Interview exclusive sponsorisée par le Military Additive Manufacturing Summit.
Croyez-vous que la nécessité est la mère de l’invention ? Je le crois, et aujourd’hui, je pense que ce dicton n’a jamais été aussi vrai que dans le secteur militaire. Il est embarrassant (pour moi), qu’il ait fallu une conversation avec John Harrison, Directeur de la Fabrication Additive pour réaliser que les premières applications de fabrication additive qui ont été commercialisées dans cette industrie, résultent probablement de solutions déployées dans le jardin secret innovant des experts militaires.
Si de nombreuses technologies conçues à des fins militaires ont trouvé leur place sur les marchés industriels, n’oublions pas que le passage d’une technologie du secteur de la défense aux marchés commerciaux et vice-versa est souvent difficile, et c’est certainement la raison d’être d’entreprises comme Phillips Corporation.
J’avais l’habitude de définir l’équipe de Phillips Corporation comme les médiateurs idéaux entre les fabricants de technologies de FA et le ministère de la défense, mais ils sont bien plus que cela. L’entreprise est reconnue pour sa gamme complète d’équipements et de services de fabrication qu’elle fournit à diverses industries, équipements et services qui englobent les outils d’automatisation et de robotique, la maintenance préventive, la formation, ainsi que la fabrication additive pour n’en citer que quelques-uns. En un mot, des solutions qui peuvent propulser les capacités, la rentabilité et la productivité.
Alors que cela fait six décennies que le gouvernement fédéral, l’industrie du secteur privé et les acteurs de l’éducation s’appuient sur les solutions de fabrication de Phillips, il convient de noter que l’entreprise a commencé son voyage dans la FA il y a environ 16 ans.
« L’une de nos premières applications était à l’hôpital Walter Reid, où les médecins faisaient pousser des plaques crâniennes à utiliser sur les soldats blessés à la tête. Phillips a développé ses partenariats pour s’assurer de pouvoir répondre pleinement aux besoins de ses clients. Dans le domaine de la fusion sur lit de poudre, nous sommes partenaires d’EOS. Notre partenaire en matière de filaments fondus est Markforged, et pour la réparation par projection à froid, nous travaillons avec VRC Systems. Spee3D est un partenaire qui a développé une excellente unité déployable sur le terrain. Haas et Sodick fournissent des solutions pour le post-traitement », indique d’emblée Harrison.
En outre, dans ce secteur, l'entreprise ne se contente pas de fournir des équipements de fabrication tiers, elle produit également des pièces et développe en interne une machine hybride qui apporte des avantages essentiels au département de la défense américaine (DoD = Department of Defense).
« Pourquoi ce focus sur le département de la défense ? »
Plusieurs raisons peuvent expliquer cet intérêt croissant pour les solutions de FA déployées par et pour le DoD. L’une d’entre elles est le fait que le ministère américain de la Défense (DoD) a publié sa toute première stratégie globale de fabrication additive (FA) en janvier 2021. Cette stratégie ne démontre pas seulement une vision commune de l’utilisation de la fabrication additive dans le cadre du programme de défense de la nation, elle révèle également certaines des pierres angulaires qui nécessiteront une attention particulière de la part de toutes les parties prenantes.
Ces pierres angulaires comprennent, entre autres, un meilleur développement des guides de qualification et de certification, un échange transparent d’idées pour favoriser l’innovation, les nouvelles conceptions et la fourniture d’une capacité rapide ; le développement d’une main-d’œuvre de praticiens, de concepteurs, de techniciens et d’acquisition, ou encore l’établissement d’une orientation vers leurs sources expéditionnaires et de point de besoin.
Focus sur les besoins de la fabrication expéditionnaire
Cette dernière pierre angulaire sur l’orientation des sources expéditionnaires et de point de besoin est devenue d’une importance capitale pour le DoD. La vérité est que l’armée de terre est confrontée à des défis permanents en matière de disponibilité opérationnelle en raison de l’obsolescence des pièces et de l’incapacité à obtenir rapidement des pièces de rechange pour les systèmes vieillissants. En fait, certains systèmes sur le terrain ont un délai d’approvisionnement moyen de 22 jours (CONUS à OCONUS = Continental U.S. à Outside the continental U.S.), d’où l’utilisation de la fabrication additive qui permet de fabriquer des pièces directement à partir d’un fichier numérique, à la demande et au point de besoin.
