Les industriels ont passé les vingt dernières années à chanter les louanges de la fabrication additive, mais la réalité montre que s’il y a une chose qui permet vraiment d’apprécier les avantages et les résultats de cette technologie, c’est bien le post-traitement. Le petit bémol est que le post-traitement est une étape complexe, confuse et parfois dérangeante du processus de fabrication.
Le post-traitement est un terme général qui englobe une variété de procédés par lesquels les pièces imprimées en 3D doivent passer avant d’être utilisées par l’utilisateur final. Quelle que soit l’étape de post-traitement par laquelle la pièce fabriquée par FA doit passer, l’objectif reste le même : éliminer les propriétés indésirables qui ont été intégrées au produit final au cours du processus de fabrication additive.
En outre, comme son nom l’indique, il a lieu à la fin du processus de fabrication, et le type d’actions de post-traitement mis à profit ainsi que la quantité de travail à ce stade de la fabrication dépendent de nombreuses variables, y compris des applications.
Les tâches de post-traitement peuvent donc inclure, sans s’y limiter, au : traitement thermique, séchage UV, l’enlèvement de support, le nettoyage et l’enlèvement des poudres, l’usinage, le revêtement ou l’infiltration, les procédés de finition de surface, l’inspection et la teinture.
Ce dossier vise à donner aux industriels des informations clés sur le post-traitement, ses différents segments et son importance dans la production en série de FA. Pour aborder cette question, le CEO d’AMT, Joseph Crabtree et Manuel Laux, responsable d’AM Solutions, prendront principalement la parole pour partager leur opinion sur plusieurs points clés. Nous remercions également FIT AG, Solukon, Protolabs et Girbau, pour les exemples fournis.
Une étape de post-traitement peut apporter de nombreuses améliorations à la pièce telles qu’une meilleure esthétique, une précision géométrique, des fonctionnalités et des propriétés mécaniques, des caractéristiques de surface souhaitées, pour n’en citer que quelques-unes. Cependant, pour obtenir le produit sous sa forme prête à l’emploi, les opérateurs sont confrontés à deux défis principaux :
– Le premier est qu’une grande partie des tâches effectuées après le processus d’impression sont manuelles.
Selon le CEO d’AMT, Joseph Crabtree, «actuellement, jusqu’à soixante pour cent des coûts de fabrication d’une pièce imprimée en 3D sont attribués aux étapes hautement manuelles de post-traitement de la pièce après son impression. En automatisant le flux de travail de post-traitement, les fabricants réduiront les coûts en produisant des pièces d’utilisation finale avec une technologie qui est fiable, répétable et reproductible ».
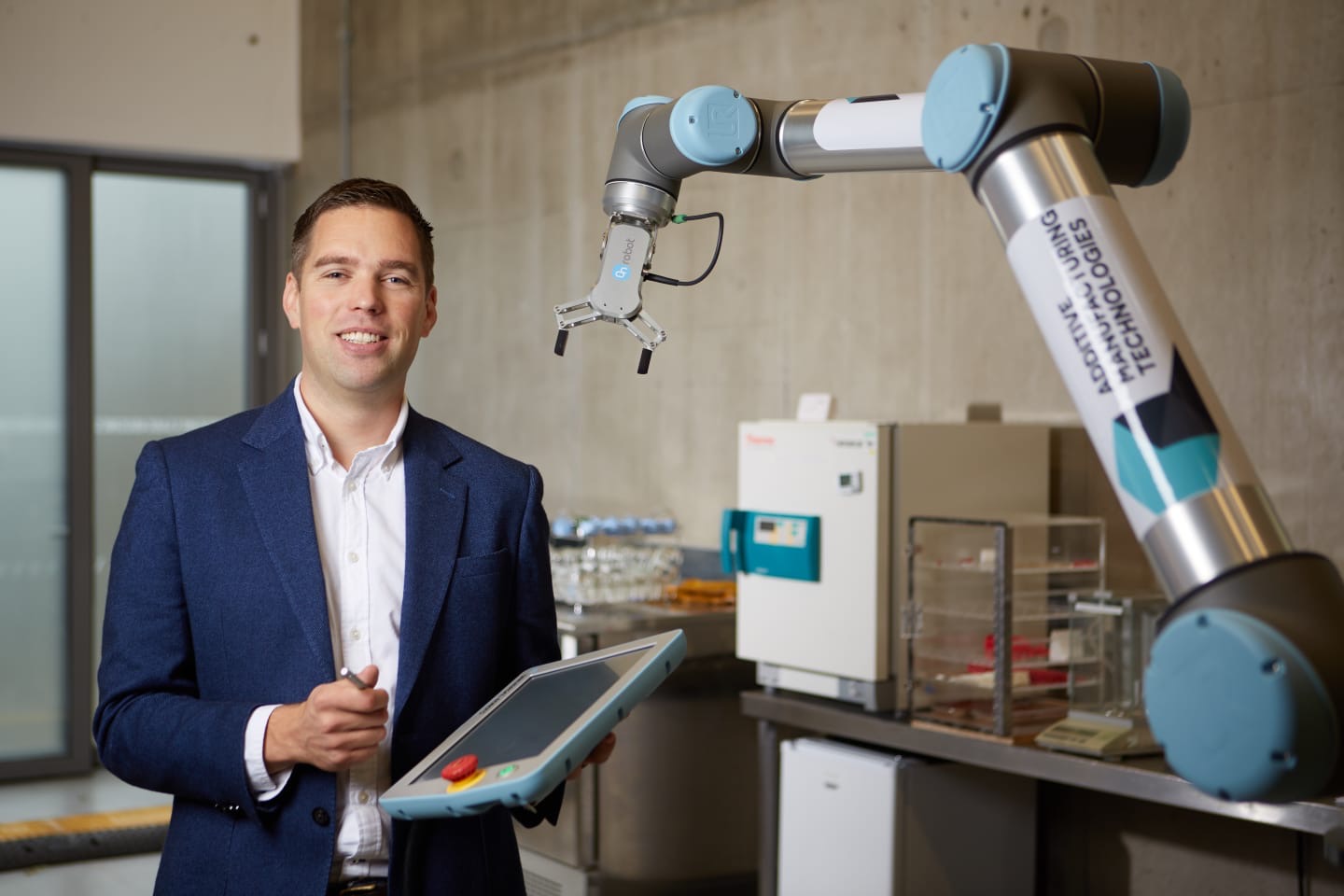
