Bois, granulés, résines, poudres, filaments… les industries peuvent imprimer en 3D presque n’importe quelle forme de matériau et les processus fascinants qui permettent de transformer ces matériaux en produits finis sont aussi ceux qui rendent l’utilisation des matériaux appropriés si complexe. À mesure que la fabrication additive (FA) progresse, elle crée de nouvelles tendances et de nouvelles complexités que les producteurs de matériaux doivent continuellement démêler. Dans cette série, 3D ADEPT Media a posé aux producteurs de matériaux diverses questions sur différents sujets qui suscitent le débat parmi les utilisateurs de matériaux de FA.
Résines d’impression 3D.
Même si le titre n’est pas officiellement reconnu, il est plus simple de décrire le groupe de machines qui travaillent avec des matériaux en résine comme l’impression 3D résine. Il existe différents types de procédés d’impression 3D résine, chacun d’eux ayant son lot d’avantages et d’inconvénients. Du point de vue de la fabrication, rappelons que les procédés d’impression 3D en résine reposent souvent sur le principe de la photopolymérisation ; ils fonctionnent selon un code (ou l’imprimante 3D crée un code directement à partir d’un modèle numérique téléchargé) ; le matériau – stocké dans un VAT – peut être une résine UV ou lumière du jour.
La SLA, la DLP et la LCD sont souvent les procédés les plus mentionnés lorsqu’on parle d’impression 3D résine, pourtant d’autres procédés sont en cours de développement et de commercialisation – des procédés tels que l’impression 3D à jet d’encre, la Digital Light Synthesis ™ ou même la technologie VLM (Viscous Lithography Manufacturing) récemment lancée. Il est intéressant de noter que, quel que soit le procédé d’impression 3D résine, l’enjeu est toujours le même au niveau des matériaux : que faut-il faire pour les utiliser en série ou en production industrielle ?
Tout d’abord, reconnaissons que les progrès extraordinaires réalisés dans la technologie des résines « à polymérisation unique », « à polymérisation double » ou dans les chimies UV (qui sont passées de diverses nuances des mêmes matériaux rigides et cassants à un spectre plus large de propriétés, notamment des résines rigides et résistantes, et des élastomères) ont laissé place à l’innovation. Le problème qui entrave le plus la production en série ou industrielle est probablement la comparaison constante avec les thermoplastiques moulés par injection et ce qu’ils permettent en termes de production. La vérité est que la SLA, la DLP ou tout autre type de technologie d’impression 3D résine peuvent atteindre des objectifs différents en matière de fabrication – sans compter qu’elles s’améliorent à leur propre rythme et selon différentes caractéristiques, mais cette comparaison est probablement le premier argument qui empêche les utilisateurs industriels d’apprécier leurs capacités.
Cela dit, malgré les progrès réalisés actuellement au niveau des matériaux, certains procédés d’impression 3D résine ne sont pas encore prêts à franchir une nouvelle étape dans la fabrication. L’impression 3D par jet d’encre, par exemple (un processus à basse température et à basse pression qui implique le dépôt de matériaux liquides ou de suspensions solides), est nativement multi-matériaux, mais elle a souvent été entravée par des applications non finales.
Il est intéressant de noter que les développements actuels en matière de résines mettent l’accent sur les résines à faible et à forte viscosité.
La viscosité est généralement mentionnée comme l’un des paramètres rhéologiques les plus importants permettant de déterminer les conditions de traitement optimales pour la FA FDM et les granulés. Tout comme la densité, la viscosité permet de donner des informations sur le matériau lui-même. « En règle générale, plus la viscosité des résines 3D est élevée, plus les propriétés mécaniques et la sécurité sont élevées », explique Nika Borges, responsable des ventes et du marketing pour le producteur de matériaux 3Dresyns, parlant de l’impression 3D résine.
En pratique, deux écoles de pensée émergent actuellement en matière de viscosité : le petit groupe de personnes qui voit les avantages des résines à faible viscosité pour l’impression 3D SLA et l’autre qui voit une série d’opportunités dans les résines à haute viscosité.
