Imaginez que le scanner de sécurité qui détecte des résidus de gaz dans un environnement public fonctionne mal en raison de la défaillance ou de la panne d’un matériau utilisé dans le processus de fabrication d’une pièce donnée. Dit de cette façon, on perçoit immédiatement l’importance que peuvent avoir les matériaux haute performance dans la fabrication d’une pièce.
Lorsqu’elles font appel à des technologies de fabrication additive, les multinationales ont habituellement en interne divers experts qui pourront apporter leur expertise dans le choix du système approprié, du bon matériau et des systèmes de pré et de post-production appropriés. Imaginez maintenant une situation où une PME n’a pas ces experts en interne pour faciliter le processus de prise de décision. Le choix d’un système d’impression 3D industriel ou professionnel n’est déjà pas une tâche facile. Cette tâche devient plus difficile lorsqu’il s’agit de matériaux.
En effet, au fur et à mesure que la technologie progresse, l’essor de termes techniques tels que matériaux haute performance, matériaux d’ingénierie ou matériaux avancés, s’accélère. A une époque où les entreprises ont tendance à prétendre être les « premières » à lancer leur technologie sur ce marché, il est facile pour l’utilisateur final potentiel de se perdre dans l’utilisation (parfois) abusive de mots techniques par les entreprises.
Le présent article vise donc à clarifier le sens des matériaux hautes performances. Il vise à aider les utilisateurs à identifier les différents types de matériaux hautes performances, à comprendre la caractérisation des matériaux et à déterminer la technologie de fabrication additive qui convient le mieux à ces matériaux. Pour aborder ce sujet, nous avons posé un certain nombre de questions à VBN Components, Armor Group et Malvern Panalytical B.V.
Matériaux haute performance, matériaux d’ingénierie ou matériaux avancés ?
Au cours des millénaires, les êtres humains ont exploité diverses substances pour développer de nouveaux matériaux utiles qu’on ne trouve pas habituellement dans la nature. En vérité, personne ne s’attendait à l’explosion de la recherche sur les matériaux qui a marqué le 20e siècle. Des automobiles aux avions, des articles de sport aux gratte-ciels, des vêtements aux ordinateurs et à une foule d’appareils électroniques – tous témoignent du potentiel des matériaux.
Plusieurs types de matériaux peuvent être mis à profit pour fabriquer des pièces de ces industries. Toutefois, la demande de composants de qualité supérieure pousse les fabricants et les fournisseurs à maîtriser les procédés d’usinage et d’assemblage de matériaux hautes performances.
Les matériaux (d’ingénierie) hautes performances visent à atteindre les performances supérieures des matériaux d’ingénierie dans les domaines suivants : résistance des matériaux, résistance à la déformation, fonctionnalité, légèreté, résistance à la corrosion, capacité à haute température, efficacité de la transformation des matériaux, durabilité et multifonctionnalité.
Selon Pierre-Antoine Pluvinage, Directeur du développement commercial chez ARMOR GROUP, pour la marque de FA KIMYA, la résistance thermique, la résistance mécanique et la résistance aux chocs sont souvent les premiers indicateurs clés de performance pris en compte pour identifier les matériaux hautes performances :
« Les matériaux hautes performances sont d’abord caractérisés par leur performance thermique. Un autre indicateur clé de performance peut être leur résistance chimique ou mécanique, ou leurs propriétés de résistance aux chocs.
Cependant, la performance thermique n’est pas nécessairement la seule caractéristique définissant un matériau de haute performance : elle peut fournir des propriétés fonctionnelles que d’autres matériaux d’ingénierie ou des matériaux facilement disponibles ne fourniraient pas ».
