L’édition 2021 de Formnext marque la septième année du rassemblement international du monde de la fabrication additive à Francfort, en Allemagne. Organisé chaque année pendant la deuxième ou la troisième semaine de novembre – avec une année sautée en 2020 – Formnext s’est fixé comme priorité de présenter une série de premières mondiales tout au long de la chaîne de processus et de démontrer les champs d’application toujours plus vastes de la fabrication additive.
Cette édition 2021 en présentiel de Formnext, qui s’est tenue du 16 au 19 novembre, était attendue depuis longtemps et a été organisée avec toute l’incertitude qui entoure le paysage de Covid-19 – l’incertitude d’être annulé à la dernière minute. L’événement s’est finalement déroulé dans les conditions de sécurité les plus strictes (2G), ce qui signifie que seules les personnes entièrement vaccinées contre le COVID-19 ou guéries de cette maladie ont été autorisées à y participer.
Plus important encore, cette édition était attendue depuis longtemps, car l’ensemble du secteur a pris conscience que les événements virtuels ne suffisent pas pour faire des affaires.
C’est la raison pour laquelle l’un des premiers points forts de cette édition était « les gens« .
Les gens : « Voir ou être vu »
Avec plus de 600 exposants de 36 pays, couvrant une surface totale de 30 000 mètres carrés, Formnext 2021 a accueilli 17 859 spécialistes et dirigeants de 76 nations.
Ce nombre équivaut peut-être à la moitié des visiteurs qui ont assisté au salon en 2019, mais il reste l’un des plus hauts niveaux de fréquentation observés dans les événements industriels dédiés à la FA. En fait, la plupart des exposants ont déclaré à 3D ADEPT Media, qu’ils ne s’attendaient pas à avoir une telle foule compte tenu du nombre croissant de cas de Covid-19 en Allemagne.
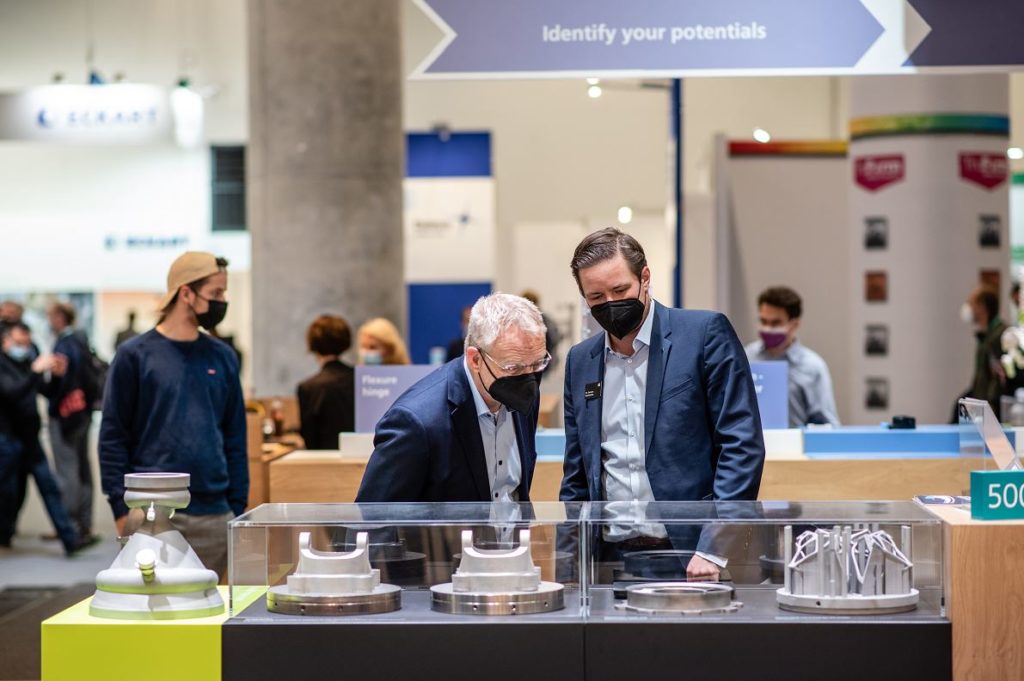
« Formnext s’est une fois de plus révélé être le point culminant de l’année pour l’industrie de la FA. Après les défis importants auxquels nous avons été confrontés l’année dernière, le nombre d’exposants et de visiteurs présents cette année a dépassé nos attentes », a commenté Sascha F. Wenzler, vice-président de Formnext chez l’organisateur Mesago Messe Frankfurt GmbH. « Cela a montré une fois de plus à quel point Formnext et les rencontres en face à face sont importants pour cette industrie innovante, qui développe des technologies à un rythme rapide et tient à les partager avec des investisseurs, des partenaires et des clients. Il était clair que Formnext était attendu avec impatience par l’ensemble du secteur. »
Tout en soulignant le sentiment d’appartenance à une communauté que l’événement crée au sein de l’industrie, que ce soit du point de vue des exposants ou des visiteurs, les diverses activités organisées à Francfort soulignent également la nécessité pour les gens de réseauter et de mieux connaître d’autres professionnels de l’industrie dans le cadre d’une gamme d’expériences très sophistiquées. Ces activités ont incluent cette année, par exemple, le très sélect walking dinner d’AM Ventures qui s’est tenu le mardi, la fête d’AMT, ou encore le happy hour de Formnext qui a eu lieu le jeudi. Et ce ne sont là que les cerises sur le gâteau… Si on ajoute à cela les diverses fêtes organisées par les exposants sur les stands où ils étaient situés, d’autres attractions marketing destinées à attirer l’attention des foules, et les sous-événements de Formnext, on obtient une autre forme d’expérience immersive dans l’événement.
