Among the wide range of technologies that can bolster an Additive Manufacturing (AM) application, nanotechnology is often the least mentioned. Yet the synergy between both technologies can lead to versatile and multifunctional applications that go beyond the healthcare industry. One reason that may explain this lack of exposure is a blurred understanding of nanotechnology and how both AM and nanotechnology can intertwine.
For some reason, nanotechnology often raises confusion with “tiny robots” or “micro-3D printing” technology. This field of activity actually refers to material science at the nanoscale. It reaches into a variety of sciences such as physics, chemistry, biology, and numerous branches of engineering.
The nanoscale is 1000x smaller than the microscale and a million times smaller than a millimeter – here one deals with individual or small groups of atoms, the latter of which are called nanoparticles. In addition to size, an interesting phenomenon is utilized when working in the nanoscale: in many instances, the increase in the ratio of [surface area]:[volume] by having more atoms exposed drastically changes the expected material properties of a device or object.
How do both AM and nanotechnology intertwine?
Simply put, AM can be applied to nanotechnology on the one hand, and nanotechnology can be applied to AM on the other hand.
In the former case, the complexity and design flexibility of nanoscale structures can be enhanced using 3D printing this means that AM becomes a tool used to create nanoscale structures and geometry. In the public’s eye, this would be a gigantic step forward as most additive technologies that are commercially available have as low as 25-50-micron resolution (SLA and DLP mostly). Several nanotechnology techniques that are additive in nature are already commonly used in the nanotech industry: 2 Photon Lithography, Dip-Pen Nanolithography, Electron Beam Melting, and Atomic Layer Deposition to name a few. Do not be mistaken, however, because these techniques are inherently quite fragile and require a great deal of precision as-is, so bringing them to an industrial market is a challenge.
In the latter case, the characteristics of 3D printed parts can be enhanced using nanomaterials’ advanced and tailorable properties. In some ways we are already seeing this – there are several companies such as Tethon3D, Covestro, and Mechnano that are adding nanocomposites to their photopolymer resin chemistries to enhance material properties significantly.