– Le deuxième problème est que, qu’il s’agisse de résine, de filament ou de métal, chaque procédé de fabrication pose ses propres défis en matière de post-traitement. Dans ce cas, les opérateurs doivent d’abord connaître les résultats escomptés pour leur pièce afin de déterminer l’étape de post-traitement qui convient le mieux à leur projet. En outre, certaines tâches de post-traitement sont obligatoires pour certaines applications, d’autres ne le sont pas.
« À l’exception des techniques de SLS à base de poudre, de HP MJF et de jet de liant pour les composants en plastique, pratiquement tous les systèmes d’impression 3D nécessitent des structures de support pour les composants avec des surplombs. Dans le cadre du processus de post-traitement, ces structures de support doivent être retirées. En outre, selon la méthode d’impression, les résidus de résine et de poudre doivent être éliminés. Enfin, la surface des composants imprimés doit être affinée par l’arrondissage des bords, le lissage de la surface et, souvent, le polissage. En moyenne, les processus d’élimination (structure de support, résine, poudre) et de finition de la surface représentent environ 75 % du travail de post-traitement. Les autres activités de post-traitement peuvent comprendre le séchage sous vide et la teinture des composants imprimés.

Pour être rentables, ces travaux ne peuvent plus être effectués manuellement, comme c’était le cas avec les pinces ou les anciennes cuves d’immersion pour l’enlèvement du support, ou le ponçage à la main. Cela prend trop de temps, produit des résultats incohérents et est trop coûteux. De préférence, le travail manuel et les cuves traditionnelles doivent être complètement remplacés par des systèmes chimiques et mécaniques entièrement automatisés », explique Manuel Laux, responsable d’AM Solutions.
Un regard sur les différentes étapes du post-traitement
1- Traitement thermique
Un certain nombre de pièces métalliques fabriquées à l’aide de la FA nécessitent une solution de traitement thermique avec une uniformité de température précise. Cela garantit que les pièces imprimées adhèrent aux propriétés métallurgiques de l’alliage métallique choisi. Pour éviter toute déformation importante, les pièces métalliques imprimées en 3D sont généralement soumises à une relaxation des contraintes en même temps que la plate-forme de construction et à un traitement thermique après avoir été coupées de la plate-forme de construction. Cette solution est souvent choisie par les entreprises en raison de la complexité des matériaux utilisés dans le processus de FA. Pour les applications aérospatiales et médicales par exemple, le procédé de FA doit respecter des règles très strictes, c’est pourquoi les avantages du traitement thermique résident dans sa capacité à réduire la contamination de surface et à maximiser les propriétés mécaniques.
