At the very beginning, when manufacturers started using Additive Manufacturing (AM), the market was severely lacking in materials specifically designed for the technology. Contract manufacturers therefore worked with leftovers and scrap with general specifications, which restrained the success of part quality.
Today, material producers have developed metal powders with AM production in mind. However, their high cost has increased the demand for recycling of unmelted powder – especially in powder-bed AM processes. For manufacturers who are willing to explore reuse or recycling strategies, meeting this demand also means enabling sustainability performance – or at least enabling an environmental framework to sustainability. Most importantly, meeting this demand requires to leverage interdisciplinary resources that go beyond the simple expertise of material experts.
The present feature ambitions to discuss some of the powder recovery/reuse technologies and strategies that could be used to save metal powder while taking into account these interdisciplinary resources. It might serve as a complementary resource to the dossier “Issues raised by metal powder removal”, as it will also focus on the importance of the recovered powder with regards to sustainability and viability of materials.
Powder recovery: the “Why”
Let’s establish some key facts: although one advantage of AM is that metal powder can be recycled for the next production, it should be noted that recyclability depends on the type of material that is utilized.
From a manufacturing standpoint, most productions reveal that only a small amount of the powder that flows into the build chamber is melted into a component which means an important quantity of powder can be reused or scrapped.
From a cost perspective, it can bring a wide range of benefits including profitability to recover and reuse the unmelted powder. Indeed, an operator who does not reuse the powder, will throw it away and will add this loss to the overall cost of the part that has been produced (and this will remain one of the reasons why metal 3D printed parts are said to be very expensive). This means that recycling the powder helps manage powder stock, and decrease the global cost per part.
From a sustainability point of view, using the same feedstock enables to maximize its output and avoid unnecessary scrap that can also be very costly to dispose of.
Andreas Hartmann, cofounder and CTO at Solukon Maschinenbau GmbH highlights each of these perspectives by laying emphasis on where powder recovery should take place:
“Firstly, taking into account the printing process itself. Only a small amount of the total amount of powder is actually fused into a component. The rest of the powder either remains in the chamber or is trapped in cavities or internal channels of the printed part – potentially reusable powder in both cases. Not recovering this powder would mean to dispose of a huge amount of powder which hasn’t been used for printing at all.
This way, powder recovery follows the fundamental idea of sustainability, i.e., the avoidance of the depletion of natural resources.
Secondly, resources are finite, this also applies to metal powder. It therefore is crucial to recover and recycle the metal powders in order to guarantee sustainability in additive manufacturing as far as possible.
The level of sustainability regarding powder recovery is heavily dependent on the industry and the application. There are industries where powder recycling is not possible (due to certifications). For these industries in particular, comprehensive concepts for proper disposal or downcycling of powder should be developed. Regarding down cycling, perhaps it is possible to use the powder for components that do not need to be certified (training components, prototypes, etc.).”
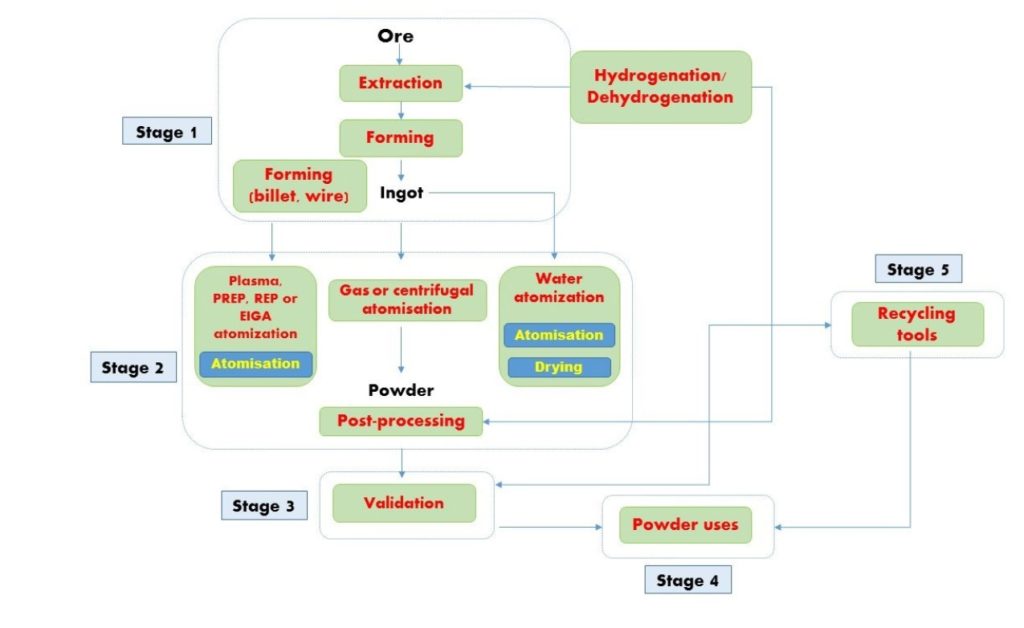
What we understand from Hartmann’s statement regarding sustainability is that not only may it raise several questions throughout the lifecycle of specific products, but it also requires to understand metal powder production lifecycle. The latter might include extraction to form a pure or alloyed metal product, some specific additional processing steps for appropriate powder production and analysis of powder specificity during production or even validation for customised metal 3D printing equipment producers.