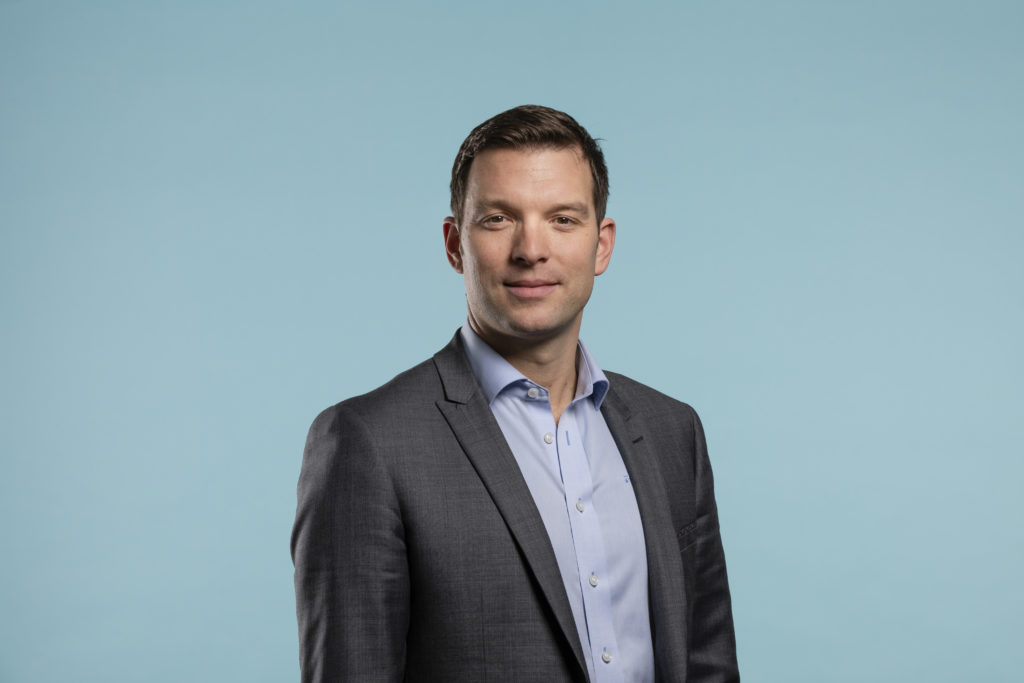
En outre, il convient de noter que plusieurs termes, dont les matériaux d’ingénierie ou les matériaux avancés, sont souvent utilisés pour désigner les matériaux hautess performance. Pourtant, une légère différence peut être observée entre les deux termes :
« Matériaux d’ingénierie » est un terme général qui fait référence à la sélection des matériaux appropriés pour l’application dans laquelle la pièce d’ingénierie est utilisée. Il faut se concentrer sur une qualité particulière de matériau en fonction de ses propriétés telles que la malléabilité ou la résistance à la traction.
Les matériaux qui sont utilisés dans des applications de haute technologie sont appelés matériaux avancés. Ce sont généralement des matériaux traditionnels dont les propriétés ont été améliorées, ainsi que des matériaux hautes performances nouvellement développés. En termes simples, lorsque l’accent est mis sur une qualité particulière de matériau, ou lorsque de nouvelles propriétés ont été développées à partir de matériaux traditionnels, le nouveau matériau est appelé « matériau avancé » ou « matériau haute performance ». Ces matériaux sont, par exemple, les mousses métalliques, les alliages magnétiques, les céramiques spéciales, etc. Ils sont utilisés dans les appareils de haute technologie comme les ordinateurs, les avions, les gadgets électroniques, etc. Certaines de leurs applications comprennent les circuits intégrés, les lasers, les écrans à cristaux liquides, les fibres optiques et bien d’autres.
Les matériaux d’ingénierie qui peuvent en dériver sont les métaux (ferreux et non ferreux), les céramiques, les polymères, les composites, les semi-conducteurs et les bio-matériaux. Cependant, dans le cadre de cet article, un accent particulier sera mis sur les polymères et les métaux.
Matériaux de haute performance : polymères (plastiques, thermoplastiques, poly carbones)
Un matériau est plus complexe que sa simple composition chimique. Ses propriétés dépendent de sa microstructure, qui peut évoluer – au cours du processus – ou de la durée de vie du matériau.
Le défi est encore plus grand pour les producteurs de matériaux polymères de haute performance. En effet, pour des industries exigeantes comme le transport, l’automobile ou même l’aérospatiale, les industriels sont en permanence à la recherche de matériaux légers aussi performants que le métal, le verre ou le caoutchouc.
Dans ce sens, le directeur du développement commercial du Groupe ARMOR explique que nous ne parlons pas seulement de matériaux hautes performances lorsqu’il s’agit de la fabrication additive. En effet, les matériaux hautes performances sont utilisés dans plusieurs processus de production comme le moulage par injection de métal ou les processus d’usinage. « Le défi consiste à évaluer comment utiliser ces matériaux et les adapter aux technologies d’impression 3D tout en conservant leurs propriétés natives », a déclaré l’expert du Groupe ARMOR.
