Focus sur les matériaux spécifiques aux applications
Farsoon Technologies a présenté pour la première fois la Flight® Technology ou Fiber Light® Technology en 2019, offrant des taux de production à la pointe de l’industrie avec la fusion laser plastique en poudre. En 2021, la configuration Dual-Laser du système Flight® 403P a été annoncée avec une productivité encore plus élevée. Depuis lors, de nombreux clients de Farsoon profitent des puissants lasers à fibre pour la production en volume de pièces d’utilisation finale de haute qualité. Doté d’une plate-forme de matériaux ouverte, le système Flight® HT403P de Sofos Robotics Co. (dénommée Sofos Robotics) permet de réaliser un certain nombre de projets industriels, du prototypage à la production en série, en utilisant une gamme variée de matériaux d’ingénierie spécifiques à une application. Jason Rodriguez, spécialiste du marketing de Farsoon Americas Corp, a interviewé le président de Sofos Robotics, John Huster, pour savoir comment ils utilisent la technologie Flight®. Voici ce que nous avons appris.
Rodriguez : Pouvez-vous partager l’histoire de la fabrication additive chez Sofos ?
Huster : Sofos Robotics a commencé comme un fournisseur de services d’automatisation et d’intégration robotique pour maximiser l’efficacité de la fabrication industrielle. Nous nous sommes lancés dans la fabrication additive pour améliorer les composants dont nous avions besoin pour les cellules d’automatisation, comme les supports et les plaques de montage personnalisés, les nids de pièces et les doigts de préhension.
Nous avons commencé avec quelques machines FDM et avons commencé à imprimer des composants pour nous-mêmes et pour une poignée de clients. Au début, nous nous sommes concentrés sur le prototypage et les petites séries. Au fur et à mesure que notre entreprise s’est développée, nous sommes arrivés au point où nous savions que la FDM ne serait pas en mesure de produire la quantité de pièces dont nous avions besoin assez rapidement. Nous avons commencé à étudier d’autres technologies et avons opté pour la machine Farsoon Flight® en raison de sa vitesse et de sa flexibilité.
Nous considérons la fabrication additive comme une technologie à fort potentiel. Nous avons l’intention de continuer à développer notre activité en trouvant de nouveaux marchés et en aidant nos clients à résoudre leurs problèmes.
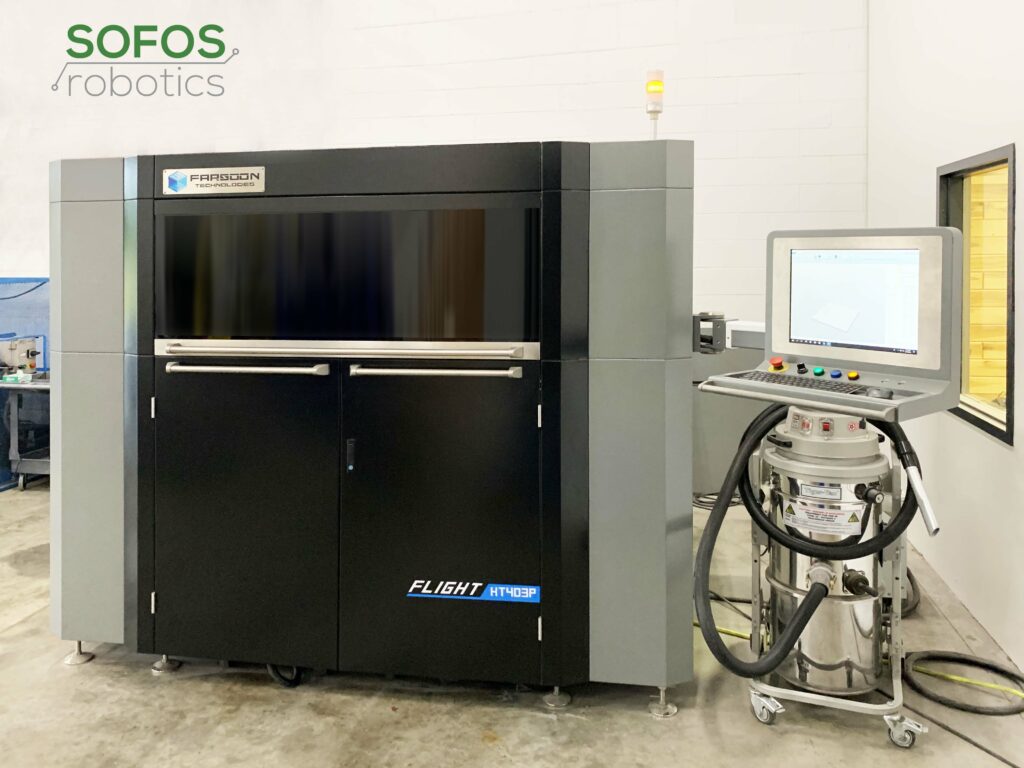
Rodriguez : Pourquoi Sofos Robotics a-t-elle choisi Farsoon et Flight® Technology ?