In other terms, this means taking into account water atomisation, gas atomisation, plasma atomisation, the plasma rotating electrode process, and centrifugal atomisation or hydride– dehydride process.
Depending on your situation, each of these steps will not necessarily be the most important to focus on. Indeed, if you are a materials producer that uses scrap to produce powder, you will mostly focus on atomisation – not to mention that, sometimes, material producers have their proprietary technology which lays emphasis on other aspects of production. However, if you are a parts manufacturer, your most important step should probably be to focus on post-processing.
Powder recovery: the “How” & the “What”
How do we effectively recover powder? What impact can the recovery process & recovered powder have on other stages of manufacturing?
At this level, the considerations (the “What”) that need to be taken into account should justify the choice of powder recovery process leveraged to recycle materials.
First and foremost, one thing manufacturers should always keep in mind is that every material ages differently therefore their characteristics are likely to change during manufacturing, recovery and reuse. Also, it becomes pivotal to trace the evolution of powder characteristics at various stages of recycling to produce parts with consistent properties.
According to Solukon’s CEO, to minimize the risks of having a material whose characteristics will be different from the raw material, operators should focus on aspects that may influence these characteristics during the powder recovery process:
“For trouble-free reuse the powder must inevitably be free of any contamination to minimize obstacles in subsequent printing processes. A clean environment for powder recovery therefore is mandatory. To improve the quality of the recovered powder a safety gas atmosphere is beneficial. Flowability of the powder is increased while humidity decreases – both mandatory for subsequent printing processes with reused powder.
In addition, when using reactive materials an inert atmosphere is mandatory to avoid the risk of explosions.
Another effect to be prevented is the so called “aging of powder“. Due to interaction with the surrounding atmosphere, the un-melted metal powder ages gradually which means the quality of the powder is reduced due to oxygen absorption. Correspondingly, the surface morphology and chemistry, the shape and size distribution as well as the flowability of the particles are modified. The aged powders may affect the final properties of the printed component negatively, making the number of times that metal powder can be cycled limited”.
All of these aspects provide a holistic approach to AM production, where process steps merge directly into one another. For Solukon, these steps consist in applying a secured unpacking stage, a depowdering stage as well as a post-processing stage.
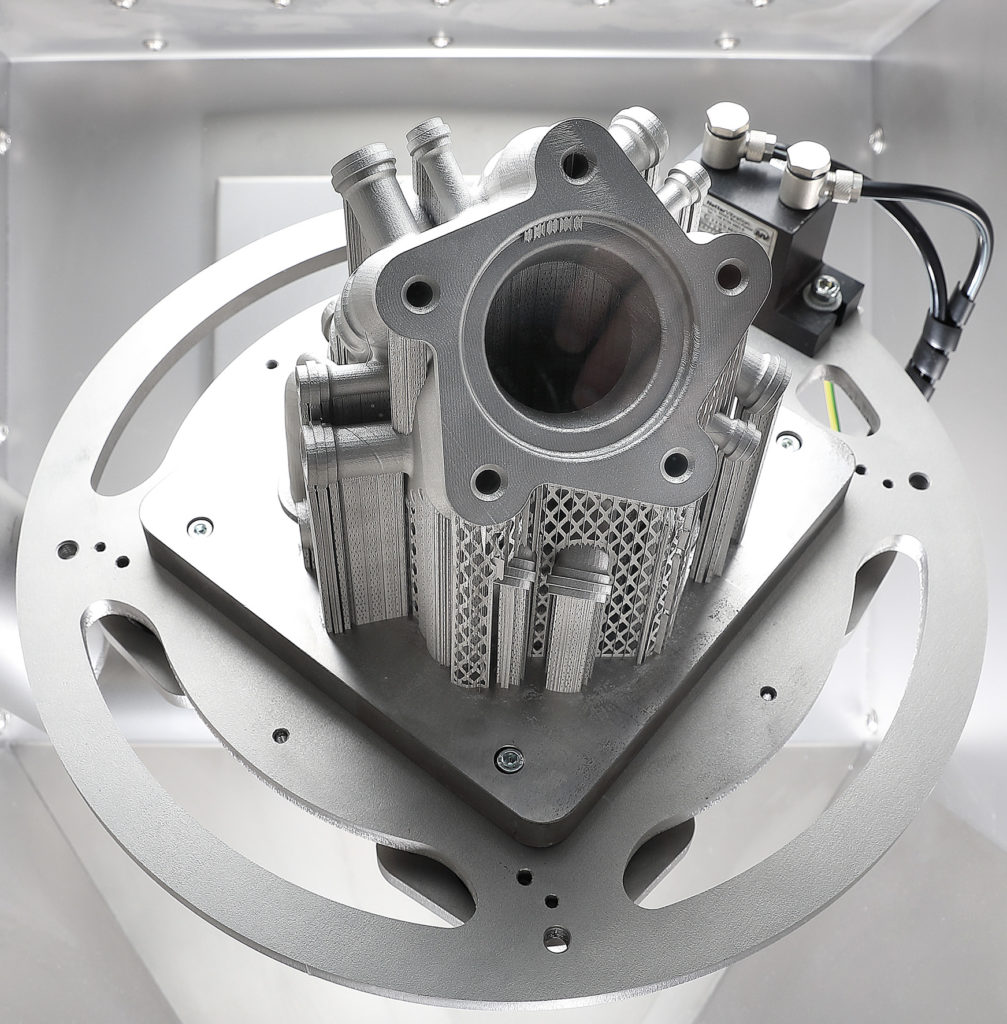
For the company, the powder recycling process should be designed as follows:
“ – Depowdering: After unpacking the parts in the 3D printer, the depowdering station removes critical powder residues from the parts in a protected atmosphere and collects them contamination-free in the chamber bottom.