Le traitement thermique à haute pression (HPHT) est une nouvelle forme de technologie utilisée pour la consolidation et la densification des pièces métalliques, céramiques et plastiques. Selon le sous-traitant FIT AG, des pressions typiques de 15 000 à 30 000 psi, des températures allant jusqu’à 4 000 °F, ainsi que des vitesses de refroidissement allant jusqu’à 4 500 K/min permettent d’obtenir une densité théorique maximale, une ductilité et une résistance à la fatigue des matériaux à haute performance.
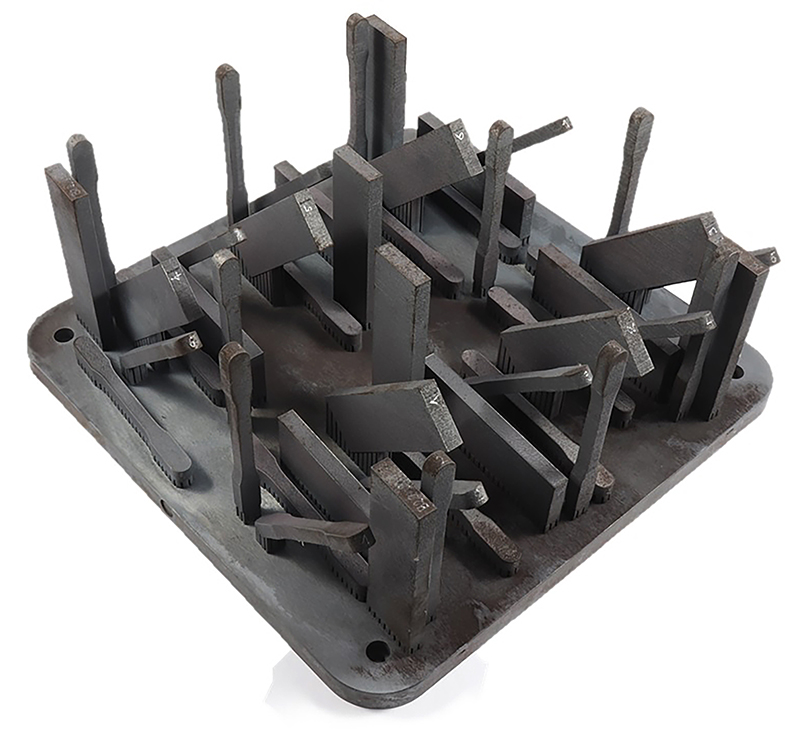
2- Le séchage UV
Cette étape de post-traitement est généralement compatible avec les composants qui ont été produits à l’aide de procédés de photopolymérisation/technologies d’impression 3D résine, comme la production d’interface liquide continue de Carbon (CLIP™), et SLA. Les composants sont exposés à la lumière UV pour durcir complètement afin d’améliorer la qualité physique de la pièce et de renforcer les caractéristiques esthétiques.
3- Retrait du support
Le retrait du support est nécessaire pour les pièces qui ont été produites avec la technologie d’impression 3D résine ou la technologie FDM. En termes simples, les composants imprimés en 3D sont généralement fixés aux plaques de construction par des échafaudages et des structures de support qui permettent de créer des structures en surplomb, réduisant ainsi le degré de gauchissement. Ces structures de support peuvent être fabriquées à partir de matériaux solubles et insolubles. Si le matériau est insoluble, plusieurs accessoires peuvent être utilisés (lames) pour enlever ces structures de support. Cependant, un matériau de support soluble offre un risque moindre d’endommager le modèle car les structures de support peuvent être dissoutes dans l’eau ou avec un produit chimique appelé Limonène.
En outre, ceux qui souhaitent réduire le travail manuel peuvent opter pour une solution plus automatisée. PostProcess Technologies, par exemple, partenaire d’AM Solutions, propose diverses solutions qui répondent aux exigences de ces différentes technologies de FA : « Avec la technologie «Submersed Vortex Cavitation (SVC)», les systèmes de PostProcess DEMI et FORTI éliminent de manière fiable les supports et l’excès de résine. Pour l’élimination des supports des produits fabriqués à partir de filaments (FDM/FFF), PostProcess propose les unités DECI et BASE utilisant le procédé «Volumetric Velocity Dispersion (VVD) », déclare Manuel Laux.
