Vous souvenez-vous que je vous ai dit qu’un nombre croissant d’outils d’analyse des défauts étaient en cours de développement et de commercialisation ? Pour rappel, certains des défauts les plus courants créés au cours de la fabrication additive – et parmi les plus difficiles à prévenir – sont les formations de trous. Ils apparaissent au cours du processus de fusion laser sur lit de poudre.
Lorsque les lasers déposent trop d’énergie et trop rapidement dans le métal fondu ou le bain de fusion, de minuscules bulles de vapeur se forment et restent piégées lorsque le métal se refroidit, ce qui affaiblit l’intégrité structurelle de la pièce. Parce qu’ils se forment sous des couches activement imprimées, les défauts en forme de trou de serrure sont difficiles à repérer en temps réel – mais pas impossibles.
Pour résoudre ce problème, le Johns Hopkins Applied Physics Laboratory (APL) de Laurel, dans le Maryland, a mis au point des capteurs suffisamment rapides pour identifier les défauts avant qu’ils ne se matérialisent.
« Si nous pouvons identifier la formation de défauts à l’état fondu, nous avons la possibilité de réparer ces imperfections avant qu’elles ne limitent les performances« , explique Morgan Trexler, qui dirige le programme Science of Extreme and Multifunctional Materials (science des matériaux extrêmes et multifonctionnels) de l’APL. « Nous nous efforçons de rendre les processus de fabrication plus intelligents, ce qui conduira intrinsèquement à une fabrication plus rapide et à des composants plus fiables.
« Nous pouvons identifier les roches sous la surface des rivières depuis l’espace, non pas parce que nous les voyons directement, mais parce que nous pouvons voir les rapides où l’écoulement de l’eau est perturbé« , explique Steve Storck, chef de projet et scientifique en chef pour les technologies de fabrication au sein du département de recherche et de développement exploratoire de l’APL. « De même, si un pore est sur le point de se former dans une pièce, le flux thermique autour de lui sera perturbé, ce qui indique un défaut dans le processus de formation. Si nous pouvons mesurer cette température et ces anomalies spectrales avec précision et rapidité, nous devrions être en mesure de dire si quelque chose se forme dans, sous ou à côté du point de fusion actif« .
Les chercheurs ont émis l’hypothèse que ces défauts en forme de trou de serrure se produisaient dans des états transitoires. S’ils pouvaient interrompre le laser de dépôt juste avant que l’anomalie ne commence à se former, le métal en fusion pourrait alors refroidir suffisamment longtemps pour se déposer et fermer la dépression de vapeur, empêchant ainsi la formation de bulles.
Du concept au processus
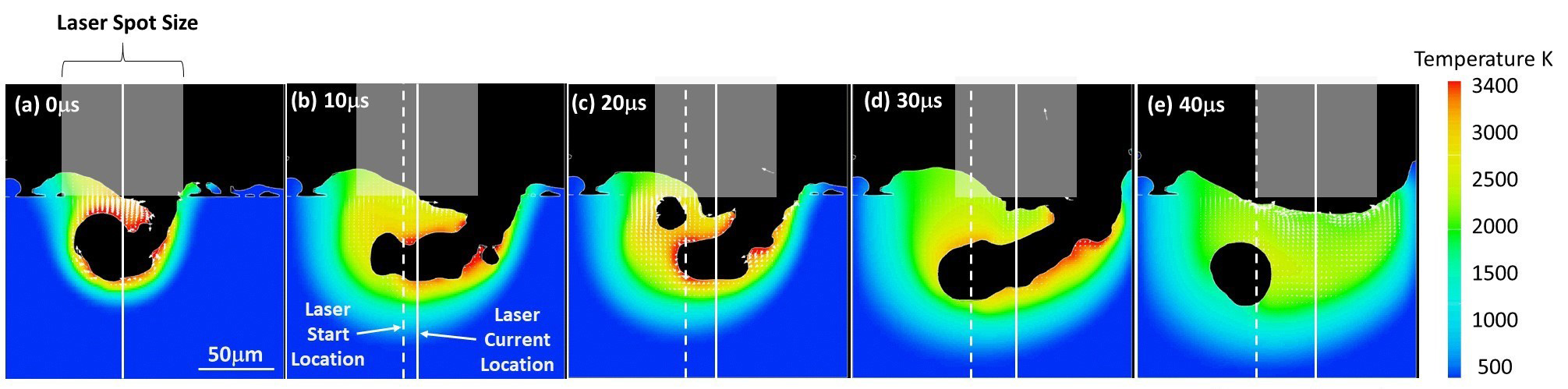
Crédit : Johns Hopkins APL
