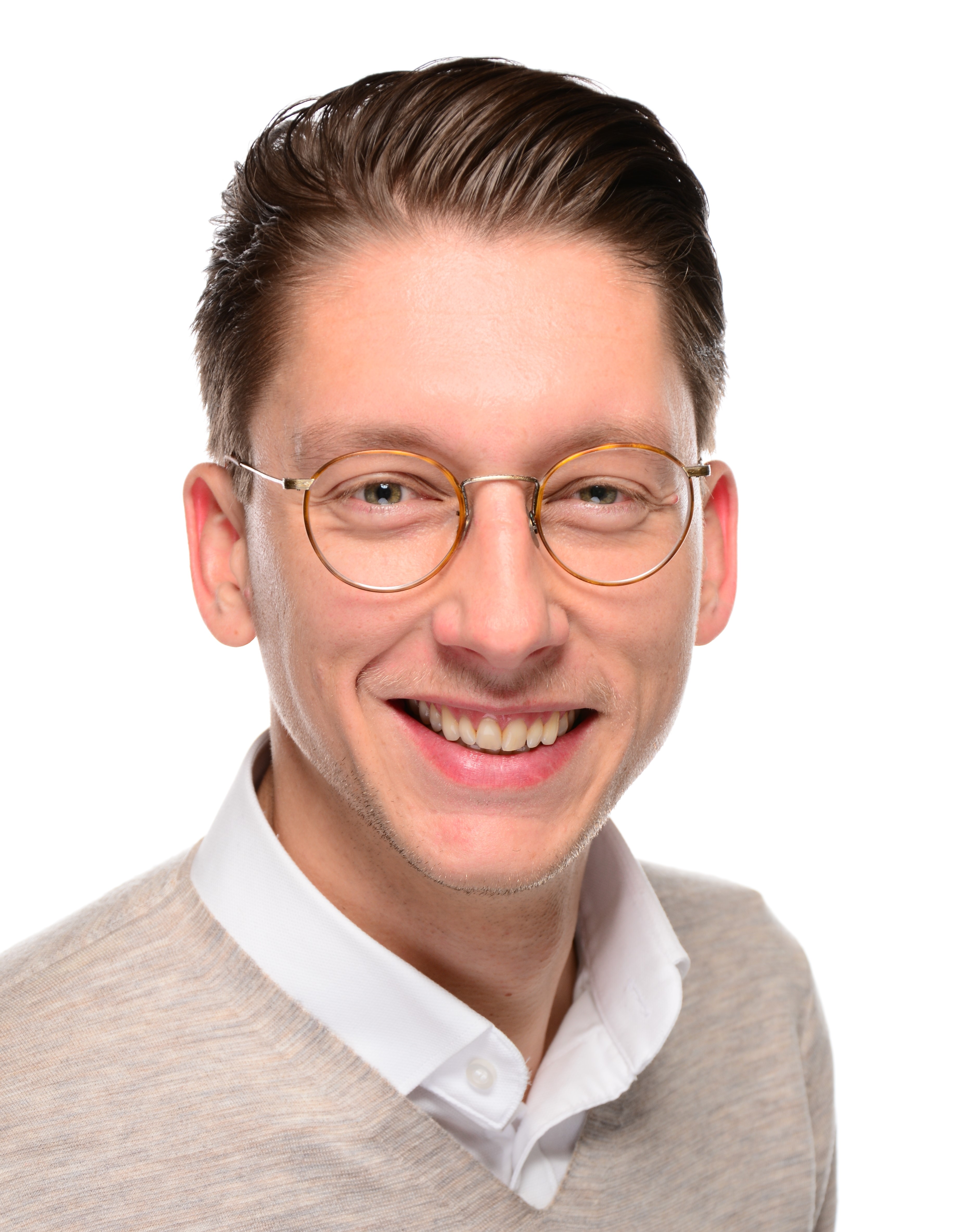
From digitization, design and simulation through manufacturing, inspection and management, 3D Systems offers a range of technologies that provides a seamless, customizable workflow designed to optimize products and processes while accelerating outcomes.
In 1983, 3D Systems introduced the world to 3D printing with the first SLA (stereolithography) system. Since then, the company has shaped the 3D printing industry through its many technological innovations and partnerships, impacting a wide range of applications – from aerospace and automotive to consumer products.
Kay-O Kissling, Sales Manager Aerospace- EMEA at 3D Systems, shared the company’s experience in metal 3D printing within the aerospace sector as part of the dossier of the June issue of 3D Adept Mag. Discover the full interview in this Opinion of the Week.