Le rôle de la viscosité des résines a été largement exploré pour la stéréolithographie, où l’on préfère un matériau à très faible viscosité. Pour Borges, le problème des résines 3D à faible viscosité est qu’elles « présentent des propriétés mécaniques inférieures, telles qu’une ténacité et une résistance mécanique médiocres. Elles contiennent des monomères à faible viscosité, [ce qui peut entraîner] une toxicité élevée (…). » Le producteur de matériaux explique que « malgré leur faible viscosité », ses résines 3D sans monomère et à base de monomère se distinguent des autres car elles « présentent des performances élevées et une sécurité uniques. »
En revanche, les résines à viscosité élevée offrent évidemment des propriétés mécaniques plus fortes et une sécurité plus élevées.
« Une viscosité plus élevée signifie une résine plus épaisse. Cela a un effet sur le reflux du polymère et sur les mouvements de la plateforme. Si vous connaissez le volume de votre modèle 3D et la densité du matériau que vous avez choisi, vous pouvez facilement calculer le poids de votre modèle imprimé en 3D », a déclaré le producteur de matériaux résines Liqcreate.
Si les résines à haute viscosité contribuent à « fabriquer des matériaux sûrs à ultra-hautes performances », Borges note qu’au niveau de la production, « elles peuvent être imprimées dans la plupart des imprimantes commerciales à 25-50ºC après installation d’un chauffage. »
Qu’il s’agisse de basse ou de haute viscosité, on gardera à l’esprit que la viscosité de la résine ne dépend pas de la précision. Une résine à haute viscosité ne signifie pas qu’elle est facile à accumuler dans les vides d’impressions, une résine à faible viscosité ne signifie pas non plus qu’elle n’est pas facile à accumuler.
Quel que soit le type de matériaux utilisés, 3Dresyns exhorte actuellement les fabricants d’imprimantes 3D à développer des imprimantes plus grandes, abordables et fiables, basées sur les technologies MLCD et DLP. En fin de compte, la variabilité liée à chaque imprimante 3D peut grandement influencer le résultat du produit fini. Prenant l’exemple de la puissance lumineuse, Borges explique : « En fonction de la technologie d’imprimante 3D choisie, de sa conception, de sa configuration, de la longueur d’onde de la lumière, de sa puissance, de sa répartition dans la cuve et du temps de fonctionnement cumulé, la puissance lumineuse réelle disponible dans la cuve pour l’impression peut varier de manière significative, et par conséquent aussi les paramètres d’impression pour des imprimantes similaires et même d’une unité à l’autre du même modèle en raison de petites différences de production entre les unités. Les graphiques suivants montrent la décroissance typique de la puissance lumineuse en fonction de la durée de fonctionnement cumulée des panneaux LCD RVB multicolores standard, des panneaux LCD monochromes, des projecteurs à lampe numérique et des projecteurs à LED, tous généralement utilisés dans les imprimantes 3D SLA, DLP et LCD. »
