Even though there is currently a broader use of composite materials in sectors like the automotive due to the desirable combination of low weight and high strength properties, those materials have long been used for advanced, high cost applications within the aerospace sector. As a matter of fact, the story of Orbital Composites started with one engineering aerospace project: “build the fastest helicopter in the world”. And as we have often seen in this industry, industry challenges encountered in one project often lead to bigger projects which eventually become viable businesses.
The challenges in Orbital Composites’ case were reliable “automated composite manufacturing tools”. The fact is, automation of composites manufacturing comes in several forms such as Automated Fiber Placement (AFP), Automated Tape Laying (ATL), filament winding to name a few.
What marked Orbital Composites (OC) the most, is the fact that over “80% of the mass (excluding propulsion/fuel) is made out of three things: carbon fiber, copper wire and matrix material to hold it all together.” On the one hand, the market revealed that the broader use of carbon fiber led several companies to question themselves on cost-efficient manufacturing processes that could print strong and lightweight parts; on the other hand, several manufacturing processes still relied on manual tasks.
With a key interest in the use of continuous fiber for different applications, Orbital Composites decided to address these issues by developing a co-axial extrusion process.
“It turns out, by developing a process to 3D print fast helicopters, we have also addressed the needs of high-volume manufacturing of VTOL aircraft. By the way, the same process applies to making cubesats in high volume. If these printing processes can be scaled up to be able to produce >100m objects, then it can be applied to make wind turbine blades, rockets and space habitat modules with synthetic gravity enabling permanent human habitation in space for millions of people”, Amolak Badesha, CEO of Orbital Composites and our guest in this Opinion of the Week.
Founded in 2015, Orbital Composites is a California-based company that recognizes the need to enhance “scale, strength, speed, and flexibility of design” in additive manufacturing. However, the company decided to play its part in the field through robotic automation solutions. The gamble seems risky since this specific field of activity is relatively nascent.
In the myriad of things that need to be done to make the marriage of additive manufacturing and robotics an attractive market share to various manufacturing industries, Orbital Composites has decided to focus on 4 pain points: robotics, materials, scalability and digital manufacturing.
How does Orbital Composites address these four pain points?
Needless to question the potential of robotics and Additive Manufacturing when they are used independently. Imagine now, what they can deliver when they are put together. Robots and AM can intersect in various ways. The Orbtial Composites team for instance, is on a mission to develop robot manufacturing fleets that could be easily programmed and managed for the 3D printing of large end-use parts, using lightweight composite materials.
Understanding the company’s core business requires to describe the concept of multi-robot printing. The concept may involve several possibilities but Badesha lays emphasis on three main use cases:
-
Robotics -
Multi-robot printing – Image: Orbital Composites
“Multiple robots in the same work cell, printing the same part, in parallel: This is important to keep the factory footprint small, yet capable of producing a large number of parts. The trick is making sure robots do not collide with each other.
Multiple robots printing the same part, in parallel: This is a more advanced use case. Not only the robots need to be coordinated to avoid collisions, the programming of multiple robots printing together in a way where you can still produce high-quality parts. This requires a lot of math!
Multi-material printing: Instead of printing monolithic parts, highly complex multi-material parts can be printed, with multiple robots holding different end-effectors for printing, pre/post processing or automation. This is akin to a number of robots working with each other to make cars, except that printing is included as one of the possible steps. Our Orbital S robotic print-cell is designed to be able to hold up to six robots”.
Although the company mostly works on silent mode, we do know that it has been developing industrial-grade robotic 3D printers that are easily adaptable. Its first commercial robotic 3D printer for instance, integrates an ORB operating system which facilitates the printing of thermoplastic composite parts. The machine features a frame-mounted robot that features a high-volume thermoplastic print head, whose position can easily be adaptable.
To scale this solution, the team has been enhancing the size, the cycle time and the accessibility of their manufacturing platform. “Due to our modular platform, we can build robotic printers with build sizes from 1m to >100m and [each of these size categories delivers fast cycle times to achieve volume production. Moreover,] to bring manufacturing back to US and allied nations, mobile manufacturing is essential as it enables new paradigms of just-in-time manufacturing near where the parts are used. [That’s why we aim to] rapidly deploy mobile print cells dramatically and simplify logistics across the entire manufacturing sector”, Badesha notes.
