Les applications de la fabrication additive métal sont remplies d’exemples impliquant l’utilisation de titane, d’inconel et, récemment, de cuivre pur. Alors que nous explorons la prochaine phase de croissance de ce segment, nous devons considérer l’aluminium et les alliages d’aluminium comme la gamme de matériaux sur laquelle les utilisateurs de la fabrication additive peuvent capitaliser. Le seul problème est que les avantages que l’on peut tirer du traitement des alliages d’aluminium par FA sont sous-estimés, voire négligés, et le plus étrange, c’est que je comprends pourquoi.
Cela fait des siècles que l’aluminium et les alliages d’aluminium répondent aux besoins d’industries telles que l’aérospatiale, l’automobile ou l’emballage, en raison de leurs propriétés mécaniques : rapport résistance/poids élevé, malléabilité, conductivité électrique, résistance à la corrosion et recyclabilité. La transformation de ces matériaux a longtemps été associée à des procédés de fabrication conventionnels tels que le moulage, le formage de la tôle ou l’usinage.
« Il existe d’excellentes options pour fabriquer des pièces en aluminium de haute performance. Par exemple, les alliages d’aluminium peuvent être usinés beaucoup plus facilement que d’autres métaux (titane, aciers inoxydables…). Nous pouvons couler l’aluminium dans des formes complexes, nous pouvons former des tôles pour en faire des canettes de boisson ou des panneaux de carrosserie automobile. De nombreux procédés d’assemblage existent (soudage, brasage, assemblage mécanique, collage…) et bien sûr, l’aluminium est recyclable à l’infini. C’est pourquoi l’aluminium est le matériau de choix dans de nombreuses applications d’emballage et de transport, en particulier lorsque la légèreté et/ou le recyclage sont des facteurs déterminants », a déclaré Alireza ARBAB, responsable de la fabrication additive chez Constellium, à 3D ADEPT Media.
En outre, si on considère les coûts, l’aluminium est moins cher que le cuivre, l’acier inoxydable, le titane et d’autres métaux – même si sa forme brute a tendance à coûter plus cher que les qualités courantes d’acier à faible teneur en carbone et d’acier faiblement allié.
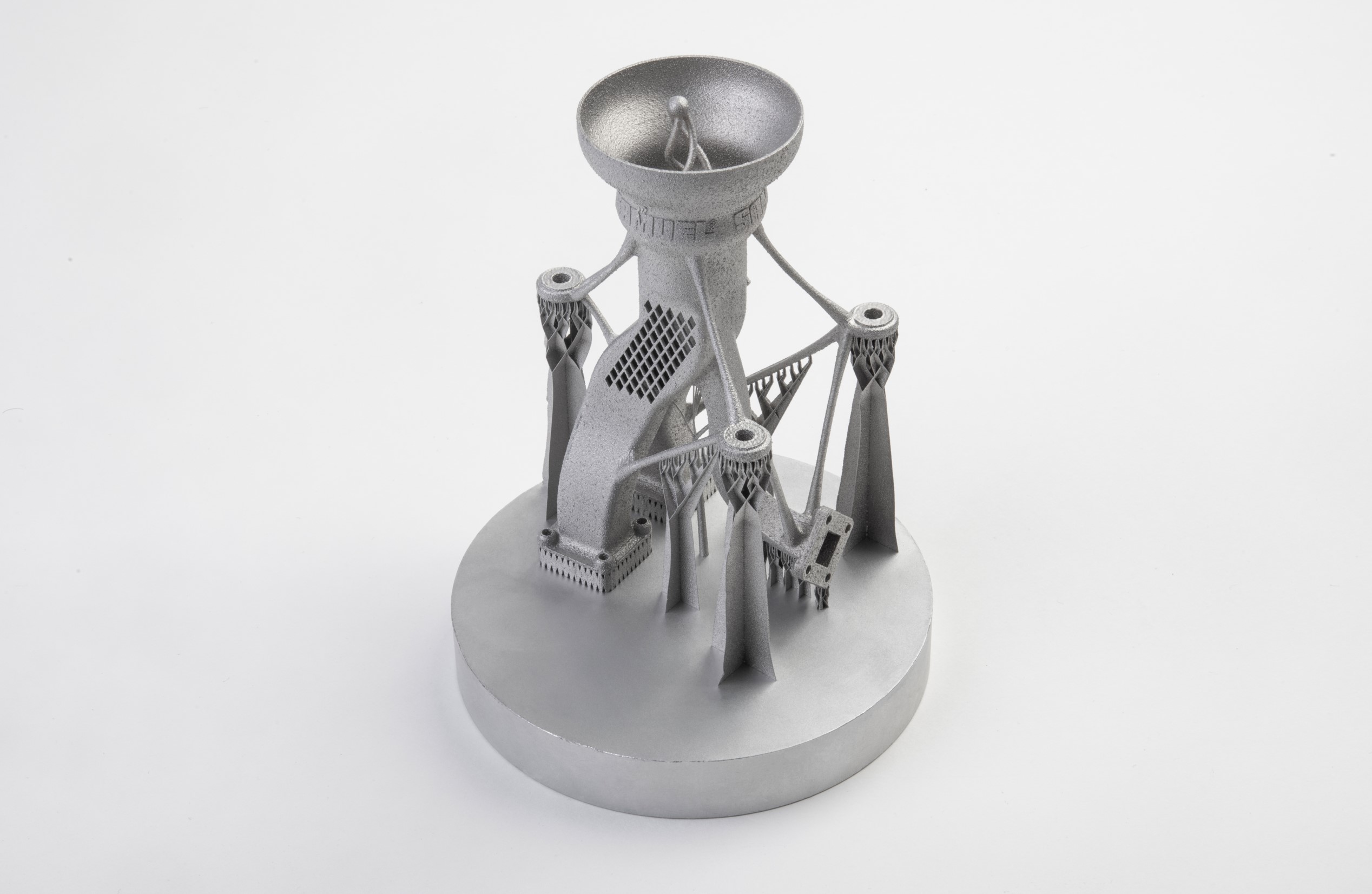
