa Romeo Racing ORLEN, the S1 system is designed for small to midsize volumes of 3D printed parts. Dedicated to automatic de-powdering and cleaning, it offers numerous technical features, such as a basket design for optimal distribution and circulation of the parts, a specially developed wear protection lining made of non-staining anti-static polyurethane, ATEX conformity, and safe and ergonomic machine handling.
“To provide costeffective solutions to our customers in this field, at the moment we are investing in several new 3D printing and post processing systems. Especially the post processing in the SLS field offers a great potential and contributes significantly to a higher quality and costefficiency of our products. With AM Solutions we found a partner who can offer excellent technological and economical solutions”, Torsten Wolschendorf, the general manager of PROTOTEC states.
The AM brand of Rösler states that PROTOTEC has been using the S1 system since July 2021, for cleaning and surface finishing of products printed with the SLS method.
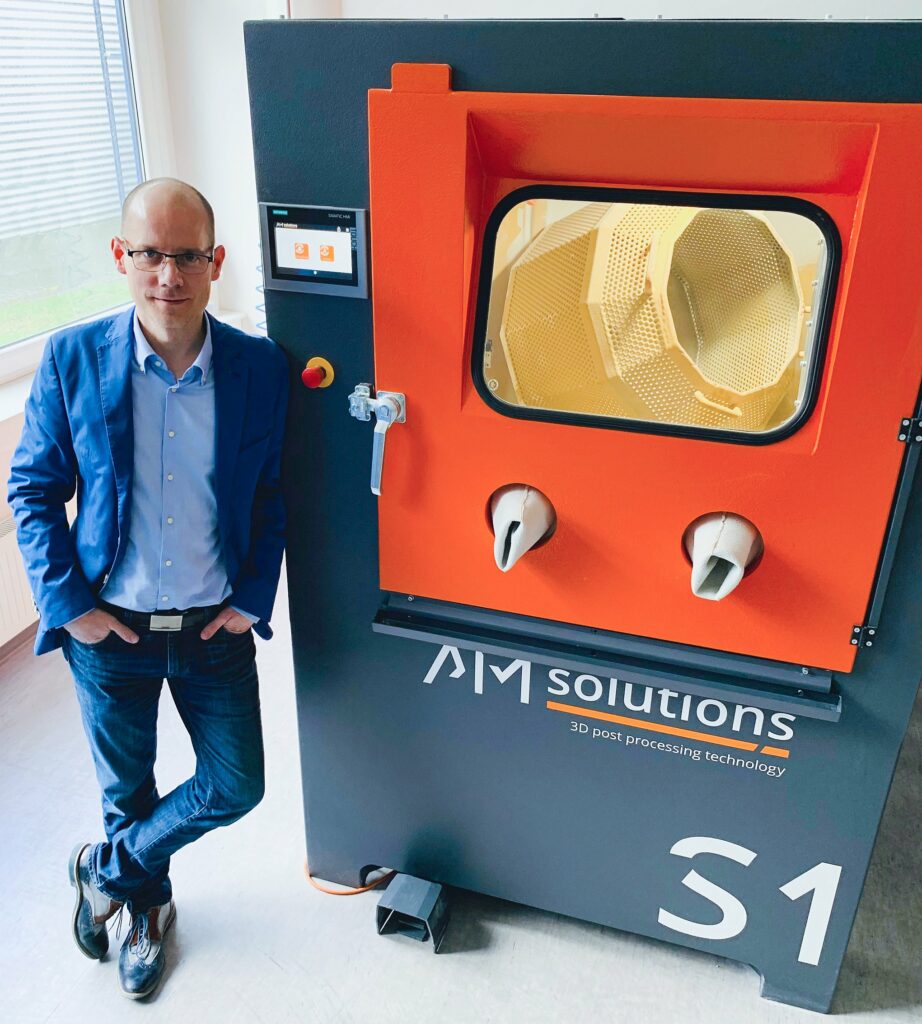
The machine’s smart plug-and-play concept is setting new standards in the field of post processing components printed with powder-bed based polymer printing systems. Especially impressive is that the de-powdering, cleaning and surface finishing functions can all be handled in one single machine. As needed, the blast media can be easily and quickly exchanged. This operation just takes a few minutes. The 2-in-1 concept saves not only the expenditures but also the space requirements for an additional machine. Whenever special single components must be processed, the integrated machine controls allow a simple switch to manual operation. Time-consuming retooling, as required with other machines, is no longer necessary. The machine controls with a full color display panel offer an intuitive navigation through the menu and allow the callup of up to 30 processing programs, AM Solutions explains.
“Actually, the cleaning performance of the S1 is so good that we are saving a lot of time with the preceding unpacking operation. In this context the effective blast media cleaning and recycling system is particularly advantageous. It separates the usable blast media from broken down media and the loose powder removed from the components. This guarantees not only consistent blast results but also a longer uptime of the dust collector cartridges. The components are processed in a tiltable rotary basket. The rotation causes the work pieces to gently tumble over each other. This ensures excellent, consistent all-around blasting results. The S1 significantly reduced the time required for post processing. Previously manual blasting of a full load of midsize components required about 5 to 8 hours. Today we only need about one hour for the same process, including unpacking”, Torsten Wolschendorf concludes.
Remember, you can post job opportunities in the AM Industry on 3D ADEPT Media free of charge or look for a job via our job board. Make sure to follow us on our social networks and subscribe to our weekly newsletter : Facebook, Twitter, LinkedIn & Instagram ! If you want to be featured in the next issue of our digital magazine or if you hear a story that needs to be heard, make sure to send it to contact@3dadept.com