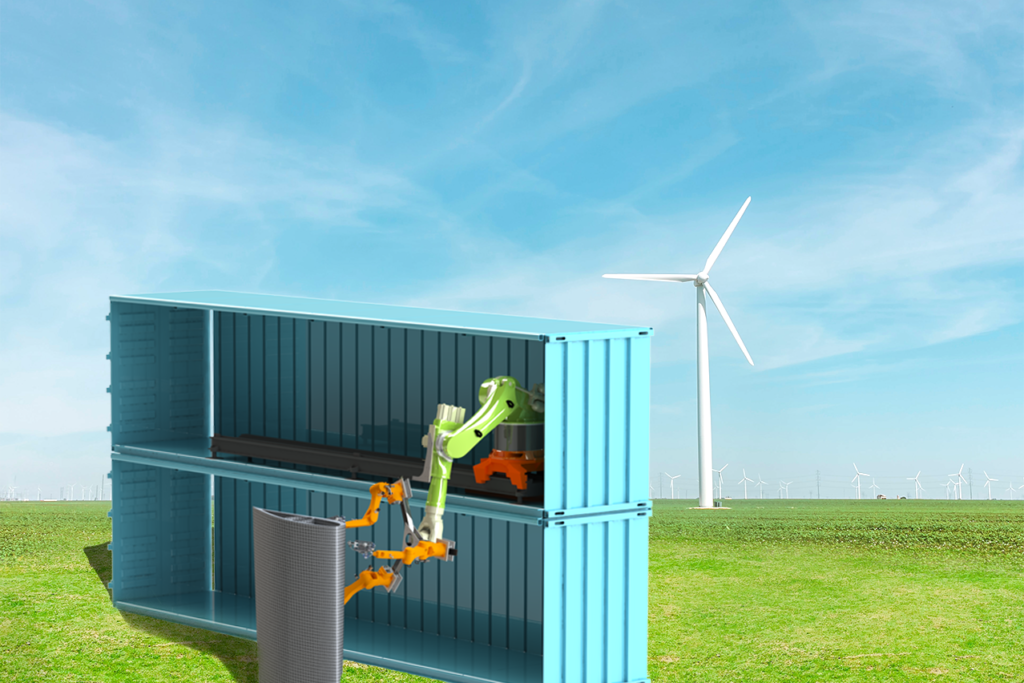
While looking at the adoption of robotics for AM today, Badesha sees for manufacturers the “ability to print out-of-plane with >12 degrees of freedom.” For the CEO, combining robotics and AM also facilitates flexible fixturing which allows for multi-step prints and the ability to print complex parts. Not to mention the possibility to use “robots for non-print operations like milling, finishing and most importantly automating part insertion and removal.”
As far as materials are concerned, as you may know, industrials often rely on composites manufacturing as a replacement of metal parts. With Orbital Composites’ platform approach, industrials could go beyond this widely-accepted idea and print with a large library of materials. “This includes thermoset and thermoplastic resins, both resin types with chopped or continuous fiber, and metal. The platform is also easily extendable to ceramic matrix composites and pre-certified materials can be utilized for accelerated adoption”, our guest explains.

Furthermore, as the company’s ultimate goal is to enable industries to manage robot manufacturing fleets, Orbital Composites necessarily needs to take into account digital manufacturing, which is why it has been developing an AI and machine learning-driven software that enables robots to autonomously print objects in the same build area. The advanced programming software can also enable multiple robots to simultaneously print the same object. As the team currently invests extra miles to push advanced composites, robotics and digital manufacturing forward, they will open up new possibilities for applications of AI/ML for large-scale polymer and composite printing and expand the development of “mission critical products with complete virtual replicas” using digital twin.
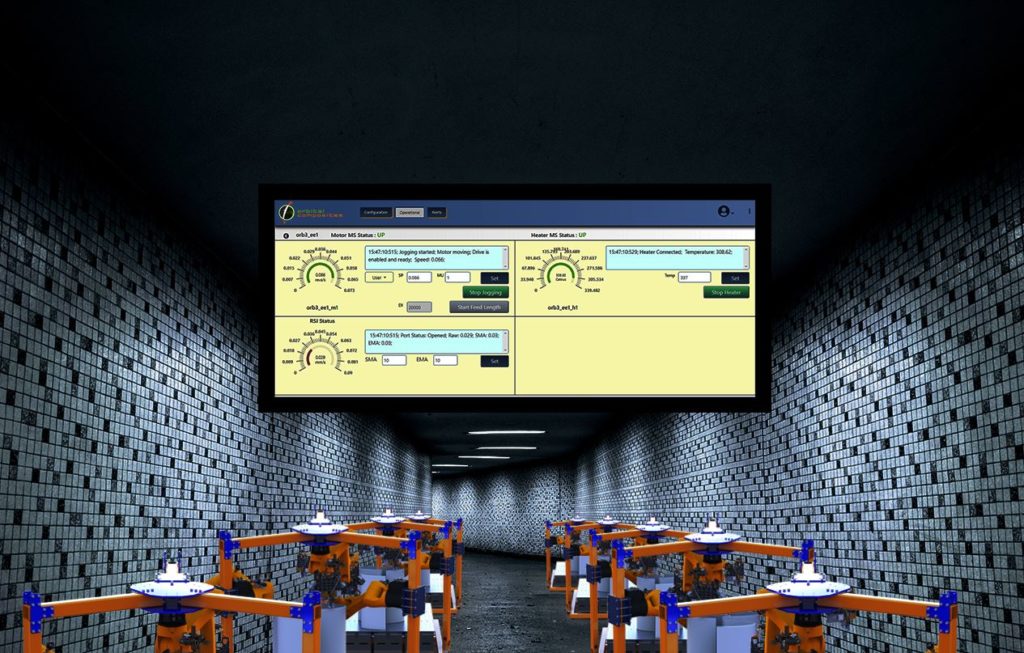
Applications and current projects
Automated composite additive manufacturing has a rosy future ahead of it and as seen at the beginning, one of the primary vertical industries that will benefit from it is the aviation industry; this includes applications related to drones and satellites.