Harrison explique que le meilleur exemple de cette fabrication expéditionnaire est l’industrie spatiale, où les ingénieurs sur terre peuvent rapidement concevoir des modèles et envoyer les fichiers numériques à leurs collègues dans des « environnements austères » afin qu’ils puissent imprimer les pièces manquantes. Toutefois, il rappelle également la première expérience de Phillips dans de tels contextes :
« Notre première expérience a eu lieu lorsqu’un Sergent d’artillerie des Marines est rentré de la guerre en Irak. Son équipe avait été chargée de renforcer l’armement des Humvees sur le terrain, mais elle ne disposait pas de l’équipement adéquat pour accomplir la mission. Les Marines connaissaient bien les machines Haas, alors nous avons adapté une fraiseuse et un tour Haas pour qu’ils tiennent dans un conteneur d’expédition. C’est ce qu’on a appelé plus tard le Shop Equipment, Machine Shop (SEMS). Nous avons conclu un accord CRADA avec l’armée de terre pour comprendre les besoins expéditionnaires du combattant et nous avons travaillé avec elle pour développer le prototype de l’ensemble d’atelier d’usinage des métaux (MWMSS = Metal Working Machine Shop Set). Cette unité a amélioré la conception de la Marine et comprenait un montage sur amortisseurs, un manuel d’utilisation complet et des modifications spéciales de la hauteur. Le MWMSS est devenu un programme de référence, Rock Island Arsenal recevant des machines Haas modifiées de Phillips et les incorporant dans l’unité expéditionnaire. Phillips, en collaboration avec Omax, a développé une unité de jet d’eau déployable qui a été utilisée par les Marines à Camp Leatherneck. Phillips a également soutenu RFAST, un programme qui a amené des ingénieurs et du matériel sur la base aérienne de Bagram pour soutenir les innovations rapides en matière de matériel sur le champ de bataille. Plus récemment, Phillips a construit un prototype qui incorpore une tête de dépôt à énergie directe alimentée par fil sur une fraiseuse Haas. Nous pensons que cela donnera au combattant plus de capacités pour réparer l’équipement sur le terrain ».
L’exemple de Harrison met en lumière la nécessité de prendre en compte certains aspects logistiques tels que les matériaux, les machines et le personnel. Plus important encore, il met en évidence la rapidité avec laquelle l’ensemble du processus doit être mis en œuvre pour répondre à un besoin urgent, ce qui devient encore plus intéressant lorsqu’on sait que certaines technologies de FA ne sont idéales que dans des environnements de recherche, et ne sont donc pas assez robustes pour répondre au besoin d’une utilisation expéditionnaire.
« Même si notre travail sur les équipements sur le terrain est important, la véritable innovation est réalisée par le combattant. Les soldats américains sur le terrain, équipés des meilleures ressources de fabrication, feront pencher le champ de bataille en notre faveur. Ils utilisent leurs compétences pour trouver des solutions à la volée. J’ai entendu parler d’exemples de la façon dont les soldats ont fabriqué des composants pour remettre les équipements en état de marche, ont amélioré la conception des équipements pour améliorer la préparation, et ont même inventé de nouvelles solutions pour protéger le combattant. Les grands esprits du ministère de la Défense imaginent de nouvelles possibilités grâce aux capacités de fabrication déployables », poursuit-il.
Le problème, c’est que la route est encore longue, car plusieurs questions doivent encore être abordées : et si la fabrication expéditionnaire était suffisamment flexible pour réduire la montagne de fer de 20 % ? Pourquoi pas de 50 % ? Et si la nouvelle technologie expéditionnaire permettait de créer des drones capables de voler à partir de l’imprimante ? Et si la technologie additive pouvait fournir des soins médicaux personnalisés aux soldats blessés ?
Au niveau de la recherche, certaines de ces questions sont actuellement explorées. Elles incluent par exemple la capacité d’imprimer de la peau pour guérir des blessures, ou des drones imprimés en 3D pour les soldats, mais une question reste sans réponse : comment tout cela se passe-t-il sur le terrain ?
Quelles technologies sont déployées sur le terrain ? Et surtout, qu’est-ce que cela implique ?