La production avant, aujourd’hui et demain
Du point de vue de la fabrication, les pièces de production prêtes à l’emploi ont toujours été l’objectif ultime des industriels. Au fil du temps, les entreprises ont pris conscience qu’aborder cette question nécessite obligatoirement d’impliquer d’autres acteurs de l’écosystème de FA, des acteurs qui ne sont pas seulement et toujours des fabricants d’imprimantes 3D.
L’édition 2019 de Formnext a par exemple mis l’accent sur plusieurs points, dont le post-traitement, pour répondre à cette problématique. Cette édition de Formnext révèle d’abord que les besoins les plus urgents au niveau de la production nécessitent de prendre en compte les écarts de la chaîne d’approvisionnement, la fabrication distribuée ou la production localisée ainsi que les préoccupations en matière de durabilité.
Contrairement aux « imprimantes 3D » qui peuvent facilement être exposées et vues, ce sont des sujets dont on ne peut discuter qu’avec les acteurs du secteur. En fait, quelques fabricants d’imprimantes 3D et producteurs de matériaux ont déclaré à 3D ADEPT Media qu’ils exposaient pour rencontrer de nouvelles entreprises qui pourraient relever les défis de distribution dans des régions où ils ne sont pas encore présents.
En outre, si on regarde la fabrication à proprement parler, on réalise que la FA polymère se dirige de plus en plus vers la production de masse. HP, par exemple, a consolidé sa position de leader dans ce domaine et ne compte pas s’arrêter en si bon chemin (compte tenu de son partenariat avec L’Oréal). En effet, sur la voie du relookage de l’industrie cosmétique, HP et L’Oréal ont signé un partenariat visant à accroître la flexibilité de la production et à créer de nouveaux emballages innovants et de nouvelles expériences pour les clients grâce à la FA. Les deux entreprises ont présenté des exemples de palets personnalisés à Formnext, ainsi que des textures uniques pour des cosmétiques de luxe, uniquement possibles grâce aux solutions d’impression 3D de HP.
Parmi les autres entreprises à surveiller dans ce domaine, citons Stratasys et voxeljet. Stratasys est depuis toujours une entreprise à suivre, encore plus depuis qu’elle a élargi le portefeuille de ses sociétés et qu’elle a dévoilé sa technologie SAF.
Ce qui me plaît dans la proposition de voxeljet dans ce domaine, c’est qu’elle se concentre sur l’aspect économique de la fabrication. L’entreprise cherche à améliorer l’utilisation de son système VX1000 (une machine qui combine les avantages du frittage laser sélectif et du jet de liant) en développant une combinaison matériau-machine avec le producteur de matériaux Covestro. Les deux sociétés ont déjà mis au point une poudre de polyuréthane thermoplastique (TPU) pour le frittage à grande vitesse (HSS) et cherchent maintenant à permettre la fabrication en volume grâce à une solution matériau-processus dédiée.
