Lorsque nous avons commencé à discuter de la transition vers les énergies renouvelables grâce à la fabrication additive (FA), nous avons inconsciemment mis l’accent sur le rôle des technologies d’impression 3D métal telles que la technologie de fusion laser sur lit de poudre (LPBF). Depuis lors, plusieurs projets ont vu le jour en Europe et ont démontré les capacités de l’impression 3D de céramiques en tant que candidat idéal à la production qui pourrait rapprocher l’économie de l’hydrogène d’une mise en œuvre efficace. 3DCeram démontre le comment et le pourquoi de ces capacités à travers le projet européen HyP3D.
Du point de vue de la fabrication, le rôle que peut jouer la FA dans la production d’hydrogène a souvent été difficile à démontrer. En théorie, les capacités de la FA dans n’importe quelle production peuvent être facilement décrites ; en pratique, les applications de ce segment spécifique ne sont pas vraiment connues, ce qui rend difficile l’appréciation du rôle tangible de la technologie.
Cet article vise à mettre en lumière :
– Le projet européen HyP3D et son lien avec la production d’hydrogène
– Comment l’impression 3D SLA de 3DCeram est utilisée pour aider à redéfinir le paysage de la production d’hydrogène.
– Qu’est-ce que cela signifie pour l’industrie de l’énergie ?
Le projet européen HyP3D et le lien avec la production d’hydrogène
À ce jour, l’une des méthodes prometteuses pour produire de l’hydrogène vert à partir de sources renouvelables consisterait à recourir à l’électrolyse.
Le processus d’électrolyse consiste à utiliser l’électricité pour séparer l’eau en hydrogène et en oxygène. Parmi les différents types de systèmes d’électrolyse qui peuvent être utilisés pour permettre cette réaction, ceux basés sur les cellules d’électrolyse à oxyde solide (SOEC) à haute température sont souvent les plus efficaces. Le problème est que leur adoption est souvent ralentie par leur fonctionnement stable à la pression atmosphérique.
Le projet européen HyP3D vise à remédier à cette limitation en démontrant la viabilité d’une technologie révolutionnaire de cellule d’électrolyse à oxyde solide à haute pression (SOEC). Au cœur du projet, on trouve un large éventail d’experts de la recherche et de l’industrie : IREC, DTU, PoliTo, et BSC ainsi que VAC-TRON, H2B2, SNAM et 3DCERAM du côté de l’industrie*.
Pour mettre au point une pile SOEC autonome ultra-compacte et à haute pression capable de transformer l’électricité en hydrogène comprimé, ce consortium exploitera la puissance de plusieurs solutions technologiques, dont l’impression 3D. Une étape clé de cette recherche sera le développement de cellules SOEC imprimées en 3D avec une surface active substantielle de 70 cm², des fonctionnalités intégrées et la capacité de produire de l’hydrogène à des densités de courant remarquablement élevées dépassant 0,90 A/cm² (~1,3 V) dans des conditions de 850 ºC et de pression de plus de 5 bars.
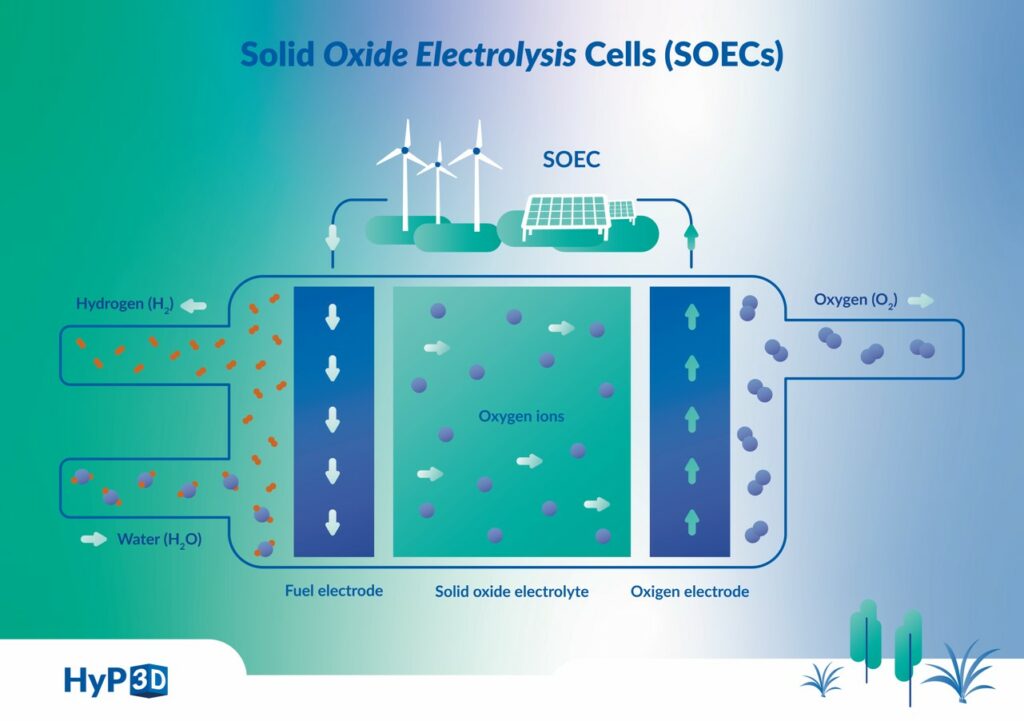
Avec l’aimable autorisation de 3DCeram. (Schéma uniquement disponible en anglais)
Comment l’impression 3D est-elle utilisée à ce niveau ?