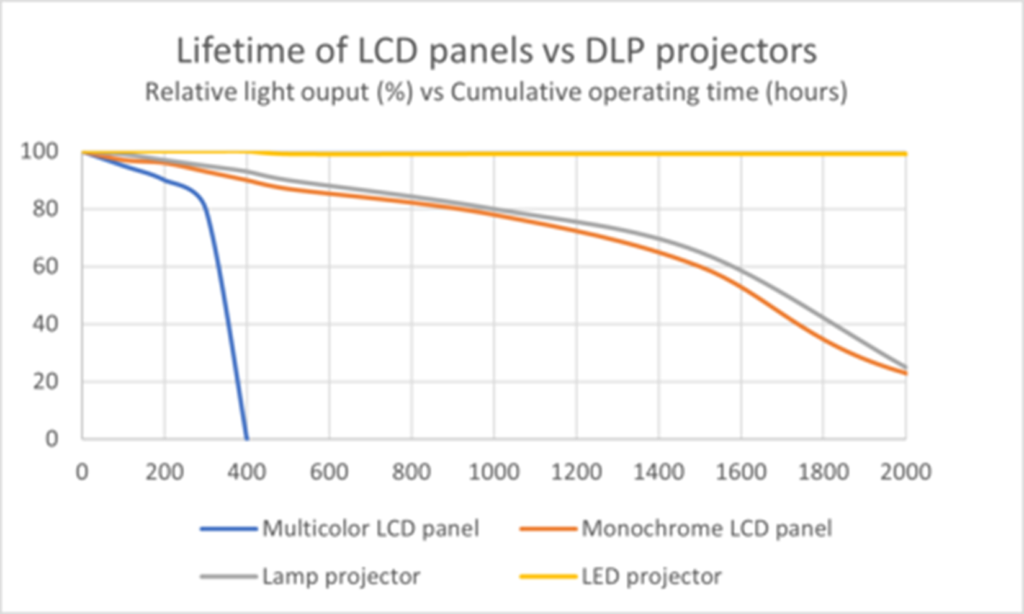
« Malheureusement, la puissance lumineuse varie et décroît en fonction du temps de fonctionnement cumulé. Même des unités différentes du même modèle, telles qu’elles sont fournies, présentent souvent des différences de puissance lumineuse de 10 à 15 %, ce qui affecte les résultats d’impression globaux. De plus, comme le montre le graphique ci-dessus, la puissance lumineuse diminue en fonction du temps de fonctionnement cumulé de l’imprimante. La variabilité de la puissance lumineuse en fonction de l’utilisation et le manque de contrôle de la puissance lumineuse dans le temps doivent être abordés pour promouvoir la révolution industrielle 3D. À l’heure actuelle, malheureusement, seuls quelques fabricants d’imprimantes ont abordé ces problèmes fondamentaux.
L’absence de contrôle de la puissance lumineuse, de surveillance et de prévention de sa dégradation est l’une des principales causes de frustration, de problèmes d’impression, de variabilité ou d’échec. L’impression professionnelle nécessite des imprimantes aux spécifications constantes pour favoriser le passage de la fabrication traditionnelle à la fabrication additive. »
Aujourd’hui, les questions des coûts et des applications continuent d’animer les discussions entre les utilisateurs d’impression 3D résine.
En ce qui concerne les applications, les utilisateurs avancés espèrent voir de nouveaux développements avec des résines composites ou nanocomposites photodurcissables.
L’adoption à grande échelle des résines à base de photopolymères est actuellement un Graal car le prix d’un grand nombre de composants photopolymères dépend de leur utilisation dans l’industrie des revêtements et des jets d’encre, où ils étaient principalement utilisés. Si la production de pièces en grand volume peut permettre de réduire le coût des matières premières, les technologies et les fournisseurs de services pourraient sensibiliser davantage l’utilisateur à la capacité d’une technologie à créer un produit dont la valeur vaut un nouveau prix.
Les composites.
Les composites sont des matériaux fascinants. Pour ceux qui ne sont pas encore familiarisés avec les composites, sachez qu’un composite désigne un matériau à matrice polymère thermodurci ou thermoplastique renforcé par des fibres continues ou discontinues. Ces fibres peuvent être des fibres de carbone, des fibres de verre ou des fibres naturelles telles que la fibre de jute, de lin, d’aramide ou de basalte.
Comme nous l’avons dit dans un dossier exclusif consacré à l’impression 3D de composites, lorsque la fabrication additive est arrivée dans la fabrication de composites, nous ne nous attendions pas à ce que cette combinaison fonctionne et conduise au développement de certaines applications de niche, intéressantes pour l’industrie.
