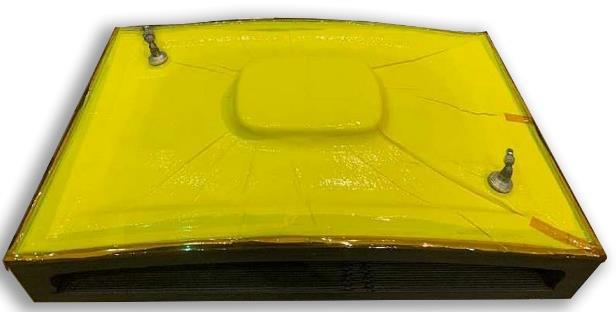
L’outillage d’autoclave est devenu essentiel pour le traitement des composants structurels aérospatiaux en composite polymère de haute qualité. Pour une industrie comme l’aérospatiale, un investissement dans ce type d’équipement doit être fait de manière très stratégique car sa fabrication s’accompagne souvent de certains défis.
La fabrication de ce composant nécessite généralement un moule rigide qui définit la forme finale de la pièce composite, et la pièce finale doit présenter des propriétés de haute performance et résister à des environnements austères.
SABIC’s Specialties business et Thermwood Corporation ont récemment exploré une nouvelle approche de fabrication pour produire les autoclaves. Dans l’industrie de la fabrication additive, SABIC est connue pour sa capacité à fournir des matériaux de FA sur mesure grâce à une chaîne de collaboration spécifique. L’entreprise a notamment développé une expertise dans la fabrication de pièces imprimées en 3D nécessitant l’utilisation de matériaux composites.
Thermwood, d’autre part, est l’une des trois entreprises qui fournit du matériel et des services d’impression 3D de très grand format avec des matériaux composites en granulés de polymère renforcé de fibres (FPR).
Dans le cadre de ce projet, les deux entreprises tirent parti de leurs compétences respectives pour produire des outils à géométrie complexe qui peuvent résister à plusieurs cycles d’autoclavage de composites thermodurcis tout en conservant une précision dimensionnelle.
Le processus de fabrication
Les deux entreprises ont d’abord évalué la viabilité de leur solution qui consiste à tirer parti de la technologie de fabrication additive grand format (LFAM) de Thermwood et des thermoplastiques haute performance de SABIC.
Pour ce faire, le fabricant d’imprimantes 3D a fabriqué un outil de panneau aérospatial de 1150 mm x 760 mm. Le processus d’impression de cet outil a nécessité huit heures et il a fallu 12 heures supplémentaires pour l’usinage à l’aide de l’imprimante LSAM® et du composé de SABIC LNP™ THERMOCOMP™ AM EC004XXAR1. Ce dernier est un matériau en résine ULTEM™ rempli de fibres de carbone à 20 %.
Après la numérisation de l’outil imprimé3D – à l’aide d’un scanner CreaformHandy SCAN 700, SABIC a produit les pièces composites requises en utilisant l’outil imprimé et une résine époxy sur un tissage de fibres de carbone à haut module appelé HexPlyF263.
Le producteur des matériaux a déclaré que « l’outil a été inspecté visuellement après chaque cycle d’autoclave et aucun signe d’usure n’a été observé. De plus, après 10 cycles d’autoclave, l’outil a été scanné à nouveau et ces résultats ont été comparés aux données du scan original. Aucun mouvement significatif n’a été observé et les différences dimensionnelles étaient dans les limites de la précision d’erreur de l’équipement de numérisation ».
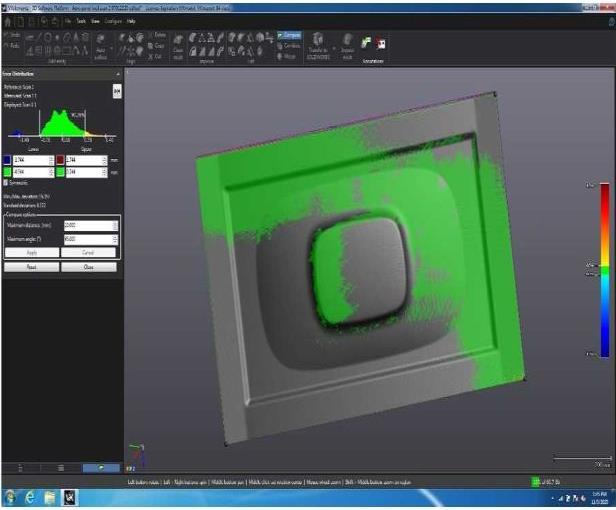
Pour assurer la viabilité du processus, l’équipe a comparé les dimensions de l’outil aux dimensions de la pièce finale dans les directions X et Z. Dans cette optique, ils ont placé des épingles dans des plaques plates imprimées en 3D et les résultats ont révélé qu’il n’y avait qu’une différence d’environ 0,025 % dans la direction X et de 0,25 % dans la direction Z. Ces résultats corroborent les tests CLTE selon la norme ASTM E-831 et soulignent le comportement anisotrope de la pièce.
Principaux avantages
Les deux entreprises ont pu livrer un outil d’autoclave performant en moins de temps qu’on ne le fait habituellement avec les procédés de fabrication conventionnels et de manière plus rentable. Sans oublier que des essais supplémentaires de l’outil d’autoclave LFAM au-delà de 10 cycles peuvent être envisagés pour illustrer d’autres gains d’efficacité par rapport aux procédés traditionnels.
N’oubliez pas que vous pouvez poster gratuitement les offres d’emploi de l’industrie de la FA sur 3D ADEPT Media ou rechercher un emploi via notre tableau d’offres d’emploi. N’hésitez pas à nous suivre sur nos réseaux sociaux et à vous inscrire à notre newsletter hebdomadaire : Facebook, Twitter, LinkedIn & Instagram !