Remember when we told you that post-processing is an umbrella term that covers a variety of stages that 3D printed parts have to undergo before being used for the final purpose? With the goal of providing a thorough understanding of each post-processing task, we have started sharing key insights into issues raised by metal powder removal, the use of furnaces in Additive Manufacturing, or even the Automated Dyeing Process For 3D Printed Parts. In this article, we will have a look at the best practices and tips to know when conducting a surface treatment method in metal 3D printing.
The theory is that, in AM, engineers can benefit from freedom of design to create complex shapes but practice reveals design constraints which show that the geometry you print will not be the same as your 3D model.
Several causes may explain that:
- During the export of your print file for instance, 3D model’s edges, contours, curved surfaces and more are approximated by triangles in a process called tessellation. When this happens, the forms of the circles are no longer perfect. They become approximations formed by a series of straight lines;
- Despite the optimization of the build direction, the layer-by-layer fabrication mode of AM can still be tricky for slanted surfaces, curved shapes, or holes; and provide a “staircase” effect;
- Other manufacturing and design challenges can be related to the geometry of the 3D model, the quality of the metal powder or the build orientation. They may affect the dimensions and tolerances of your final 3D printed part.
These issues may be some of the reasons why operators decide to conduct a surface treatment process; so that in the end, they could improve the appearance of their component, enhance their durability or the ability of the part to better withstand wear, corrosion, heat or other elements, smooth out uneven surfaces or improve its electrical conductivity.
This feature will provide a closer look at surface treatment methods operators can conduct for metal 3D printed parts. To discuss this topic, we have invited key contributors from two companies: Jan Panhuis, Senior technical commercial advisor at Leering Hengelo (Normfinish) as well as Paul Gagorik, Solution Architect and Behrang Poorganji, VP Material Technology from Morf3D.
In case you are not familiar with these companies, please note that, Normfinish (known as Leering Hengelo in the Benelux region), has been operating in the world of blasting and surface technology since 1980. The company provides a wide range of products and services for operations related to fine blasting, polishing, matting, finishing, deburring, surface roughing, cleaning of surfaces such as rust (oxides) and coating, as well as shot peening.
Morf3D on the other hand, brings a user experience around this “table”. The company leverages an unmatched experience to deliver AM serial production to aerospace companies. As a parts producer, Morf3D leverages its in-house post-processing capabilities to achieve fully optimized functional structures and build processes for top-tier aerospace clients. Once a build is removed from the build chamber, the Morf3D team can conduct a wide range of post-processing steps. They include for instance, depowdering, NDI (X-RAY, CT Scan), Heat Treatment (Stress Relieve, HIP, Solution, Age, Quench), removal of substrate (build plate), support removal, CNC Machining, surface treatment (Media Blast, Ultrasonic Cleaning, Electropolish, Pickling, Passivation, Coatings, Paint), Assembly/Installation as well as Digital Data Package/Certification. Gagorik and Poorganji will focus here on surface treatment methods.
We also thank machine manufacturer 3DEO, online manufacturing platform Factorem and SPC – Surface Treatment Experts for the resources shared.
Justifying the importance of surface treatment methods
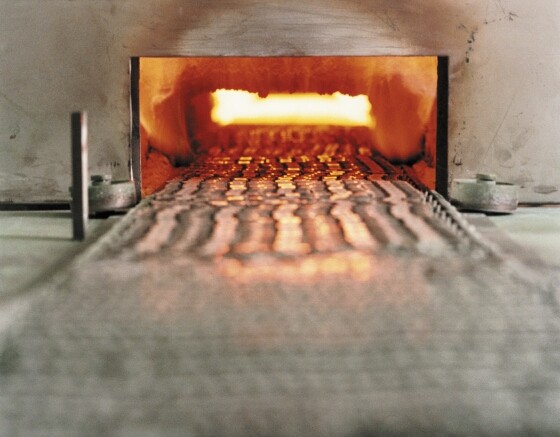
Categories of surface treatment methods are not standardized. Therefore, their listing often varies from one organization to another; or it depends on the type of “aesthetic, feel or part properties” they deliver to parts. Soo far, we have identified:
- The finishing methods that include hand polishing, sandblasting or numerical control grinding. The “Mechanical finishes” category that includes sanding, ultrasonic polishing¸ rumbling and tumbling, magnetic polishing, lapping, filing or vapour smoothing.