This means that nanoparticles (NPs) can be incorporated into a 3D printing host material like polymer or a ceramic matrice to form a nanocomposite. The new material can then be used as a feedstock material in AM processes such as FDM, SLS or SLA. Such incorporation can fill the gap that could help deliver macroscale geometries with exceptional properties, addressing this way the most prevalent issues of AM: the limited feedstock materials that are compatible with a given AM process.
In most instances, these nanocomposites are nanoscale ceramic particles or even carbon nanotubes, but these materials are becoming more advanced and unique every day. As such, the more there is a focus on materials development, the more one will see the critical role of nanotechnology.
What challenges may arise in combining both technologies?
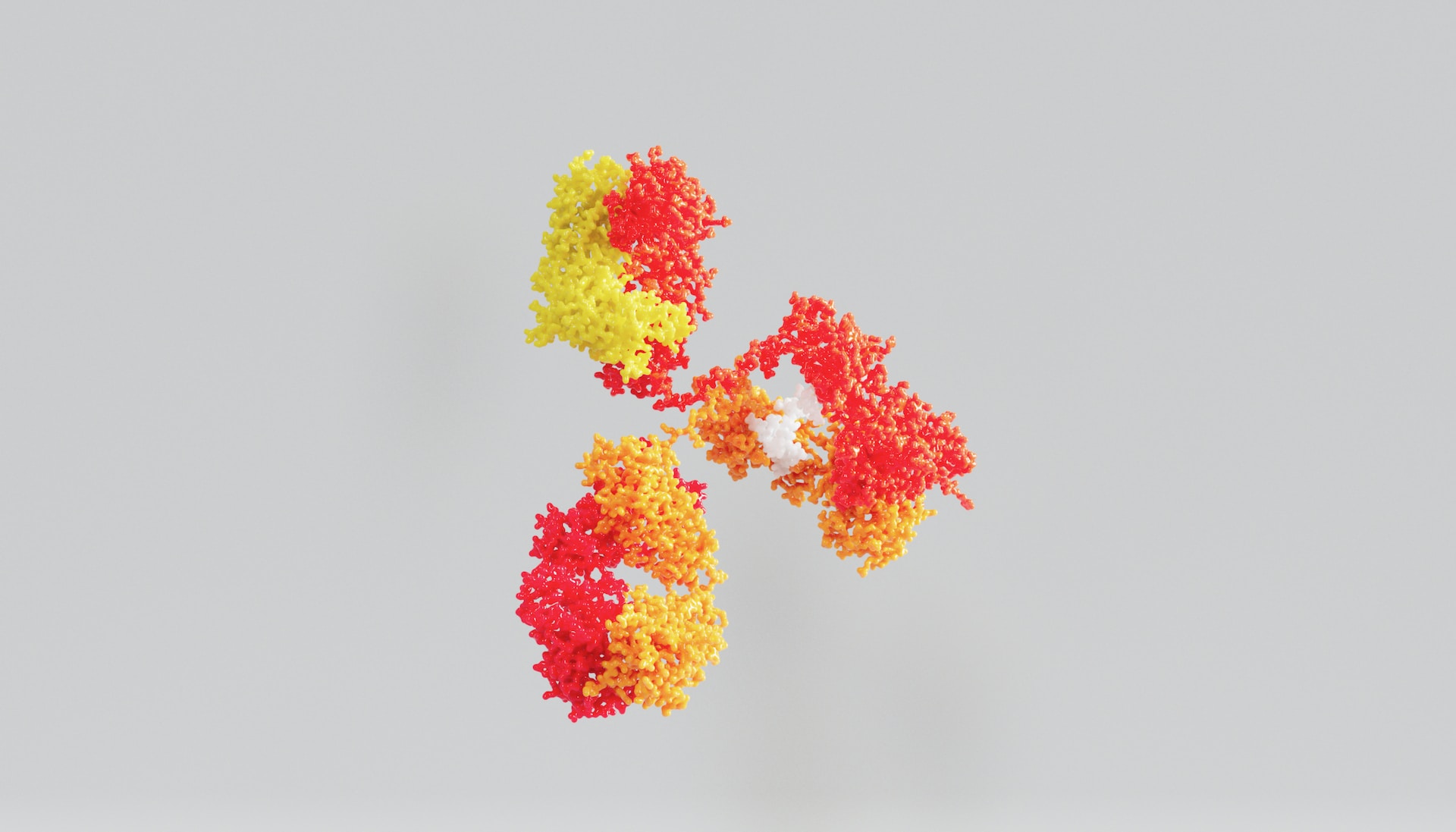
One of the main problems in adding nanotechnology to existing additive manufacturing techniques is the concern for environmental and personal safety. To this day, we are still exploring the negative impact of microplastics and finding traces of them on our beaches and in our bloodstream. Much like how previous generations struggled with exposure to mercury, lead, and asbestos, the last thing the world needs is to struggle with undesired exposure to nanotechnology. In many instances nanotechnology is safe – for example, your sunscreen is white largely because of the titanium dioxide nanoparticles found within it to reflect UV radiation from the sun, or the silver nanoparticles in your laundry detergent which have an amazing antimicrobial effect. The sheets of hexagonal boron-nitride found in your makeup provide an effective lubricant that requires no liquid or gas molecules, not to mention one of the most famous pieces of nanotechnology – graphite in pencils!
However, it is important to understand that for every nanoscale material or device that has overwhelmingly positive effects in our everyday lives, there is another that could cause severe health problems. A great amount of testing and regulation is used in the research phases of R&D to prevent these environmental and personal health risks from becoming ‘the next microplastic’ so to speak and this topic of responsibility is heavily discussed within the nanotechnology community.
What applications?