Comment l’impression 3D SLA de 3DCeram est utilisée pour redéfinir le paysage de la production d’hydrogène ?
Fondée en 2001 par Richard GAIGNON et Christophe Chaput, la société 3DCeram a acquis une grande expertise dans la fabrication d’imprimantes 3D céramique basées sur la technologie SLA. Au fil du temps, l’offre de l’entreprise a évolué pour accompagner les clients sur l’ensemble de la chaîne de valeur.
« Lorsqu’il s’agit d’industrialisation, la stéréolithographie devient un atout important car il s’agit d’un processus de construction de haut en bas. Cela signifie que les couches sont construites de bas en haut, ce qui évite l’utilisation de nombreux supports. Il s’agit là d’un point crucial à prendre en considération. Après l’impression, les pièces sont nettoyées, et moins il y a de supports, plus l’opération est facile et rapide, tout en réduisant les risques de déchets dus à une éventuelle casse lors de l’enlèvement des supports », explique l’entreprise.
Dans le cadre de ce projet, le rôle de 3DCeram sera de définir et de mettre en œuvre le scénario d’application établi au niveau de la recherche. Cela implique de développer un processus d’optimisation complexe englobant la matière première imprimable Zr8Y, les paramètres d’impression 3D et les traitements thermiques.
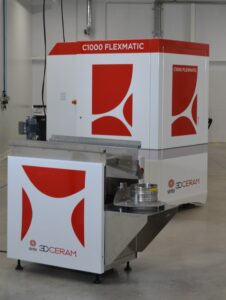
Pour atteindre son objectif ultime – produire des pièces de forme complexe reflétant les dimensions finales de la cellule – l’équipe passera par un certain nombre d’étapes différentes : de la conception de procédures optimales à l’étude du comportement rhéologique et aux tests d’impression en formulant des boues spécialisées pour l’impression 3D SLA à l’aide de poudres YSZ commerciales.
La production s’appuiera sur l’imprimante 3D C1000 FLEXMATIC de l’entreprise, qui vise à automatiser l’ensemble du processus.
Cette ligne de production semi-automatique dispose d’une plateforme de construction de 320*320 mm qui correspond aux ambitions industrielles du projet. Dévoilée l’année dernière, l’imprimante 3D a été conçue avec deux options de laser qui peuvent répondre à différents besoins de production. Sa capacité d’automatisation assure la phase de recyclage du matériau non polymérisé ainsi que la phase de nettoyage des pièces et des plateaux. Le processus d’impression nous permet de gagner du temps car les pièces imprimées en 3D ne nécessitent que peu ou pas de support.