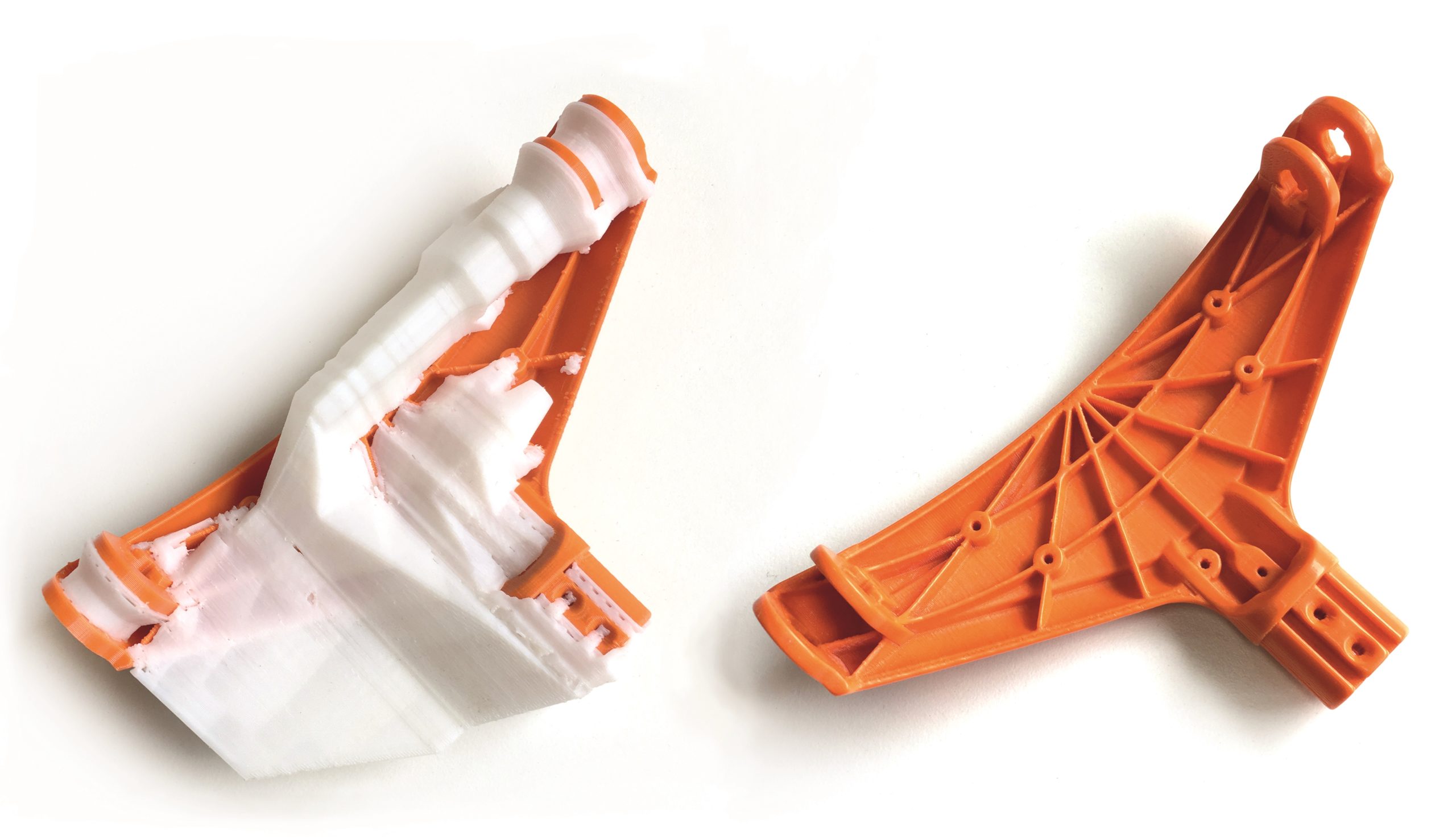
4- Nettoyage et enlèvement des poudres
Le terme « dépoudrer » ou « enlèvement des poudres » est souvent utilisé de manière interchangeable avec « nettoyer ». Cependant, si le nettoyage peut faire référence à la capacité d’enlever les structures de support pour les technologies de projection de FDM, de résine ou de matériaux, « dépoudrer » reste le mot le plus explicite pour décrire la capacité d’enlever les résidus de poudre qui restent dans les pièces fabriquées par FA.
L’enlèvement des poudres ou « dépoudrage » entre en jeu lorsque les composants ont été produits à l’aide de technologies de fabrication additive métallique à base de poudre. Il s’agit en fait de la première étape et du goulot d’étranglement actuel de la chaîne de post-traitement après le processus d’impression. Un large éventail d’autres étapes de post-traitement sont souvent nécessaires après cette tâche, c’est pourquoi certains experts préfèrent appeler cette étape « pré-traitement ».
Prenons l’exemple d’une pièce complexe produite sur un système de fusion sur lit de poudre. Le dépoudrage de cette pièce nécessitera généralement une brosse et un aspirateur. Par la suite, cette pièce devra être déstressée, sciée et retournée. Selon l’application, d’autres tâches peuvent être nécessaires : CNC et durcissement par précipitation, pour n’en citer que quelques-unes. Le coût des procédés mis à part ; ces procédés manuels peuvent prendre plusieurs jours avant qu’on obtienne le résultat final souhaité. Pour remédier à cette situation, certains fabricants de machines intègrent des étapes de post-traitement dans leurs systèmes de FA, d’autres fabricants et utilisateurs de FA qui possèdent déjà un parc de systèmes de FA optent simplement pour une solution d’élimination automatisée de la poudre.