En outre, nous continuerons à nous intéresser de près aux start-ups de la FA, car elles sont particulièrement bien placées pour perturber le secteur, ainsi qu’aux fabricants de machines qui ont l’ambition de proposer des solutions abordables sur le marché. En fin de compte, ces dernières permettent à un large éventail d’industries de faire leurs premiers pas dans la FA, notamment la FA métal qui reste le processus le plus étendu du marché. Xact Metal est un très bon exemple dans cette catégorie. Le fabricant de machines a présenté la série d’imprimantes 3D métal XM200G à Formnext. Avec un volume de construction de 150 x 150 x 150 mm, la nouvelle imprimante 3D permet des temps d’impression plus rapides grâce à un système galvanométrique haute performance. Avec une configuration multi-laser, la machine offrirait une zone de recouvrement de 66 % à une taille de spot de 50μm, et une zone de recouvrement de 100 % à une taille de spot de 100μm. Fidèle à sa mission de rendre la fusion sur lit de poudre métallique (PBF) plus accessible ; Xact a abaissé le prix de son imprimante XM200C de 90 000 $ (79786 €) à 65 000 $ (57623 €).
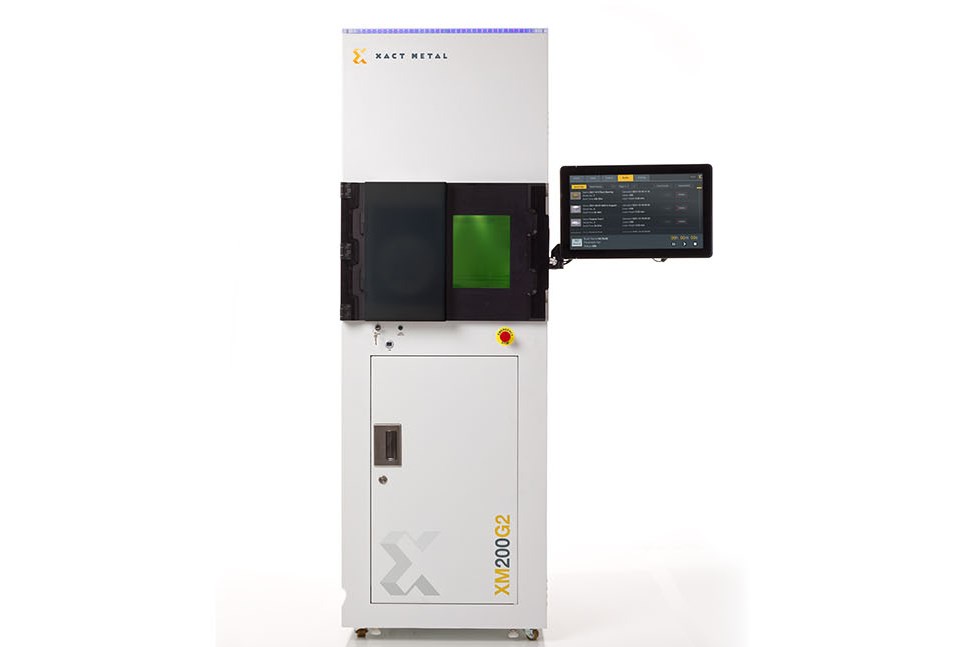
Cependant, la fusion sur lit de poudre est peut-être la technologie de FA la plus connue dans le créneau de la FA des polymères, mais n’oublions pas que la croissance de ce domaine est également due à l’essor d’autres procédés. Je pense ici à l’alternative bien connue qu’est la SLS, aux procédés d’extrusion, ainsi qu’à d’autres technologies dans le créneau de la photopolymérisation.
