The 2021 edition of Formnext marks the seventh year of the International Gathering of the world of Additive Manufacturing in Frankfurt, Germany. Held every year during the second or the third week of November – with one skipped year in 2020 – Formnext has made it a priority to feature a series of world premieres throughout the entire process chain and to demonstrate the ever-growing fields of application of Additive Manufacturing.
This 2021 in-person edition of Formnext, held from November 16th to 19th, was long-awaited and has been organized with all the uncertainty surrounding the Covid-19 landscape – the uncertainty of being cancelled at the last minute. The event finally took place under the highest ‘2G’ safety conditions, meaning that only those fully vaccinated against or recovered from COVID-19 were allowed to attend.
Most importantly, this edition was long-awaited as the entire industry came to realize that virtual events are not enough to do business.
That’s the reason why, one of the first highlights of this edition was “People”.
People: “See and Be Seen”
With over 600 exhibitors from 36 countries, covering a total floor space of 30,000 square meters, Formnext 2021 welcomed 17,859 specialists and executives from 76 nations.
This number is perhaps equivalent to half of the visitors who attended the show in 2019, but this remains one of the highest levels of attendance observed in AM-dedicated industry events. As a matter of fact, most exhibitors told 3D ADEPT Media, that they didn’t expect to have such a crowd giving the increasing number of Covid-19 cases in Germany.
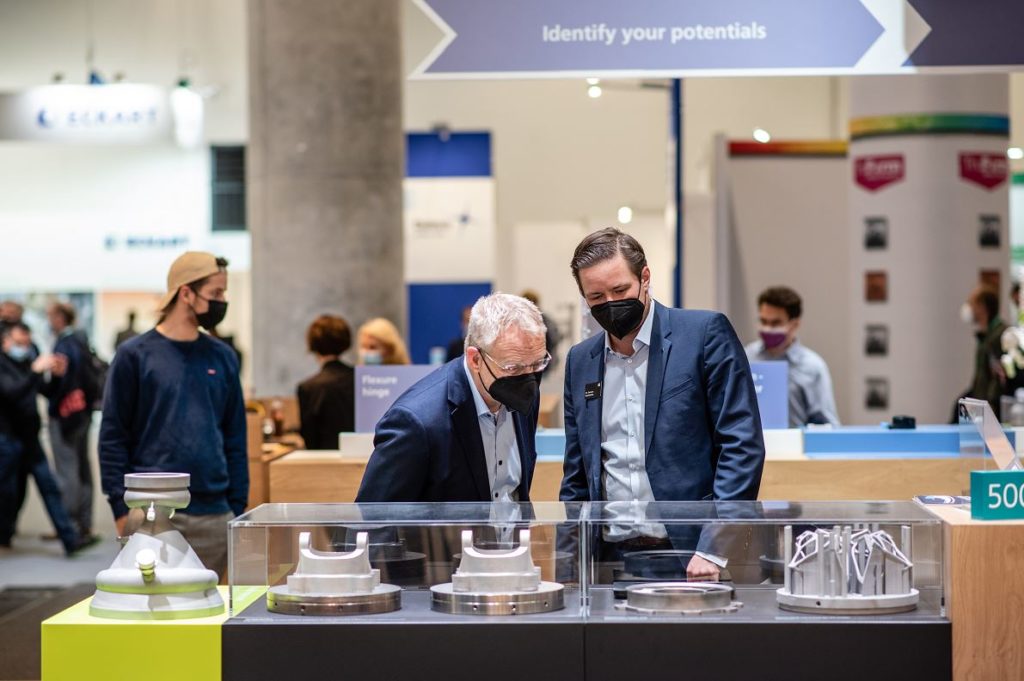
“Formnext has once again shown itself to be the highlight of the year for the AM industry. After the significant challenges we faced last year, this year both the number of exhibitors and visitors in attendance surpassed our expectations,” commented Sascha F. Wenzler, Formnext Vice President at organizer Mesago Messe Frankfurt GmbH. “It has shown once again just how important Formnext and face-to-face meetings are for this innovative industry, which develops technologies at a rapid pace and is keen to share these with investors, partners, and customers. It was clear that Formnext had been eagerly awaited by the entire industry.”
While this reemphasizes the sense of belonging to a community the event creates within the industry, be it from an exhibitor or a visitor’s standpoint, the various activities held in Frankfurt, also highlight the need for people to network and to further know other industry professionals in a very sophisticated range of experiences. This year, these activities included for instance, the very select AM Ventures’ walking dinner held on Tuesday, the AMT party, or even, the Formnext happy hour that was held on Thursday. And these are just the cherries on the cake…Added to this the various booth parties, exhibitors held where they were located, other marketing attractions to draw crowds’ attention, and sub-events of formnext, you obtain another form of immersive experience into the event.