« Une caractéristique unique des solutions de post-traitement automatisé d’AMT est que toutes les technologies d’AMT sont sûres et durables, et spécifiquement conçues pour la fabrication additive, contrairement aux autres technologies de post-traitement sur le marché. La technologie d’AMT pour le dépoudrage, PostProDP, et la finition de surface, PostPro3D, permet de finir les pièces en douceur à l’échelle industrielle. Non seulement les technologies d’AMT améliorent l’esthétique des pièces, mais elles améliorent également leurs propriétés mécaniques, telles que l’allongement à la rupture (EAB), et éliminent l’entrée d’eau et de gaz. Grâce à des algorithmes intelligents et à l’apprentissage machine, les technologies d’AMT sont dotées de recettes programmées pour chaque combinaison de matériaux courants, offrant ainsi une véritable solution «plug and play» », a déclaré M. Crabtree à 3D ADEPT Media.
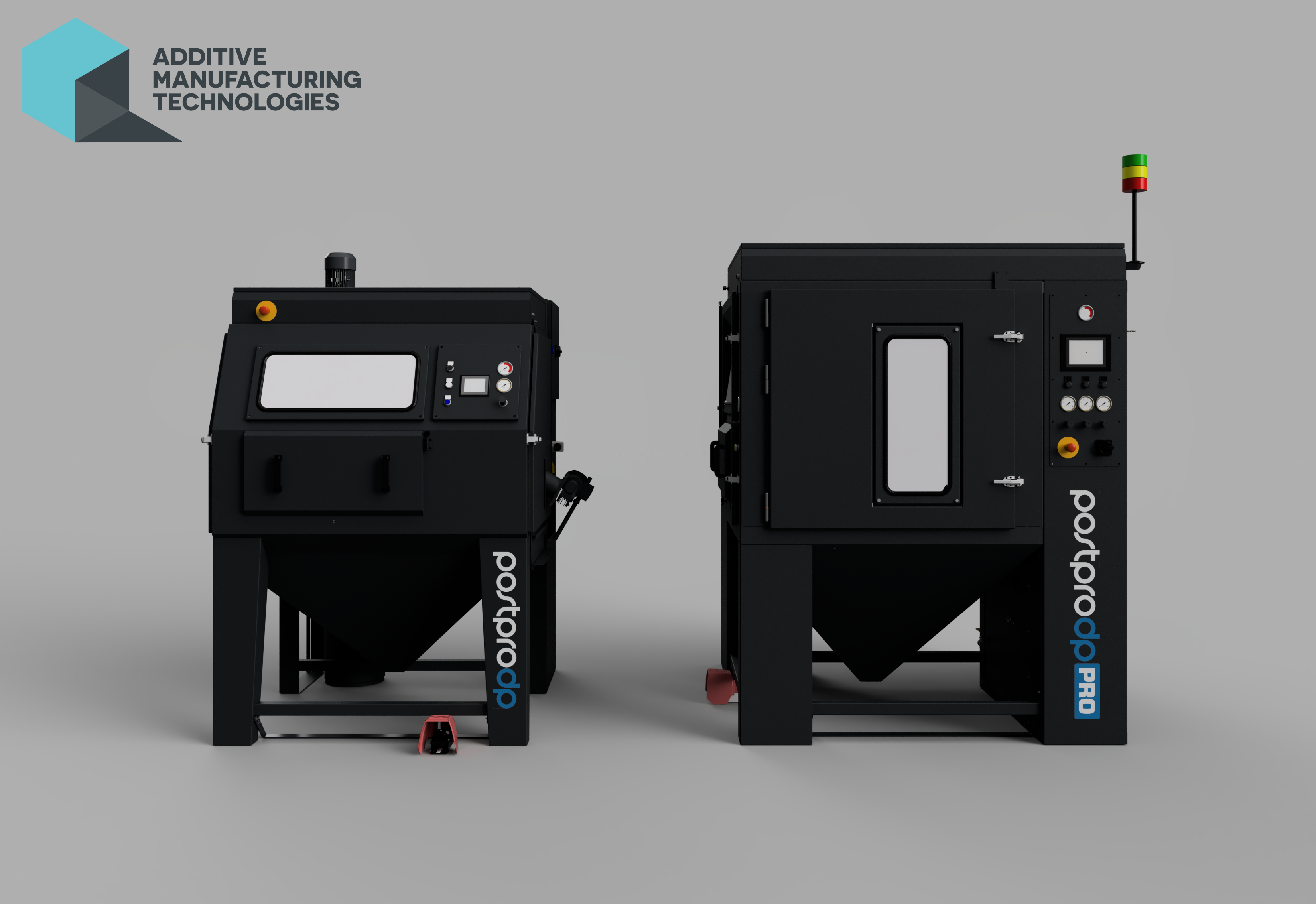
Un autre fabricant qui se démarque également dans cette catégorie est Solukon. Pour résoudre les problèmes liés à la complexité des pièces comportant des canaux et des vides qui retiennent la poudre, Solukon a mis au point une série de machines de dépoudrage automatisées et programmables qui éliminent la poudre des pièces métalliques imprimées en 3D. Les systèmes de la société allemande ne se contentent pas de tourner et de vibrer dans la direction spatiale pour enlever la poudre restante, ils assurent également un haut degré de protection contre l’accumulation de poussières dangereuses, et l’infusion de gaz inerte pour éviter une atmosphère explosive.