L’équipe a d’abord testé des capteurs conventionnels pour voir s’ils pouvaient identifier les signatures de défauts assez rapidement, mais elle s’est heurtée à des limites de résolution optique et de vitesse. C’est pourquoi elle a collaboré avec Mark Foster, professeur agrégé d’ingénierie électrique et informatique à la Whiting School of Engineering de l’université Johns Hopkins, et avec plusieurs étudiants postdoctoraux de la Whiting School pour améliorer un capteur développé et breveté par l’APL. Alliant leur expertise en science des matériaux, en fabrication additive, en ingénierie optique et en science des données, ils ont ajouté des photodiodes à plusieurs longueurs d’onde et augmenté la fréquence d’échantillonnage pour mesurer des données à haute résolution spatiale et temporelle sur le bain de fusion et sa dynamique, ce qui leur a permis de recueillir les informations nécessaires pour identifier les premiers stades d’un défaut de trou de serrure à une échelle de temps qui pourrait permettre une réparation en temps réel.
Une fois le capteur à grande vitesse opérationnel, les chercheurs ont mis au point un cadre de contrôle capable de communiquer entre le capteur et le laser et d’ordonner à ce dernier de s’éteindre lorsque le bain de fusion devenait trop chaud et risquait de créer un défaut, le tout dans un délai de 10 à 20 millionièmes de seconde.
En continuant à faire appel à l’expertise de l’APL, Storck et Pagán ont contacté le développeur Mike Brown, qui a adapté un réseau de portes programmables à grande vitesse – essentiellement un circuit intégré qui peut être programmé pour répondre à des besoins spécifiques – conçu à l’origine à des fins de défense, afin de rechercher des missiles dans le ciel.
« L’un des aspects uniques du travail à l’APL est la capacité d’exploiter des technologies provenant de domaines apparemment sans rapport ; par exemple, nous pouvons prendre les connaissances et l’expertise que nous appliquons à la défense antimissile – répondre aux données de mesure très rapidement et faire des ajustements encore plus rapidement – et les appliquer à la fabrication additive« , a déclaré M. Storck.
Après avoir intégré tous les systèmes, l’équipe a démontré avec succès la capacité du système à réagir en 952 nanosecondes seulement, soit moins d’une microseconde ou plus vite qu’un clignement d’œil.
« Ces résultats étaient excellents, car nous devons au moins mesurer deux fois plus vite que ce qui se passe physiquement, afin de pouvoir saisir les pics et les creux de la réponse spectrale en corrélation avec la température« , a expliqué M. Storck. « Notre système peut mesurer les relevés spectraux et de température et réagir dix fois plus vite que ce qui est nécessaire d’après les simulations de la formation des trous de serrure.
L’équipe prévoit d’intégrer l’intelligence artificielle dans le processus afin d’accélérer la boucle de rétroaction et d’indiquer avec plus de précision où et comment les défauts se forment. Selon Storck, cela permettra un contrôle et une réparation en temps réel, l’APL s’efforçant de produire des pièces dignes de confiance dès leur fabrication.
N’oubliez pas que vous pouvez poster gratuitement les offres d’emploi de l’industrie de la FA sur 3D ADEPT Media ou rechercher un emploi via notre tableau d’offres d’emploi. N’hésitez pas à nous suivre sur nos réseaux sociaux et à vous inscrire à notre newsletter hebdomadaire : Facebook, Twitter, LinkedIn & Instagram !