La plupart du temps, lorsqu’une entreprise dit qu’elle développe une technologie d’impression 3D, on pense directement au « développement d’une imprimante 3D ». C’est l’erreur que nous avons commise lorsque nous avons entendu parler de Headmade Materials et de la manière intrigante dont ils ont fabriqué cette pédale en métal imprimée en 3D. Headmade Materials n’est pas un fabricant d’imprimantes 3D, pourtant, la technologie d’impression 3D que la société développe est l’une des plus intéressantes que nous ayons jamais vues sur ce marché – pour la production de matériaux.
Cette technologie est appelée Cold Metal Fusion (CMF) – un concept qui est né lorsque les cofondateurs travaillaient encore dans un institut local de recherche sur les polymères, Das Kunststoff-Zentrum (SKZ). L’histoire a commencé il y a environ cinq ans avec les cofondateurs Christian Staudigel et Christian Fischer.
Certains diront que c’est de la chance, mais on aime penser que le dévouement à leur projet – qui portait à l’époque sur le traitement des hauts polymères et le procédé de frittage laser -, le travail et, surtout, les performances de leur technologie ont permis de faire passer rapidement le concept du stade de la R&D à celui de la commercialisation – en moins de cinq ans.
« Nous avions déjà une très bonne première impression après la première expérience, lorsque nous avons obtenu une densité élevée de 96 %. Mais il a fallu un mois pour approfondir le marché et découvrir les difficultés et les avantages des clients potentiels. Après avoir trouvé assez facilement des clients pilotes plus importants, nous avons réalisé que notre procédé répondait vraiment à une demande du marché« , nous dit Staudigel au milieu d’une conversation.
Alors, quel est ce concept qui permet d’atteindre une densité élevée de 96 % des pièces?
La technologie Cold Metal Fusion est une technologie d’impression 3D basée sur le frittage qui permet d’imprimer des pièces métalliques. Conçue pour la production en série, cette solution combine les mondes du SLS avec les processus standard de la métallurgie des poudres pour le déliantage et le frittage et peut aider les fabricants à réaliser plus de 100 000 pièces/an.
« Dans notre technologie de fusion métal à froid, notre matériau d’alimentation unique, composé de poudre métallique et de liant, est traité sur des machines de frittage laser pour polymère afin d’obtenir une pièce verte. Ensuite, la pièce verte est découennée et frittée en pièces métalliques complexes selon des procédés standard de métallurgie des poudres« , explique notre invité dans cette Opinion de la semaine.
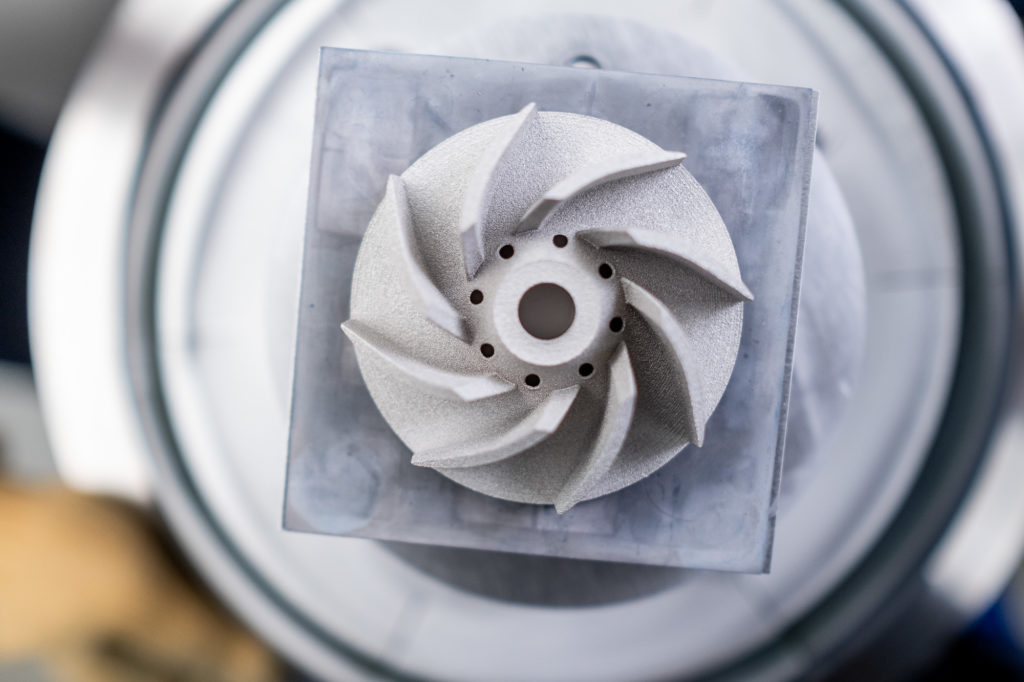
Ce qui est particulièrement intéressant ici, c’est que le SLS et la métallurgie des poudres ont tous deux fait leurs preuves en termes de qualité dans les opérations de fabrication. Pourtant, l’équipe de Headmade Materials a trouvé un moyen d’améliorer et de combiner les deux méthodes en intégrant un matériau de base au jeu, qui ne nécessite aucun autre processus ou ajustement des machines. Dans cette optique, l’un des tout premiers avantages que l’on peut attendre est la disponibilité d’un large éventail d’options de matériaux. En fait, l’acier inoxydable 316L, le cobalt-chrome, le titane Ti6Al4V, le titane CP-Ti Grade 1 et les alliages de tungstène sont déjà disponibles dans le portefeuille de Headmade. L’acier inoxydable 17-4PH, l’acier à outils à haute dureté sans post-traitement thermique, l’alliage de cuivre pour une conductivité thermique et électrique élevée ainsi que le super alliage devraient suivre dans les semaines ou mois à venir.