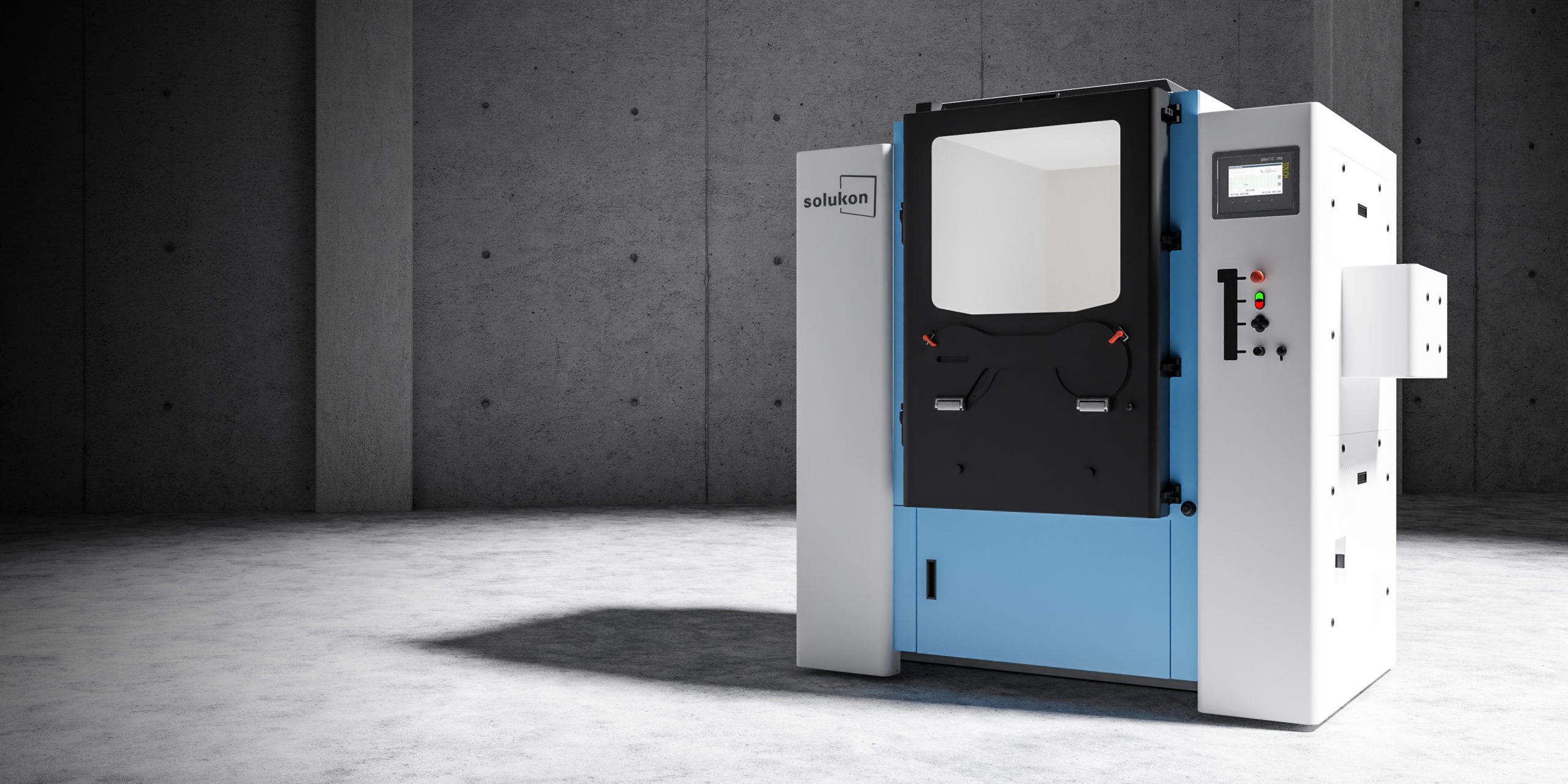
5- Procédés de finition de surface
Selon l’application, les composants imprimés en 3D peuvent nécessiter un affinement supplémentaire de la surface par un rayon de bord, un lissage de surface et, éventuellement, un polissage.