Ces derniers mois ont vu le développement de solutions de fabrication in situ telles que les concepts d' »usine d’impression 3D portable » ou d' »usine intelligente mobile ». Ces solutions sont certainement très utiles, mais Harrison souligne « qu’il existe de nombreuses pièces qui peuvent être fabriquées sur le terrain et qui ne nécessitent pas de contrôle in-situ. À mesure que la technologie sera mieux acceptée, des pièces critiques pour le vol et la sécurité seront fabriquées. Ces pièces devront être contrôlées et certifiées avant d’être utilisées. La fabrication au plus près du point de besoin est l’avenir. Je pense qu’il y aura des solutions additives à chaque niveau de soutien, des installations de réparation CONUS (Continental U.S.) aux bases intermédiaires et de transit OCONUS (Outside the continental U.S.), en passant par les bases d’opérations avancées, ou « impression dans la poussière ». Ce qui variera, c’est la distance à laquelle la technologie additive peut être déployée. Certaines technologies nécessitent une meilleure alimentation, de grands volumes de gaz d’assistance, des environnements cohérents, etc. Nos partenaires l’ont reconnu et ont créé des machines conçues pour les expéditions : Markforged, par exemple, a créé un X7 déployable sur le terrain qui est utilisé par les Marines et testé par la Marine. De son côté, Spee3D a réalisé des essais sur le terrain avec l’armée australienne. »
Il va sans dire que des technologies autres que la FA métal peuvent être envisagées pour des applications militaires. Le fait est que le choix d’une autre technologie – l’impression 3D polymère par exemple – recentre le débat sur l’identification/sélection des pièces.
« Il y a des centaines de milliers de pièces dans la chaîne d’approvisionnement, les filtrer rapidement pour déterminer quelles pièces peuvent être imprimées (selon les besoins du DOD) est important. Nous sommes très intéressés par les plastiques déployables qui sont durables », note notre invité.
Si les matériaux renforcés de fibres de carbone et de Kevlar de Markforged méritent d’être cités en exemple, la réalité est que les technologies évoluent vers des logiciels basés sur le cloud. L’énergie disponible, les services publics, la taille des équipements, la capacité de survie, la facilité d’entretien, la formation et l’outillage sont autant d’éléments clés qui doivent être repensés pour que les soldats puissent s’adapter facilement à chaque situation. Pour répondre à cette flexibilité, Philipps Corporation a développé la machine hybride Phillips en tenant compte de toutes ces variables.
Un regard sur la machine hybride Phillips
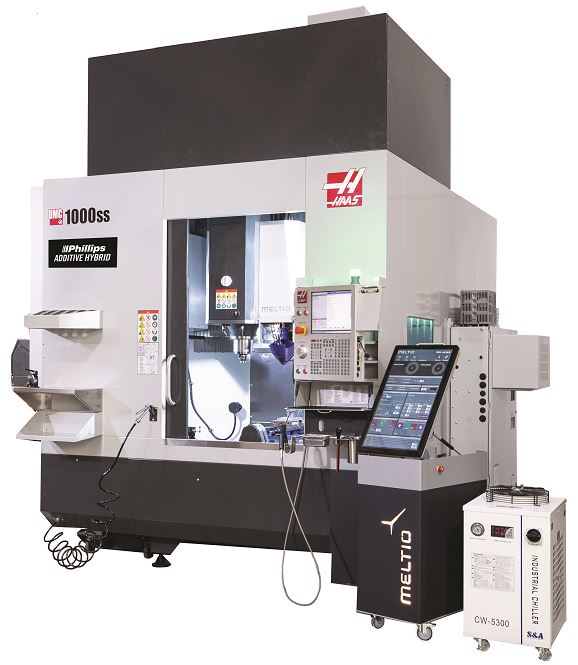
Pour un processus de fabrication considéré comme le meilleur des deux mondes, l’équipe de Phillips a combiné deux solutions technologiques pour développer la Phillips Additive HybridTM : une technologie de dépôt de métal par laser de Meltio et la fraiseuse CNC de Haas.
Dossier : Les fabricants peuvent-ils parier sur les technologies de fabrication hybrides ?