- Coatings, which can include anodization, powder coating, painting or plating.
- The “undefined cutting edge finish” category that includes abrasive blasting, and vibratory finishing
- The “electric power finish” category which involves electropolishing;
- Solidification by plastic deformation: Shot peening
According to Panhuis, no matter what surface treatment option you choose, the most important issues to address concern the “dimensions of the part, the desired roughness, the optical requirements, the type of treatment (is it a manual or an automatic treatment?)”. Needless to say, the type of parts you process can also play a key role in the surface treatment option you will choose. A medical 3D printed part made in Titanium will not be post-processed as another one made in steel. A medical 3D printed part may only be blasted while a steel part, depending on its mechanical characteristics and the final purpose, can be painted, plated, or filed. “For some parts again, we need to check the allowed amount of contamination with blasting media”, Panhuis adds.
Gagorik and Poorganji go further as they take into account the complexity of the part, its performance but also all the steps that may influence its final cost. They draw attention on the fact that “the ability to correctly/thoroughly apply a treatment to all intended surfaces, can be impeded by increasing the complexity of part design”. Key contributors in this case, include cleanliness, surface topology, and accessibility. “One important concern is how surface requirements in 3D printed part relates to materials property (For example HCF, LCF, Corrosion) and overall part performance. This is critical as dictates what surface finish treatment and metrics need to be achieved for each part CTQs*. This will eventually drive the cost and viability of AM process”, the experts explain.
*CTQ = Critical to Quality specifications
A closer look at surface treatment methods
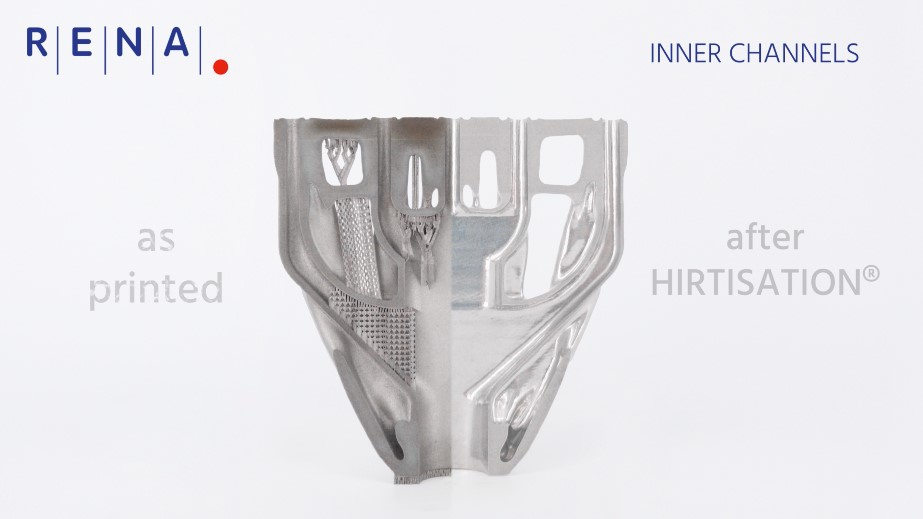
While many of the same reasons for conducting a surface finish option apply to both 3D-printed parts and parts fabricated via conventional manufacturing processes, the first features to consider when choosing a surface finish method are the part’s ones.
“It should be driven greatly by the intended operating environment (assembly/installation, operation/performance, maintenance, decommission) of the part. It should not be driven solely by existing standards, specifications, “best-practices”, etc.. – as all these approaches were created with specific assumptions/conditions that may not apply in all cases. Significant savings (in downstream lead-time and cost) can be realized when taking necessary time to interrogate your application before you design/define. The surface treatment is typically determined by the part CTQs, dimensional requirements, and heavily depends on the AM process (Modality)”, the Morf3D experts lay emphasis on.