Ces propriétés favorables et ces considérations de coût ont suscité l’intérêt des utilisateurs de la FA et des fournisseurs de solutions de FA qui ont commencé à explorer comment ils pouvaient combiner ces avantages avec ceux de la FA, offrant ainsi une autre option de fabrication aux industries verticales qui adoptent la FA.
L’article ci-dessous vise à comprendre les opportunités et les défis de la FA aluminium. Pour ce faire, il mettra l’accent sur les points suivants :
Tout d’abord, l’aluminium ou les alliages d’aluminium ?
Les différentes technologies de FA qui peuvent traiter l’aluminium : l’accent est mis sur le procécdé LPBF et sur un processus de fabrication spécialement conçu pour les composants en aluminium.
Les applications de FA qui stimuleront l’utilisation des alliages d’aluminium dans le segment de la FA des métaux.
Et les considérations à prendre en compte pour explorer la voie de la durabilité.
1- D’abord, l’aluminium ou les alliages d’aluminium ?
Si vous êtes nouveau dans l’industrie des matériaux, une question peut légitimement vous venir à l’esprit : pourquoi utilise-t-on des alliages d’aluminium plutôt que de l’aluminium pur ? La réponse varie évidemment d’une application à l’autre, mais il convient de noter que pour la plupart des applications industrielles, l’aluminium pur est souvent considéré comme coûteux, trop mou et trop faible pour servir de matériau structurel – en dépit de ses nombreuses propriétés gagnantes.
À notre connaissance, Elementum3D, basé aux États-Unis, et m4p (metals 4 printing), basé en Allemagne, sont les deux producteurs de matériaux qui ont réussi à développer des poudres d’aluminium pur pour le procédé L-PBF.
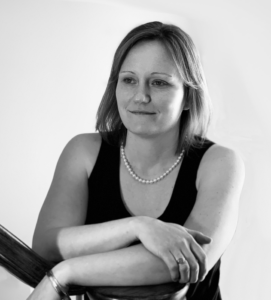
« L’aluminium est presque toujours allié et traité thermiquement ou trempé pour augmenter sa résistance. L’alliage dépend de l’application. Le moulage et le procédé PBF nécessitent tous deux la fusion et l’écoulement ; ils présentent donc généralement des niveaux élevés de silicium et les pièces qui en résultent sont sujettes à la porosité. Cela réduit la résistance des pièces. Le processus de forgeage des tôles d’Alloy ne nécessite pas de fusion ou de coulée, ce qui permet d’obtenir une plus grande variété d’alliages d’aluminium et d’éviter le problème de la porosité. Notre premier alliage est le 6061 – entièrement dense », explique Alison Forsyth, CEO d’Alloy Enterprises.