Ces matériaux ont gagné leur place dans diverses applications rendues possibles par la fabrication additive aujourd’hui, et il existe un large éventail de techniques de fabrication additive capables de les traiter : fabrication d’objets laminés, fusion sur lit de poudre, photopolymérisation VAT et extrusion de matériaux (cette dernière comprenant 5 sous-segments différents) – chacune d’entre elles présentant son lot d’avantages et d’inconvénients :
Techniques | Avantages | Inconvénients | Alignement des fibres |
Fabrication d’Objet par Laminage ou fabrication d’objets stratifies (en anglais : Laminated object manufacturing) | Faible coût Possibilité de produire des pièces à haute résistance Aucune structure de soutien n’est nécessaire | Un gaspillage de matériaux plus importantIl est relativement difficile de construire des pièces avec des cavités complexes. | Orientation aléatoire des fibres Orientation uniforme de la fibre |
Fusion sur lit de poudre | Les structures de support peuvent être retirées facilementDes composites avec un renforcement plus important de la charge peuvent être réalisés.Résolution fineLes poudres non utilisées peuvent être réutilisées. | Finition rugueuse de la surfaceImpression lenteImpossibilité de fabriquer des composites à fibres longuesCoûteuxForte porosité des pièces finales | Orientation aléatoire des fibres |
VAT photopolymerization | Les fibres peuvent être alignées de manière aléatoire Résolution plus fine | Il y a formation de bullesDes matériaux limités ne peuvent être utilisés. Sédimentation des fibres dans la résine Augmentation de la viscosité de la résine avec l’ajout de fibresLe problème de la pénétration des rayons UV | Orientation aléatoire des fibresDans la direction du champ électriqueDans la direction du champ magnétiqueDans le sens de la poseEn fonction du motif des fibres du tapis |
Extrusion de matériaux | Facile à fabriquerÉconomique Capacité multi-matériaux Les têtes d’impression peuvent être facilement modifiées | Dégradation de la buseEffet obus couche par couchePour une charge de renfort plus élevée, la buse se bouche. | Dans le sens d’impression |
Tableau : Avantages et inconvénients des techniques de fabrication additive pour les matériaux composites. Crédit : Un aperçu de la fabrication additive d’un composite de polymère renforcé par des fibres
L’avancement de la fabrication additive des composites dépend principalement des partenariats entre les fabricants et les adoptants. Selon Hexcel, « les utilisateurs finaux déterminent les exigences techniques, qui remontent la chaîne d’approvisionnement pour informer les fabricants de machines et de matériaux. La personnalisation des propriétés des matériaux composites et les différences que l’orientation de la construction peut entraîner dans les matériaux composites font de ce lien un véritable moteur de l’innovation. »
Cela dit, il est intéressant de rappeler que la FA des composites ouvre de nouvelles possibilités pour l’allègement, alors que les experts envisagent de passer du métal au polymère. « L’allègement a été un moteur dans l’adoption des composites traditionnels et cette tendance se poursuit dans la FA », rappelle Hexcel. En effet, si la résistance et la rigidité sont souvent mentionnées comme des propriétés souhaitées délivrées lors de l’exploitation des composites (et notamment des fibres continues) avec la FA, elles ne sont pas aussi puissantes que l’avantage de l’allègement.
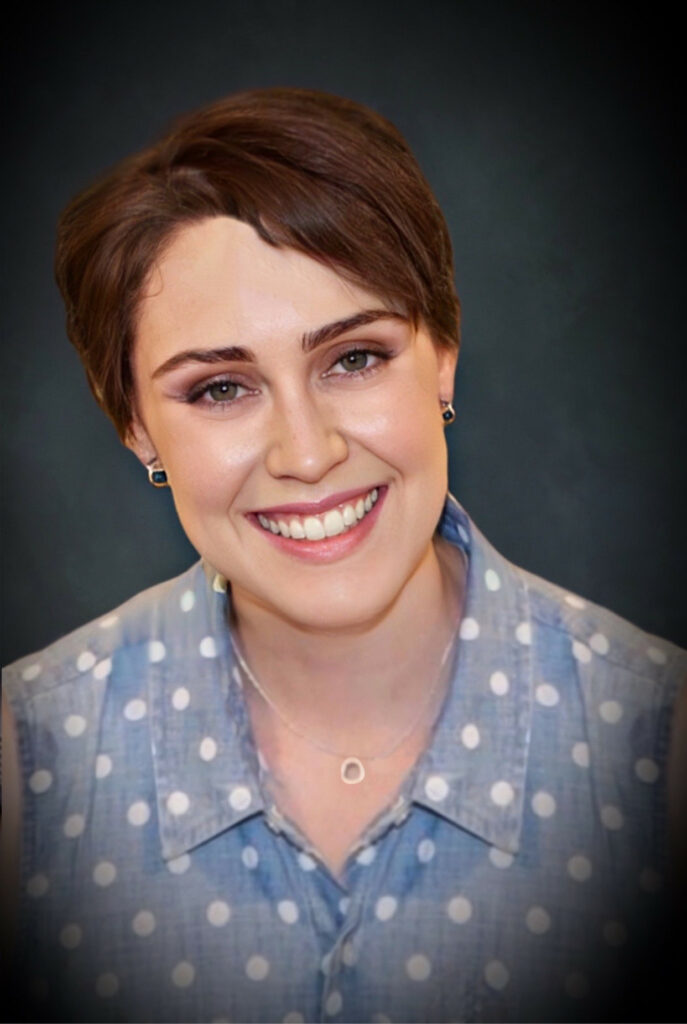
« Lorsque nous remplaçons des composants métalliques par HexPEKK-100, un matériau CF PEKK fabriqué par SLS, le gain de poids pour nos clients de l’aérospatiale est aussi important que les économies que nous apportons au programme. Les composites se prêtent également à la personnalisation des propriétés des matériaux. Conductivité, flexibilité, résistance à l’impact : tous ces domaines ont une incidence sur les possibilités de contrôle et d’ajustement d’un matériau dans un système de matériaux composites », souligne l’expert.