That being said, let’s have a look at some of these methods – irrespective of their main category:
- Sanding is one of the most widely known surface treatment methods. It consists in rubbing abrasive particles on the surface of a work-piece creating random, non-linear surface texture. In other terms, a rough material such as sandpaper can be used to smooth out and remove small imperfections from a surface. Sanding is most useful when applied to curved or contoured surfaces. However, experts doubt its efficiency when it comes to tight corners.
- Ultrasonic Polishing on the other hand is ideal for internal finishing of tight corners, holes or pockets that can be quite difficult to access. In this method, a soft, fine tipped tool mounted onto an ultrasonic spindle vibrates at 30 kHz which, in combination with an abrasive slurry, induces a pressure wave that safely works away at the surface to create a fine polish. What’s interesting about this process is that the tip of the tool is not in contact with the work face. It works well on hardened steel, and there is little chance to cause damage to the part.
- The polishing options also include laser polishing where a high-energy laser beam melts the surface material of parts again to reduce the surface roughness. In theory, this method can deliver a surface roughness of 2~3μm (Ra). In practice, the high cost of laser polishing equipment slows down the adoption of this technique in AM post-treatment processes.
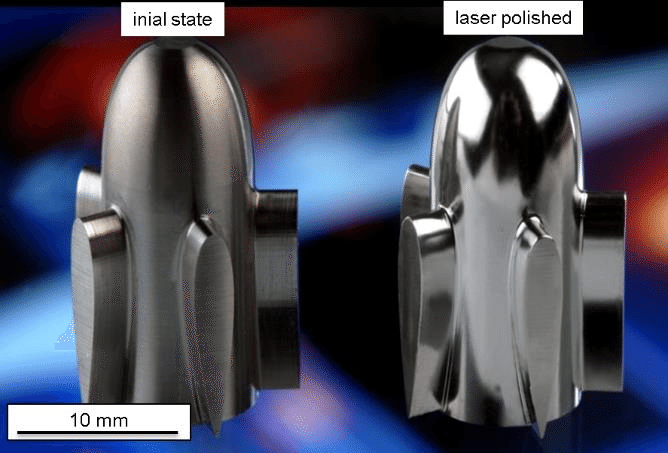
- Chemical polishing can also reduce the surface roughness of a given part to 0.2~1μm.
- Rumbling and tumbling are similar to sanding to the extent that abrasive particles are used to modify the surface roughness of the 3D printed part. According to SPC, tumbling is similar to vibration, but it rotates the components and the polishing medium around in a drum rather than vibrating them. This is a gentler movement, which makes tumbling better for more delicate parts and those with fine details. The unit used is often called a centrifugal barrel system.
- Intended for increasing the strength and durability of a part, shot peening consists in the use of pressurized air shoots tiny metal or plastic beads at a surface at high speeds.
- The shot peening process is very similar to bead blasting. This process makes it easy to reach the insides of channels and other tricky spots. The operator uses here a spray gun to shoot finely reground thermoplastics at the surface, removing therefore imperfections and smoothing out the surface.
- In the method of sandblasting, the operator blasts the part’s surface with abrasive particles under high pressure. Those abrasive particles can be used in combination with air and water, and cover a large surface area fairly quickly. Different levels of surface finish can be achieved by using varying types of abrasive media. Depending on the use case, the operator can enhance the mechanical properties of metal by increasing its fatigue strength and improving corrosion resistance through shot-peening.
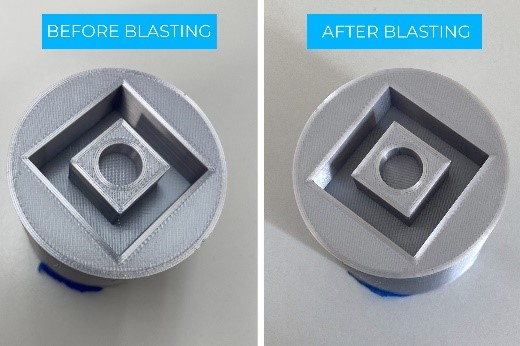
- Vibratory Finish is a machining process with an undefined cutting edge. The goal is to improve surface quality of small parts. This is done by rounding edges, smoothing processes, and grinding.