As Orbital Composites is a relatively new comer in this sphere, we’ve asked for a tangible application the team has already achieved in robotics AM. Orbital Composites’ spokesperson mentioned a product they have developed in collaboration with Lore, a team of engineers who has developed a 3D printed carbon hard-shelled shoe.
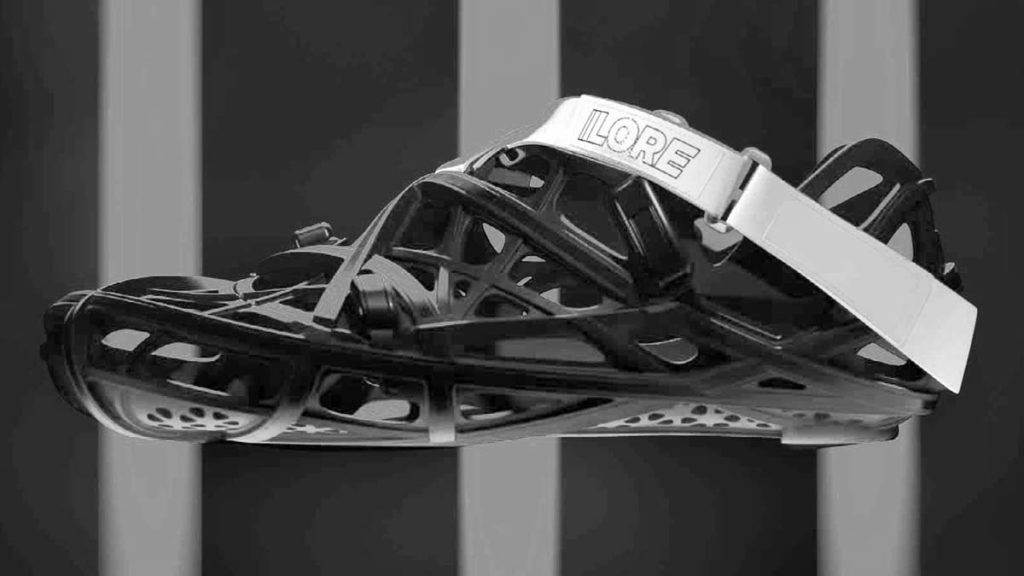
This “breakthrough cycling shoe is custom 3D printed based on the scan of each cyclist’s feet. It is only possible with 12-axis continuous fiber 3D printing; only possible with two robots collaborating together. As can be seen from the shoe example, complex geometries, such as organic shapes and curves, are notoriously difficult to make, [and can now be created using] robotic AM with continuous fiber. While out-of-plane printing allows mass customization of complex shaped end-products, the agility of the robots allows scale into mass production” the expert enthuses.
Right now, to demonstrate the capabilities of its 3D printing robots, Orbital Composites is currently collaborating with Oak Ridge National Laboratory (Oak Ridge, Knoxville, Tenn., U.S.) and the University of Maine (UMaine, Orono, Maine, U.S.) to develop on-site, high-throughput manufacturing of wind blades with large-scale continuous fiber additive manufacturing. The project is being carried out as part of a $4 million grant from the U.S. Dept. of Energy (DOE), Office of Energy Efficiency and Renewable Energy (EERE).