De plus, l’aluminium peut être allié à de nombreux autres éléments pour surmonter sa faible résistance. Selon Arbab, l’aluminium peut être combiné avec des éléments tels que le magnésium, le zinc, le cuivre, le silicium, le manganèse, pour n’en citer que quelques-uns. L’essentiel est de pouvoir concevoir les alliages d’aluminium adaptés aux différents marchés et processus de production.
2- Les différentes technologies de FA qui peuvent traiter l’aluminium et les alliages d’aluminium
Parmi la vaste gamme de procédés de FA disponibles sur le marché, vous ne serez peut-être pas surpris de lire que la fusion sur lit de poudre (PBF = Powder Bed Fusion) est le procédé le plus utilisé pour l’aluminium. Parmi les autres procédés figurent le WAAM, la projection de liant, le procédé DED, l’EBAM et le Kinetic. Chacune de ces technologies peut traiter un type spécifique d’alliages d’aluminium.
Par rapport à d’autres métaux, la réflectivité élevée vis-à-vis de la longueur d’onde typique des lasers à fibre, la conductivité thermique élevée et la tendance à se fissurer pendant la solidification sont des éléments qui rendent difficile le traitement de l’aluminium par un procédé à faisceau laser. C’est pourquoi les alliages de coulée conventionnels tels que AlSi10Mg et AlSi12 ont été principalement utilisés pour le procédé LPBF. Ils sont relativement faciles à traiter par rapport aux alliages d’aluminium à haute résistance.
Parmi les procédés susmentionnés, la fusion sur lit de poudre par faisceau laser (LPBF) et le dépôt d’énergie dirigée (DED) peuvent utiliser un faisceau laser, ce dernier pouvant utiliser une poudre ou un fil comme matière première.
Concentrons-nous quelques instants sur la fusion laser sur lit de poudre.

Le responsable de FA de Constellium a déclaré à 3D ADEPT Media que « les nombreux alliages développés pour les applications existantes ne sont pas optimisés pour la production à l’aide des technologies de FA, en particulier la fusion laser sur lit de poudre (LPBF) ». Pour l’expert, il est nécessaire d’avoir une vue d’ensemble pour comprendre le processus complet – de la gestion des poudres aux pièces finales, en passant par l’impression, le post-traitement et le contrôle qualité – et les domaines qui peuvent nécessiter des points d’intérêt spécifiques.
« Notre alliage Aheadd® CP1 [un matériau spécialement conçu pour la FA] utilise l’avantage de la vitesse de solidification extrêmement rapide du procédé LPBF, ce qui permet à Constellium d’utiliser des règles de conception d’alliage spécifiques pour créer une solution bien meilleure. À titre d’exemple, le CP1 contient 1 % de fer en tant qu’élément d’alliage clé. Dans la plupart des alliages d’aluminium, l’alliage de fer est limité en tant qu’impureté », souligne-t-il.
Par ailleurs, outre la forte réflectivité et la faible absorption du laser qui peuvent entraîner des défauts, les propriétés de certains alliages d’aluminium peuvent également entraîner des défauts tels que la porosité, les fissures, un mauvais état de surface, le retrait, l’oxydation et les contraintes résiduelles.
En outre, chaque imprimante 3D est dotée d’un ensemble de paramètres uniques. Cela signifie qu’un problème observé sur la machine X n’est pas nécessairement le même que celui observé sur la machine Y.
Parmi les solutions qui peuvent être explorées pour surmonter ces défauts, on note l’utilisation d’additifs, la puissance du laser, la numérisation et le séchage des poudres.