Dans un processus d’affinage de surface qui combine des systèmes de sablage et de finition, explique M. Laux, directeur d’AM Solutions : « la surface initiale des pièces imprimées en 3D peut parfois être assez rugueuse avec des lectures Ra allant jusqu’à 1 000 micro-pouces. Dans de tels cas, il peut être avantageux de faire passer les pièces par un processus de sablage pour une réduction initiale de la rugosité de surface avant de les traiter dans le système de finition proprement dit. Cela permet de réduire les valeurs Ra jusqu’à < 20 micro-pouces ».
Si l’opérateur recherche des surfaces extra-lisses sur des composants métalliques, AM Solutions peut proposer un « système de finition produisant des finitions de surface extrêmement fines avec des valeurs Ra de < 5 micro-pouces sur des composants métalliques imprimés en 3D. Ce résultat est obtenu grâce à la technologie brevetée d’électropolissage à sec DRYLITE®, qui ne nécessite aucun électrolyte liquide ».
En outre, le terme « finition » désigne une série d’activités de post-traitement telles que l’apprêtage, le remplissage, le meulage, la préparation à la peinture, l’ébavurage, etc. Elles sont généralement utilisées comme base pour d’autres post-traitements, comme le revêtement des métaux.
6- L’usinage
Les pièces peuvent nécessiter un usinage supplémentaire pour enlever d’autres structures de support. Cette tâche de post-traitement peut être effectuée après presque tous les processus de FA. Elle est absolument nécessaire pour les procédés métalliques qui ne permettent pas d’obtenir des géométries proches du contour final.
7- Revêtement ou infiltration
Le revêtement consiste en l’infiltration de composants microporeux avec des polymères. L’objectif de cette activité est de produire des composants totalement étanches aux gaz ou aux liquides.
8- La teinture
Si l’aspect visuel de vos pièces en polymère à base de poudre doit être amélioré, alors vous avez probablement besoin d’une étape de post-traitement de teinture. La teinture peut être effectuée, soit manuellement dans des pots d’eau chaude, soit à l’aide d’un équipement de teinture automatisé. Cette technique de post-traitement est surtout utilisée par les utilisateurs de la technologie Multi-Jet Fusion de HP. Les résultats sont plus visibles sur les pièces sujettes à l’usure (les lunettes par exemple), car la couleur pénètre la surface de la pièce. Girbau, par exemple, est l’un des spécialistes de l’industrie des équipements de teinture qui a conçu ses équipements pour la technologie MJF de HP.
9- L’inspection
Cette étape de post-traitement permet de valider la précision dimensionnelle et les propriétés mécaniques d’une pièce. Cette étape de post-traitement est généralement considérée comme un avantage dans les situations de fabrication à la demande. Protolabs est un fournisseur de services de fabrication industrielle qui intègre à son offre des services de rapports détaillés de mesure et d’inspection. La société explique que le « processus d’inspection vérifie que les pièces finales sont conformes au dessin original, au bon de commande et aux autres spécifications indiquées. L’inspection dimensionnelle utilise des équipements CMM pour s’assurer que les dimensions des pièces sont dans les tolérances et s’alignent sur les mesures fournies dans le dessin original.
Le rapport final détaille l’emplacement sur la plaque de construction, la façon dont la géométrie a été orientée, le placement de la structure de support, et un fichier journal de construction détaillant l’ensemble du processus de construction de la machine ».
Prenant l’exemple de pièces qui ont été fabriquées par frittage laser direct des métaux (DMLS), le fabricant de pièces explique que la numérisation par tomographie assistée par ordinateur (CT) est souvent la méthode d’inspection idéale pour ces pièces. En effet, elle offre un moyen non destructif de validation des pièces. Selon Protolabs, le procédé peut être utilisé pour inspecter et valider des caractéristiques évidées ou des canaux internes. Il permet de mesurer les variations d’épaisseur des parois ou de détecter les déformations et les fissures, et de vérifier qu’il ne reste pas de poudre résiduelle dans la pièce.