Huster : Nous avons commencé dans la technologie additive, comme beaucoup d’autres, en utilisant des imprimantes 3D FDM. Nous avions quelques clients pour lesquels nous faisions des prototypes de pièces, et ils ont commencé à nous demander quelles étaient nos capacités de production. Nous avons vu une opportunité de nous développer et avons commencé à étudier différentes technologies d’impression 3D. Nous avons opté pour la Farsoon Flight® HT403P en raison de son grand volume de construction, de ses vitesses incroyablement rapides et de sa plateforme ouverte de matériaux et de paramètres. Nous avons également apprécié que Farsoon ait moins de consommables et des forfaits de service plus rentables que certaines des autres machines que nous avons examinées.
Rodriguez : Pouvez-vous partager une histoire d’application spécifique avec la fabrication additive chez Sofos ?
Huster : L’un de nos clients nous a confié la production d’un protecteur en nylon personnalisé et sécurisé ESD. Pour cette pièce, en raison de l’environnement, nous devions utiliser un matériau sûr ESD. Avant d’utiliser la fabrication additive, les protections étaient en acier inoxydable et les deux moitiés étaient soudées ensemble. Les clients souhaitaient une nouvelle solution monobloc pour réduire le taux de défaillance. En utilisant la machine Farsoon Flight® et un matériau en nylon ESD de BASF, nous avons été en mesure de leur fournir une solution structurellement intégrée à un coût moindre et dans un délai plus court. Avant d’avoir la machine Farsoon, il fallait 12 heures à l’une de nos machines FDM pour imprimer une protection. Nous sommes maintenant capables d’imprimer 12 protections plus un ensemble complet de supports d’accompagnement dans le même laps de temps.
Rodriguez : Nous savons que de nombreux projets à Sofos utilisent des matériaux d’ingénierie spécifiques. Quelle est votre expérience avec la plateforme ouverte de matériaux / paramètres de Farsoon ?
Huster : C’était l’un des principaux arguments de vente lorsque nous avons cherché à savoir quelle machine acheter. Nous avons vraiment aimé l’idée d’une plateforme de matériaux ouverte et la possibilité de rechercher des matériaux auprès de différents fabricants pour trouver les bonnes solutions pour nos clients. Nous recevons des demandes très variées de la part de nos clients et le fait de pouvoir utiliser des matériaux de différents fournisseurs nous a été très utile à plusieurs reprises.
La plateforme à paramètres ouverts est formidable ! Elle nous permet d’adapter rapidement un nouveau matériau en une ou deux constructions. C’est agréable de pouvoir contrôler autant de paramètres tels que la température de fonctionnement, la puissance du laser, la distance de balayage, etc. La plateforme ouverte nous permet d’attribuer différents paramètres à chaque pièce de la construction et de tester plusieurs combinaisons pour trouver la recette parfaite. Nous pouvons également ajouter ou retirer des pièces pendant que la machine imprime. Tout cela est très utile lorsque nous essayons un nouveau matériau pour la première fois.
Rodriguez : Nous savons que Sofos a testé avec succès quelques matériaux BASF. Pouvez-vous partager avec nous d’autres résultats d’essais, et s’il y a une industrie ciblée ?
Huster : Nous avons eu une excellente expérience avec BASF. Ils ont un large choix de matériaux et de paramètres de pièces correspondants. Nous utilisons actuellement leurs matériaux PA11 ESD, TPU et PA6 à charge minérale. Les matériaux ont fait leurs preuves lors des tests et sur le terrain et nous sommes impatients d’utiliser davantage de leurs produits à l’avenir.
Certains projets sur lesquels nous travaillons avec le TPU sont des ventouses personnalisées et des protections pour les contrôleurs pendulaires. Nous nous amusons beaucoup avec ce matériau et nous attendons avec impatience d’autres applications avec lui.
Rodriguez : Pouvez-vous partager votre expérience de travail avec Farsoon et la machine Flight® 403P ?
Huster : Nous avons eu une excellente expérience de travail avec Farsoon, ils ont été très utiles tout au long du processus et continuent à nous soutenir pour toutes les questions que nous avons.
N’oubliez pas que vous pouvez poster gratuitement les offres d’emploi de l’industrie de la FA sur 3D ADEPT Media ou rechercher un emploi via notre tableau d’offres d’emploi. N’hésitez pas à nous suivre sur nos réseaux sociaux et à vous inscrire à notre newsletter hebdomadaire : Facebook, Twitter, LinkedIn & Instagram !