Des chercheurs de l’Université norvégienne des sciences et technologies expliquent dans une recherche que la catégorie « additifs » fait référence à des solutions qui incluent l’ajout d’additifs à la poudre d’alliage d’aluminium ou à de nouveaux alliages. Cela signifie que des mélanges d’alliages peuvent être créés pour améliorer les propriétés souhaitées. La puissance du laser fait référence à des solutions où il est proposé d’augmenter ou de diminuer la puissance du laser. Cette solution est souvent associée à d’autres solutions telles que la modification de la vitesse de numérisation. La catégorie numérisation comprend des solutions où les paramètres de numérisation sont modifiés, comme la modification de la vitesse de numérisation ou l’exécution d’une double numérisation. Avec le séchage des poudres, il est possible de pré-sécher la poudre d’alliage d’aluminium avant de la faire fondre.
Et si nous envisagions un processus spécifiquement conçu pour les pièces en aluminium ?

Alison Forsyth nous a ouvert les yeux sur une nouvelle façon de fabriquer des pièces et des matériaux en aluminium grâce à la fabrication à grande vitesse. Pour Alison Forsyth, l’aluminium est différent des autres métaux car il « forme une couche d’oxyde robuste en quelques millisecondes ». Il est donc difficile de le coller ou de l’imprimer, en particulier dans les processus présentant un rapport surface/volume élevé, qui maximise la quantité d’oxyde. Le processus de forgeage de feuilles d’Alloy a été conçu pour surmonter ce défi.
Parlant de leur processus de forgeage de tôle, elle a expliqué que « Alloy Enterprises transforme la façon dont les composants en aluminium sont fabriqués. Alloy fabrique des composants en aluminium entièrement denses, ce qui permet à ses clients de passer du prototype à la production. Contrairement aux procédés de fabrication additive à base de poudre, le processus de forgeage de tôles d’Alloy est à haut débit et produit des composants aux propriétés matérielles supérieures. Le processus commence par le découpage numérique du composant 3D en couches discrètes. Les couches sont ensuite découpées au laser dans les matières premières personnalisées d’Alloy et un agent inhibiteur est appliqué de manière sélective pour créer des supports in situ. La pile complète de feuilles enregistrées est ensuite collée par diffusion. Enfin, les pièces sont retirées du bloc et soumises à un traitement thermique. Le processus d’Alloy offre la flexibilité des propriétés des matériaux corroyés et la complexité géométrique de la fabrication additive pour produire des composants légers avec une résistance, une durabilité et une conductivité thermique optimales ».
Nous ne connaissons pas encore les limites de ce procédé, mais s’il fonctionne bien, il pourrait apporter un avantage significatif en termes de vitesse par rapport au procédé LBPF, puisqu’il n’a pas besoin de se déplacer point par point dans l’ensemble de la zone.
3- Les applications de FA qui stimuleront l’utilisation des alliages d’aluminium
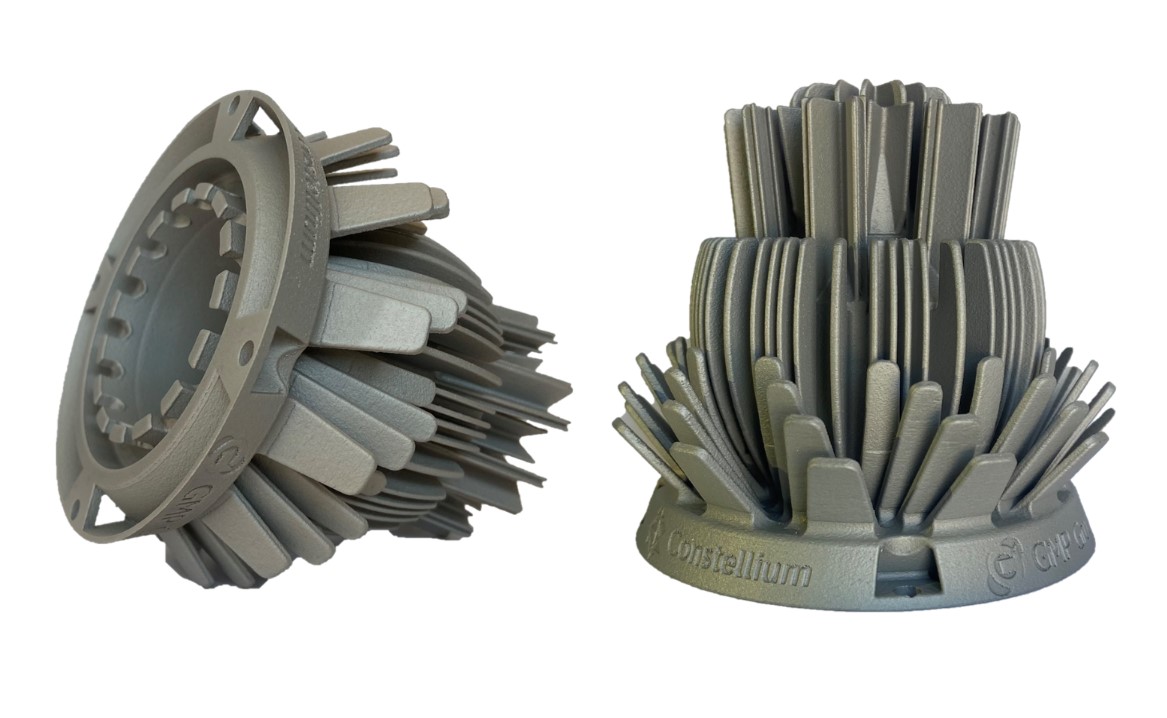