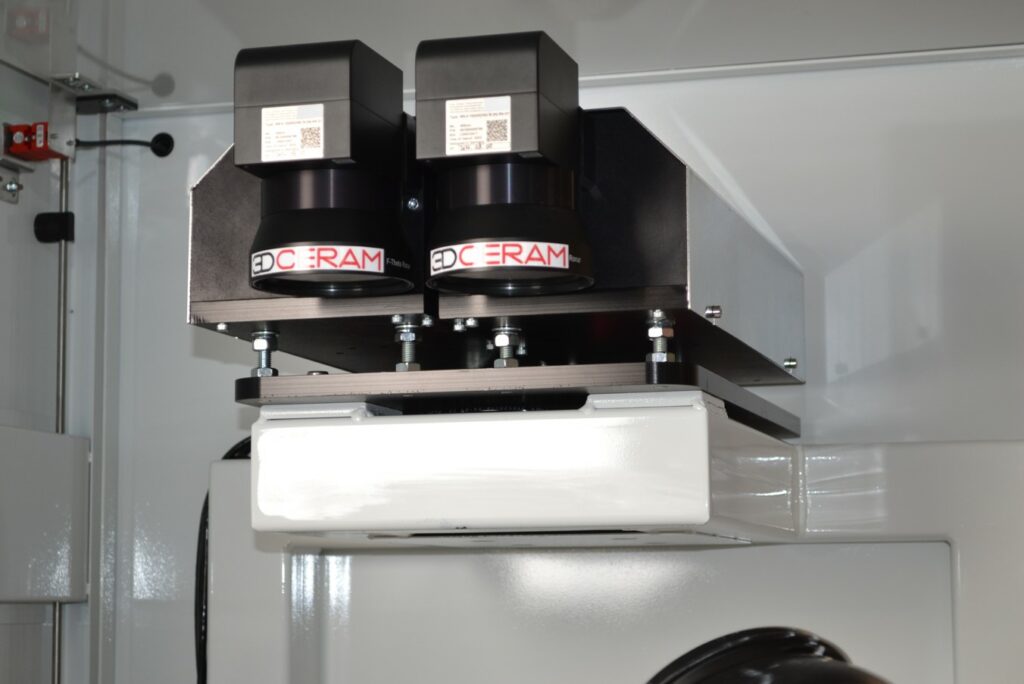
Pourquoi l’impression 3D SLA de 3DCeram est-elle le candidat idéal pour ce projet ?
Pour mieux comprendre les capacités de la technologie de 3DCeram, il est important de garder à l’esprit que ces pièces sont toujours fabriquées à l’aide de techniques de fabrication conventionnelles telles que la coulée de bande. Les défis de ce processus de fabrication sont la difficulté de garantir les propriétés rhéologiques des boues de bandes vertes qui permettront la performance de l’électrolyte. En outre, le processus de fabrication produit une cellule plate et non fonctionnalisée, ce qui fait qu’il n’est pas toujours idéal pour la production.
Au contraire, l’impression 3D SLA confère à la cellule une géométrie complexe qui permet de modifier la forme de la surface et d’ajouter des voies de gaz pour optimiser les parties qui en ont besoin.
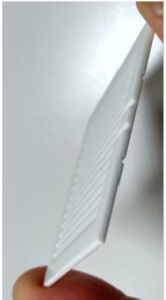
3DCeram rapporte que les piles SOEC imprimées en 3D et à très haute densité de puissance fournissent une puissance de 2,14 kW dans un volume compact de 630 cm3. Cela se traduit par une multiplication par trois de la puissance spécifique par unité de volume, qui passe à 3,4 kW/, et par une multiplication par quatre de la puissance spécifique par unité de masse, qui passe à 1,10 kW/kg. Ces résultats dépassent actuellement toutes les références de l’industrie.
Qu’est-ce que cela signifie pour l’industrie de l’énergie ?
En tant que partenaire clé du projet HyP3D, 3DCeram repousse les limites de sa technologie en démontrant les capacités d’automatisation qui seront nécessaires aux industries cherchant à augmenter la production de cellules SOEC imprimées en 3D.