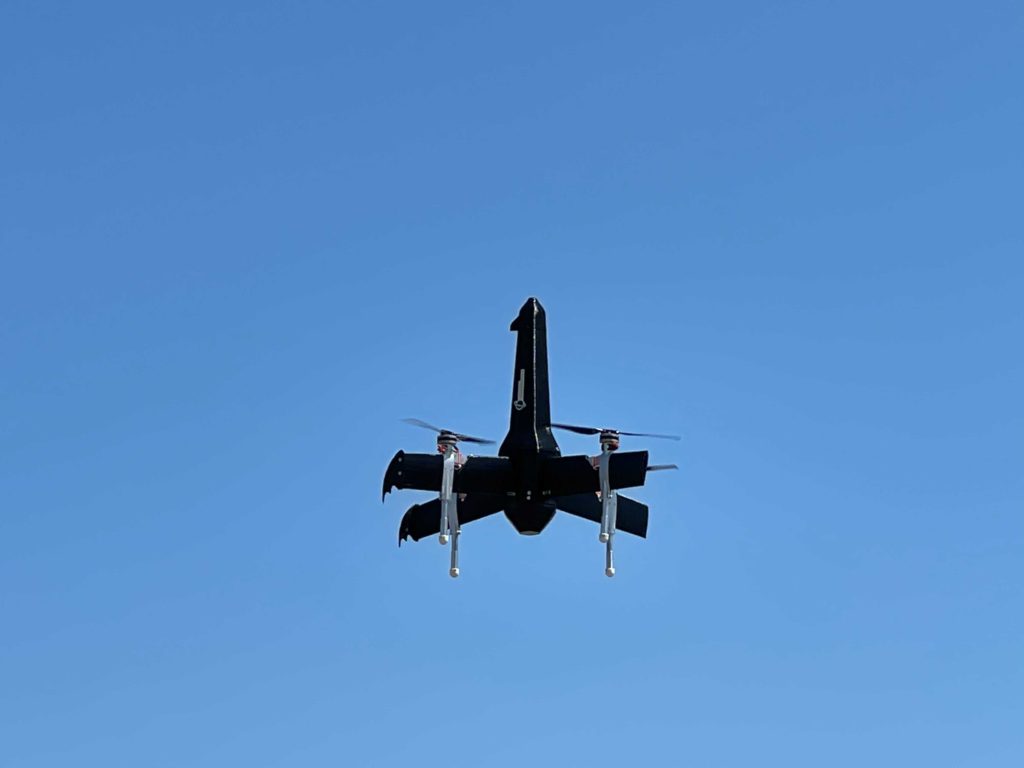
“Another project with Oak Ridge National Laboratory demonstrates Orbital’s rapid prototyping and scaled production capabilities applied to high-performance VTOL aircraft. Through an STTR grant from US Air Force’s Agility Prime program, we are developing a high-performance cargo drone that can meet the challenging mission requirements and yet can be entirely 3D printed. Our AM platform will be combined with compression molding, to advance the AM-CM process to demonstrate high-volume manufacturing of propeller blades. The hybrid AM-CM process combines the benefits of Additive Manufacturing with Compression Molding, enabling high volume production of high-performance composite parts made from multi-material polymers and continuous fiber.
We have also recently delivered our Orbital S system to the University of Minnesota, Duluth. We are supporting their AM research efforts by providing them with hardware, software, and technical support. Lastly, we were selected to participate in the Catalyst Accelerator’s On-Orbit Servicing, Assembly, and Manufacturing Cohort. This program, supported by the Air Force Research Laboratory Space Vehicles Directorate (AFRL/RV and Space Force), empowered us to develop “on-orbit manufacturing of large, precise, and resilient space structures like solar arrays, RF antennas, and segmented optics.” We advanced these technologies as we collaborated and engaged with industry experts, governmental and commercial emissaries, and customers. Our experience culminated in a live demonstration of our accomplishments at the Catalyst Campus for Technology and Innovation. We created many lasting business relationships and partnerships within and outside our cohort, and plan to continue to work with them to create the next generation of space exploration technology”, Badesha states.
“We have a number of additional projects that will become public over time or are strictly confidential from our customers” he adds.
The next step in OC’s pipeline
Combining robotics and AM seems to bring a lot of advantages whether it is in terms of workforce or automated mass manufacturing. But several stages still need to be enhanced to foster the adoption of this powerhouse marriage of processes. One of the most urgent stages that require improvements is software. There is “a lack of unified workflow from CAD to print. There are a number of steps involved and our goal is to build a unified software combining all the intermediate steps into one. We are already well on our way to do this with the development of Orbital OS, our operating system that can control an unlimited number of robots. This allows us to manage large robotic factories seamlessly and usher in the era of Software-Defined-Manufacturing or SDM”, Badesha points out.
However, their most immediate next steps will be to enable national labs, universities and research institutions to explore and adopt robotic, continuous fiber 3D printing by taking advantage of their Orbital S printers. The robotics AM expert is also looking to deliver Manufacturing-as-Service (MaaS) to customers who are interested in mass-customized, high-volume polymer, composite, metal or hybrid products and obviously to develop breakthrough products by partnering with key customers in different verticals.
Remember, you can post job opportunities in the AM Industry on 3D ADEPT Media free of charge or look for a job via our job board. Make sure to follow us on our social networks and subscribe to our weekly newsletter : Facebook, Twitter, LinkedIn & Instagram ! If you want to be featured in the next issue of our digital magazine or if you hear a story that needs to be heard, make sure you send it to contact@3dadept.com