Named ENESKApostpro, Joke Technology’s new post-processing system has been built with protection in mind.
The German manufacturer develops a wide range of tools that can be used for several stages of the post-processing step. They include for instance blasting systems, cleaning systems, chipping tools, diamond and CBN tools, driving motors and handpieces as well as grinding and polishing tools.
Designed to remove support structures on the 3D printed part, the new system ensures safe completion of multiple working stages in a single unit.
In addition to its enclosed working area, the machine is equipped with electrical and pneumatic tools as well as powerful suction devices.
The enclosed working area is meant to protect the operator from risk of explosion but also from cancerous and cardiovascular diseases. Indeed, metallic powders such as titanium or aluminium can lead to explosions and fires if they are not well handled.
In this regard, “the ENESKApostpro is therefore completely earthed to prevent spark discharge. An integrated moisture separator is optionally available for particularly reactive substances. The extraction system achieves an impressive output of 410 m³/h and its suction power is further enhanced by the side channel compressor. In addition, a compressed-air gun and a suction arm assist cleaning in more concealed corners. The fine dusts from gaps in a workpiece can therefore be removed without any risk of explosion”, explains the company.
To lay emphasis on the system’s safety standards, it should be noted that the device meets important IG Metall trade union “golden rules” for dust control, such as dust extraction directly at the point of exit.
There is an approximately ten-second post-suction phase before the unit can be opened – only then is the glass dome unlocked and the finished workpiece can be removed.
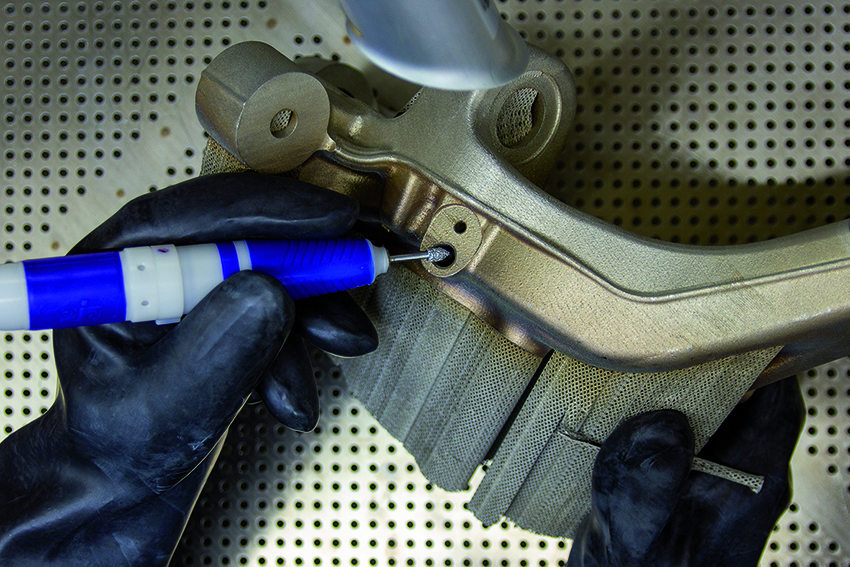
A versatile post-processing technology
Apart from its safety standards, the main characteristic that enables the ENESKApostpro to stand out from the crowd is its ability to achieve multiple steps of the post-processing phase: powder removal, removal of substrate materials or support structures.
“Its interior of just less than one square metre provides enough space for even the largest printing plates. Various electric and hydraulic tools for deburring, milling, grinding or polishing are driven by integrated control units. Three different micromotors can currently be connected simultaneously – which means a reduction in set-up times and allows rapid, versatile work”, concludes the company in a press release.
Remember, you can post free of charge job opportunities in the AM Industry on 3D ADEPT Media or look for a job via our job board. Make sure to follow us on our social networks and subscribe to our weekly newsletter : Facebook, Twitter, LinkedIn & Instagram ! If you want to be featured in the next issue of our digital magazine or if you hear a story that needs to be heard, make sure to send it to contact@3dadept.com