Même si la plupart de leurs expériences sont réalisées sur des machines EOS Formiga P110 et Sintratec S2 qu’ils possèdent en interne, le directeur général explique que la production de pièces métalliques imprimées en 3D peut être réalisée sur un large éventail de systèmes de frittage laser. En outre, aucune plaque de construction ni structure de support n’est nécessaire pour le processus d’impression 3D, comme c’était le cas pour les processus de fusion à lit de poudre.
D’autres caractéristiques susceptibles de susciter l’intérêt des fabricants pour cette technologie sont la compatibilité du procédé avec les processus de déliantage et de frittage du MIM, sa capacité à permettre une faible température de traitement, ce qui permet d’économiser du temps de chauffage et de l’énergie et de supprimer la nécessité d’un traitement thermique ultérieur après impression, ainsi que les caractéristiques des pièces (en termes de densité, de limite d’élasticité, de résistance à la traction, d’allongement) auxquelles il peut répondre.
« La densité obtenue par le procédé de fusion froide des métaux dépend du matériau, du processus d’impression et de frittage, mais elle est généralement supérieure à 97 % pour l’acier inoxydable 316L et peut atteindre 100 % pour les alliages en phase liquide. En optimisant les étapes du processus pour chaque pièce métallique, des densités reproductibles allant jusqu’à 99 % sont possibles« , explique la société.
Même si le nombre de pièces pouvant être fabriquées par lot dépend de la taille de la pièce et de la taille de la machine, Staudigel assure que « l’une des caractéristiques les plus intéressantes de [sa] technologie est sa facilité d’adaptation« .
Du point de vue des applications, la technologie CMF peut cibler à la fois les opérateurs de l’industrie de la métallurgie des poudres et ceux de l’impression 3D. Cela signifie que toutes les industries verticales telles que les secteurs médical, automobile, aérospatial et industriel, qui adoptent habituellement les technologies de FA, peuvent trouver dans la solution d’Headmade Materials une proposition à valeur ajoutée.
D’un point de vue financier, le porte-parole d’Headmade Materials note que sa technologie reste « moins chère que la SLM. Cependant, par rapport à la SLS où l’opérateur obtient des pièces en plastique à la fin, elle reste une alternative intéressante, notamment pour ceux qui cherchent à passer des prototypes et des très petites séries à des quantités plus importantes. »
« Notre procédé CMF est davantage un complément au SLM qu’une alternative directe. Nous fournissons aux industries une approche basée sur le frittage qui offre les avantages de l’impression SLS. Le spectre des pièces ainsi que le domaine d’utilisation sont généralement très différents de ceux du SLM. En fin de compte, notre technologie offre une alternative de meilleure qualité et plus économique que les technologies Binder Jetting« , rappelle-t-il.
Quelles sont les prochaines étapes ?
La société a obtenu l’an dernier un financement de 1,9 million d’euros par l’intermédiaire de la société de capital-risque btov Partners et cherche maintenant à développer son activité.
« Nous avons commencé avec deux personnes il y a deux ans et nous avons maintenant une équipe de 10 personnes. Nous nous développons rapidement et nous devons continuer à nous développer. D’un point de vue technique, nous allons lancer dans les semaines à venir de nouveaux alliages, de nouvelles caractéristiques de produits qui sont uniques dans le secteur de l’impression 3D« , conclut Staudigel.
N’oubliez pas que vous pouvez poster gratuitement les offres d’emploi de l’industrie de la FA sur 3D ADEPT Media ou rechercher un emploi via notre tableau d’offres d’emploi. N’hésitez pas à nous suivre sur nos réseaux sociaux et à vous inscrire à notre newsletter hebdomadaire : Facebook, Twitter, LinkedIn & Instagram !