Malgré ces avantages, la FA des composites présente encore quelques zones d’ombre en ce qui concerne les possibilités offertes par les polymères renforcés de fibres de carbone et de verre (carbon and glass fiber reinforced polymers = CFRP and GFRP). En effet, le CFRP (qui signifie plastique renforcé de fibres de carbone) est léger et a une faible densité. Il est également extrêmement conducteur et très cher, ce qui est souvent considéré comme une limitation clé dans plusieurs applications.
Le plastique renforcé de fibres de verre (GFRP), quant à lui, a une densité et un poids moyens. Il est isolant et moins coûteux.
Pour ouvrir davantage de perspectives, Hexcel préfère se concentrer sur les nouvelles propriétés que les composites permettent d’obtenir lorsqu’ils sont combinés à la FA – que l’on ne peut pas obtenir avec les procédés de fabrication conventionnels.
« Dans cette phase d’adoption, la plupart des clients échangent la FA contre les méthodes de fabrication traditionnelles. La FA des composites présente un grand avantage dans cette compétition. Face à des composants traditionnellement métalliques, les composites peuvent apporter des propriétés telles que le blindage des signaux électromagnétiques, que nous proposons dans notre offre HexPEKK-EM, et qui étaient jusqu’à présent réservées aux remplacements non métalliques. »
En outre, une autre zone d’ombre concerne le processus actuel de génération de matériaux admissibles, ainsi que la qualification des machines et des pièces. Ce processus n’est pas spécifique aux composites car c’est aussi ce qui ralentit l’adoption de la FA en général. La vérité est que, pour un grand nombre d’utilisateurs de la FA – en particulier ceux qui viennent d’une industrie exigeante, c’est un véritable goulot d’étranglement de prévoir tous les matériaux admissibles pour une pièce spécifique. En raison du manque de données précises, les ingénieurs et les experts en matériaux doivent redéfinir le matériau idéal à chaque fois ou prendre en charge le développement de la simulation du processus de FA pour prédire les caractéristiques du matériau tel qu’il est construit.
« Pour Hexcel, cela nous a conduit à nous concentrer sur l’homogénéité de la flotte et le travail sur les matériaux admissibles afin de donner à la communauté technique les informations dont elle a besoin pour concevoir le matériau sans avoir à recommencer depuis le début pour chaque nouvelle pièce. À long terme, cela signifie qu’il faut s’appuyer davantage sur la vérification en cours de processus ou après le processus, comme l’inspection non destructive ou l’échantillonnage de qualité, et moins sur le verrouillage de chaque détail de fabrication pour chaque pièce spécifique. L’adoption est beaucoup plus rapide si tout le monde est d’accord sur ce qu’est un bon matériau à la fin et si vous donnez à l’équipe de fabrication la possibilité de modifier et d’optimiser le processus pour y parvenir. L’efficacité s’en trouve améliorée, ce qui donne aux adoptants un argumentaire plus large pour justifier l’intérêt de cette technologie », note Hexcel.
Filaments.