Alors que des fabricants comme Nexa3D veulent faciliter l’exploration des applications dans un environnement commercial, nous devons reconnaître les efforts d’Anisoprint pour améliorer la FA des composites. La toute dernière imprimante 3D à fibres continues d’Anisoprint est l’une des machines que nous avons vues le dernier jour du salon, mais nous aurions dû le faire dès les premiers jours. En effet, son développement ne met pas seulement en évidence l’expertise de Bosch en matière de technologie d’automatisation, mais il marque également le point d’entrée d’Anisoprint dans l’IoT, qui est une voie que la plupart des producteurs d’équipement s’efforcent d’atteindre.
D’autre part, j’ai également appris qu’il reste encore beaucoup à faire dans le domaine des applications industrielles d’impression 3D à jet d’encre. Il a fallu une collaboration entre Altana et dp polar pour que je réalise que l’impression 3D multi-matériau a souvent été entravée par des applications sans usage final, et c’est un domaine que j’espère voir évoluer dans les prochains mois ou années.
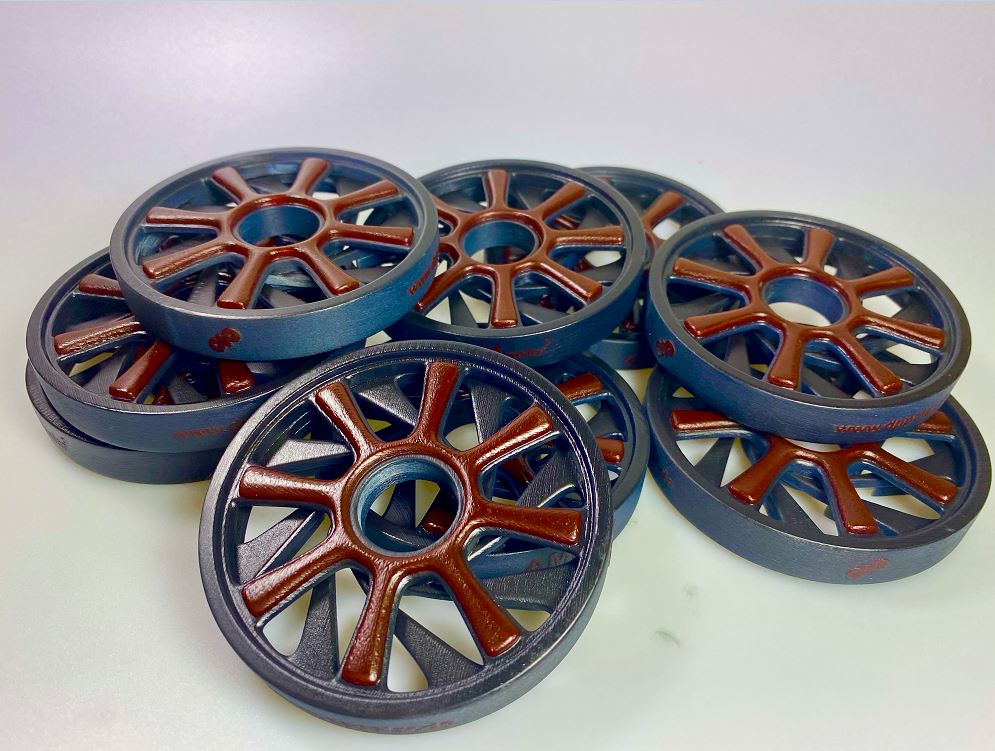
Dans le même ordre d’idées, il pourrait être facile de mettre de côté ce qui se passe du côté des logiciels dans l’industrie manufacturière, alors que ce sont les logiciels qui font danser les machines de FA sur le plancher de production.
Le fait est qu’il y a tellement de considérations à prendre en compte au niveau du logiciel (dont certaines ont été abordées dans notre reportage vidéo général qui sera bientôt publié), mais pour certaines raisons, l‘identification et la simulation des pièces restent les plus importantes à mes yeux. Alors que la première vous aide à déterminer la bonne pièce à produire par FA, la simulation est essentielle pour garantir ou atteindre une « première bonne impression », ou du moins tôt dans la phase de conception et de production. C’est particulièrement important dans les applications d’impression 3D de métaux où les paramètres sont souvent complexes à régler pour chaque matériau et chaque pièce, et où les opérateurs s’efforcent d’éviter le gaspillage de matériaux et de gagner du temps.