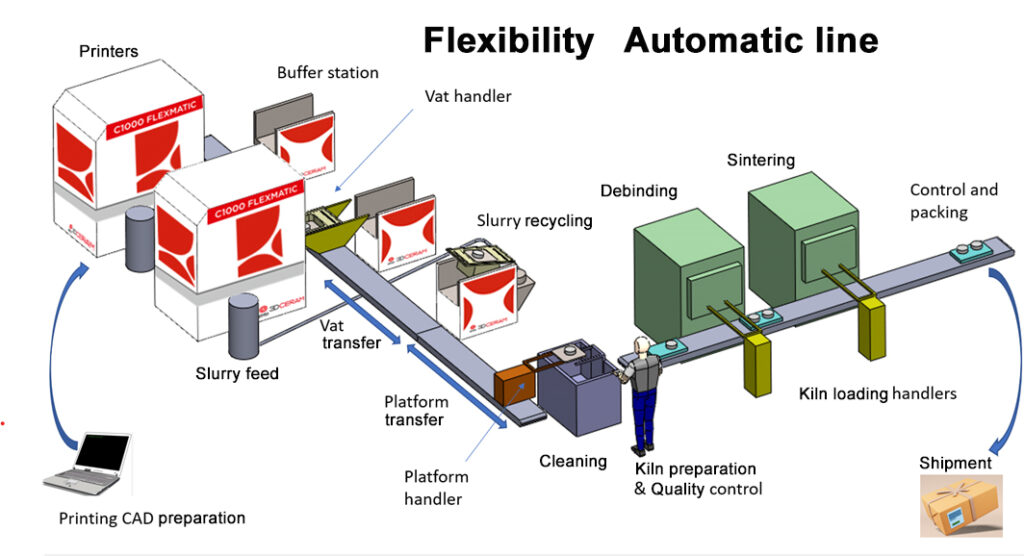
À l’heure actuelle, l’entreprise a démontré le potentiel de l’impression 3D de céramiques pour un secteur critique comme celui de l’énergie. Avec des robots et des systèmes de production automatisés capables de gérer toutes les étapes, de la conception à la cuisson des pièces, 3DCeram est prête à aider l’industrie de l’énergie à augmenter sa production grâce à sa technologie.
Si avec l’imprimante 3D C1000 FLEXMATIC, 3DCeram permet déjà d’automatiser l’ensemble du processus (du grattage aux stratégies de laser, de la qualité des formulations céramiques prêtes à imprimer au recyclage et au post-traitement), il faut noter que la ligne de production de l’entreprise comprend des imprimantes 3D comme la C3600 ULTIMATE avec des volumes plus importants. Nous pensons que ces imprimantes 3D seront également adaptées à la production industrielle, mais c’est un sujet que nous serons heureux de discuter dans un autre article.
En attendant, la vision de HyP3D ne s’arrête pas à la matérialisation de composants denses et mécaniquement robustes. 3DCeram va actuellement plus loin en développant et en modélisant une pile de production d’hydrogène. En collaborant étroitement avec l’IREC, un centre d’excellence en recherche énergétique appliquée, l’entreprise se concentrera désormais sur les stratégies d’impression optimales, afin de garantir la fiabilité et de maximiser le rendement de la production.
Si le projet est couronné de succès – et il est probable qu’il le soit au vu des premiers résultats prometteurs -, il contribuera à atteindre les objectifs de promotion de l’économie de l’hydrogène, en réduisant considérablement les délais de mise sur le marché, en diminuant la consommation de matières premières de 76 % et en minimisant l’investissement initial de 42 % par rapport aux processus de fabrication conventionnels.
« Avec cette initiative révolutionnaire HyP3D, le secteur de l’énergie voit converger les prouesses de l’impression 3D et l’innovation dans le domaine de l’hydrogène, propulsant le monde vers un avenir énergétique plus durable », conclut 3DCeram.
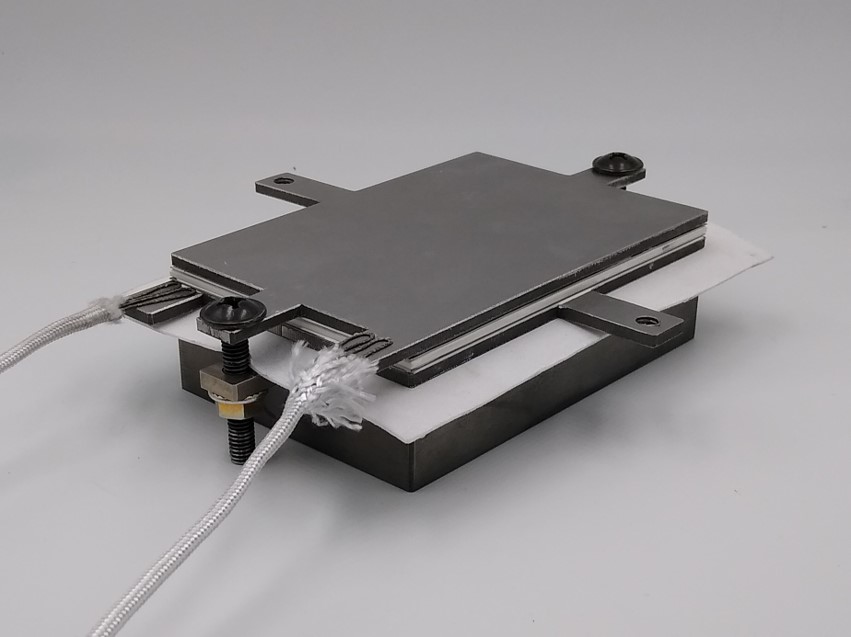
Co-écrit par Kety S. et Yosra K.