Leur utilisation croissante dans la fabrication additive démontre que les matériaux les plus convoités peuvent résister à des températures élevées. Ces matériaux incluent par exemple : PAEK (PEEK, PEKK), PEI ou ULTEM ainsi que PPSU.
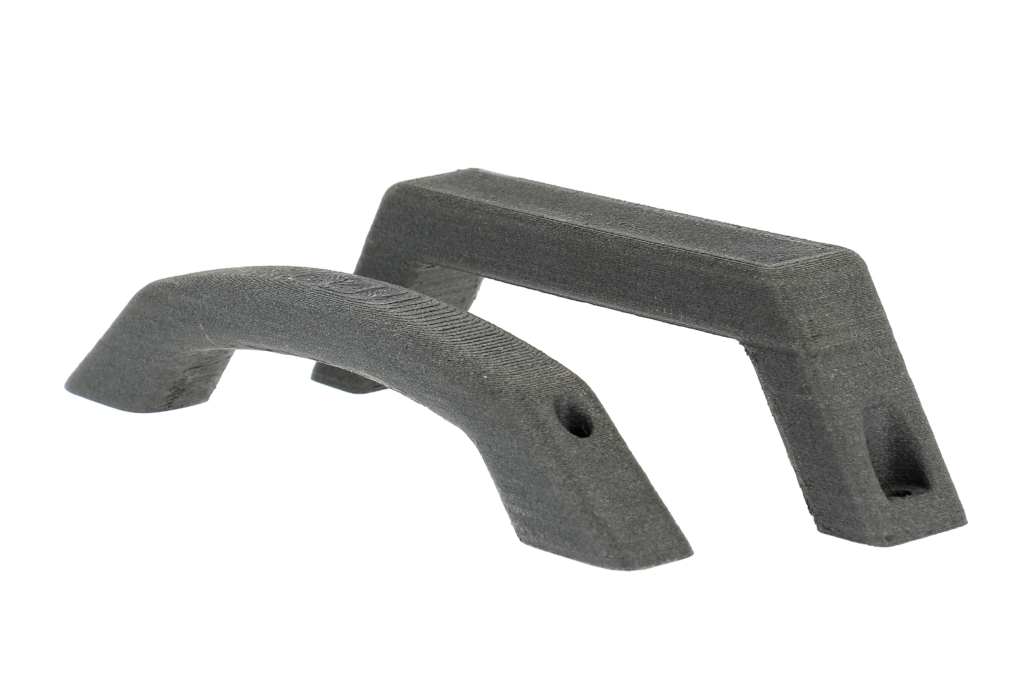
Lorsqu’un ou plusieurs polymères ou additifs sont ajoutés à une résine, cette combinaison donne un plastique technique qui intègre une haute résistance et plusieurs bonnes propriétés. Par exemple, pour développer le matériau Kimya PEKK-A, la résine Arkema Kepstan PEKK a été ajoutée lors de la fabrication. Le matériau final intègre un taux de cristallisation plus lent, ce qui permet d’obtenir des adhérences plus efficaces. De plus, il est reconnu pour sa grande résistance aux hautes températures (260°C), et sa capacité à recevoir d’autres fonctionnalités.
Maintenant, pour attester de la qualité de ce matériau, et de sa capacité à être traité sur diverses imprimantes 3D, la caractérisation des matériaux entre en jeu.
Caractérisation des matériaux
Au fur et à mesure que la technologie progresse, la caractérisation des matériaux devient de plus en plus sophistiquée. Plusieurs techniques existent pour étudier et mesurer les propriétés physiques, chimiques, mécaniques et microstructurales des matériaux. Le procédé peut être appliqué à plusieurs étapes de l’élaboration des matériaux.
Toutefois, quel que soit le processus, l’objectif global est, d’une part, de comprendre les éléments clés nécessaires pour résoudre des questions importantes, comme les causes de défaillance et les problèmes liés au processus, et d’autre part, de prendre des décisions critiques concernant les matériaux.
Des méthodes d’analyse normalisées et des techniques avancées spécialisées spécifiques à l’application peuvent être appliquées au cours de ce processus.
