Both companies share first feedback of tests on a series of 3D-printed Structural Steel Connectors
MX3D and Takenaka have worked together on the production of customized and engineered steel connectors using robotic 3D metal printing. Their collaboration started in 2019 with the goal of exploring the use of robotic Wire Arc Additive Manufacturing (WAAM) in the production of large customized steel connectors for the infrastructure industry.
The past three years saw a few great achievements from the Netherlands-based 3D metal printing company, which include an industrial robot arm or an aluminium 3D printed bike frame to name a few of them. Therefore, the collaboration with the Japanese architecture and construction firm was quite intriguing.
During the first year of their collaboration, the two teams revealed a successful production of the first connector prototype.
Thereafter, the two teams decided to focus on mechanical and material properties testing, a crucial step to get market validation.
In a press communication, they explain that destructive testing on a series of printed structural connectors showed strong and constant mechanical and material properties, paving the way to certification. Tensile tests, fatigue tests and buckling tests performed on the connectors showed convincing results. CT scans relieved the interior was dense and solid. Moreover, compressive failure tests confirm the clear effect of mortar filling on buckling resistance and ultimate strength. A 4mm-thick connector filled with mortar has approximately the same strength as an 8mm-thick connector (2.2 kN vs. 2.3 kN resp.), reducing 50% of required material making the freedom of form that 3D metal printing offers even more advantageous. The material properties and mechanical testing achieved desired specs and consistency, establishing the relevance of robotic 3D printing to the industry.
The series of connectors has been printed in duplex stainless steel, as the initial prototype. The alloy is renowned for its good mechanical properties and excellent corrosion resistance, ideal for structural applications. The hollow steel structure filled with concrete is highly effective and economical for safety performance, where the other steel bears bending and tensile forces and the inner concrete core delays or prevents local buckling of steel.