Une même technologie de post-traitement peut-elle être compatible avec plusieurs types de technologies de fabrication additive ?
Tout d’abord, il convient de noter que les spécialistes des technologies de post-traitement élaborent généralement leurs solutions pour répondre à une demande spécifique de l’industrie de la FA. Au fil du temps, les applications ont tendance à étendre leur domaine de compétence à d’autres technologies.
De plus, choisir entre l’ensemble des technologies de FA le procédé idéal pour son projet est assez compliqué. Cependant, malgré les nombreuses techniques de post-traitement susmentionnées, le choix peut rapidement être fait pour une solution de post-traitement.
« Un nombre relativement restreint d’équipements de post-traitement, que ce soit pour l’élimination des supports et de la résine résiduelle, le dépoudrage et le nettoyage ou la finition de surface, peut être utilisé pour des groupes entiers de technologies de fabrication additive. Par exemple, pour le dépoudrage, le nettoyage et le lissage de surface initial, les équipements de la gamme S de AM Solutions peuvent être utilisés pour les composants en plastique et, en termes de métal, pour le lissage de surface initial.
Lorsqu’il s’agit de la finition de surface des mêmes composants en plastique ou en métal, la série M-Line d’AM Solutions est tout à fait adaptée », déclare Manuel Laux d’AM Solutions.
En outre, l’expérience acquise dans diverses applications pourrait facilement permettre aux opérateurs de déterminer la technique de post-traitement idéale pour leur projet.
Dans les applications d’outillage par exemple, la texture des pièces à la fin du processus d’impression est similaire à celle du velours côtelé. C’est pourquoi ces pièces doivent être usinées après les processus d’impression et de refroidissement.
Enfin, les similitudes et les disparités entre les technologies de fabrication additive doivent absolument être prises en compte. Le jet de liant, par exemple, présente des exigences de post-traitement similaires à celles de la fabrication de filaments fondus (FFF). En revanche, les pièces métalliques FFF peuvent nécessiter des investissements supplémentaires en post-traitement. En effet, avec cette technologie de FA, la matière première est constituée d’un filament avec un liant en plastique ou en cire fortement chargé de poudre métallique. Le liant doit être retiré une fois que la pièce est sortie de la machine. Suivent ensuite un déliantage à chaud ou dans un bain d’acide et une étape de frittage.
« Il ne s’agit pas seulement de rendre les pièces esthétiques, il s’agit d’améliorer les propriétés mécaniques des pièces pour obtenir des performances élevées ».
La fabrication additive elle-même a prouvé sa capacité à réduire les temps de production à quelques jours seulement. Cependant, sa viabilité pour la production en volume et en série n’est pas encore unanime.
Pour AM Solutions, « cela est dû dans une large mesure à des méthodes de post-traitement laborieuses caractérisées par une prépondérance du travail manuel, l’utilisation de méthodes anciennes et le manque d’automatisation. Le résultat : un post-traitement qui prend beaucoup de temps, produit des résultats incohérents avec un faible débit et est très coûteux. Ce n’est qu’avec des solutions de post-traitement automatisées et intelligentes que la fabrication additive peut être véritablement intégrée dans les lignes de production industrielles. Mais le post-traitement automatisé permettra d’obtenir beaucoup plus : Il permettra d’utiliser pleinement les capacités des imprimantes, ce qui se traduira par des temps de cycle considérablement réduits, un débit global plus élevé et une rentabilité nettement améliorée. Il produira une qualité élevée et constante des composants post-traités, ce qui réduira considérablement le taux de rejet (moins de gauchissement et de gonflement dus à l’absorption d’eau, moins de cassures, etc.)
L’intégration des traitements automatisés de post-traitement a pour effets secondaires positifs de réduire les stocks de produits en cours, d’améliorer la traçabilité des pièces et de renforcer la sécurité sur le lieu de travail (le dépoudrage manuel pouvant être dangereux) ».
« Pour dimensionner le post-traitement de manière sûre et durable, le développement de nouvelles technologies et l’automatisation sont essentiels. Il ne s’agit pas seulement de rendre les pièces esthétiques, mais aussi d’améliorer les propriétés mécaniques des pièces pour obtenir des performances élevées », ajoute AMT.
Les collaborations entre les fabricants d’imprimantes 3D et les fournisseurs de systèmes de post-traitement d’une part, ainsi que les collaborations entre les utilisateurs de FA et les spécialistes du post-traitement favoriseront certainement l’intégration de solutions de post-traitement plus automatisées dans les productions de FA, mais la compréhension de ces préoccupations et des disparités est une clé essentielle de la production en série.
Ce dossier a été initialement publié dans le numéro de Mai – Juin de 3D ADEPT Mag.