En ce qui concerne les filaments d’imprimante 3D, les propriétés mécaniques telles que la contrainte de déformation, la limite d’élasticité, la dureté, la résistance aux chocs ou la flexion sont d’abord testées pour tous les matériaux nouvellement fabriqués. Ces tests permettent de classer les matériaux en fonction de leurs spécifications et de déterminer si le matériau répond aux exigences du client. En outre, les spécialistes des matériaux effectuent un essai de résistance à la traction pour comparer le filament commercial et le filament fabriqué.
En ce qui concerne les matériaux prêts à être commercialisés, Pierre-Antoine Pluvinage a mentionné certains des critères qui sont pris en compte pour attester de leur qualité :
« Il y a plusieurs critères à prendre en compte pour contrôler la qualité des filaments : contrôle du diamètre, contrôle de l’ovalité, contrôle des imperfections (bulles d’air). On peut aussi ajouter l’imprimabilité, ainsi que l’évaluation des attributs fonctionnels liés aux spécifications techniques du produit », explique le Groupe ARMOR.
Le procédé idéal de fabrication additive
Les matériaux hautes performances à base de polymères peuvent être traités sur une imprimante 3D FDM ou sur une technologie SLS. Cependant, dans ce cas précis, voyons leurs conditions préalables sur une solution d’impression 3D FDM.
Malgré leur capacité à résister à des températures élevées, l’opérateur de FA doit faire attention à trois environnements de température : la température d’extrusion, la plaque d’impression et la chambre d’impression. Une buse qui présente une température trop élevée peut entraîner une déformation partielle de la pièce imprimée ou un suintement du matériau. Une température trop basse, par contre, ne permet pas une cohésion parfaite entre les couches.
En ce qui concerne la plaque d’impression, si la température est trop élevée, il ne sera pas possible de retirer facilement la pièce imprimée. En effet, le premier acteur aurait tellement adhéré à la plaque d’impression que celle-ci pourrait être endommagée. Une température trop basse provoquera un problème d’adhérence et entraînera une déformation de la pièce.
Quant à la chambre chauffée, sa température permet d’obtenir une bonne adhérence entre les couches et empêche le retrait lorsque le matériau fondu devient solide.
En plus de ces températures, l’opérateur de FA doit également faire attention au phénomène de cristallisation des matériaux. Les matériaux semi-cristallins comme le PEKK ont tendance à former des cristaux dans des environnements plus chauds que leur température de transition vitreuse. Ce phénomène peut d’abord conduire à un retrait et à une déformation de la pièce, et à la fin, à une défaillance du processus d’impression.
« Les avantages des matériaux haute performance résident précisément dans leur polyvalence et leur large éventail d’applications possibles. Les matériaux semi-cristallins offrent généralement des propriétés chimiques et mécaniques exceptionnelles, y compris [la capacité de résister] à des conditions de température élevées. Ils peuvent être utilisés dans des applications structurelles ainsi que dans des applications qui impliquent un frottement et une érosion. Par exemple, le PEKK-SC présente une résistance chimique et thermique élevée combinée à des propriétés d’isolation électrique et diélectrique. Les matériaux amorphes tels que le PPSU ou le PEKK-A conservent parfaitement leurs propriétés mécaniques jusqu’à la température de transition vitreuse et présentent d’excellentes propriétés électriques. Grâce à leur exceptionnelle stabilité dimensionnelle, ces matériaux sont adaptés aux composants de précision », a conclu le porte-parole du GROUPE ARMOR.
Matériaux de haute performance : métaux
Bien que les thermoplastiques aient attiré le plus l’attention au début de l’impression 3D, la FA métallique reste la technologie qui encourage la croissance de l’industrie de la fabrication additive.
Les métaux sont connus comme des matériaux ductiles. En d’autres termes, ils peuvent facilement résister aux contraintes de traction. Cependant, plus la technologie progresse, plus les problèmes tels que les points de fusion élevés, l’épaisseur des couches, la vitesse d’impression et la capacité de production sont abordés.
Un certain nombre de métaux différents sont disponibles sous forme de poudre pour répondre à divers procédés et exigences. Ces poudres comprennent le titane, l’acier, l’acier inoxydable, l’aluminium et le cuivre, le chome de cobalt, le titane ainsi que les alliages à base de nickel. Ces matériaux comprennent également des métaux précieux comme l’or, le platine, le palladium et l’argent.