*Notes de l’éditeur :
Au cœur du projet, on trouve un large éventail d’experts de la recherche et de l’industrie : IREC, DTU, PoliTo et BSC, ainsi que VAC-TRON, H2B2, SNAM et 3DCERAM du côté de l’industrie. Même si nous nous concentrons sur la compréhension des capacités de l’impression 3D SLA de 3DCeram dans cet article, il convient de noter que chacun de ces partenaires apporte une expertise précieuse au projet.
L’IREC est un centre d’excellence en matière de recherche appliquée sur l’énergie. L’Institut de recherche énergétique de Catalogne (IREC) dirige le projet HyP3D et en est le principal coordinateur. L’Institut de recherche énergétique de Catalogne (IREC), situé à Barcelone, en Espagne, prend la tête de l’initiative HyP3D et joue le rôle de coordinateur principal du projet. L’IREC joue un rôle central dans le domaine de la recherche énergétique. Le département « Nanoionics and Fuel Cells » de l’IREC apporte une expertise considérable dans la fabrication et l’évaluation de cellules à oxyde solide pour l’électrolyse et la production d’énergie, en utilisant des techniques d’impression 3D de pointe.
DTU est une université technique européenne qui possède plus de 20 ans d’expérience dans le développement et la mise à l’échelle de céramiques fonctionnelles avancées.
Le Politecnico di Torino (PoliTO) est une université de premier plan en Italie et en Europe, axée sur la recherche technico-scientifique et leader dans le domaine des matériaux. Leur expertise sera combinée pour produire des assemblages résistants aux hautes pressions pour HyP3D.
Le Barcelona Supercomputing (BSC) est une institution nationale espagnole dédiée au calcul à haute performance (HPC). Elle gère MareNostrum, l’un des superordinateurs les plus puissants d’Europe. BSC réalisera des modèles fluido-dynamiques, électro-thermo-chimiques et mécaniques de haute-fidélité pour la technologie HyP3D, parallèlement à la création d’un jumeau numérique de la pile HyP3D.
VAC-TRON est une PME spécialisée dans la technologie d’étanchéité verre-métal pour des applications très exigeantes telles que l’aérospatiale et l’industrie pétrolière et gazière. Elle apportera au projet HyP3D une expertise importante dans les domaines de la conception de joints pour les hautes pressions et les hautes températures, ainsi que dans la création de procédures d’étanchéité fiables à l’échelle de la masse.
H2B2 est une organisation spécialisée dans les systèmes de production d’hydrogène par électrolyse de l’eau à différents niveaux : développement, financement, conception, intégration, construction, exploitation et maintenance. Elle propose des solutions de bout en bout pour la production d’hydrogène vert, à chaque étape du processus. Ils apporteront à HyP3D leur connaissance approfondie de l’efficacité énergétique et des stratégies de réduction des coûts des systèmes conçus. En outre, H2B2 est propriétaire de la ligne pilote de fabrication qui sera utilisée pour produire les cellules HyP3D.
SNAM est un opérateur de premier plan dans le transport et le stockage de gaz naturel en Europe, avec une infrastructure qui soutient la transition énergétique. Forte de ses 80 ans d’expérience dans la gestion et le développement de réseaux et d’usines, la SNAM assure la sécurité de l’approvisionnement énergétique et conduit la transition énergétique sur différents territoires en investissant dans les gaz verts, tels que le biométhane et l’hydrogène, ainsi que dans l’efficacité énergétique. La SNAM contribuera à l’équilibre des installations du système HyP3D.