Le constructeur automobile Local Motors a continuellement amélioré son véhicule électrique autonome Olli 2.0 afin de répondre aux exigences de la mobilité durable. La navette Olli 2.0 a été dévoilée il y a deux ans et a nécessité un large éventail de collaborations avec des producteurs de matériaux et des développeurs de logiciels. La dernière collaboration de la société est celle annoncée avec le fabricant de pièces et le producteur de matériaux CRP Technology pour la fabrication de pièces utilisant des matériaux composites Windform.
Carlo Lacovini, directeur général EMEA de Local Motors, déclare : « Olli fonctionne dans les campus, les stades, les zones industrielles et les communautés locales du monde entier. Pour approuver les déploiements en Europe, il avait besoin de quelques composants supplémentaires, non requis sur le marché américain. »
Parmi les pièces imprimées en 3D, il y avait les essuie-glaces. Lacovinin explique que pour ajouter les essuie-glaces, ils ont opté pour la technique du rétrofit, ou processus de réadaptation, par une intégration sur le modèle 2.0.
« Nous sommes partis du projet initial, et nous l’avons adapté à nos besoins. Ces phases (rétrofit et intégration) ont été réalisées en Italie, sur la base de la conception originale produite par l’équipe d’ingénierie de Chandler. Ce fut un travail exigeant, car le design unique d’Olli 2.0 se caractérise par une haute nacelle rectangulaire avec des phares larges et de grandes fenêtres nichées dans un cadre. C’est exactement la raison pour laquelle le bras des essuie-glaces ne pouvait pas être positionné par le haut, mais par le côté inférieur de la fenêtre avant. Ainsi, le département d’ingénierie de Local Motors a conçu un nouveau pare-chocs avant avec des supports pour fixer à la fois le moteur de démarrage des essuie-glaces et le réservoir de lave-glace avant », ajoute-t-il.
Pendant la phase d’assemblage des essuie-glaces, l’équipe d’ingénieurs de Local Motors a remarqué que le moteur dépassait du pare-chocs avant modifié : « Pour éviter le problème, nous avons donc pensé à ajouter deux couvertures coordonnées, dans le but de dissimuler la partie saillante (la première couverture) et de protéger le système de pression du réservoir de lave-glace des agents extérieurs (la seconde couverture)», commente Lacovini.
Parmi les autres pièces qui ont été fabriquées figurent le couvercle du moteur ainsi que le clapet du réservoir de lave-glace.

L’équipe de Local Motors a réalisé un nouveau design du couvercle du moteur qui devrait répondre aux exigences d’homogénéité de l’ensemble de la structure. En effet, le clapet du réservoir d’eau doit être positionné symétriquement à celui de la charge.
Ensuite, ils l’ont envoyé à l’équipe de CRP Technology pour la fabrication. Le processus de fabrication nécessite la combinaison de l’impression 3D professionnelle / du processus de fusion en lit de poudre avec des fibres de polymères composites renforcées (également connu sous le nom de frittage sélectif par laser). L’équipe de fabrication a utilisé deux matériaux de la gamme Windform® TOP-LINE : le matériau composite à base de polyamide Windform XT 2.0 renforcé de fibres de carbone pour le moteur de démarrage des essuie-glaces et le matériau composite à base de polyamide Windform LX 3.0 renforcé de fibres de verre pour le clapet du réservoir de lave-glace (composant à vocation principalement fonctionnelle et partiellement esthétique).
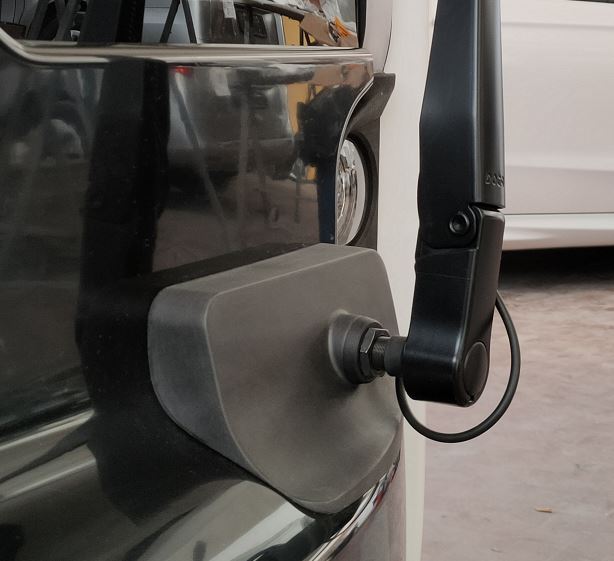
La fibre de carbone Windform XT 2.0 a déjà été utilisée dans plusieurs applications dans les secteurs de l’aérospatiale, de l’espace et de la mobilité. Elle permet d’apporter l’esthétique et la fonctionnalité idéales à une pièce tout en lui apportant rigidité, résistance et légèreté. Dans ce cas précis, elle supporte le mouvement oscillatoire du moteur. La pièce est une sorte de parallélépipède oblique en saillie avec une perforation pour le placement du bras d’essuie-glace et une plus petite pour le tuyau d’eau. Outre son rendu esthétique, la pièce placée à côté du moteur garantit la compatibilité électromagnétique, résiste au mouvement oscillant du bras et du balai d’essuie-glace, supporte les contraintes et les vibrations continues causées par la circulation sur les routes et préserve l’unité électrique des agents extérieurs.