Connector_Analysis_Predicted_Peformation_vs_Actual_Deformation_Takenaka_MX3D
Researchers from Takenaka Corp. used information from physical testing of material specimens to generate a FE simulation model and assess the mechanical behaviour of the connectors. These results have been tested against real-life behaviour of the connectors undergoing compressive load. As the picture below shows, the results provided by the simulations were very close to the behaviour shown during the mechanical tests. Furthermore, tensile strength tests showed a highly consistent pattern, required for architects and engineers to include this technology in their tool kit. The full research will be published soon.
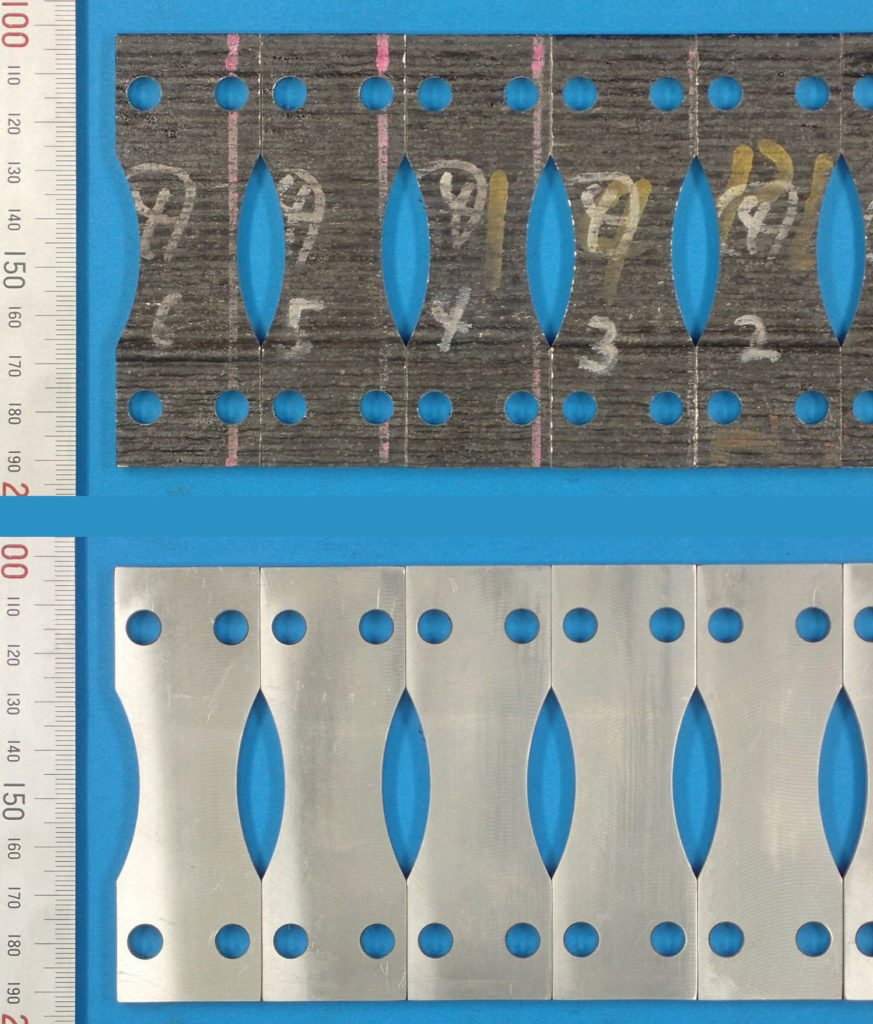
Following the successful fabrication of the optimized and printed structural steel connectors and the strong test results, the partners involved intend to implement the bigger version(s) in an actual building project.
Closing the digital design loop is key for the architecture, engineering and construction industry. MX3D’s robotic WAAM technology used to produce these connectors allows for full digital control over the design, production, timeline and cost with great logistic benefits and excellent integration with BIM applications. MX3D’s MetalXL now enables fabricators to quickly start 3D metal printing large-scale metal applications in their own facilities.
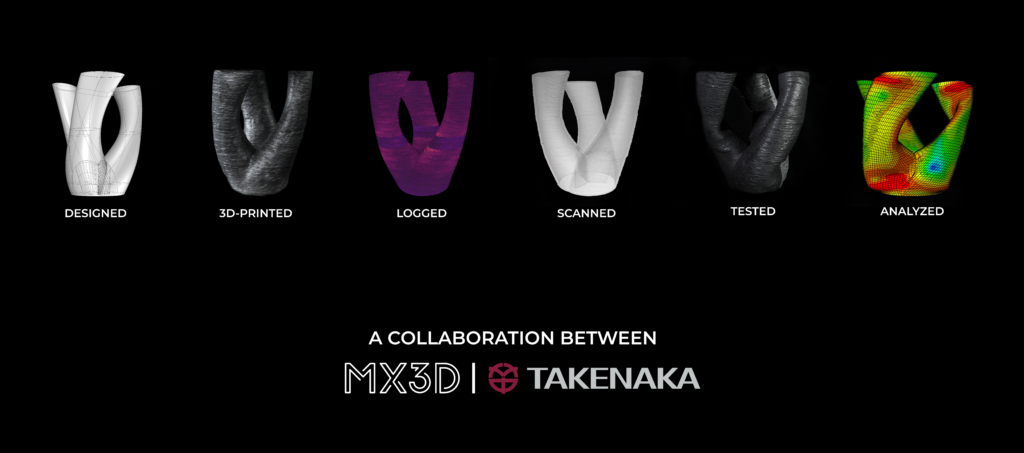
The strong mechanical and material results from the research project confirm the relevance of robotic 3D metal printing for architecture, engineering and construction and open up a new generation of structural connections for the AEC industry. Remember, you can post job opportunities in the AM Industry on 3D ADEPT Media free of charge or look for a job via our job board. Make sure to follow us on our social networks and subscribe to our weekly newsletter : Facebook, Twitter, LinkedIn & Instagram ! If you want to be featured in the next issue of our digital magazine or if you hear a story that needs to be heard, make sure to send it to contact@3dadept.com