L’impression 3D commence avec les filaments, progresse grâce aux filaments (et à d’autres matériaux évidemment) et est actuellement en pleine révolution grâce aux possibilités de production plus durable et locale créées par les filaments. Cependant, un certain nombre de questions continuent de susciter le débat dans tous les secteurs, des questions concernant la durabilité des matériaux, la certification et l’impression 3D métal.
En ce qui concerne la durabilité, rappelons que l’impression 3D a toujours prétendu être durable en raison de la réduction du gaspillage dans la fabrication par rapport à d’autres formes de fabrication comme l’usinage. Cependant, les matériaux les plus populaires ont toujours été les polymères à base de carbone, qui ne sont pas durables par nature puisqu’ils sont dérivés de ressources non renouvelables. S’agissant précisément des filaments, certains producteurs de matériaux ont commencé à mettre en avant les « avantages écologiques » de leurs matériaux.
En réalité, ils sont assez « peu clairs sur le caractère durable de [leurs matériaux], par exemple le pourcentage de matériaux recyclés, la provenance de la partie recyclée, etc. Pour accroître l’adoption de matériaux durables dans la production, les clients doivent être convaincus que le matériau est durable, qu’il possède de bonnes propriétés techniques et, surtout, qu’il sera reproductible », explique Thiago Medeiros Araujo, chef de produit mondial de LUVOCOM 3F.
Des caractéristiques telles que la recyclabilité et la réutilisabilité ont été une tendance qui s’est imposée en 2021 comme une approche différente de la durabilité dans l’impression 3D, mais les mentionner ne suffit plus aujourd’hui.
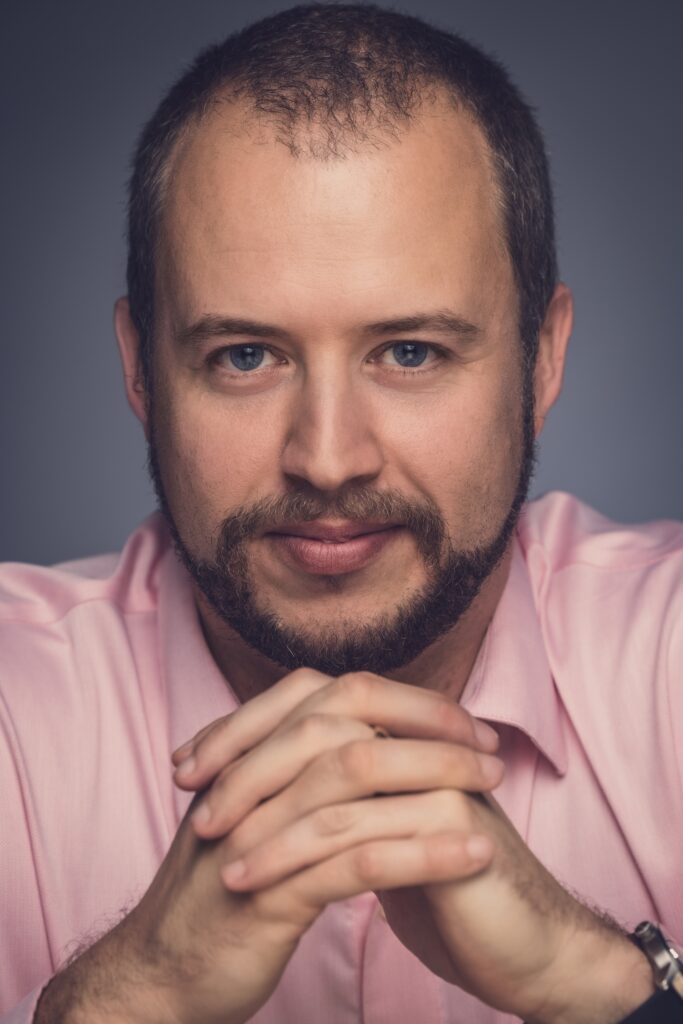
Certification.
La question de la certification a souvent été posée par des utilisateurs domestiques qui devaient s’assurer que leurs matériaux respectaient une norme de sécurité en matière de qualité de l’air intérieur. Dans un cadre industriel, cette caractéristique tend à rassurer les ingénieurs sur la qualité du matériau utilisé pour leurs projets.