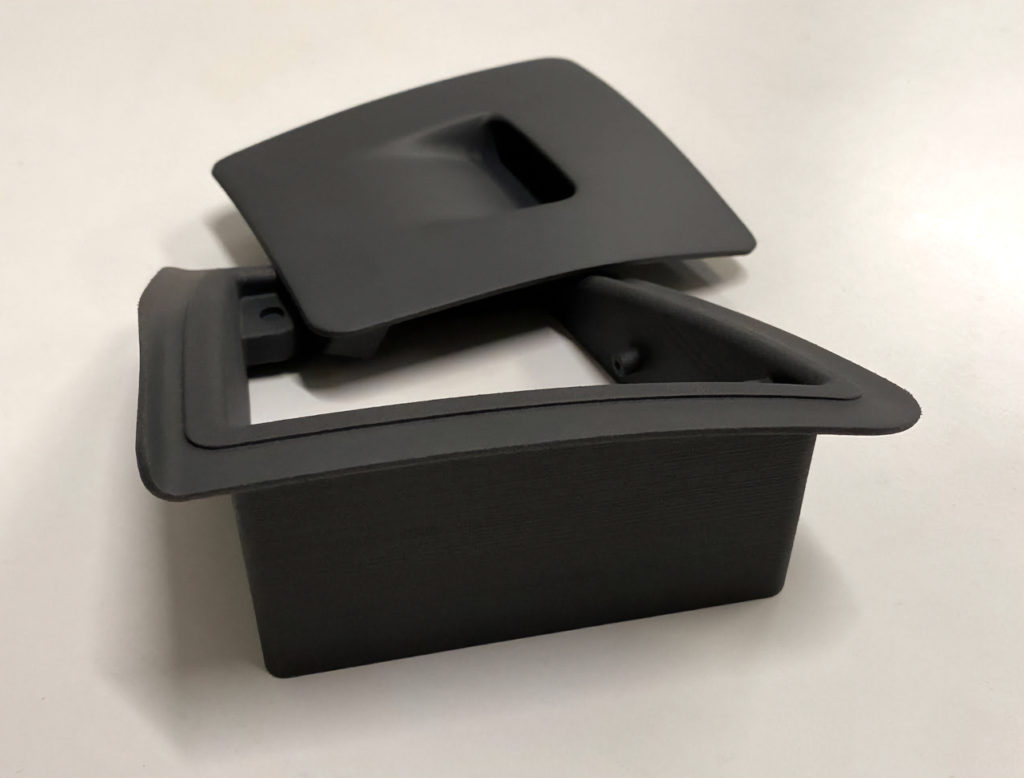
Idéale pour les applications difficiles, la fibre de verre Windform LX 3.0 résiste aux vibrations, aux déformations, aux températures élevées et basses et aux liquides. Le clapet du réservoir de lavage des essuie-glaces a un cadre à structure rectangulaire et le clapet est équipé d’aimants pour accéder au réservoir de lavage des essuie-glaces. Son objectif principal est d’assurer un accès rapide au réservoir de lave-glace situé à l’arrière, de le protéger des agents extérieurs et de résister aux contraintes et aux vibrations continues causées par la circulation sur les routes.
Après avoir fabriqué les pièces, CRP Technology a effectué les tests finaux et la livraison. Ensuite, un fournisseur de Local Motors les a installées sur Olli sans rencontrer de problèmes de montage et de fixation. Ensuite, Local Motors a effectué sur l’Olli « modifiée » des tests d’électromagnétisme dans la chambre anéchoïque. Les tests CEM ont concerné l’ensemble des essuie-glaces et ont donné d’excellents résultats. Aucun problème critique n’a été proposé en ce qui concerne les pièces imprimées en 3D en composites Windform, confirme CRP Technology dans un communiqué de presse.
N’oubliez pas que vous pouvez poster gratuitement les offres d’emploi de l’industrie de la FA sur 3D ADEPT Media ou rechercher un emploi via notre tableau d’offres d’emploi. N’hésitez pas à nous suivre sur nos réseaux sociaux et à vous inscrire à notre newsletter hebdomadaire : Facebook, Twitter, LinkedIn & Instagram !