In the most challenging environments, where elements are harsh and durability is key, it is truer than ever that materials matter. A few weeks after the release of their super-duplex stainless steel, Nikhil Dixit, Application Engineer at Sandvik Additive Manufacturing shares further insights into the benefits, potential and impact of this material for additive manufacturing applications.
While iron-based and highly corrosion resistant materials increasingly raise interest for additive manufacturing applications, super-duplex stainless steel remain one of the most challenging materials to process with AM technologies. The truth is, many have tried and failed to obtain the combination’s substantial benefits in terms of application performance and business optimization.
Together with BEAMIT, materials producer Sandvik has developed the super duplex Osprey® 2507 material, a durable, corrosion resistant powder that seems to be the ideal material candidate for the offshore industry.
The Sandvik team has been working on the development of these materials for decades, launching alloy variations with improved performance and properties. Nikhil Dixit, an Application Engineer at Sandvik Additive Manufacturing, focuses specifically on Powder Bed Fusion (PBF) processes in AM. As far as super duplex is concerned, Nikhil has been heavily involved in the development of process parameters and the material qualification for the company’s laser PBF.
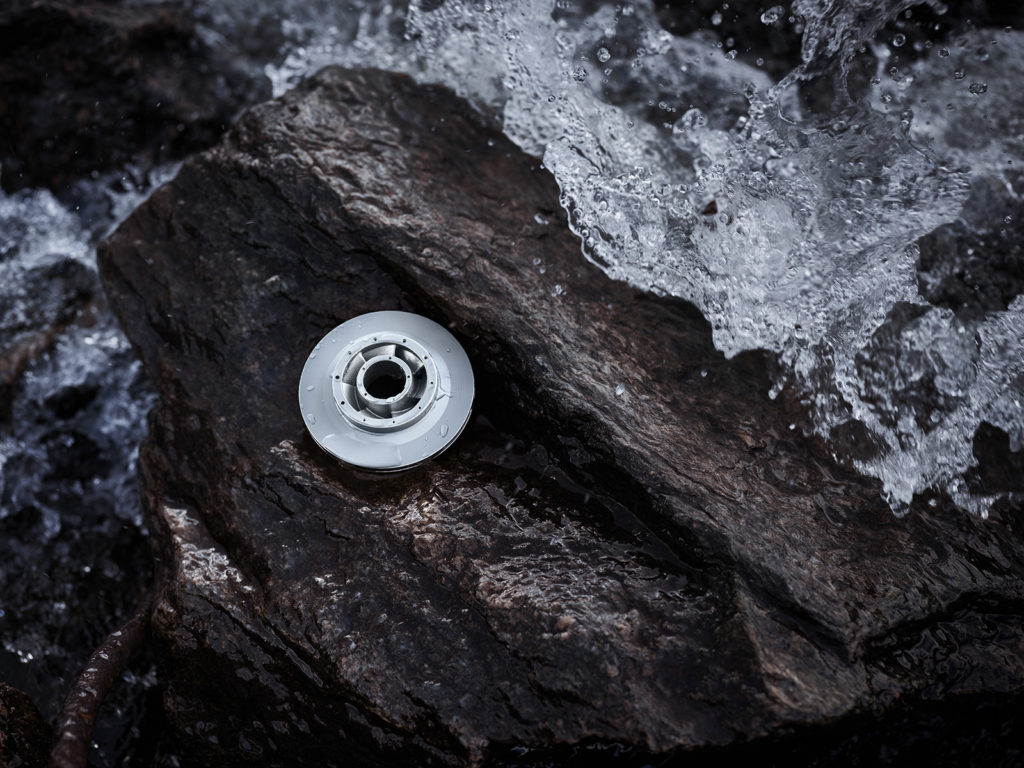
Can you tell us about the process leading up to the point of Sandvik presenting the ability to successfully print super-duplex stainless steel to the market?
First of all, the suitability of super duplex in corrosive environments is already well known. However, it is important to note that using super duplex in additive manufacturing is one thing – and printing it with great outcome is something entirely different.
Being a duplex materials authority, we combine this expertise with the additive know-how found within Sandvik and the BEAMIT Group to bring the use of super-duplex stainless steel to the next level.
What kind of results have you seen in the printed super-duplex components, and how do they differ from those of conventionally manufactured parts?
Well, there’s more to additive manufacturing than printing alone. With our “Plan it, Print it, Perfect it” approach, one clearly sees that printing is just one of the seven steps you need to master in order to succeed in the industrialization of additive manufacturing. Using premium raw materials is essential in order to obtain a high-quality, printed component and the super-duplex metal powder produced and optimized for 3D printing within Sandvik, definitely stands out in terms of powder characteristics and low oxygen levels. So this fact is at the very core of observing the performance of our printed Osprey® 2507 components. In terms of tensile impact and corrosion properties, additively manufactured super-duplex stainless steel doesn’t just meet the performance of conventionally manufactured components, but actually exceeds them. We have observed components that are near fully dense (>99.9%) and crack free – even before post processing.
We’ve already established super-duplex as a durable and corrosion resistant material. What does it take to optimize it for additive manufacturing, without compromising its highly valued properties?
Again, it all comes down to the quality of your raw material – i.e. the super duplex metal powder. Since we atomize these powders in-house at Sandvik, we have a unique ability to control the full value chain, from raw material sourcing, to finished component. Every result is based on controlling the details, and from the get-go in our state-of-the-art powder plant, through the extensive additive machine park and post processing, we leave no stone unturned in order to safeguard the quality, continuity, and traceability along the additive value chain.
How would you describe the potential related to additively manufactured super-duplex, other than those of the material itself?
The industries where super-duplex stainless steel is the material of choice are also positioned to enjoy the benefits of implementing additive manufacturing. AM is seen as a disruptive technology across a variety of business segments, enabling revolutionary levels of performance optimization, reduced material waste and environmental impact, as well as on-demand production – just to name a few. In the offshore industries specifically, I would say the implementation of 3D printed super duplex, including on-demand production of spare parts, decreased stock keeping, and timely deliveries, could have a revolutionary impact on profitability and performance alike.
So, from the launch of this game-changing ability… What can we expect now?
We are very excited to partner up and get down to business with customers across various offshore segments, to experience this in full effect. Apart from that, together with BEAMIT, we are already hard at work to develop print parameters for multiple-laser machines, in order to expand our offering to include even larger applications – which will allow for even more customers to implement AM into their operations. Acting on this rapidly expanding market, and in such an innovative environment, I feel confident to say this is only the beginning.
Interview edited for length and clarity.
Remember, you can post job opportunities in the AM Industry on 3D ADEPT Media free of charge or look for a job via our job board. Make sure to follow us on our social networks and subscribe to our weekly newsletter : Facebook, Twitter, LinkedIn & Instagram ! If you want to be featured in the next issue of our digital magazine or if you hear a story that needs to be heard, make sure to send it to contact@3dadept.com