– Sifting: The powder residue can then be fed to the powder-recycling unit. There it is sieved and refreshed with fresh powder.
– Reuse of powder: the powder is now ready for further printing processes.”
While an automated powder recycling process suggests that the reused powder after reconditioning (sieving process) may have similar characteristics than the raw metal powder, it should be noted that these characteristics may vary from one specific metal AM process to another. In this vein, an operator who uses metal AM machines with a vacuum cleaner for instance, might obtain a material with different properties.
Moreover, AM machines such as the one from Renishaw that integrate an internal sieve have dedicated reuse methods.

Furthermore, in order to know if reusing the unfused powder or if the recovery process is worthy for a specific project, operators should also take into account production and purchase considerations.
Evonik raises our attention on the fact that the number of times one can reuse a powder “depends on the parts and the build job. Ideally [operators] should be able to work with a fix old/new ratio without any scrap.” The fact is, once the criteria that the parts need to meet have been defined, some operators often find if more affordable to purchase powders close to the production specifications. In this case, the number of reuse cycles will also be limited as the powder can degrade only so much before it is out of use. Not to mention that, the property requirements of the component to be printed will determine how much the operator will monitor the powder or how many times it can be reused.
As for the viability of the powder, sometimes, recovery and reuse might result in a refined particle size distribution, but with marginal change in powder morphology. Other times, “viscosity has to be measured” – as is the case with polymer powders. “Depending on the result the old/new ratio has to be adjusted”, Evonik told us.
The sustainability perspective
“How sustainable is powder recovery process in AM?” Reality shows that powder recovery has a proven record in terms of overall costs of production parts, and reuse of powders. Unlike ten years ago, the current AM market is filled with automated post-processing solutions that can facilitate this process. “Solukon depowdering systems for instance, usually recollect up to 100 % of the powder, contamination free and in a protected atmosphere”, the company notes. But is it enough? As Hartmann continues, it “is the door-opener for a reasonable approach to sustainability in the first place.”
We couldn’t agree more with him but there should be more as the industry is continuously seeking for key data that may help them understand the lifecycle sustainability in Metal AM processes, post-processing processes and materials production processes, key data that are based on demonstrative methods of lifecycle assessment (LCA), and databased inventories.
We have to admit that at the moment, very few resources are available to sustain these. “With rising serial production, the need for sustainability will grow not only for ethical recycling reasons but also with regard to costly disposal of the powder”, the CEO ensures.
In the meantime, what should we do?
This exclusive feature has first been published in the 2021 September/October edition of 3D ADEPT Mag.