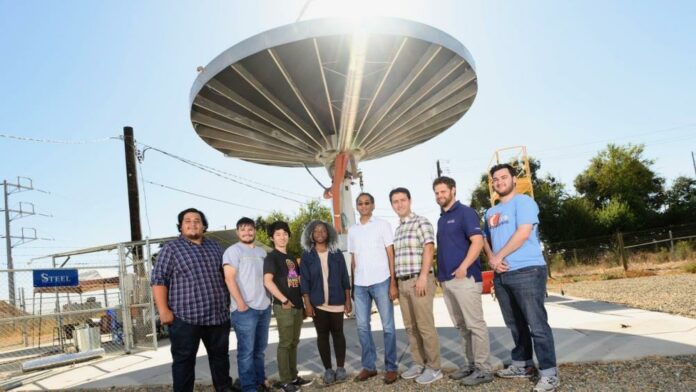
Si l’exploitation de l’énergie solaire est la clé d’un monde décarboné, parvenir à ces températures élevées nécessaires à l’industrie est souvent le Saint Graal des industriels. Pour les atteindre, ils doivent utiliser soit de l’électricité issue de sources renouvelables, soit de l’énergie solaire à haute température.
Dans le cadre d’un projet multi-institutionnel de trois ans, d’un montant de 4,6 millions de dollars, financé par le ministère américain de l’énergie (DOE), le professeur de génie mécanique et aérospatial Vinod Narayanan explorera des alternatives vertes comme l’énergie solaire thermique pour capturer l’énergie tout en diminuant l’empreinte carbone.
Il existe deux façons de capter l’énergie du soleil : l’utilisation de cellules solaires traditionnelles, appelées photovoltaïques, et la concentration de l’énergie solaire thermique. L’énergie solaire thermique utilise des miroirs pour concentrer la lumière du soleil sur un récepteur, qui transfère l’énergie à un fluide de travail à haute température pouvant générer de la chaleur industrielle ou faire fonctionner un cycle électrique. Cette méthode peut être associée à un stockage thermique moins coûteux pour fournir de l’électricité ou de la chaleur industrielle même la nuit. Elle est idéale pour les endroits qui reçoivent beaucoup de lumière directe du soleil, comme le sud-ouest des États-Unis, le Moyen-Orient, l’Afrique du Nord et l’Europe du Sud.
Dans le cadre de ce nouveau projet, Narayanan et son équipe développeront des récepteurs haute température et haute pression imprimés en 3D qui pourront être utilisés pour produire de l’électricité ou de la chaleur industrielle renouvelable. Ses collaborateurs sont quatre autres universités – l’université Carnegie Mellon, l’université d’État de Pennsylvanie, l’université du Michigan et l’université d’État de l’Utah -, trois entreprises – Sunvapor Inc, Materials Resources LLC et AMETEK Specialty Metal Products – et Sandia National Laboratories.
Pour construire un récepteur, l’équipe a besoin d’un objet capable de résister à des températures et à des pressions extrêmement élevées, ainsi qu’aux flux et aux transitoires extrêmes qui se produisent lorsque le soleil se lève et se couche chaque jour. Elle a également besoin d’un récepteur qui transfère autant d’énergie que possible à un fluide de travail.
« Vous pouvez penser à prendre la lumière du soleil que vous recevez un jour d’été et à la concentrer 1000 fois », a déclaré Narayanan. « Si vous la concentrez sur une zone de quelques centimètres et que vous n’avez pas de mécanisme pour évacuer la chaleur, vous pouvez brûler l’acier. Le but du récepteur est de prendre cette chaleur et de la transférer à un fluide de travail qui peut faire quelque chose avec cette chaleur – soit le chauffage du processus, soit la production d’énergie. »
La fabrication additive métal, un procédé de fabrication crucial pour le projet
La fabrication d’un récepteur par fabrication additive métal est un élément clé du projet. En raison de la chaleur élevée, Narayanan explique que les techniques traditionnelles de gravure, de diffusion et de collage ne tenaient pas sur les conceptions précédentes, et que les dispositifs échouaient souvent ou se dégradaient rapidement. La fabrication additive, communément appelée impression 3D, est une solution potentielle.
« Avec la fabrication additive, vous pouvez tout construire en une seule fois, de sorte que vous n’avez pas besoin de faire des choses comme le soudage ou le brasage pour construire le composant », a déclaré Narayanan. « Cela vous aide également en termes de longévité, de fluage et de fatigue du récepteur, de sorte que vous limitez le nombre de points de défaillance. »
« La fabrication additive permet une liberté de conception, l’utilisation de matériaux avancés, la consolidation des pièces et une rotation rapide de la conception à la fabrication de la forme nette, en plus des échangeurs de chaleur qui sont prêts à être testés avec un minimum de post-traitement supplémentaire », a ajouté Tony Rollett, le chercheur principal de l’université Carnegie Mellon pour le projet.
En cas de succès, il espère s’associer à ses collègues du College of Engineering pour coupler son récepteur à de nouvelles méthodes de stockage thermique afin de décarboniser davantage l’industrie et de rendre ces méthodes viables pour l’industrie dans de nouvelles régions du monde.
N’oubliez pas que vous pouvez poster gratuitement les offres d’emploi de l’industrie de la FA sur 3D ADEPT Media ou rechercher un emploi via notre tableau d’offres d’emploi. N’hésitez pas à nous suivre sur nos réseaux sociaux et à vous inscrire à notre newsletter hebdomadaire : Facebook, Twitter, LinkedIn & Instagram !