Dans le but de développer des chaussures d’athlétisme (en jargon, des chaussures à crampons), le coureur de demi-fond Miro Buroni a travaillé avec la marque de vêtements de sport Diadora et la société d’ingénierie CRP technology.
Comme on le voit dans la quasi-totalité de ses projets, CRP Technology apporte ici son expertise dans le procédé de fusion en lit de poudre avec des polymères composites renforcés de fibres (abréviation de Selective Laser Sintering), combinés à des matériaux composites chargés de fibres de carbone comme Windform® SP.
Le coureur de demi-fond Miro Buroni a créé et développé des chaussures d’athlétisme Pleko, personnalisées et révolutionnaires (en jargon, des chaussures à crampons) avec des caractéristiques innovantes en termes de technologie de production et de matériaux. Diadora, quant à elle, apporte son expertise en matière d’analyse historique et de conception.
La fabrication des chaussures
La création de Pleko a commencé par le scan tridimensionnel du pied de l’athlète. Cette étape a été suivie par l’analyse biomécanique de l’acte de courir et du pied grâce au scan 3D du pied.
« Grâce à cette cartographie – commente Buroni – nous avons pu modéliser la chaussure en fonction des besoins de l’individu en termes de structure du pied et de performances athlétiques. De plus, le scan et l’analyse biomécanique nous ont permis de comprendre le meilleur placement du « système de traction » sous la semelle extérieure, les « pins ».
Pour donner vie au projet, Buroni s’est appuyé sur CRP Technology qui a imprimé en 3D la semelle extérieure, la semelle intermédiaire et les nervures – les structures porteuses des chaussures.
Selon CRP Technology, les résultats de l’enquête sur la force transmise aux chaussures de piste pendant la course sur piste et les exigences liées, ont révélé l’importance d’un matériau approprié dans ce processus.
Windform SP est un matériau composite chargé en fibre de carbone de la gamme Windform TOP-LINE de CRP Technology pour la technologie de frittage laser PBF, avec d’excellentes caractéristiques de résistance à la déformation et de flexibilité : « les bonnes caractéristiques pour les chaussures de piste d’athlétisme« .
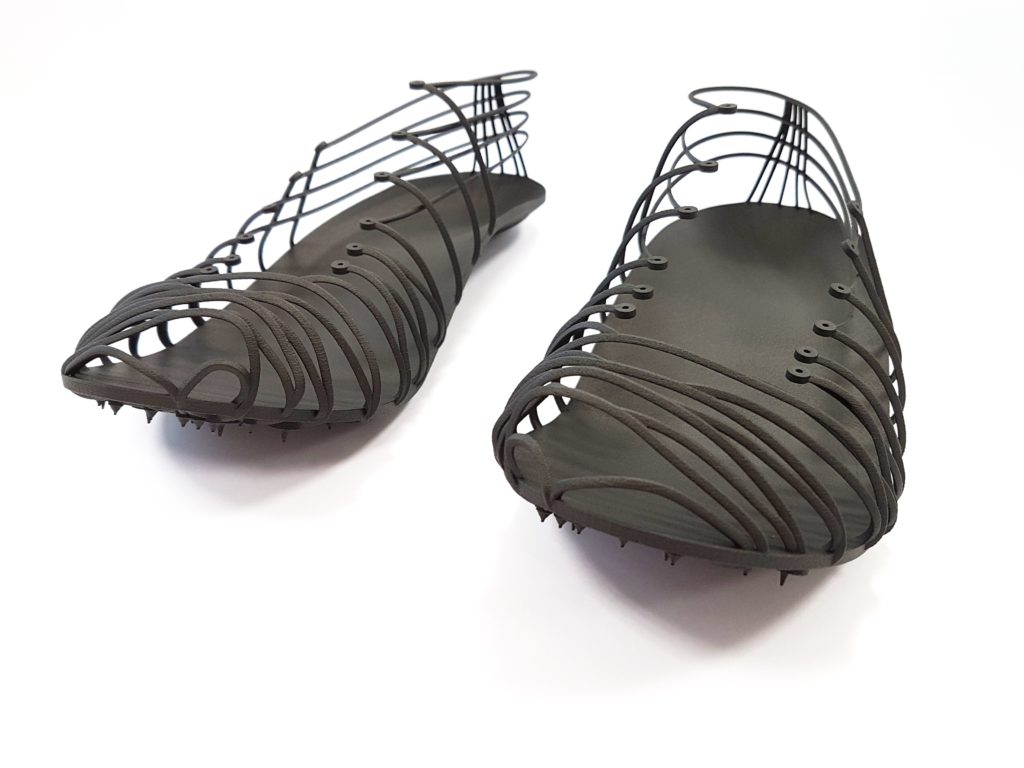
La pièce fabriquée en Windform SP
La technologie CRP a permis de fabriquer en une seule unité la semelle extérieure, la semelle intermédiaire, les nervures et les picots de Pleko.
Les nervures naissent sous la semelle extérieure, en correspondance avec les lignes d’effort maximal pendant la course sur piste.
Grâce aux nervures, la structure de la Windform SP embrasse le pied de l’athlète « comme une cage », qui enveloppe le pied et facilite l’amélioration de la technique de course. Les nervures sont chargées de transporter l’énergie cinétique libérée par le mouvement biomécanique pendant la course sur piste, et d’empêcher sa dispersion.
La tige en forme de chaussette est presque entièrement détachée de la structure et est chargée de protéger le pied.
« Grâce aux picots situés sous la semelle extérieure – ajoute Miro – la « cage » de la Windform SP permet à l’athlète de développer le plus de force possible, sans perdre d’énergie. J’ai positionné les picots les plus profonds aux points de pression supérieure du pied contre le sol. J’ai également placé des goujons plus petits dans d’autres parties de la semelle extérieure : ces goujons sont à part égale essentiels pour la stabilité des chaussures de piste. »
Une fois la partie structurelle imprimée en 3D, d’autres tests ont été réalisés sur la Pleko.
Buroni s’est montré très satisfait des résultats obtenus : « Les technologies de conception et de fabrication, associées à la Windform SP et à ses caractéristiques mécaniques, ont rendu les chaussures de piste Pleko très innovantes, portant l’ensemble du projet au plus haut niveau de personnalisation et de spécialisation. Je suis très satisfait de mes Pleko et Windform SP imprimées en 3D« .
N’oubliez pas que vous pouvez poster gratuitement les offres d’emploi de l’industrie de la FA sur 3D ADEPT Media ou rechercher un emploi via notre tableau d’offres d’emploi. N’hésitez pas à nous suivre sur nos réseaux sociaux et à vous inscrire à notre newsletter hebdomadaire : Facebook, Twitter, LinkedIn & Instagram !