- Plating consists in coating steel with a small layer of an inert material. It enables protection from corrosion and oxidation of the base part. Despite these advantages, it should be noted that the part can be damaged by impact, wear and other external factors.
A surface treatment method can be conducted after the part has cooled down and is free from powder. However, as you may guess, the advantages of a surface treatment method can compensate for the disadvantages that another many cause to the part. That’s why, Gagorik and Poorganji said the appropriate order of the post-processing steps depends on the requirements of the final configuration of a given part.
“Surface Preparation processes (including Ultrasonic Cleaning, Abrasive Flow, Electro-polishing, Chemical Milling) typically happen prior to any surface Coatings (including Anodize, Metallic/Ceramic, Paint), and can sometimes be required (as cleaning operations) prior to Heat Treatments and Assembly processes as well. Usually, the surface finishing is coming at the later / final stages of the post processing. However, the sequences of the process is designed in a way to maximize the performance and minimize the cost”, the experts point out.
One key consideration at the heart of surface treatment methods: surface roughness
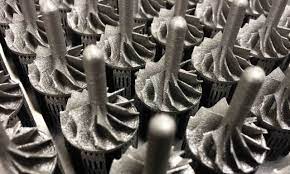
Experts have made it clear that all aspects of the 3D printed part, such as the material, shape, thickness, and weight, its planned use, and the environment in which it will be used, count when it comes to choosing a surface finish option. However, beyond all these aspects, a key emphasis has been made on “the surface roughness problem” of additive manufactured parts.
“Surface roughness is a measure of the variance in a part’s surface topology. Roughness can affect part aesthetics (e.g. shiny or maNe) and mechanical behaviour like crack initiation, wear resistance, fatigue life, marine, sealing, bearing, and fluid dynamics. The rougher the surfaces in an integrated dynamic machine, the less quietly, efficiently, and safely it will operate. Reducing roughness, or friction, is critical in mechanical parts like pistons, bearings, and seal surfaces where too much contact between moving surfaces can lead to rapid wear and tear. Specifications may differ by case, but the smoothness required of an end-use part can be an important factor in costing it. Surface roughness analysis includes the use of parameters to inspect and determine whether the part manufactured meets quality control standards. This helps manufacturers and designers quantify the roughness of the surface finish they select” Matt Sand, Founder & CEO at 3DEO, comments.
This explanation implies another one: surface condition can vary significantly by 3D printing process [even within the same process, but with different process parameters]. Therefore, we can’t legitimately say certain surface treatment options work well with certain metal 3D printing processes.
For Morf3D, it is essential to understand the starting conditions for acceptable application of the surface treatment needed for the given material and part application, and then determine what manufacturing processes are necessary to get you there. Taking the example of their in-house capabilities, Gagorik and Poorganji note that the surface treatments they are using today, are the advanced/developed version of the existing processes for conventional processes which are modified or geared towards the needs of 3D printed parts. For example, access to internal channels which are rougher than a machined channel, or chemical-mechanical polishing of a rotating component surface.
Lastly, the reasons for using a surface finish apply both to 3D printed parts and parts manufactured with traditional processes. Since different finishing options come with different costs, responsibility, as per the words of Morf3D’s experts, lies not on the technology used to manufacture, but on informed design and manufacturing teams in collaborating to make the best decisions on what to use.
This exclusive dossier has first been published in the 2022 January/February issue of 3D ADEPT Mag.
Remember, you can post job opportunities in the AM Industry on 3D ADEPT Media free of charge or look for a job via our job board. Make sure to follow us on our social networks and subscribe to our weekly newsletter : Facebook, Twitter, LinkedIn & Instagram ! If you want to be featured in the next issue of our digital magazine or if you hear a story that needs to be heard, make sure to send it to contact@3dadept.com