Production before, today, and tomorrow
From a manufacturing perspective, ready-to-use production parts have always been the ultimate goal of industrials. Over time, companies came to realize that addressing this issue necessarily requires to involve other stakeholders of the AM ecosystem, stakeholders that are not only and always 3D printer manufacturers.
The in-person 2019 edition for instance, laid emphasis on several items including post-processing, to address this issue. This edition of Formnext first reveals that the most urgent needs at the production level require to take into account supply chain discrepancies, distributed manufacturing or localized production as well as sustainability concerns.
Unlike “3D printers” that can easily be displayed and seen, these are topics one can only discuss with stakeholders of the industry. As a matter of fact, a few 3D printer manufacturers and material producers told 3D ADEPT Media that they exhibited to meet new companies that could meet distribution challenges in regions they are not present yet.
Furthermore, the manufacturing standpoint highlights how Polymer AM is increasingly heading towards mass production. HP for instance, has cemented a leading position in this area, and does not intend to stop now (given its partnership with L’Oréal). Indeed, on the path to the makeover for the cosmetics industry, HP and L’Oréal signed a partnership to increase production flexibility and to create innovative new packaging and customer experiences using AM. Both companies showcased examples of the custom pucks at Formnext, as well as unique textures for luxury cosmetics only possible with HP’s 3D printing solutions.
Other companies that are worth watching in this field include Stratasys and voxeljet. Stratasys has always been a company to watch, even more so now that it has expanded the portfolio of its companies and has unveiled its SAF technology.
What I like about voxeljet’s proposition in this field, is that they are focussing on the economics side of manufacturing. The company is looking to enhance the use of its VX1000 system (a machine that combines the benefits of selective laser sintering and binder jetting) by developing a material-machine combination with materials producer Covestro. Both companies have previously developed a Thermoplastic Polyurethane (TPU) powder for HSS (High Speed Sintering) and now they are looking to enable volume manufacturing thanks to a dedicated material-process solution.
Moreover, we will keep a keen interest in AM startups as they are uniquely positioned to disrupt the industry and in machine manufacturers that ambition to bring affordable solutions to the market. At the end of the day, the latter makes it possible for a wide range of industries to take their first steps in AM, especially metal AM which remains the most extensive process of the market. Xact Metal is a very good example in this category. The machine manufacturer has showcased the XM200G metal 3D printer series at Formnext. With a build volume of 150 x 150 x 150 mm, the new 3D printer enables faster print times thanks to a high-performance galvanometer system. With a multi laser configuration, the machine would offer a 66% overlapping area at 50μm spot size, and a 100% overlapping area at 100μm spot size. Faithful to its mission of making metal powder bed fusion (PBF) more accessible; Xact has lowered the price point of its XM200C printer from $90,000 (€79786) to $65,000 (€57623).
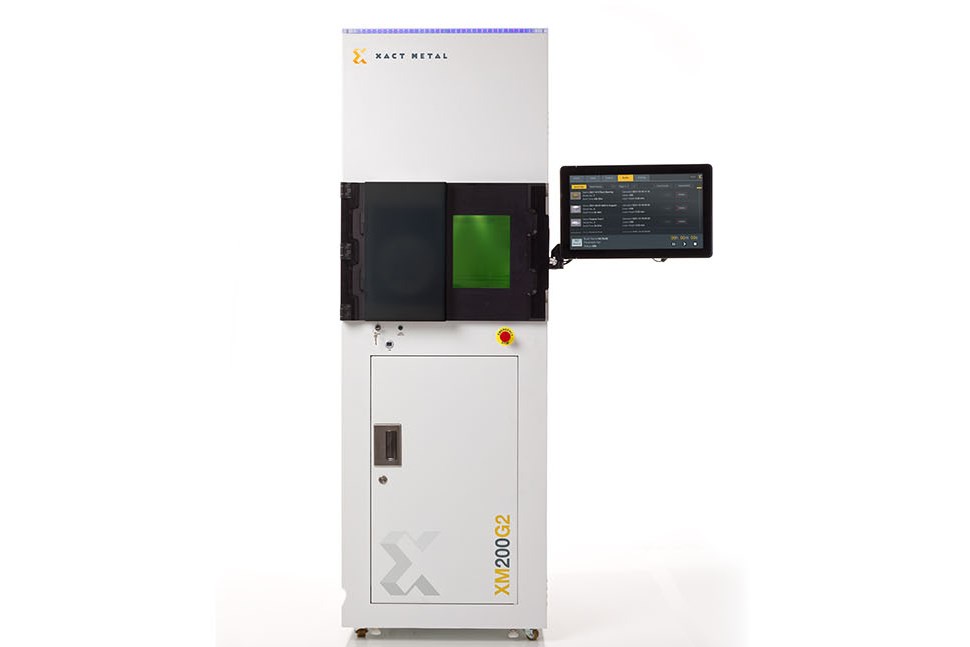
However, powder-bed fusion might be the widely known AM technology in the polymer AM niche, but let us not forget that this field’s growth is also due to the rise of other AM processes. I am thinking here to the well-known alternative SLS, the extrusion processes, as well as other technologies in the photopolymerization niche.