Pour l’équipe, l’intégration d’une tête laser DED à fil sur la machine Haas est parfaitement adaptée à la réparation et aux autres applications de fabrication. De plus, non seulement la machine peut traiter différents matériaux additifs sur la même pièce, ce qui permet d’obtenir une conception précise, ainsi qu’un poids et une résistance idéaux, mais elle peut également imprimer en 3D une forme presque nette et réaliser l’usinage en une seule configuration de pièce. En outre, les explications d’Harrison révèlent également que la machine permet la fabrication de pièces à haute densité dans un environnement de travail propre avec le fil laser DED et qu’elle est compatible avec les logiciels de programmation hors ligne tels qu’Autodesk, GibbsCAM et Mastercam.
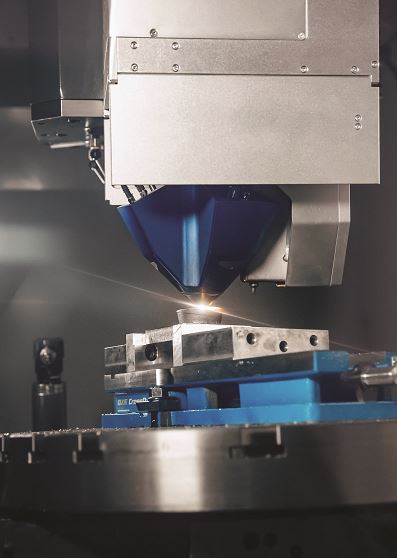
« Nous avons fait beaucoup de recherches. Nous aimons le matériau filaire pour le processus, car il est très propre et stable lorsque le matériau est stocké. La technologie que nous avons choisie ne nécessite pas d’environnement inerte et minimise les gaz de protection. La réponse à l’offre initiale a été très bonne. Nous avons expédié un grand modèle à 5 axes à une société de logiciels à des fins de développement. Nous avons également obtenu un contrat avec la Marine pour un prototype de bord. L’armée nous a également confié un contrat pour le développement d’une solution permettant d’adapter la tête hybride à la plate-forme MWMSS. Outre les applications DOD, l’intérêt pour l’industrie commerciale est fort. Je pense que la raison en est que nous combinons la bonne technologie additive avec la fraiseuse CNC la plus populaire aux États-Unis », souligne le président de la Division fédérale.
Quelle sera la prochaine étape ?
La fabrication expéditionnaire est l’un des sujets clés qui suscitent actuellement l’intérêt du ministère de la Défense, dont l’objectif ultime est de moderniser les systèmes de défense nationale en améliorant les performances à l’aide d’équipements conçus avec la FA ; d’accroître la disponibilité du matériel pour prototyper et produire rapidement des pièces directes, ainsi que de permettre aux combattants d’utiliser des solutions innovantes sur le champ de bataille.
Cette conversation avec John Harrison révèle certaines des contraintes auxquelles le DoD pourrait être confronté pour répondre à ces préoccupations, et met en lumière d’autre part les solutions existantes pour permettre la fabrication expéditionnaire. Harrison rappelle toutefois qu’il ne s’agit pas ici de remplacer les procédés de fabrication conventionnelle par les technologies de fabrication additive, mais bien d’utiliser des solutions pratiques où c’est absolument nécessaire, pour agir plus vite et plus efficacement sur le terrain. En ce sens, on gardera dans notre radar le travail actuel de SPEE3D avec l’armée australienne qui pourra déboucher sur des solutions technologiques commercialisables sur d’autres marchés.
Une chose est sûre, d’autres solutions seront déployées, plusieurs applications seront réalisées, mais le « secret défense » nous fera certainement attendre plusieurs années avant de les voir arriver sur le marché commercial. En attendant, l’une des options dont nous disposons pour savoir tout ce qui se passe à l’intérieur par des initiés, est de participer à des événements dédiés comme le Military Additive Manufacturing Summit.
Contenu exclusif créé en partenariat avec le Defense Strategies Institute.
N’oubliez pas que vous pouvez poster gratuitement les offres d’emploi de l’industrie de la FA sur 3D ADEPT Media ou rechercher un emploi via notre tableau d’offres d’emploi. N’hésitez pas à nous suivre sur nos réseaux sociaux et à vous inscrire à notre newsletter hebdomadaire : Facebook, Twitter, LinkedIn & Instagram !