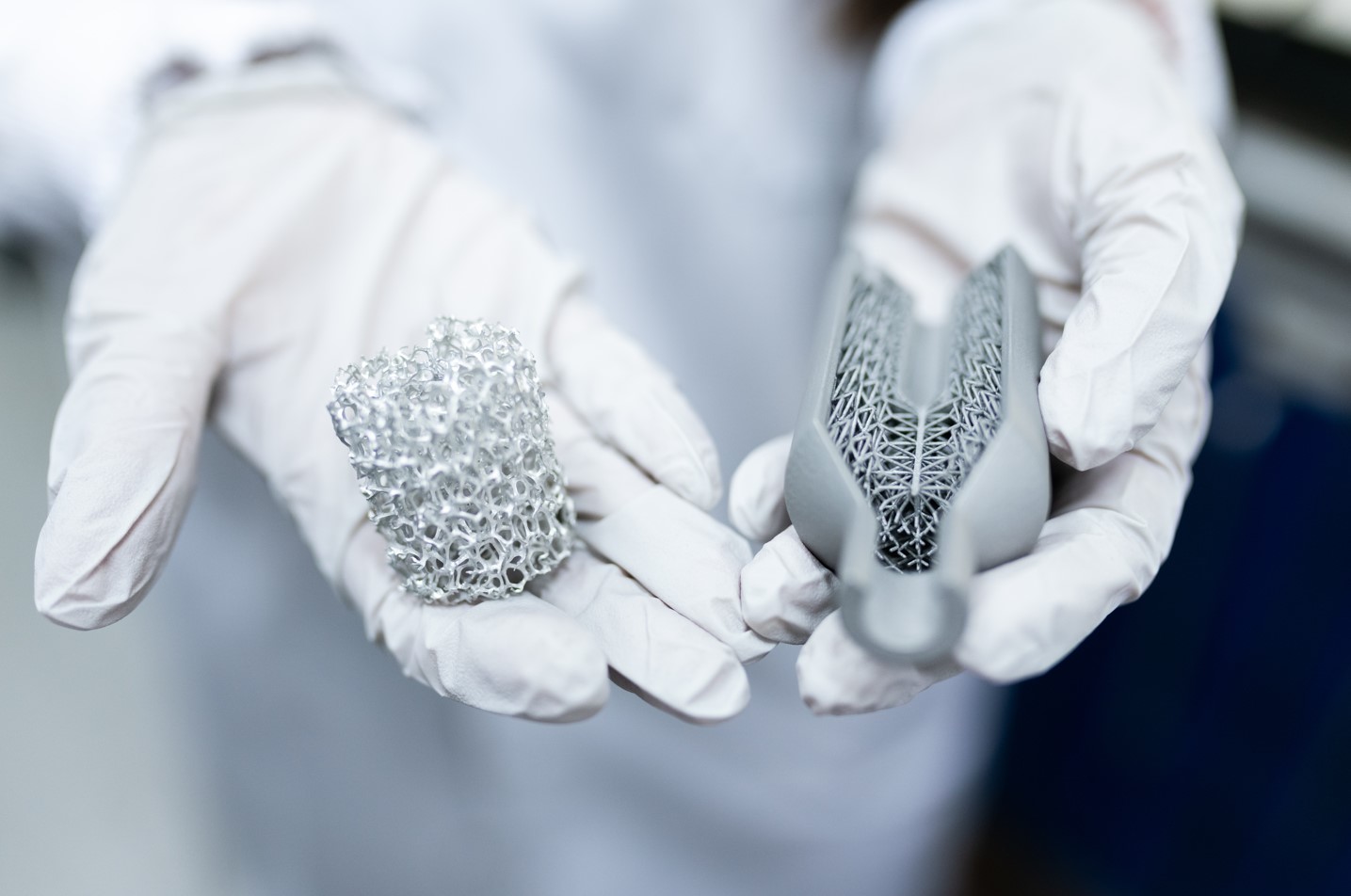
On another note, the main industries that could benefit from 3D printing nanocomposites are the biomedical and electronic sectors. An increase in organizing the atoms of any structure comes with greater material properties and thus better-engineered devices/structures. The photopolymer resins with nanocomposite fillers have already shown a huge leap in material properties: strength, thermal conductivity, electrical resistance, impact resistance, and more. For example, by integrating carbon-nanotubes and hydroxyapatite (HAp) NPs into the acrylic polymer polymethylmethacrylate (PMMA) for instance, it is possible to improve the flaws that may occur in the surgical fixation of artificial joints.
Photopolymer resins for SLA, DLP, and some material jetting techniques will foster the use of nanotech as these are the easiest materials to enhance, followed by thermoplastics for FDM. It will likely take longer for metal additive manufacturing to implement it due to the harsh processing conditions of techniques like powder bed fusion and directed energy deposition.
Creating structures with perfect surfaces, microscale features, and unparalleled consistency linked with the automation of AM definitely promises to be a powerful combination.
This article was first published in the July/August edition of 3D ADEPT Mag.
About the author
This feature has been co-written by Andrew Miller. Mechanical Engineer by training, Miller has decided to devote his career to AM and nanotechnology. By co-authoring 2 publications on metal additively manufactured heat exchangers, he learned of the fracture mechanics of rocket engine parts when working as an aerospace engineer for Blue Origin. It was there that it became clear to him that expanding his horizons into the realm of material science would expand his knowledge of additive manufacturing, and specializing in the field of nanotechnology would futureproof that education.
He is part of the Johns Hopkins Engineering for Professionals graduate program and with lessons learned from Professor John Slotwinski, Chair of the ASTM Executive Committee on AM technologies, he dreams of contributing to the AM community by implementing nanotechnology in new, unforeseen ways during the remainder of his career.