Si la certification confère au matériau une certaine légitimité, Medeiros Araujo attire l’attention sur le fait qu’elle ne signifie pas nécessairement que ce matériau présente des « capacités industrielles » :
« Certifier un matériau en soi dans le cadre de l’impression 3D n’est pas quelque chose qui apporte une valeur ajoutée, car dans la plupart des cas, ses propriétés sont directement liées à la façon dont le matériau a été imprimé. Cependant, le fait de disposer d’un processus de fabrication certifié de manière indépendante a un impact énorme sur l’adoption du matériau, car il donne au client suffisamment de confiance pour utiliser le matériau immédiatement. Ainsi, l’utilisateur économise non seulement les coûts liés à l’évaluation du matériau, mais il réduit également le temps d’adoption. »
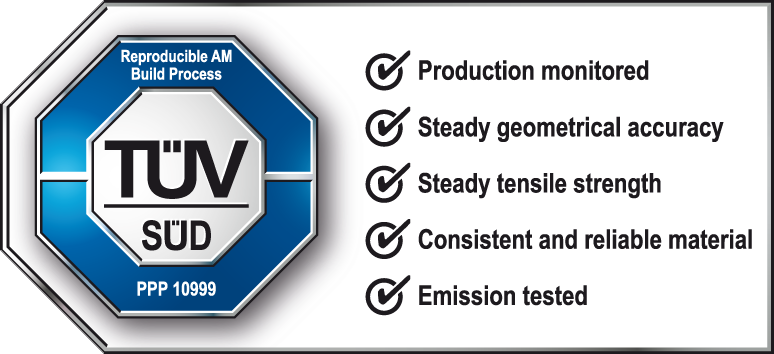
Impression 3D métal.
L’extrusion de filaments métal-polymère prend actuellement de l’ampleur car les professionnels sont constamment à la recherche d’une solution d’impression 3D métal abordable.
D’un point de vue commercial, ce segment d’activité se développe de plus en plus, donnant l’opportunité aux fabricants industriels d’imprimantes 3D FDM comme 3DGence de développer des machines capables de traiter des filaments d’impression 3D métalliques ou aux producteurs de matériaux comme Nanovia ou BASF de développer des filaments métalliques.
« Cependant, il faut garder à l’esprit qu’il ne s’agit pas seulement de produire le filament métallique mais de fournir au client l’ensemble de la structure pour le traitement ultérieur des pièces, par exemple le déliantage et le frittage », alerte l’expert de Lehvoss.
En effet, au niveau de la fabrication, les filaments métalliques d’impression 3D et d’autres matériaux contenant des additifs doivent souvent être frittés pour augmenter la densité des pièces, ce qui aide les utilisateurs à obtenir l’ensemble des propriétés mécaniques de haute performance.
Pour l’avenir, l’un des principaux défis de l’industrie reste de parvenir à une solution « bonne du premier coup », quel que soit le matériau utilisé. Et pour ce faire, il est important de rappeler que c’est une étape qui peut être atteinte grâce à des collaborations entre les différentes parties prenantes. Comme le dit Medeiros Araujo, « chaque partenariat exige beaucoup d’engagement et d’efforts de la part des deux parties pour que l’expérience soit sans faille dans le parcours de fabrication additive des clients. »
Notes aux lecteurs
Cet article opinion a été initialement publié dansle numéro Mars/Avril de 3D ADEPT Mag. L’article ci-dessus a mis en lumière les points de vue de producteurs de matériaux sur des sujets qui suscitent actuellement des débats dans les industries. Les principales opinions partagées sur ce sujet proviennent de 3Dresyns, Hexcel et Lehvoss Group. Leurs représentants partagent leurs points de vue sur les résines, les composites et les filaments.
N’oubliez pas que vous pouvez poster gratuitement les offres d’emploi de l’industrie de la FA sur 3D ADEPT Media ou rechercher un emploi via notre tableau d’offres d’emploi. N’hésitez pas à nous suivre sur nos réseaux sociaux et à vous inscrire à notre newsletter hebdomadaire : Facebook, Twitter, LinkedIn & Instagram ! Si vous avez une innovation à partager pour le prochain numéro de notre magazine numérique ou si vous avez un article à faire connaître, n’hésitez pas à nous envoyer un email à contact@3dadept.com