Un exemple que j’ai retenu du salon est la plateforme logicielle de gestion des processus basée sur le cloud Amp de GE Additive. Avec une sortie limitée des deux premiers modules (Modèle d’impression et Simulation & Compensation), le logiciel est conçu pour les utilisateurs de la machine Concept Laser M2.
« Amp est le quatrième pilier de la solution complète de GE Additive, avec les machines, les matériaux et les services », a déclaré Igal Kaptsan, directeur général – logiciel chez GE Additive.
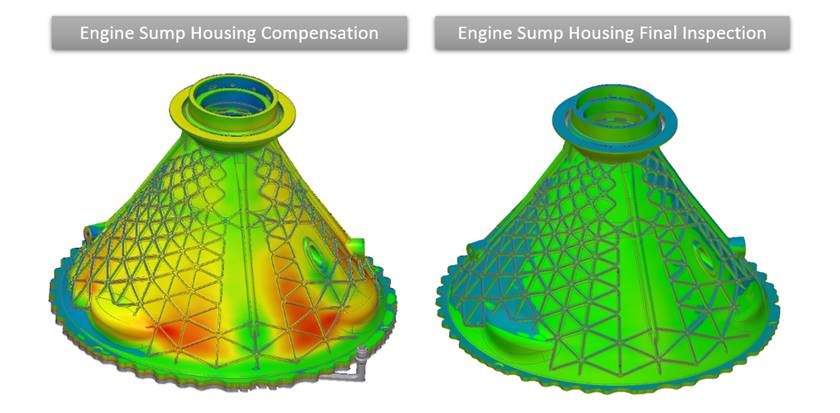
Amp supprime les cloisonnements entre les données de CAO, de préparation de la fabrication, de simulation, de compensation et d’inspection pour aider à améliorer la production de pièces. Avec des données centralisées, les utilisateurs peuvent accéder à des outils qui simulent le déroulement du processus de fabrication en temps réel et voir les estimations de coût et de temps pour une pièce tout au long du processus. Amp rationalise le processus. Il utilise une base de données unique qui permet une transition transparente des données entre une tâche et une autre. Outre la base de données, Amp intègre également les connaissances industrielles, les meilleures pratiques et les flux de travail, ainsi que les analyses temps/coût que GE a mis au point au cours de la dernière décennie, explique la société.
La conversation sur les coûts
Admettons-le : Parler d’argent n’est pas sexy et c’est une conversation que personne n’aime avoir. Nous sommes très heureux que nos conversations avec des entreprises de la FA, comme AMCM GmbH, mettent en évidence la nécessité de réduire le coût final par pièce comme l’un des principaux défis à relever, dans toutes les industries verticales.
En effet, pour parvenir à une commercialisation complète à grande échelle, les industriels ou les fabricants de pièces continueront d’évaluer la FA par rapport à d’autres méthodes de fabrication, aux tendances en matière de prix des matériaux, sans parler du paradigme logiciel qui entre en jeu.
Une chose que j’ai observée dans l’industrie de la FA, c’est que les fabricants d’imprimantes 3D ne prennent pas souvent les devants à ce niveau – du moins, très peu de comparaisons sont révélées à ce stade. Je crois fermement que les industries verticales ne seront servies que si on leur montre à l’avance les avantages en termes de coûts en investissant dans les technologies de FA, plutôt que les seuls avantages de la technologie.
Vous comprendrez qu’avec plus de 600 entreprises sur les halls de Mesago, il devient de plus en plus difficile de partager les principaux points forts de Formnext. Restez connectés pour d’autres comptes rendus.
N’oubliez pas que vous pouvez poster gratuitement les offres d’emploi de l’industrie de la FA sur 3D ADEPT Media ou rechercher un emploi via notre tableau d’offres d’emploi. N’hésitez pas à nous suivre sur nos réseaux sociaux et à vous inscrire à notre newsletter hebdomadaire : Facebook, Twitter, LinkedIn & Instagram ! Si vous avez une innovation à partager pour le prochain numéro de notre magazine numérique ou si vous avez un article à faire connaître, n’hésitez pas à nous envoyer un email à contact@3dadept.com.