What is the contribution of 3D printing to the aeronautics industry?
3D printing contributes in the aerospace sector at 2 main levels:
First of all, there is the aircraft part itself. By leveraging a concept called DfAM – Design for Additive Manufacturing – 3D printing can improve part performance – including reducing the weight of the part which is so critical in aerospace – through design innovation. With DfAM, the engineer designs a part according to the desired functionality; with conventional manufacturing, the engineer designs the part according to what can be manufactured. This is the crucial difference between additive and conventional manufacturing. 3D printing also enables part customization (important for branding as well as cost-effective low volume production) and reduced part count – meaning that a part assembly may have 5 parts instead of 20 – again due to DfAM.
Another major contribution is to the supply chain. Commercial aviation has a very diverse and complex supply chain with millions of parts going into an aircraft and hundreds of suppliers involved. What 3D printing offers is the potential of reducing the complexity of the supply chain (resulting in more transparency) and offering a shorter time to market… Using 3D printing for part production eliminates the need for time-consuming tooling, reducing production time and costs while ensuring on-time part delivery. It also offers a potential back-up solution to traditional manufacturing. Let’s say an aircraft delivery is delayed because one supplier did not produce their part on time. In this case, the part may be able to be 3D printed, which typically takes less time to produce since no tooling is required. Also, with distributed manufacturing, it is possible to 3D print the missing part closer to the location of the final aircraft assembly, further saving shipping and transportation time.
Are there any differences in the use of additive manufacturing in the automotive and in the aeronautics sectors?
One of the main differences is that in the automotive sector, additive manufacturing is used more for prototyping and checking part designs for fit, form and function. Lightweighting the parts is also important for better fuel economy but in aerospace, lightweighting is even more crucial. Production volumes are of course vastly different – aircraft are produced in relatively small numbers, making the industry a perfect candidate for 3D printing.
The last key difference is in the complexity of the documentation. The aeronautic sector is more documented than any other industry. Every part and material must be certified and traceable by the aviation authorities. The qualification and certification processes are the key challenges of this sector. Full traceability – from the raw material to the final aircraft part – is an absolute must.
Speaking of a specific example of the metallic additive manufacturing of a part, what are the advantages and disadvantages compared to traditional manufacturing methods?
As mentioned earlier, the main advantages are weight reduction, part performance and part consolidation – enabled by DfAM…
As for the disadvantages, in terms of feasibility, 3D printing is optimized for low to moderate volumes. It would not make sense to produce tens of thousands of parts with metal 3D printing. Also, if you are designing a very basic part, 3D printing may not be your best bet. However, if you want to improve part functionality and increase the part’s geometric complexity, this is where 3D printing really adds value. Again, it enables you to think out of the box.
Do 3D printed parts have the same characteristics of parts that are manufactured with traditional techniques?
3D printed metal parts generally have the same density, isotropic properties and surface quality as CNC’d parts. In both cases, the parts have to undergo the same traditional sub-machining processes. However, with DfAM, the parts can be produced to require less post-processing, i.e. with larger tolerances.
What would be the limits of additive manufacturing in the aeronautic sector in terms of materials?
First of all, it should be noted that 3D Systems offers the possibility to manufacture parts in Titanium, Stainless Steel, Cobalt-Chrome, Aluminum Alloy, Maraging Steel, Nickel and Super Alloy materials.
The aerospace market is quite slow to adopt new materials.
How do you perceive the metal additive manufacturing market in the long run?
For aerospace, we are still a few years out for mass adoption. At the moment, the industries we see leading adoption are space – rockets, satellites, etc. and – low volume production of aircraft interior parts.
We are also beginning to see increased adoption in the military and defense sectors where certification is less stringent than commercial aviation.
Your last word?
The key companies shaping the future in the aerospace sector must be able to cover the whole value chain with end-to-end solutions but also be able to customize solutions for the customer’s requirements – leveraging software, materials, 3D printers, engineering expertise, partnerships, and more. 3D Systems can support customers in every step of the design and production process and help them understand the different characteristics of different technologies.
For further information about 3D Printing, follow us on our social networks and subscribe to our newsletter
Would you like to subscribe to 3D Adept Mag? Would you like to be featured in the next issue of our digital magazine? Send us an email at contact@3dadept.com
//pagead2.googlesyndication.com/pagead/js/adsbygoogle.js
(adsbygoogle = window.adsbygoogle || []).push({});