While manufacturers like Nexa3D want to make it easy for companies to explore applications in a commercial environment, we should recognize Anisoprint’s efforts to enhance composites AM. Anisoprint’s newest continuous fiber 3D printer is one of the machines we saw on the last day of the show, but we should have done it on the very first days. Indeed, its development does not only highlight Bosch’s expertise in automation technology, but it also marks Anisoprint’s entry point into IoT, which is a path most hardware producers are striving to achieve.
On the other hand, I also learned that a lot sill needs to be done in industrial 3D inkjet printing applications. It took a collaboration between Altana and dp polar for me to realize that multi-material 3D printing has often been hindered by non-end-use applications, and that’s an area I hope to see evolve over the next months or years.
In the same vein, it might be easy to set aside what’s happening in the software side of the manufacturing industry, yet it is the software that makes AM machines dance on the production floor.

The thing is, there are so many considerations to take into account at the software level (some of which have been addressed in our general video report that will be released soon), but for some reasons, part identification and simulation remain one of the most important ones in my eyes. While the first one helps you determine the right part to produce for AM, simulation is pivotal to ensure or reach a “First Time Right”, or at least early in the design and production stage. This is particularly important in metal 3D printing applications where parameters are often complex to set for every material and part, and where operators are struggling to avoid material waste, and to save time.
One example that I have kept from the show is the Amp cloud-based, process management software platform from GE Additive. With limited release of the first two modules (Print Model and Simulation & Compensation), the software is designed for Concept Laser M2 machine users.
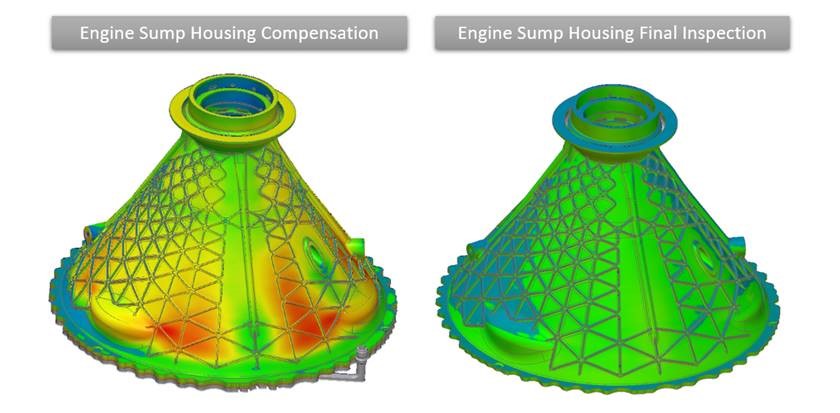
“Amp is the fourth pillar in GE Additive’s full solution along with machines, materials and services,” said Igal Kaptsan, general manager – software at GE Additive.
Amp breaks down the silos between CAD, build prep, simulation, compensation and inspection data to help improve part production. With centralized data, users can access tools that simulate how the manufacturing process unfolds in real time and see the estimates for cost and time for a part throughout the process. Amp streamlines the process. It uses a single database that supports seamless data transition between one task and another. In addition to the database, Amp also incorporates the industrial knowledge, best practices and workflows, and time/cost analyses that GE has pioneered over the past decade, the company explains.
The Cost conversation
Let’s admit it. Talking about money is not sexy and it’s a conversation, nobody likes to have. We are super glad that our conversations with AM companies like AMCM GmbH, highlight the need to bring down the final cost per part as one of the key challenges to address, in all vertical industries.
Indeed, in order to reach full commercialization at scale, industrials or parts manufacturers will continue to evaluate AM versus other manufacturing methods, trends in material pricing, not to mention software paradigm that comes into play.
One thing, I have observed in the AM industry, is that 3D printer manufacturers do not often take the lead at this level – At least, very few comparisons are revealed at this stage. I strongly believe, it will only serve more vertical industries if they are shown in advance the benefits in terms of costs by investing in AM technologies, rather than just the benefits of the technology.
You do understand that with over 600 companies on the exhibition floor, it becomes more and more difficult to share the key highlights of Formnext. Stay Tuned for other reviews.
Remember, you can post job opportunities in the AM Industry on 3D ADEPT Media free of charge or look for a job via our job board. Make sure to follow us on our social networks and subscribe to our weekly newsletter : Facebook, Twitter, LinkedIn & Instagram ! If you want to be featured in the next issue of our digital magazine or if you hear a story that needs to be heard, make sure you send it to contact@3dadept.com