L’intérêt croissant pour les matériaux de haute performance fabriqués avec ces matériaux réside dans le fait que ces composants imprimés en 3D ne sont pas souvent reproduits. A long terme, si l’opérateur a réussi à tirer parti de toutes les étapes du processus de fabrication, il peut bénéficier de faibles coûts de production.
Dans le même ordre d’idée, il faut noter que pour attester de la qualité des poudres susmentionnées, les mêmes propriétés ne sont pas nécessairement toujours testées.
VBN Components, par exemple, développe un acier rapide appelé Vibenite® 280, Isabelle Bodén, responsable des relations clients, explique que pour ce matériau, l’usure réelle à l’usage (« c’est-à-dire quelle quantité de matériau est usé lorsqu’il est exposé à l’abrasion ») et la dureté à long terme sont des caractéristiques clés qui doivent être prises en compte pour attester de la qualité de ce matériau.
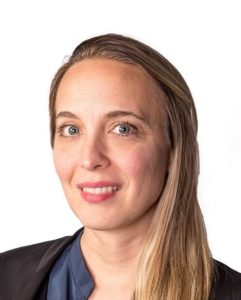
« Nos matériaux sont extrêmement résistants à l’usure. Par exemple, notre acier rapide Vibenite® 280 est utilisé dans une fraise mère, coupant deux fois plus profondément et durant deux fois plus longtemps avant d’avoir besoin d’être réaffûté, comparé à un acier supérieur traditionnel dans la même application. Les carbures de nos matériaux sont très fins et bien dispersés, ce qui permet d’obtenir des niveaux de dureté allant jusqu’à 72 HRC et une ténacité supérieure à ce que l’on peut attendre de matériaux aussi durs », a expliqué le porte-parole de l’entreprise basée en Suède.
Caractérisation des matériaux
Pour la FA d’une pièce donnée, le coût de la poudre représente jusqu’à un tiers du coût de production, sans compter que la viabilité commerciale doit être soutenue par une chaîne d’approvisionnement solide et des stratégies efficaces de recyclage de la poudre. En outre, il existe aujourd’hui plus de 14 technologies de FA à base de métaux. Toutefois, nous prendrons en compte les technologies de fusion sur lit de poudre pour discuter de ces techniques d’analyse.
Selon Malvern Panalytical, « les propriétés chimiques et physiques de la poudre ont un impact direct sur le processus de fabrication et la qualité des composants finaux et doivent être contrôlées et optimisées pour assurer la robustesse et l’uniformité du processus. Pour obtenir cette poudre, les propriétés doivent être caractérisées à différentes étapes de la chaîne d’approvisionnement, depuis le développement de nouveaux alliages jusqu’au recyclage de la poudre. La diffraction laser, l’analyse automatisée des images, la fluorescence des rayons X (XRF) et la diffraction des rayons X (XRD) sont quatre techniques analytiques clés qui sont couramment utilisées pour caractériser les poudres de fabrication additive. »
La diffraction laser est intéressante pour mesurer la distribution granulométrique des poudres de métal, de céramique et de polymère pour la fabrication additive. Dans les procédés de fusion en lit de poudre, la distribution de la taille des particules affecte le tassement du lit de poudre et la fluidité, ce qui a un impact sur la qualité de fabrication et les propriétés finales des composants. L’utilisation d’un procédé de diffraction laser permet d’obtenir la distribution granulométrique en quelques minutes en utilisant des techniques de dispersion humide ou sèche.
« L’analyse automatique d’images statiques peut être utilisée pour classer et quantifier la taille et la forme des poudres de métal, de céramique et de polymère en combinant des mesures de taille de particules telles que la longueur et la largeur, avec des évaluations de forme de particules telles que la circularité et la convexité sur un échantillon statistiquement représentatif (>10 000 particules) », explique Malvern Panalytical.
Enfin, si la radiographie par fluorescence X aide les spécialistes des matériaux à déterminer la composition élémentaire des alliages métalliques et à détecter la présence de contaminants ou d’inclusions, elle fournit des informations sur les caractéristiques micro-structurelles qui peuvent être influencées par les processus thermiques et mécaniques.
En résumé, le développement des machines de FA est un domaine d’intérêt important car la technologie est continuellement adaptée pour fournir des débits plus élevés. Cependant, les propriétés des poudres utilisées occupent une place de plus en plus importante dans la stratégie de production. La caractérisation des matériaux n’est que le début de l’histoire. #RestezConnectés