La production de pièces en cuivre imprimées en 3D bénéficie d’un nouveau souffle grâce à la société de gaz et d’ingénierie Linde qui présente les capacités de sa solution d’alimentation en gaz ADDvance® Laser230 au salon Formnext 2023.
Présentée l’année dernière à Formnext, la solution d’alimentation en gaz ADDvance® Laser230 optimise l’impression 3D de cuivre en résolvant des problèmes clés au niveau de la fabrication de pièces dans des industries hautement réglementées. La société présente également son laboratoire d’essai d’atomisation des poudres et ses solutions d’alimentation en gaz pour la pulvérisation à froid de nouvelle génération à l’occasion de l’événement de Francfort.
La solution d’alimentation en gaz ADDvance® Laser230
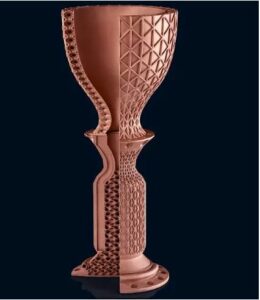
Le système ADDvance® Laser230 développé par Linde utilise une intensité laser plus élevée qui ne peut pas être perturbée par la propriété réfléchissante du cuivre, évitant ainsi la perte de puissance dans le processus de fabrication additive.
Le nouveau mélange gazeux est doté d’un système de contrôle de l’oxygène appelé ADDvance® O2 precision, développé en collaboration avec Ariane, qui permet de fabriquer des pièces imprimées 3D en cuivre de haute qualité de manière constante. Les deux entreprises ont récemment annoncé qu’elles travaillaient à l’amélioration de l’impression 3D du cuivre pour les futures fusées spatiales.
Au cœur de leur collaboration se trouve l’ADDvance Laser230, qui a permis d’optimiser les résultats d’impression dans le processus de fusion laser sur lit de poudre (LPBF). Grâce à son mélange d’argon et d’hélium, il permet d’atténuer la formation de fumées et d’éclaboussures et d’accélérer les temps de cycle, ce qui rend le processus d’impression plus fiable et réduit le coût par pièce. Il est indépendant des alliages et idéal pour la fabrication additive de structures complexes ou en treillis.
L’ajout d’ADDvance O2 precision dans le processus d’impression garantit qu’un niveau d’oxygène maximum aussi bas que 10 ppm ne subsistera que dans la chambre d’impression. Ce niveau d’oxygène résiduel extrêmement bas garantit que la surchauffe et l’oxydation sont atténuées, ce qui permet une impression plus efficace, sans qu’il soit nécessaire d’attendre que les couches refroidissent. L’avantage supplémentaire est que la poudre non oxydée peut être réutilisée, ce qui réduit les coûts des matériaux.
« Pour garantir la compétitivité des futurs moteurs de lanceurs, l’amélioration des processus de fabrication additive est un facteur clé, permettant de réduire les coûts de fabrication et d’améliorer les délais tout en maintenant la qualité et la fiabilité non négociables qui ont fait d’Ariane un leader de l’industrie« , a déclaré Mathias Palm, spécialiste des processus, Ariane Group. « Nous sommes convaincus que l’expertise de Linde en matière de gaz contribuera à optimiser le processus de fabrication additive. »
Atomisation de gaz chauds et démonstration d’un banc d’essai atomique
L’entreprise a également fait la démonstration de sa technologie d’atomisation par gaz chauds à l’aide d’un objet 3D qui montre comment le système fonctionne en injectant une pression élevée dans les buses tout en produisant des poudres métalliques. Le processus peut être accéléré pour créer des poudres plus fines si un réchauffeur de gaz augmente la température à plusieurs centaines de degrés, ce qui accélère le mouvement du gaz à travers la buse. Cette installation est souvent équipée de solutions d’alimentation en gaz et de panneaux de commande Linde pour obtenir de meilleurs résultats.
Grâce au banc d’essai d’atomisation, Linde a obtenu une conception de buse et des paramètres de gaz « réels » qui améliorent l’atomisation des poudres métalliques, grâce à des fenêtres, des éclairages, des caméras à grande vitesse et des images schlieren spécialement adaptés (au cas où vous ne le savez pas, la photographie Schlieren est un procédé visuel utilisé pour photographier l’écoulement de fluides de densité variable). Cela permet une meilleure surveillance et une meilleure saisie des données de chaque changement de paramètre gazeux, car le banc d’essai repose sur la structure gazeuse de l’atomisation et non sur le métal en fusion. En quelques minutes, des centaines de combinaisons de paramètres tels que la pression, la température, le volume et le type de gaz peuvent être vérifiés par l’atomiseur.
Autres systèmes présentés
La société présente également la solution d’alimentation en gaz LINSPRAY® Connect, lancée en mars, qui améliore la sécurité du processus de pulvérisation à froid grâce à un flux de gaz de haute qualité avec une variation minimale. Grâce à cette technologie, les entreprises d’AM peuvent surveiller les paramètres du processus de fabrication additive, notamment le niveau du réservoir d’azote, la température et la pression.
L’entreprise met également en avant la solution d’alimentation en gaz LINSPRAY® Connect, lancée en mars, qui renforce la sécurité du processus de pulvérisation à froid grâce à un flux de gaz de haute qualité avec une variation minimale. Grâce à cette technologie, les entreprises de fabrication additive peuvent surveiller les paramètres du processus de fabrication additive, notamment le niveau du réservoir d’azote, la température et la pression.
La solution ADDvance® Sinter250 de Linde, qui optimise les atmosphères de frittage pour prévenir l’oxydation dans la modélisation par dépôt de métal fondu (FDM), est également présentée au salon Formnext. Ce système garantit l’intégrité structurelle et la résistance des pièces imprimées en 3D en acier inoxydable grâce à un contrôle avancé de l’atmosphère créé à partir de mélanges d’argon et d’hydrogène.
Les passionnés de l’industrie de la FA peuvent visiter le stand C82 dans le hall 11 où Linde présente ses solutions d’approvisionnement en gaz.
N’oubliez pas que vous pouvez poster gratuitement les offres d’emploi de l’industrie de la FA sur 3D ADEPT Media ou rechercher un emploi via notre tableau d’offres d’emploi. N’hésitez pas à nous suivre sur nos réseaux sociaux et à vous inscrire à notre newsletter hebdomadaire : Facebook, Twitter, LinkedIn & Instagram !