Parmi les industries verticales mentionnées ci-dessus, l’une d’entre elles pourrait voir l’utilisation croissante des alliages d’aluminium : l’industrie des véhicules électriques. Plus les véhicules électriques seront développés, plus les équipementiers de ce secteur auront besoin de matériaux solides et légers tels que l’aluminium.
Selon le CEO d’Alloy Enterprises, l’aluminium fera partie du parcours d’électrification de tout ce qui bouge, et la fabrication flexible à la demande et à des coûts compétitifs sera essentielle à cette transition. À propos de leur processus de forgeage de tôles, elle explique : « Le processus de forgeage de tôles d’Alloy peut être utilisé pour l’automobile, les véhicules électriques, les équipements lourds et industriels. En outre, certains alliages d’aluminium ont une conductivité thermique élevée par rapport à leur poids. Les applications de refroidissement et de gestion thermique, à mesure que nous embarquons davantage de batteries ou d’électronique dans les véhicules, les machines et les ordinateurs, continueront à favoriser l’adoption du procédé de forgeage de tôles d’Alloy. »
Pour Arbab, il existe déjà de nombreuses applications passionnantes créées par la technologie LPBF qui peuvent être réalisées avec des alliages d’aluminium. Il s’agit, par exemple, des composants de satellites, de la défense, des échangeurs de chaleur et des pièces automobiles haut de gamme.
« À mesure que les coûts diminuent et que les concepteurs prennent conscience des nouvelles possibilités offertes par des alliages spécifiques tels que le matériau Aheadd® CP1, nous recevons déjà de nombreuses demandes d’études d’application. Nous recevons déjà de nombreuses demandes d’études d’application dans des domaines tels que les pièces de rechange à la demande, les applications de l’industrie des semi-conducteurs… L’activité actuelle n’est que la partie émergée de l’iceberg », ajoute-t-il.
4- Quelles sont les considérations à explorer sur la voie de la durabilité ?

À l’heure actuelle, outre la réutilisation des poudres, on constate que les producteurs de matériaux se concentrent principalement sur les facteurs de durabilité inhérents au processus de fabrication de leurs matériaux.
Forsyth a expliqué à 3D ADEPT que la matière première utilisée dans le processus de forgeage en feuille d’Alloy a été conçue pour réduire les émissions de carbone de 15 fois par rapport à la poudre.
Les déchets issus du processus de forgeage de feuilles peuvent être réutilisés sans nécessiter de processus de recyclage coûteux et gourmands en énergie.
De même, la poudre de Constellium peut être recyclée plusieurs fois dans les machines de FA, sans aucune limite physique. Arbab a indiqué que l’équipe travaillait actuellement à l’optimisation du rendement, de la qualité et du recyclage de la production de poudre avec sa ligne pilote d’atomiseurs à l’Institut de recherche et de technologie IRT M2P, dans le nord de la France, qui est entièrement dédié à l’optimisation des processus de production, y compris le recyclage.
Cela dit, la compréhension du cycle de vie complet d’un matériau est probablement la première étape à franchir pour les entreprises qui cherchent à fabriquer des produits plus durables, ce qui devrait faire l’objet d’un autre article.
Ce dossier a été initialement publié dans le numéro de Septembre/Octobre de 3D ADEPT Mag.